What is Back Drilling in PCB Fabrication?
Back drilling, also known as controlled depth drilling or depth controlled drilling, is a PCB Drilling technique used to remove the unused portion of a plated through hole (PTH) in multilayer printed circuit boards. The main purpose of back drilling is to improve the signal integrity of high-speed designs by reducing the stub length in the PTH.
In a typical multilayer PCB, the Plated Through Holes extend through the entire thickness of the board, even if the connection is only required on certain layers. The unused portion of the PTH, called the stub, acts as an unterminated transmission line, which can cause signal reflections and degrade the overall signal quality.
How Back Drilling Works
The back drilling process involves drilling a larger diameter hole from the backside of the PCB to remove the stub portion of the PTH. The depth of the back drill is precisely controlled to reach just above the last layer that requires the PTH connection, effectively eliminating the unused portion of the hole.
The back drilling process typically follows these steps:
- The PCB is first drilled with the standard PTH sizes required for the design.
- The board is then flipped over, and a larger diameter drill bit is used to remove the stub portion of the PTH from the backside of the board.
- The depth of the back drill is carefully controlled to ensure that it reaches just above the last required layer without damaging the PTH connection.
Importance of Back Drilling in High-Speed PCB Design
Signal Integrity Improvement
The primary reason for using back drilling in PCB fabrication is to improve signal integrity in high-speed designs. As the operating frequencies of electronic devices continue to increase, the impact of signal reflections caused by PTH stubs becomes more significant.
The stub portion of the PTH acts as an unterminated transmission line, which can cause several signal integrity issues:
-
Signal Reflections: When a high-speed signal encounters an unterminated stub, a portion of the signal energy is reflected back towards the source, causing signal distortion and reducing the overall signal quality.
-
Impedance Mismatch: The presence of the stub can create an impedance mismatch, leading to further signal reflections and degradation.
-
Resonance: The stub can also cause resonance effects, where the reflected signal energy constructively interferes with the original signal, leading to signal overshoots and undershoots.
By removing the stub portion of the PTH through back drilling, these signal integrity issues can be significantly reduced, resulting in cleaner and more reliable high-speed signal transmission.
Improved Timing and Reduced Jitter
In high-speed digital systems, timing and jitter are critical factors that can impact the overall system performance. The presence of PTH stubs can contribute to timing errors and increased jitter due to the signal reflections and distortions caused by the stubs.
By eliminating the stubs through back drilling, the signal path becomes more consistent and predictable, reducing the impact of signal reflections on timing and jitter. This improvement can be particularly important in applications such as high-speed serial communication, where even small timing errors can lead to data corruption or link failures.
Design Considerations for Back Drilling
Identifying Signals for Back Drilling
Not all signals in a PCB design require back drilling. Typically, back drilling is used for high-speed signals that are sensitive to the effects of PTH stubs. These signals may include:
- High-speed digital interfaces such as PCIe, USB, SATA, etc.
- High-frequency analog signals
- Differential pairs used for high-speed communication
During the PCB design process, it is essential to identify the signals that would benefit from back drilling and clearly communicate this information to the fabrication house.
Back Drill Depth Control
The depth of the back drill is a critical factor in ensuring the effectiveness of the technique. The back drill must remove the maximum amount of the stub without damaging the PTH connection on the last required layer.
Typically, the back drill depth is specified as a distance from the backside of the PCB to the last required layer. This distance, known as the “stub depth,” must be carefully calculated based on the PCB Stackup and the location of the signal layers.
Layer | Thickness (mm) | Cumulative Thickness (mm) |
---|---|---|
Top Copper | 0.035 | 0.035 |
Prepreg | 0.2 | 0.235 |
Inner Layer 1 | 0.035 | 0.27 |
Core | 0.5 | 0.77 |
Inner Layer 2 | 0.035 | 0.805 |
Prepreg | 0.2 | 1.005 |
Bottom Copper | 0.035 | 1.04 |
For example, consider a 4-layer PCB with the stackup shown in the table above. If a signal on Inner Layer 1 requires back drilling, the stub depth would be calculated as follows:
Stub Depth = Total PCB Thickness – Cumulative Thickness up to Inner Layer 1
Stub Depth = 1.04 mm – 0.27 mm = 0.77 mm
It is important to communicate the stub depth information clearly to the fabrication house to ensure accurate back drilling.
Pad and Via Size Considerations
When designing for back drilling, it is essential to consider the sizes of the pads and vias used for the PTH connections. The back drill diameter must be larger than the pad diameter to ensure complete removal of the stub.
However, increasing the back drill diameter also increases the risk of damaging nearby traces or components on the PCB. Therefore, it is crucial to find a balance between the back drill diameter and the pad size to ensure effective stub removal without compromising the PCB layout.
As a general guideline, the back drill diameter should be at least 0.1 mm larger than the pad diameter. For example, if a PTH has a pad diameter of 0.5 mm, the back drill diameter should be at least 0.6 mm.
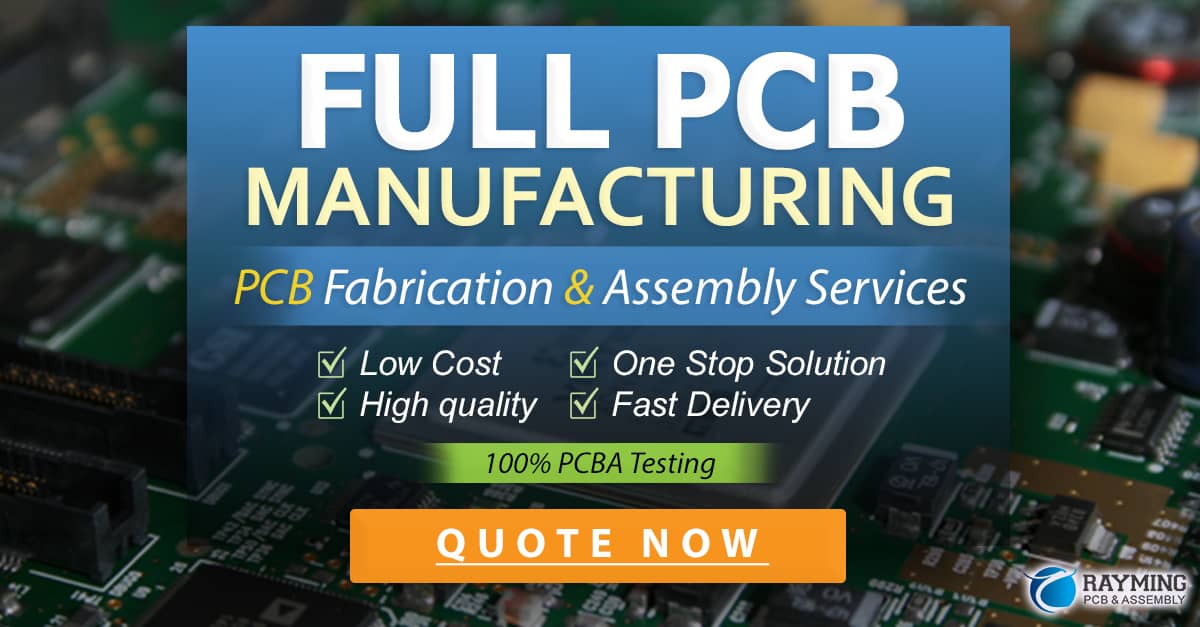
Back Drilling and PCB Manufacturing Process
Additional Processing Steps
Back drilling introduces additional processing steps in the PCB manufacturing process, which can impact the overall production time and cost. The main steps involved in back drilling include:
- Drilling the standard PTH sizes
- Flipping the board and setting up the back drill machine
- Performing the back drilling operation
- Cleaning the back drilled holes to remove any debris
These additional steps require specialized equipment and expertise, which may not be available at all PCB fabrication houses.
Increased Manufacturing Cost and Time
Due to the additional processing steps and the need for specialized equipment, back drilling can increase the overall manufacturing cost and lead time for a PCB.
The cost impact of back drilling depends on several factors, such as the number of holes to be back drilled, the PCB size, and the overall complexity of the design. On average, the addition of back drilling can increase the PCB fabrication cost by 10-20%.
Similarly, the additional processing steps can add to the overall manufacturing time. The back drilling process itself may not take a significant amount of time, but the setup and cleaning steps can contribute to the increased lead time. On average, back drilling can increase the PCB manufacturing lead time by 1-2 days.
Communication with PCB Fabrication House
To ensure successful implementation of back drilling in a PCB design, it is crucial to communicate clearly with the PCB fabrication house. The following information should be provided to the fabricator:
- The specific holes or nets that require back drilling
- The stub depth for each back drilled hole
- The desired back drill diameter
- Any special requirements or constraints related to back drilling
Clear communication helps the fabricator understand the design intent and ensures that the back drilling process is carried out correctly, meeting the specified requirements.
Alternatives to Back Drilling
While back drilling is an effective technique for improving signal integrity in high-speed PCB designs, there are alternatives that can be considered in certain situations.
Blind and Buried Vias
One alternative to back drilling is the use of blind and buried vias. Blind vias are drilled from one side of the PCB and terminate at an inner layer, while buried vias are located entirely within the inner layers of the PCB.
Using blind and buried vias can eliminate the need for back drilling, as the vias do not extend through the entire thickness of the board, thus avoiding the creation of stubs. However, blind and buried vias are more expensive to manufacture and can increase the overall complexity of the PCB design.
Optimized PCB Stackup
Another approach to minimizing the impact of PTH stubs is to optimize the PCB stackup. By carefully arranging the signal layers and minimizing the distance between the signal layers and the end of the PTH, the stub length can be reduced, thus mitigating the signal integrity issues.
However, optimizing the stackup may not always be possible due to other design constraints, such as the need for specific layer arrangements or the presence of components with fixed pin assignments.
Frequently Asked Questions (FAQ)
-
What is the purpose of back drilling in PCB fabrication?
Back drilling is used to remove the unused portion of a plated through hole (PTH) in multilayer PCBs, known as the stub. By eliminating the stub, back drilling improves signal integrity and reduces signal reflections in high-speed designs. -
How does back drilling improve signal integrity?
The stub portion of a PTH acts as an unterminated transmission line, causing signal reflections, impedance mismatches, and resonance effects. By removing the stub through back drilling, these signal integrity issues are minimized, resulting in cleaner and more reliable high-speed signal transmission. -
What signals typically require back drilling?
High-speed signals that are sensitive to the effects of PTH stubs often require back drilling. These can include high-speed digital interfaces (e.g., PCIe, USB, SATA), high-frequency analog signals, and differential pairs used for high-speed communication. -
How does back drilling affect the PCB manufacturing process?
Back drilling introduces additional processing steps in PCB manufacturing, such as drilling the standard PTH sizes, setting up the back drill machine, performing the back drilling operation, and cleaning the back drilled holes. These extra steps can increase the overall manufacturing cost and lead time. -
Are there any alternatives to back drilling?
Yes, alternatives to back drilling include the use of blind and buried vias, which do not extend through the entire thickness of the board, and optimizing the PCB stackup to minimize the distance between the signal layers and the end of the PTH. However, these alternatives may have their own limitations and cost implications.
0 Comments