Introduction to ATE PCB Assembly as the PCB-OEM Interface
In the world of electronic manufacturing, the relationship between printed circuit board (PCB) manufacturers and original equipment manufacturers (OEMs) is crucial for the successful production of high-quality electronic devices. One key aspect that facilitates this relationship is the use of automated test equipment (ATE) in PCB assembly. ATE PCB assembly serves as the trusted interface between PCB manufacturers and OEMs, ensuring that the manufactured PCBs meet the required specifications and perform optimally in the final product.
What is ATE PCB Assembly?
ATE PCB assembly refers to the process of using automated test equipment to assemble and test PCBs during the manufacturing process. This equipment is designed to handle various aspects of PCB assembly, including component placement, soldering, and testing. By automating these processes, ATE PCB assembly offers several benefits, such as increased efficiency, accuracy, and consistency in the manufacturing process.
The Role of ATE PCB Assembly in the PCB-OEM Relationship
ATE PCB assembly plays a vital role in the relationship between PCB manufacturers and OEMs. It serves as a common language and a set of standards that both parties can rely on to ensure the quality and functionality of the manufactured PCBs. Some of the key roles of ATE PCB assembly in this relationship include:
- Quality assurance
- Standardization
- Cost-effectiveness
- Faster time-to-market
The Benefits of ATE PCB Assembly for PCB Manufacturers
For PCB manufacturers, implementing ATE PCB assembly offers several advantages that can help improve their manufacturing process and strengthen their relationship with OEMs.
Increased Efficiency and Productivity
One of the primary benefits of ATE PCB assembly for PCB manufacturers is increased efficiency and productivity. By automating various aspects of the assembly process, manufacturers can significantly reduce the time and labor required to produce PCBs. This, in turn, allows them to handle larger production volumes and meet the growing demands of OEMs.
Improved Quality and Consistency
ATE PCB assembly also helps PCB manufacturers improve the quality and consistency of their products. Automated equipment is capable of placing components with high precision and accuracy, reducing the risk of human error. Additionally, automated testing ensures that each PCB meets the required specifications and performs as expected, minimizing the chances of defective products reaching the OEM.
Cost Reduction
Implementing ATE PCB assembly can help PCB manufacturers reduce their production costs in several ways. First, the increased efficiency and productivity offered by automation can lower labor costs and minimize waste. Second, the improved quality and consistency of the manufactured PCBs can reduce the need for rework and repairs, further cutting down on expenses.
Enhanced Flexibility and Scalability
ATE PCB assembly also provides PCB manufacturers with enhanced flexibility and scalability in their production process. Automated equipment can be easily reprogrammed to handle different PCB designs and specifications, allowing manufacturers to quickly adapt to changing OEM requirements. Moreover, the scalability of ATE systems enables manufacturers to easily expand their production capacity as their business grows.
The Benefits of ATE PCB Assembly for OEMs
For OEMs, working with PCB manufacturers that utilize ATE PCB assembly offers several benefits that can help them create high-quality, reliable electronic devices.
Assured Product Quality
One of the most significant advantages of ATE PCB assembly for OEMs is the assurance of product quality. By relying on automated testing and assembly processes, OEMs can be confident that the PCBs they receive from manufacturers meet their specified requirements and will perform optimally in their final products. This, in turn, helps reduce the risk of product failures and enhances customer satisfaction.
Faster Time-to-Market
ATE PCB assembly can also help OEMs bring their products to market faster. The increased efficiency and productivity offered by automation allow PCB manufacturers to deliver PCBs more quickly, reducing lead times for OEMs. This can be particularly beneficial in industries where time-to-market is a critical factor, such as consumer electronics and automotive.
Cost Savings
Working with PCB manufacturers that employ ATE PCB assembly can also result in cost savings for OEMs. The improved quality and consistency of the manufactured PCBs can reduce the need for rework and repairs, lowering overall production costs. Additionally, the increased efficiency and productivity of automated assembly can help PCB manufacturers offer more competitive pricing to OEMs.
Access to Advanced Technology
ATE PCB assembly also provides OEMs with access to advanced technology and capabilities that may not be available through manual assembly processes. Automated equipment can handle complex PCB designs and advanced components, enabling OEMs to create more sophisticated and innovative electronic devices.
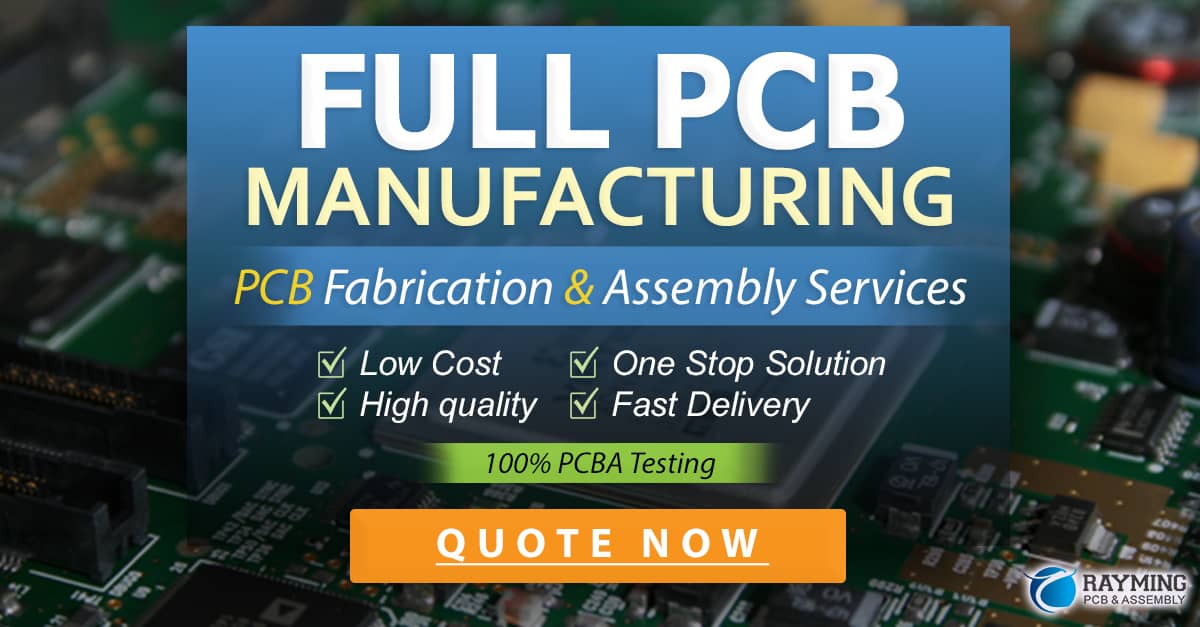
Key Considerations for Successful ATE PCB Assembly Implementation
To ensure the successful implementation of ATE PCB assembly and maintain a strong PCB-OEM interface, both PCB manufacturers and OEMs should consider several key factors.
Effective Communication and Collaboration
Effective communication and collaboration between PCB manufacturers and OEMs are essential for the successful implementation of ATE PCB assembly. Both parties should work together to establish clear requirements, specifications, and testing procedures to ensure that the manufactured PCBs meet the OEM’s needs. Regular communication and feedback can help identify and resolve any issues quickly, maintaining a smooth production process.
Standardization and Documentation
Standardization and documentation are also crucial for successful ATE PCB assembly implementation. PCB manufacturers and OEMs should agree on a set of standards and specifications for the PCBs, including design rules, component selection, and testing requirements. These standards should be clearly documented and easily accessible to both parties to ensure consistency and minimize misunderstandings.
Continuous Improvement and Optimization
Continuous improvement and optimization are key to maintaining a strong PCB-OEM interface through ATE PCB assembly. PCB manufacturers should continuously monitor and analyze their assembly processes to identify areas for improvement and implement necessary changes. OEMs should provide regular feedback on the performance of the manufactured PCBs and work with manufacturers to optimize designs and specifications for better results.
Training and Skill Development
Investing in training and skill development is essential for the successful implementation of ATE PCB assembly. PCB manufacturers should ensure that their personnel are well-trained in the operation and maintenance of automated equipment, as well as in quality control and testing procedures. OEMs should also have a good understanding of the capabilities and limitations of ATE PCB assembly to ensure that their designs are compatible with the manufacturing process.
Real-World Examples of Successful ATE PCB Assembly Implementation
To illustrate the benefits of ATE PCB assembly in the PCB-OEM interface, let’s look at some real-world examples of successful implementation.
Example 1: Consumer Electronics Manufacturer
A leading consumer electronics manufacturer partnered with a PCB manufacturer that utilizes ATE PCB assembly to produce the PCBs for their latest smartphone model. By leveraging the efficiency and accuracy of automated assembly, the PCB manufacturer was able to deliver high-quality PCBs in a shorter timeframe, enabling the OEM to bring their product to market faster. The improved quality and reliability of the PCBs also resulted in fewer product returns and higher customer satisfaction.
Example 2: Automotive Supplier
An automotive supplier collaborated with a PCB manufacturer that employs ATE PCB assembly to produce the PCBs for their advanced driver assistance systems (ADAS). The automated assembly process allowed the PCB manufacturer to handle the complex designs and strict quality requirements of the automotive industry. The resulting PCBs demonstrated excellent performance and reliability, helping the automotive supplier meet the rigorous safety standards and maintain their competitive edge in the market.
Example 3: Medical Device Company
A medical device company worked with a PCB manufacturer that uses ATE PCB assembly to produce the PCBs for their life-critical medical devices. The automated assembly and testing processes ensured that the PCBs met the stringent quality and reliability requirements of the medical industry. By partnering with a PCB manufacturer that utilizes ATE PCB assembly, the medical device company was able to create innovative and reliable products that improve patient outcomes and save lives.
The Future of ATE PCB Assembly in the PCB-OEM Interface
As technology continues to advance and the demand for more complex and reliable electronic devices grows, the role of ATE PCB assembly in the PCB-OEM interface is expected to become even more critical.
Advancements in Automation Technology
The future of ATE PCB assembly will be shaped by advancements in automation technology. As automated equipment becomes more sophisticated and intelligent, PCB manufacturers will be able to handle even more complex PCB designs and components with greater efficiency and accuracy. This will enable OEMs to create more innovative and advanced electronic devices that meet the evolving needs of their customers.
Increased Adoption of Industry 4.0 Principles
The adoption of Industry 4.0 principles, such as the Internet of Things (IoT), artificial intelligence (AI), and big data analytics, will also have a significant impact on the future of ATE PCB assembly. By integrating these technologies into their assembly processes, PCB manufacturers can collect and analyze real-time data to optimize their operations, predict and prevent potential issues, and improve overall equipment effectiveness (OEE).
Growing Importance of Sustainability
Sustainability will also play a growing role in the future of ATE PCB assembly and the PCB-OEM interface. As environmental concerns and regulations become more pressing, both PCB manufacturers and OEMs will need to adopt more sustainable practices in their production processes. ATE PCB assembly can contribute to sustainability by reducing waste, minimizing energy consumption, and enabling the use of eco-friendly materials and components.
Continued Emphasis on Quality and Reliability
Despite the advancements in technology and the growing focus on sustainability, quality and reliability will remain the top priorities in the future of ATE PCB assembly and the PCB-OEM interface. Both PCB manufacturers and OEMs will need to continue investing in quality control and testing processes to ensure that the manufactured PCBs meet the highest standards of performance and durability.
Frequently Asked Questions (FAQs)
-
What is the difference between manual and automated PCB assembly?
Manual PCB assembly involves human operators placing components and soldering them onto the PCB by hand, while automated PCB assembly uses machines to place components and solder them onto the PCB with minimal human intervention. Automated assembly offers greater speed, accuracy, and consistency compared to manual assembly. -
How does ATE PCB assembly ensure the quality of manufactured PCBs?
ATE PCB assembly ensures the quality of manufactured PCBs through automated testing processes. These processes include in-circuit testing (ICT), flying probe testing, and functional testing, which verify that the PCBs meet the specified requirements and perform as expected. Automated testing helps identify and eliminate defects early in the production process, reducing the risk of faulty products reaching the OEM. -
What are the main challenges in implementing ATE PCB assembly?
Some of the main challenges in implementing ATE PCB assembly include the initial investment in equipment and infrastructure, the need for skilled personnel to operate and maintain the automated systems, and the potential for compatibility issues between the PCB design and the automated assembly process. Effective communication and collaboration between PCB manufacturers and OEMs can help overcome these challenges and ensure successful implementation. -
How can OEMs ensure that their PCB designs are compatible with ATE PCB assembly?
OEMs can ensure that their PCB designs are compatible with ATE PCB assembly by following established design guidelines and standards, such as the IPC standards for PCB design and manufacturing. They should also communicate closely with their PCB manufacturer to understand the capabilities and limitations of their automated assembly processes and make any necessary adjustments to their designs. -
What is the future outlook for ATE PCB assembly in the electronics industry?
The future outlook for ATE PCB assembly in the electronics industry is positive, as the demand for high-quality, reliable, and complex electronic devices continues to grow. Advancements in automation technology, the adoption of Industry 4.0 principles, and the growing importance of sustainability are expected to drive further innovation and growth in ATE PCB assembly, strengthening its role as the trusted interface between PCB manufacturers and OEMs.
Conclusion
ATE PCB assembly serves as the trusted interface between PCB manufacturers and OEMs, enabling the production of high-quality, reliable, and complex electronic devices. By automating the assembly and testing processes, ATE PCB assembly offers numerous benefits, including increased efficiency, improved quality and consistency, cost reduction, and faster time-to-market.
To ensure the successful implementation of ATE PCB assembly and maintain a strong PCB-OEM interface, both PCB manufacturers and OEMs must prioritize effective communication and collaboration, standardization and documentation, continuous improvement and optimization, and training and skill development.
As technology advances and the electronics industry evolves, the role of ATE PCB assembly in the PCB-OEM interface will become even more critical. By embracing advancements in automation technology, adopting Industry 4.0 principles, and prioritizing sustainability and quality, PCB manufacturers and OEMs can continue to leverage the power of ATE PCB assembly to create innovative, reliable, and high-performing electronic devices that meet the ever-changing needs of their customers.
0 Comments