What is Circuit Trace?
Circuit trace, also known as PCB trace or copper trace, refers to the conductive paths etched from copper sheets laminated onto a non-conductive substrate. These traces are the “wires” of a printed circuit board (PCB) that carry electrical signals and power between components on the board. The proper design and implementation of circuit traces are crucial for the performance, reliability, and manufacturability of a PCB.
The Importance of Circuit Trace in PCB Design
Circuit traces play a vital role in PCB design as they determine how well the board functions. Some key aspects that make circuit traces important include:
-
Signal Integrity: Properly designed traces ensure that signals reach their intended destinations without degradation, reflection, or crosstalk.
-
Power Distribution: Traces carry power from the power source to various components on the board. Adequate trace width and thickness are necessary to handle the required current without excessive voltage drop or heat generation.
-
Electromagnetic Compatibility (EMC): Trace routing and spacing affect the board’s susceptibility to electromagnetic interference (EMI) and its potential to emit EMI.
-
Manufacturing Feasibility: Trace width, spacing, and copper thickness must adhere to the capabilities of the PCB manufacturing process to ensure reliable and cost-effective production.
Factors Affecting Circuit Trace Design
Several factors influence the design of circuit traces on a PCB. These include:
Trace Width
Trace width is a critical parameter that depends on the current carrying requirement, allowable temperature rise, and the PCB manufacturing process. Wider traces have lower resistance and can carry more current, but they also consume more board space. The IPC-2221 standard provides guidelines for determining the appropriate trace width based on the current and temperature rise.
Trace Thickness
Trace thickness, or copper weight, affects the current carrying capacity and the impedance of the trace. Thicker traces can carry more current and have lower resistance, but they also increase the cost of the PCB. Common copper weights include 0.5 oz, 1 oz, and 2 oz per square foot.
Trace Spacing
The spacing between traces, also called the trace pitch, depends on the voltage difference between adjacent traces and the PCB manufacturing process. Adequate spacing is necessary to prevent short circuits, reduce crosstalk, and ensure reliable PCB Fabrication. The IPC-2221 standard provides minimum spacing requirements based on the voltage difference and the PCB material.
Trace Routing
Trace routing refers to the path that a trace takes from its source to its destination. Proper trace routing is essential for signal integrity, EMC, and manufacturability. Some key considerations in trace routing include:
- Minimizing trace length to reduce resistance and inductance
- Avoiding sharp corners and using smooth curves to minimize reflections
- Providing a continuous ground plane beneath sensitive traces to reduce crosstalk
- Separating high-speed traces from low-speed traces to minimize interference
- Following the manufacturer’s design rules for trace width, spacing, and via size
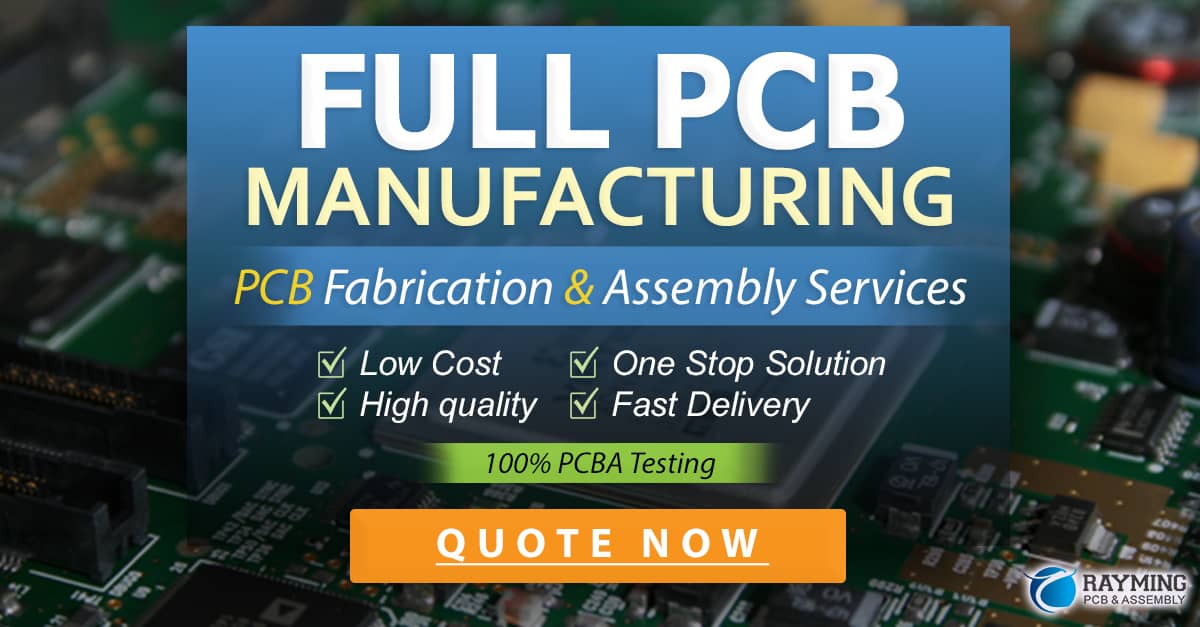
Circuit Trace Materials
The most common material for circuit traces is copper due to its excellent electrical conductivity, thermal conductivity, and ease of fabrication. However, other materials such as aluminum, silver, and gold are also used in specific applications.
Copper
Copper is the standard material for circuit traces in PCBs. It offers several advantages, including:
- High electrical conductivity (5.96 × 10^7 S/m)
- High thermal conductivity (401 W/m·K)
- Good resistance to corrosion
- Easy to etch and plate
- Relatively low cost compared to other conductive materials
Aluminum
Aluminum is sometimes used as an alternative to copper in PCBs for high-power applications or when weight is a concern. Advantages of aluminum include:
- Lower density compared to copper (2.70 g/cm³ vs. 8.96 g/cm³)
- Good thermal conductivity (237 W/m·K)
- Lower cost than copper
However, aluminum has some drawbacks, such as:
- Lower electrical conductivity compared to copper (3.50 × 10^7 S/m)
- Higher susceptibility to corrosion
- Difficulty in soldering
- Requires special fabrication processes
Other Materials
In some specialized applications, other materials like silver or gold may be used for circuit traces. These materials offer higher conductivity than copper but are more expensive and less commonly used.
- Silver has the highest electrical conductivity (6.30 × 10^7 S/m) and thermal conductivity (429 W/m·K) among metals. It is used in high-frequency and RF applications.
- Gold is highly resistant to corrosion and is used in high-reliability and aerospace applications. However, it has lower conductivity than copper (4.10 × 10^7 S/m) and is significantly more expensive.
Circuit Trace Manufacturing Process
The manufacturing process for circuit traces involves several steps, including:
-
PCB Design: The PCB layout is designed using electronic design automation (EDA) software, following the design rules and guidelines for the chosen manufacturing process.
-
PCB Fabrication: The designed PCB is fabricated using a multi-step process that includes:
- Applying a photoresist layer to the copper-clad laminate
- Exposing the photoresist to UV light through a photomask that contains the trace pattern
- Developing the photoresist to remove the exposed areas
- Etching away the unwanted copper using a chemical etchant
- Stripping the remaining photoresist
- Drilling holes for vias and component mounting
-
Applying a soldermask and silkscreen for protection and labeling
-
PCB Assembly: The fabricated PCB is populated with components using surface mount technology (SMT) or through-hole technology (THT).
-
PCB Testing: The assembLED PCB undergoes various tests, such as in-circuit testing (ICT), functional testing, and boundary scan testing, to ensure proper functionality and reliability.
Circuit Trace Design Guidelines
To ensure optimal performance and manufacturability of circuit traces, designers should follow these guidelines:
- Use appropriate trace width and thickness based on the current requirements and PCB manufacturing constraints.
- Maintain adequate spacing between traces to minimize crosstalk and ensure manufacturability.
- Use a continuous ground plane beneath sensitive traces to reduce crosstalk and improve signal integrity.
- Minimize trace length to reduce resistance, inductance, and signal delay.
- Avoid sharp corners and use smooth curves to minimize signal reflections.
- Separate high-speed traces from low-speed traces to minimize interference.
- Follow the manufacturer’s design rules for trace width, spacing, and via size.
- Use appropriate circuit trace materials based on the application requirements and cost constraints.
Circuit Trace Troubleshooting
When problems arise in a PCB, circuit traces are often the culprit. Some common issues related to circuit traces include:
-
Open Circuits: An open circuit occurs when there is a break in the trace, preventing current from flowing. This can be caused by manufacturing defects, mechanical damage, or excessive current that leads to trace burnout.
-
Short Circuits: A short circuit happens when two or more traces that should not be connected come into contact with each other. This can be due to manufacturing defects, damage, or conductive debris bridging the traces.
-
Excessive Resistance: If a trace is too long, too thin, or made of a material with high resistivity, it can have excessive resistance, leading to voltage drop and heat generation.
-
Signal Integrity Issues: Improper trace routing, inadequate spacing, or lack of a proper ground plane can lead to signal integrity problems like reflections, crosstalk, and EMI.
To troubleshoot circuit trace issues, designers can use techniques such as:
- Visual inspection using a microscope or high-resolution camera
- Continuity testing using a multimeter or ohmmeter
- Time-domain reflectometry (TDR) to locate faults in traces
- X-ray inspection to detect internal defects or damage
- Thermal imaging to identify areas of excessive heat generation
Frequently Asked Questions (FAQ)
-
What is the difference between a trace and a via?
A trace is a conductive path that carries signals and power on the surface of a PCB, while a via is a conductive hole that connects traces on different layers of the PCB. -
How do I calculate the appropriate trace width for my PCB?
The appropriate trace width depends on the current requirement, allowable temperature rise, and PCB manufacturing constraints. You can use the IPC-2221 standard or online Trace Width Calculators to determine the suitable width for your application. -
Can I use different trace widths on the same PCB?
Yes, you can use different trace widths on the same PCB to accommodate varying current requirements and space constraints. However, make sure to follow the PCB manufacturer’s design rules for minimum and maximum trace widths. -
What is the difference between 0.5 oz and 1 oz copper weight?
Copper weight refers to the thickness of the copper layer on the PCB. A 0.5 oz copper weight means that the copper layer is 0.5 ounces per square foot, which translates to a thickness of about 17.5 microns. A 1 oz copper weight is twice as thick, at about 35 microns. -
How can I minimize crosstalk between traces?
To minimize crosstalk between traces, you can: - Increase the spacing between traces
- Use a continuous ground plane beneath sensitive traces
- Route high-speed traces away from low-speed traces
- Use differential signaling for high-speed traces
Factor | Description |
---|---|
Trace Width | Depends on current, temperature rise, and manufacturing process |
Trace Thickness | Affects current capacity, impedance, and cost |
Trace Spacing | Depends on voltage difference and manufacturing process |
Trace Routing | Affects signal integrity, EMC, and manufacturability |
Trace Material | Copper is most common; aluminum, silver, and gold are also used |
Troubleshooting Technique | Description |
---|---|
Visual Inspection | Uses microscope or high-resolution camera to detect faults |
Continuity Testing | Uses multimeter or ohmmeter to check trace continuity |
Time-Domain Reflectometry | Locates faults in traces by analyzing reflected signals |
X-Ray Inspection | Detects internal defects or damage in traces |
Thermal Imaging | Identifies areas of excessive heat generation in traces |
0 Comments