Introduction to Annular Rings
Annular rings are essential components in the manufacturing of printed circuit boards (PCBs). They play a crucial role in ensuring proper electrical connectivity and mechanical stability of the board. In this comprehensive guide, we will dive deep into the world of annular rings, exploring their importance, design considerations, manufacturing processes, and best practices for beginners.
What are Annular Rings?
An annular ring, also known as a pad or land, is a circular copper area surrounding a drilled hole on a PCB. The primary purpose of an annular ring is to provide a reliable electrical connection between the component lead and the copper trace on the board. Additionally, annular rings help to distribute mechanical stress around the hole, preventing damage to the board during component assembly and use.
Why are Annular Rings Important?
Annular rings are critical for several reasons:
-
Electrical Connectivity: Annular rings ensure a robust electrical connection between the component lead and the copper trace on the PCB. This is essential for the proper functioning of the electronic device.
-
Mechanical Stability: The annular ring distributes the mechanical stress around the hole, preventing the copper trace from lifting or separating from the board. This is particularly important during component assembly and when the device is subjected to vibration or shock.
-
Manufacturing Reliability: Well-designed annular rings minimize the risk of manufacturing defects, such as drill breakout or insufficient copper coverage. This leads to higher yields and lower production costs.
Annular Ring Design Considerations
Designing annular rings involves several key considerations to ensure optimal performance and manufacturability. Let’s explore these factors in detail.
Annular Ring Size
The size of the annular ring is determined by the diameter of the drilled hole and the required copper coverage around it. The minimum annular ring size is typically dictated by the manufacturing capabilities of the PCB fabricator and the industry standards, such as IPC-6012.
Hole Diameter (mm) | Minimum Annular Ring (mm) |
---|---|
0.2 – 0.4 | 0.05 |
0.4 – 0.8 | 0.075 |
0.8 – 1.5 | 0.1 |
1.5 – 3.0 | 0.15 |
Table 1: Minimum annular ring sizes based on hole diameter (IPC-6012)
It is essential to maintain a consistent annular ring size across the board to ensure uniform electrical and mechanical properties. Variations in annular ring size can lead to manufacturing issues and performance inconsistencies.
Pad Shape and Orientation
Annular rings can have different shapes and orientations depending on the component type and the design requirements. The most common pad shapes are circular, oval, and rectangular.
-
Circular Pads: These are the most widely used pad shapes and are suitable for most through-hole components. Circular pads provide uniform stress distribution and are easy to manufacture.
-
Oval Pads: Oval pads are used when additional copper coverage is required around the hole, such as for high-current applications or to accommodate larger component leads. The elongated shape allows for more copper area without increasing the overall pad size.
-
Rectangular Pads: Rectangular pads are typically used for surface-mount components, such as chip resistors and capacitors. They provide a larger contact area for the component terminations and help with alignment during assembly.
The orientation of the pads should be consistent with the component placement and the board layout. Proper pad orientation ensures correct component alignment and minimizes the risk of assembly errors.
Copper Thickness and Plating
The copper thickness and plating of the annular rings are critical factors in ensuring reliable electrical connections and mechanical strength.
-
Copper Thickness: The copper thickness of the annular ring should be sufficient to carry the required electrical current and withstand the mechanical stresses during assembly and use. The typical copper thickness for PCBs ranges from 0.5 oz to 2 oz (17.5 μm to 70 μm).
-
Plating: Annular rings are often plated with a protective finish to prevent oxidation and improve solderability. Common plating options include hot air solder leveling (HASL), immersion silver, and electroless nickel immersion gold (ENIG). The choice of plating depends on the application requirements, such as environmental conditions, shelf life, and assembly process.
Solder Mask and Clearance
Solder mask is a protective coating applied over the copper traces and pads on the PCB. It helps to prevent solder bridging and short circuits during assembly. When designing annular rings, it is essential to consider the solder mask clearance and coverage.
-
Solder Mask Clearance: Solder mask clearance refers to the distance between the edge of the annular ring and the opening in the solder mask. The clearance should be sufficient to ensure proper solder wetting and prevent solder mask from encroaching on the pad area. The typical solder mask clearance is 0.05 mm to 0.1 mm, depending on the manufacturing capabilities.
-
Solder Mask Coverage: The solder mask should cover the annular ring area that is not intended for soldering. This helps to prevent solder from spreading beyond the pad area and causing short circuits. The solder mask coverage should be consistent across the board to ensure uniform soldering results.
Manufacturing Processes for Annular Rings
The manufacturing of annular rings involves several key processes that impact the quality and reliability of the PCB. Let’s explore these processes in detail.
Drilling
Drilling is the first step in creating annular rings. The holes are drilled through the PCB substrate using a computer numerical control (CNC) drilling machine. The accuracy and precision of the drilling process are critical for ensuring proper annular ring formation.
-
Drill Bit Selection: The choice of drill bit depends on the hole size, material, and required hole quality. Carbide drill bits are commonly used for PCB Drilling due to their high wear resistance and precision.
-
Drilling Parameters: The drilling parameters, such as spindle speed, feed rate, and depth of cut, should be optimized to minimize drill wander and breakout. Improper drilling parameters can lead to oversized or misaligned holes, affecting the annular ring size and shape.
-
Hole Cleaning: After drilling, the holes must be cleaned to remove any debris or burrs. This is typically done using a deburring or desmearing process, which ensures a clean and smooth hole surface for proper copper plating.
Copper Plating
Once the holes are drilled and cleaned, the next step is to plate them with copper to form the annular rings. The copper plating process involves several sub-processes, including:
-
Electroless Copper: An initial layer of copper is deposited onto the hole walls using an electroless plating process. This thin layer of copper acts as a conductive seed layer for the subsequent electrolytic plating.
-
Electrolytic Copper: The bulk of the copper is deposited using an electrolytic plating process. The PCB is immersed in a copper sulfate solution, and an electric current is applied to deposit copper onto the hole walls and surface of the board. The thickness of the electrolytic copper layer determines the final copper thickness of the annular rings.
-
Copper Balancing: After electrolytic plating, a copper balancing process is performed to ensure uniform copper thickness across the board. This involves selectively etching or plating copper in specific areas to achieve the desired thickness distribution.
Etching and Solder Mask Application
After copper plating, the next steps are etching and solder mask application. These processes define the final shape and size of the annular rings.
-
Etching: The unwanted copper areas on the board are removed using a chemical etching process. The etching process selectively removes copper from the areas not protected by the etch resist, leaving behind the desired copper patterns, including the annular rings.
-
Solder Mask Application: The solder mask is applied over the copper traces and pads, leaving openings for the annular rings and other areas intended for soldering. The solder mask application process involves screen printing or photoimaging the solder mask material onto the board, followed by curing and developing.
Inspection and Testing
Inspection and testing are critical steps in ensuring the quality and reliability of the annular rings. Visual inspection is performed to check for any defects, such as oversized or undersized annular rings, copper lifting, or solder mask violations.
Electrical testing, such as continuity and insulation resistance tests, is conducted to verify the electrical integrity of the annular rings and the overall PCB. These tests help to identify any manufacturing defects or design issues that may affect the performance of the final product.
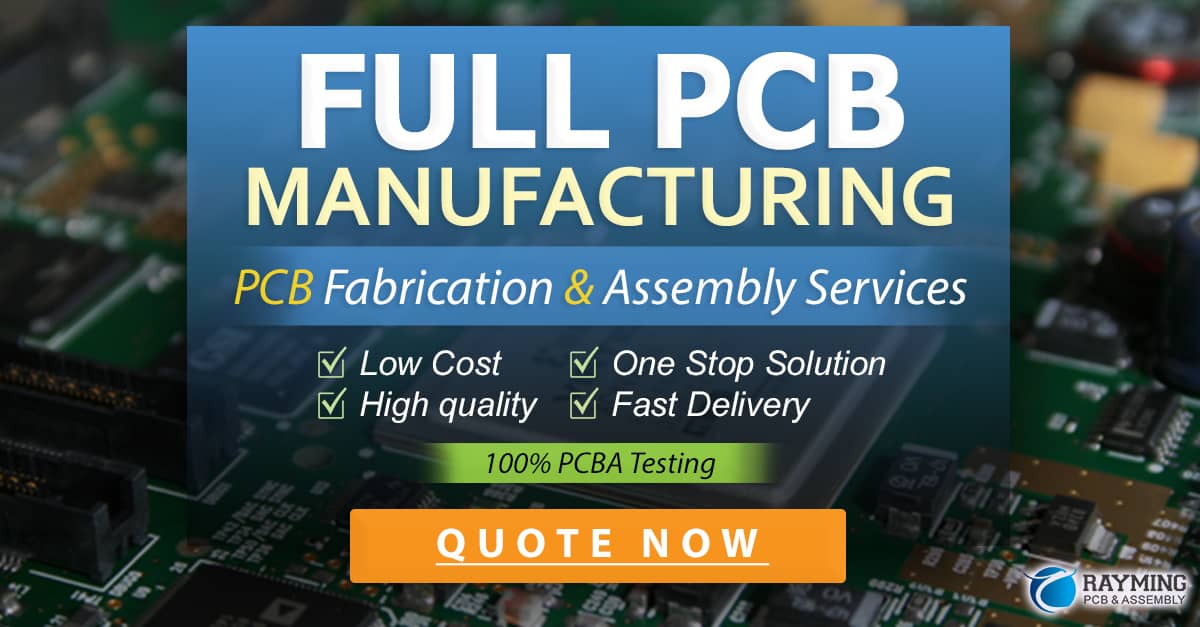
Best Practices for Annular Ring Design and Manufacturing
To ensure optimal annular ring performance and manufacturability, consider the following best practices:
-
Follow Industry Standards: Adhere to industry standards, such as IPC-6012, for annular ring design and manufacturing. These standards provide guidelines for minimum annular ring size, copper thickness, and other critical parameters.
-
Collaborate with PCB Fabricators: Work closely with your PCB fabricator to understand their manufacturing capabilities and limitations. This collaboration helps to ensure that your annular ring design is compatible with their processes and can be manufactured reliably.
-
Use Design for Manufacturing (DFM) Tools: Utilize DFM tools to analyze your PCB design and identify any potential manufacturing issues related to annular rings. These tools can help to optimize your design for manufacturability and minimize the risk of defects.
-
Implement Robust Quality Control: Establish a robust quality control process to monitor and maintain the quality of the annular rings throughout the manufacturing process. This includes regular inspections, testing, and data analysis to identify and correct any issues promptly.
-
Consider the End-Use Environment: When designing annular rings, consider the end-use environment of the PCB. Factors such as temperature, humidity, and vibration can impact the performance and reliability of the annular rings. Design your annular rings to withstand the expected environmental conditions.
Frequently Asked Questions (FAQs)
-
What is the minimum annular ring size for a given hole diameter?
The minimum annular ring size depends on the hole diameter and the manufacturing capabilities of the PCB fabricator. Refer to industry standards, such as IPC-6012, for guidelines on minimum annular ring sizes. For example, a hole diameter of 0.8 mm to 1.5 mm typically requires a minimum annular ring of 0.1 mm. -
Can I use different annular ring sizes on the same board?
While it is possible to use different annular ring sizes on the same board, it is generally recommended to maintain a consistent annular ring size for all holes of the same diameter. This ensures uniform electrical and mechanical properties across the board and simplifies the manufacturing process. -
What is the purpose of solder mask clearance for annular rings?
Solder mask clearance is the distance between the edge of the annular ring and the opening in the solder mask. It serves two main purposes: (1) to ensure proper solder wetting of the annular ring during assembly, and (2) to prevent solder mask from encroaching on the pad area, which can lead to soldering issues. -
How does copper thickness affect annular ring performance?
Copper thickness is a critical factor in the electrical and mechanical performance of annular rings. Thicker copper provides better current carrying capacity and mechanical strength. However, excessive copper thickness can lead to manufacturing challenges, such as difficulty in drilling and plating. It is essential to strike a balance between performance and manufacturability when selecting the copper thickness for your annular rings. -
What are the common defects associated with annular rings, and how can they be prevented?
Common defects associated with annular rings include oversized or undersized annular rings, copper lifting, solder mask violations, and insufficient solder wetting. These defects can be prevented by following best practices in annular ring design and manufacturing, such as adhering to industry standards, collaborating with PCB fabricators, using DFM tools, implementing robust quality control, and considering the end-use environment.
Conclusion
Annular rings are critical components in PCB manufacturing, ensuring reliable electrical connectivity and mechanical stability. By understanding the design considerations, manufacturing processes, and best practices associated with annular rings, beginners can create robust and manufacturable PCB designs.
Remember to collaborate closely with your PCB fabricator, follow industry standards, and implement a strong quality control process to ensure the success of your annular ring design and manufacturing. With the knowledge gained from this comprehensive guide, you are well-equipped to tackle your next PCB project with confidence.
0 Comments