Introduction
SMT (surface mount technology) assembly machines are vital pieces of equipment in modern electronics manufacturing. As products continue to get smaller and more complex, SMT machines allow for the accurate, high-speed placement of surface mount components onto PCBs (printed circuit boards). In this guide, we’ll explore the key features and considerations when investing in SMT equipment.
How SMT Assembly Machines Work
SMT assembly machines use advanced automation to precisely pick electronic components from reels or trays and place them onto solder paste-coated PCBs. Here is a high-level overview of the SMT assembly process:
- PCB Loading: The bare PCB is loaded into the machine and held in place by a specialized conveyor system.
- Solder Paste Deposition: The machine uses a stencil to apply an even layer of solder paste to the contact pads on the PCB.
- Component Placement: Feeders provide a constant supply of components which are picked and placed onto the solder paste. High-speed, high-precision robots or gantries handle the placement.
- Solder Reflow: Once all components are placed, the PCB passes through a reflow oven to melt the solder and permanently attach the components.
- Inspection: Automated optical inspection validates the quality of solder joints and component placement.
Major Components of SMT Assembly Machines
SMT assembly equipment consists of several key subsystems:
- Conveyor: Transports PCBs smoothly through the assembly line.
- Solder Paste Printer: Deposits solder paste on the PCB through a stencil.
- Pick and Place Head: Picks components from feeders and places them on the PCB with extreme precision.
- Feeders: Tape, stick, or tray feeders that constantly supply components to the pick-and-place head.
- Reflow Oven: Solder paste is melted to form reliable solder joints and permanently attach components.
- PCB Handling: Mechanisms to load, support, and unload PCBs.
- Vision and Inspection System: Optical inspection of component placement, solder joints, etc.
Key Specifications and Considerations
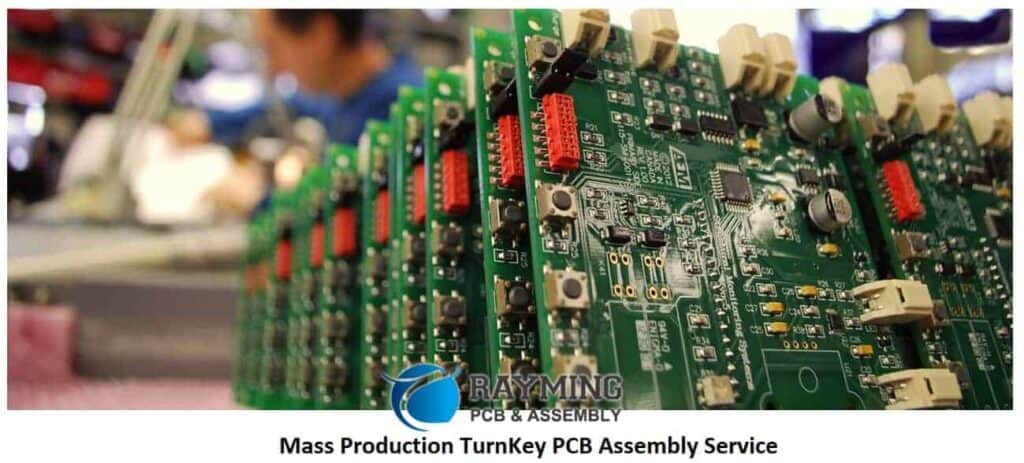
Selecting the right SMT equipment depends on many factors. Here are some key specifications and criteria to evaluate:
Placement Speed
- High-speed pick-and-place improves overall throughput.
- Measure placement speed in components per hour (CPH).
- Top-end machines can achieve 150,000+ CPH.
Placement Accuracy
- Precision component placement minimizes defects.
- Accuracy is measured in terms of repeatability and variance from programmed position.
- Leading machines can achieve under 10μm accuracy.
Feeder Capacity
- More feeder slots means supporting more component types.
- High-mix lines require 300+ feeder capacity.
- Large-volume lines optimize changeovers with fewer, larger feeders.
Board Size Capability
- The machine’s x-y size envelope limits maximum PCB size.
- Standard machines support 305mm x 457mm.
- Larger formats are available for bigger boards.
Changeover Time
- Minimizing changeover times boosts flexibility.
- Automated feeder carts, tape feeders, offline programming software all help.
- Leading edge under 10 minutes for full setup.
Software and Programming
- Intuitive software interfaces minimize programming time.
- Support for CAD, Gerber, IPC-2581 speeds data preparation.
- Programming can be done offline to boost utilization.
Specification | Entry-level | Mid-range | High-end |
---|---|---|---|
Placement speed | 20,000 CPH | 60,000 CPH | 150,000+ CPH |
Accuracy | 50μm | 25μm | 10μm |
Feeder capacity | 60 | 180 | 500+ |
Max board size | 250 x 300mm | 406 x 305mm | 610 x 510mm |
Setup time | 30+ minutes | 10-15 minutes | <10 minutes |
Advanced Features
Today’s most advanced SMT assembly machines incorporate technologies to handle cutting-edge manufacturing needs:
Multi-Gantry Design
- Independent gantries boost throughput via parallel processing.
- Dual-gantry machines double output over single gantry.
Advanced Optics and Lighting
- Telecentric optics minimize placement errors.
- Programmable lighting simplifies inspection programs.
Integrated 3D SPI
- 3D solder paste inspection validates printing quality.
- Reduces defects by catching paste print issues early.
Robotic Material Handling
- Automated material towers manage PCBs and feeders.
- Reduces changeover time and labor requirements.
Force-Controlled Placement
- Closed-loop force monitoring improves odd-form placement.
- Prevents damage to fragile components during placement.
Buying Considerations
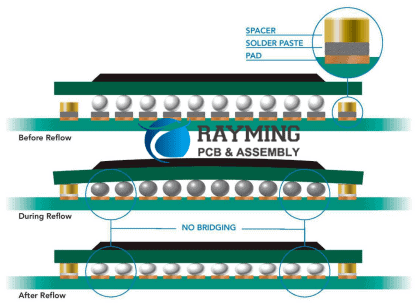
Here are some tips when shopping for SMT placement machines:
- Evaluate suppliers based on experience, reputation, and service/support capabilities. Look for strong application expertise.
- Consider total cost of ownership, not just purchase price. Factors like changeover time, yield, programming complexity, and maintenance all impact long-term costs.
- Validate machine capabilities and accuracy by seeing a demo and assessing sample builds. Don’t rely on specs alone.
- Carefully plan required capacity and expansion. Consider bottlenecks like feeding components, inspection, and reflow.
- Assess software and programming factors like CAD support, library elements, offline programming options, and ease of use.
- Determine if in-house capacity or outsourcing makes more sense based on production volumes and complexity.
Conclusion
SMT assembly equipment is a major investment, but advanced automation pays dividends through faster cycle times, lower labor requirements, and minimal defects. As products shrink in size, SMT will only grow in prominence. By selecting the right solution and supplier, manufacturers can build a highly agile, optimized production line to gain a true competitive advantage. With smart planning, surface mount technology promises a bright future.
Frequently Asked Questions
What is the difference between SMT and through-hole assembly?
With SMT, components are mounted directly onto the surface of the PCB. Through-hole components have leads that puncture the PCB and are soldered on the reverse side. SMT allows for smaller, lighter, and higher-density PCBs.
Can the same machine place 01005 components and large QFPs?
The best SMT machines can handle the broadest range of component sizes from ultra-fine chips up to large plastic packages. Wide component clearance, good lighting, and precision mechanics are key.
How often should we run production boards for process validation?
It’s wise to revalidate key products quarterly or semiannually. Running current boards gives early warning of potential issues before defects occur. It also provides data on factors like paste volume and reflow profiles.
What is head impact force and why does it matter?
Head impact force is the amount of downward pressure the pick-and-place head exerts on the component. Excessive force can damage fragile components. Look for machines with closed-loop force monitoring.
Should we hire in-house machine operators or rely on the machine supplier?
For the initial bring-up, suppliers provide expert operators. But for production, most OEMs recommend developing in-house staff. Well-trained operators ensure optimal utilization plus flexibility for model changeovers.
0 Comments