What is a Castellated PCB?
A castellated PCB, also known as a castellated hole PCB or castellated edge PCB, is a printed circuit board that has a series of plated semi-circular holes or slots cut into one or more edges. These castellations act as both electrical connections and mechanical supports, allowing the PCB to be mounted perpendicular to another PCB or surface. Castellated PCBs provide a simple, compact, and low-profile method for assembling multiple PCBs together into a larger system.
The term “castellated” comes from the resemblance of the semi-circular holes to the battlements or turrets of a castle wall. The castellations are typically plated with copper, gold, or tin to provide reliable electrical connections and prevent corrosion.
Advantages of Castellated PCBs
Castellated PCBs offer several advantages over other methods of assembling multiple PCBs, such as connectors or wire soldering:
-
Space savings: Castellated PCBs allow for a very compact and low-profile assembly, as the PCBs can be mounted directly together without the need for additional connectors or wires. This is especially important in applications where space is limited, such as in wearable devices, smartphones, or IoT sensors.
-
Simplified assembly: Assembling castellated PCBs is a straightforward process that can be done by hand soldering or using reflow soldering techniques. This eliminates the need for complex and time-consuming wiring or connector assembly.
-
Reduced cost: By eliminating the need for additional connectors or wires, castellated PCBs can reduce the overall cost of the assembly. Additionally, the simplified assembly process can lead to reduced labor costs and faster production times.
-
Improved reliability: Castellated PCBs provide a robust mechanical and electrical connection between the boards, reducing the risk of connection failures due to vibration, shock, or thermal stress. The plated castellations also provide a reliable and corrosion-resistant electrical connection.
-
Design flexibility: Castellated PCBs allow for greater design flexibility, as the castellations can be placed at any desired location along the edge of the board. This enables designers to create custom board shapes and sizes to fit their specific application requirements.
Applications of Castellated PCBs
Castellated PCBs are used in a wide range of applications across various industries, including:
-
Consumer electronics: Castellated PCBs are commonly used in smartphones, smartwatches, and other wearable devices to connect multiple boards in a compact and low-profile assembly.
-
IoT devices: Many IoT sensors and devices use castellated PCBs to connect sensor boards, communication modules, and power management boards in a small form factor.
-
Automotive electronics: Castellated PCBs are used in automotive applications such as dashboard displays, infotainment systems, and advanced driver assistance systems (ADAS) to connect multiple boards in a reliable and space-efficient manner.
-
Medical devices: Castellated PCBs are used in medical devices such as wearable health monitors, implantable devices, and diagnostic equipment to provide compact and reliable board-to-board connections.
-
Industrial automation: Castellated PCBs are used in industrial control systems, sensors, and communication modules to create rugged and reliable multi-board assemblies that can withstand harsh environments.
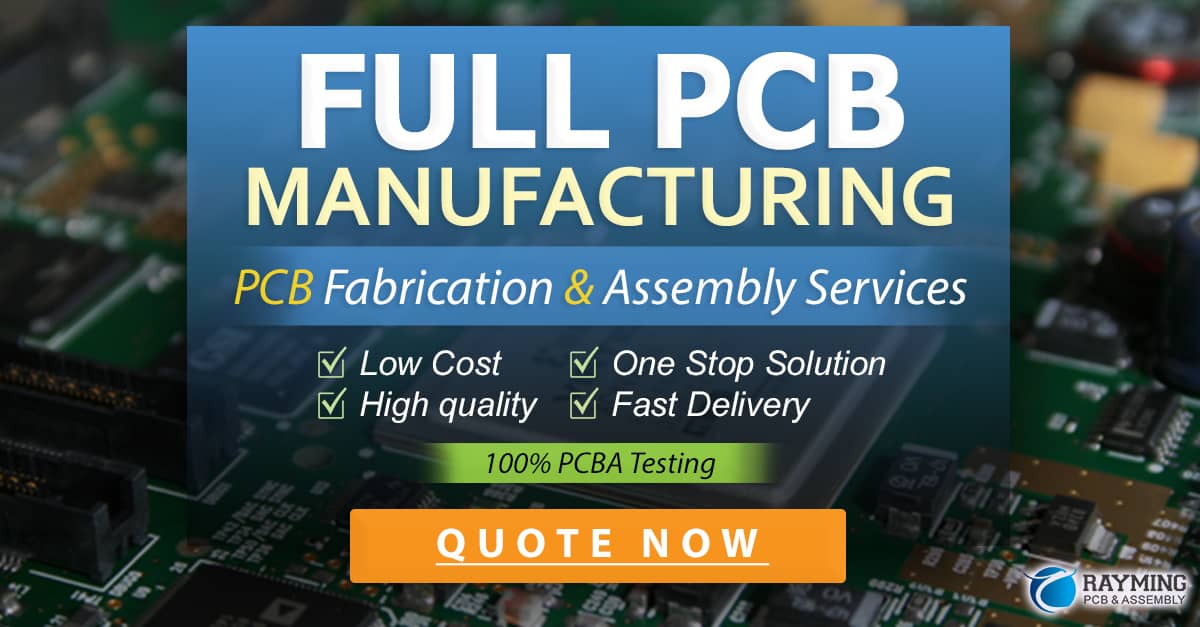
Designing Castellated PCBs
When designing castellated PCBs, there are several key considerations to keep in mind:
-
Castellation size and spacing: The size and spacing of the castellations should be carefully chosen based on the electrical and mechanical requirements of the application. Smaller castellations allow for a more compact assembly but may be more difficult to solder and may have lower current carrying capacity. Larger castellations are easier to solder and can carry higher currents but will result in a larger overall assembly.
-
Board thickness: The thickness of the PCB should be chosen based on the mechanical requirements of the application and the depth of the castellations. Thinner boards will result in shallower castellations that may be more difficult to solder, while thicker boards will have deeper castellations that provide a stronger mechanical connection.
-
Plating: The castellations should be plated with a suitable material, such as copper, gold, or tin, to provide reliable electrical connections and prevent corrosion. The plating thickness and material should be chosen based on the environmental and electrical requirements of the application.
-
Solder mask: A solder mask should be applied to the PCB to prevent solder bridging between adjacent castellations during the soldering process. The solder mask should be carefully designed to ensure that it does not cover the castellations or interfere with the soldering process.
-
Alignment features: Alignment features, such as holes or cutouts, should be incorporated into the PCB design to ensure proper alignment and orientation of the boards during assembly. These features can also provide additional mechanical support and stability to the assembly.
Manufacturing Castellated PCBs
The manufacturing process for castellated PCBs involves several key steps:
-
PCB Fabrication: The PCB is fabricated using standard PCB manufacturing techniques, such as etching, drilling, and plating. The castellations are typically created by drilling or routing holes or slots along the edge of the board and then plating them with copper.
-
Solder mask application: A solder mask is applied to the PCB to prevent solder bridging between adjacent castellations during the soldering process. The solder mask is typically applied using a screen printing or photoimaging process.
-
Surface finish: A surface finish, such as gold or tin, is applied to the castellations to provide a solderable surface and prevent corrosion. The surface finish is typically applied using an electroplating or immersion plating process.
-
Singulation: The individual boards are singulated from the panel using a routing or punching process. Care must be taken to ensure that the castellations are not damaged during the singulation process.
Assembling Castellated PCBs
Assembling castellated PCBs can be done using either hand soldering or reflow soldering techniques:
-
Hand soldering: For small-scale assemblies or prototypes, castellated PCBs can be assembled by hand soldering the boards together. This involves applying solder paste or solder wire to the castellations and then heating the solder with a soldering iron to create the electrical and mechanical connection.
-
Reflow soldering: For larger-scale production, castellated PCBs can be assembled using reflow soldering techniques. This involves applying solder paste to the castellations using a stencil or syringe and then placing the boards together in a reflow oven. The reflow oven heats the solder paste to its melting point, creating the electrical and mechanical connection between the boards.
Castellated PCB design considerations
Consideration | Description |
---|---|
Castellation size | The size of the castellations should be chosen based on the electrical and mechanical requirements of the application. Smaller castellations allow for a more compact assembly but may have lower current carrying capacity, while larger castellations can carry higher currents but will result in a larger overall assembly. |
Castellation pitch | The pitch, or spacing, between the castellations should be chosen based on the routing and component placement requirements of the PCB. A smaller pitch allows for a more compact assembly but may make routing and component placement more challenging. |
Board thickness | The thickness of the PCB should be chosen based on the mechanical requirements of the application and the depth of the castellations. Thinner boards will result in shallower castellations that may be more difficult to solder, while thicker boards will have deeper castellations that provide a stronger mechanical connection. |
Plating | The castellations should be plated with a suitable material, such as copper, gold, or tin, to provide reliable electrical connections and prevent corrosion. The plating thickness and material should be chosen based on the environmental and electrical requirements of the application. |
Solder mask | A solder mask should be applied to the PCB to prevent solder bridging between adjacent castellations during the soldering process. The solder mask should be carefully designed to ensure that it does not cover the castellations or interfere with the soldering process. |
Alignment features | Alignment features, such as holes or cutouts, should be incorporated into the PCB design to ensure proper alignment and orientation of the boards during assembly. These features can also provide additional mechanical support and stability to the assembly. |
Frequently Asked Questions
- What is the difference between a castellated PCB and a standard PCB?
A castellated PCB has a series of plated semi-circular holes or slots cut into one or more edges, which act as both electrical connections and mechanical supports. A standard PCB does not have these castellations and relies on other methods, such as connectors or wire soldering, for board-to-board connections.
- Can castellated PCBs be used for high-current applications?
Yes, castellated PCBs can be used for high-current applications, but the size and spacing of the castellations must be carefully chosen to ensure adequate current carrying capacity. Larger castellations and thicker plating can help to increase the current carrying capacity of the assembly.
- How small can the castellations be on a castellated PCB?
The minimum size of the castellations on a castellated PCB is typically limited by the manufacturing capabilities of the PCB fabricator. In general, castellations as small as 0.5mm in diameter can be reliably manufactured, but smaller castellations may be possible with advanced manufacturing techniques.
- Can castellated PCBs be used in harsh environments?
Yes, castellated PCBs can be used in harsh environments, but the design and manufacturing of the PCBs must take into account the specific environmental requirements of the application. This may include the use of special plating materials, Conformal Coatings, or other protective measures to ensure reliable operation in harsh conditions.
- Are there any limitations to using castellated PCBs?
One potential limitation of castellated PCBs is that they may not be suitable for applications that require frequent disassembly or reconfiguration, as the soldered connections between the boards can be difficult to remove without damaging the PCBs. Additionally, castellated PCBs may not be suitable for applications that require very high-speed or high-frequency signals, as the castellations can introduce impedance discontinuities or signal reflections that can degrade signal integrity.
Conclusion
Castellated PCBs offer an excellent solution for assembling multiple PCBs into a compact, reliable, and low-cost assembly. By using plated semi-circular holes or slots along the edges of the boards, castellated PCBs provide both electrical connections and mechanical support, eliminating the need for additional connectors or wires.
When designing castellated PCBs, careful consideration must be given to the size and spacing of the castellations, the thickness of the board, the plating material, the solder mask design, and the incorporation of alignment features. By carefully optimizing these design parameters, engineers can create castellated PCB assemblies that meet the specific requirements of their application, whether it be a compact wearable device, a rugged industrial sensor, or a high-performance automotive system.
As electronic devices continue to shrink in size and increase in complexity, castellated PCBs will play an increasingly important role in enabling the next generation of compact, reliable, and cost-effective electronic assemblies.
0 Comments