Pick and place machines are essential for automating the assembly of printed circuit boards (PCBs) in the electronics manufacturing industry. Selecting the right pick and place machine manufacturer is key to improving production efficiency, quality, and reducing costs. This article provides an overview of leading global pick and place machine manufacturers, their key technologies, and solutions for smart factory automation.
Overview of Pick and Place Machines
A pick and place machine, also known as a PNP machine or SMT placement equipment, automatically positions and places surface mount technology (SMT) components onto PCBs during the SMT assembly process. The key parts of a PNP machine include:
- Feeders – hold components like resistors, capacitors, ICs
- Placement heads – use suction to pick components and place them on boards
- Transport system – moves PCBs into position
- Vision systems – align components and boards
Modern pick and place systems are highly flexible and can place thousands of components per hour onto PCBs autonomously using advanced software and vision systems. This automation enables electronics manufacturers to scale up production and improve consistency.
Leading SMT Pick and Place Manufacturers
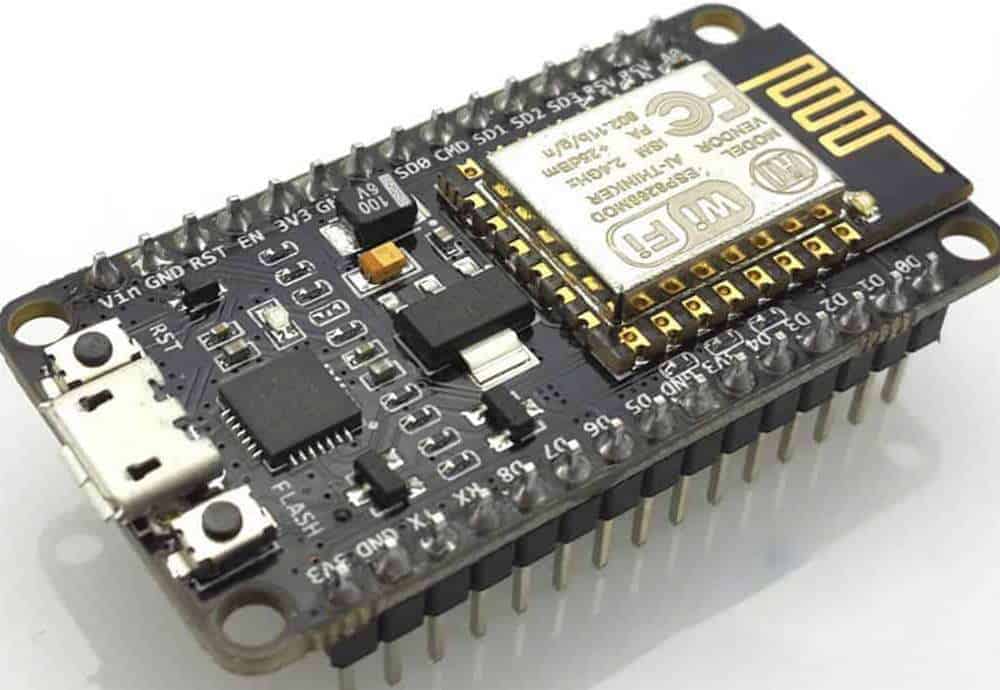
There are over a dozen major global manufacturers supplying pick and place machines to the electronics manufacturing industry. Here are some of the leading brands:
1. ASM Assembly Systems
Founded in 1968, ASM Assembly Systems is headquartered in Munich, Germany and has over 3000 employees worldwide. It is one of the pioneers and largest suppliers of SMT pick and place systems.
Some key technologies of ASM’s SMT placement systems include:
- High speed Siplace placement heads with upto 132,000 cph (components per hour)
- TwinLane and MultiLane transport systems allowing flexible dual track processing
- Agilis flexible feeder system with toolless changeover
- Intelligent software like SIPLACE Pro with optimization assistants
The ASM Siplace platform offers placement accuracy down to 35μm @ 3 sigma and handling of components as small as 01005 chips. With solutions scaling from low volume to ultra high volume production, ASM equipment is used by leading electronics manufactuers worldwide.
2. Juki Automation Systems
Headquartered in Japan, Juki is a well-known supplier of SMT assembly machines and solutions. Their pick and place systems are known for high accuracy, flexibility and reliability.
Key features of JUKI’s solutions include:
- High speed multi-function heads
- Rotary indexer table for continuous production
- 3D SPI (Solder Paste Inspection) for process control
- Support for wide range component sizes – 0402 to 54mm
Juki’s modular RX-7R placement system with 7th generation multi-function heads can achieve upto 157,200 cph placement speeds with accuracy of ±35 μm at 3σ. JUKI’s solutions range from entry-level to advanced high-speed lines ideal for agile SMT production.
3. Yamaha Surface Mount Technology (SMT)
Yamaha Motors started providing SMT equipment since 1987 and Yamaha SMT today is headquartered in Japan with offices globally.
Some unique technologies provided by Yamaha SMT include:
- High performance YV series placement heads -Advanced 3D flexible dual-arm robot YRM20 for optimal productivity
- Component storage systems like IC Bank for large components
- Leading edge software suite YST for smart factory control
Yamaha SMT’s placement systems like the YSM20R can deliver industry leading speeds upto 105,000 cph @ 01005 size chips with advanced vision accuracy of ±25 μm @ 3σ. The wide range of Yamaha SMT placement systems are trusted by major automotive, industrial and medical device manufacturers globally.
4. Panasonic Factory Solutions
Panasonic Factory Solutions Co. based in Japan provides a wide range of SMT assembly equipment including mounters, screen printers, dispensers, handlers and more.
Key benefits of Panasonic’s solutions include:
- Highly modular placement systems like NPM-D series
- Advanced software suite like iPCS for optimization and traceability
- Fast, multi-function and flexible heads
- Wide component support – 01005 to large modules upto 210mm length
The NPM Series can achieve industry leading placement speeds upto 150,000 cph while handling ultra-miniature 01005 (0.4 x 0.2 mm) chips reliably due to advanced features like PanaCIMizer pattern recognition software. With solutions for low, mid and high volume manufacturing, Panasonic equipment is used globally for automotive, industrial, medical and other applications.
5. Fuji Machine Manufacturing
Fuji Machine Mfg. Co based in Japan has been providing SMT assembly machines since 1948. Their popular solutions include:
- NXT III Series placement systems with multi-functional rotary heads
- Flexible component supply systems like stick feeders
- Advanced SPI, AOI and software solutions for smart factory
- Lead-free processing equipment
The NXT III series delivers high accuracy ±35 μm @ 3σ for reliable ultra-high-speed assembly. The systems support dual-track or multi-lane configurations for maximum flexibility. Fuji’s AIMEX-V no-clean solder paste printers, Aquaeos water-wash systems and optimized software enable complete SMT lines to be created. Fuji’s equipment is widely used in consumer electronics, automotive and industrial applications.
Smarter Software and Solutions for Electronics Manufacturing
To optimize the performance of pick and place systems and create smart SMT assembly lines, advanced software and integrated solutions play a key role in addition to the core hardware. Some ways leading pick and place manufacturers are driving software innovation are:
- Intelligent feeder setup and optimization software to maximize line changeover efficiency and UPH. Examples are Asm Siplace Pro/SIPLACE ProOptimizer and Juki SC-10 Smart Controller.
- Advanced digital twin, simulation and virtual commissioning software to validate and optimize programs and line performance digitally before physical setup. Eg. Asm Siplace Digtal Twin, Panasonic iPCS digital twin.
- Integration of AI and machine learning for auto-optimization of feeder setups, minimizing changeover time, maximizing line OEE. Eg. Yamaha YST Guidance Suite
- Full traceability and process data analytics across all machines for yield improvement and predictive maintenance. Eg. Fuji NXT Manager
- Easy programming and open interfaces for system integration across vendor machines. Eg. Juki unified programming interface
In addition to the core SMT placement systems, manufacturers also provide a range of compatible solutions for material handling, soldering, cleaning, inspection and packaging to create complete optimized SMT lines.
Conclusion
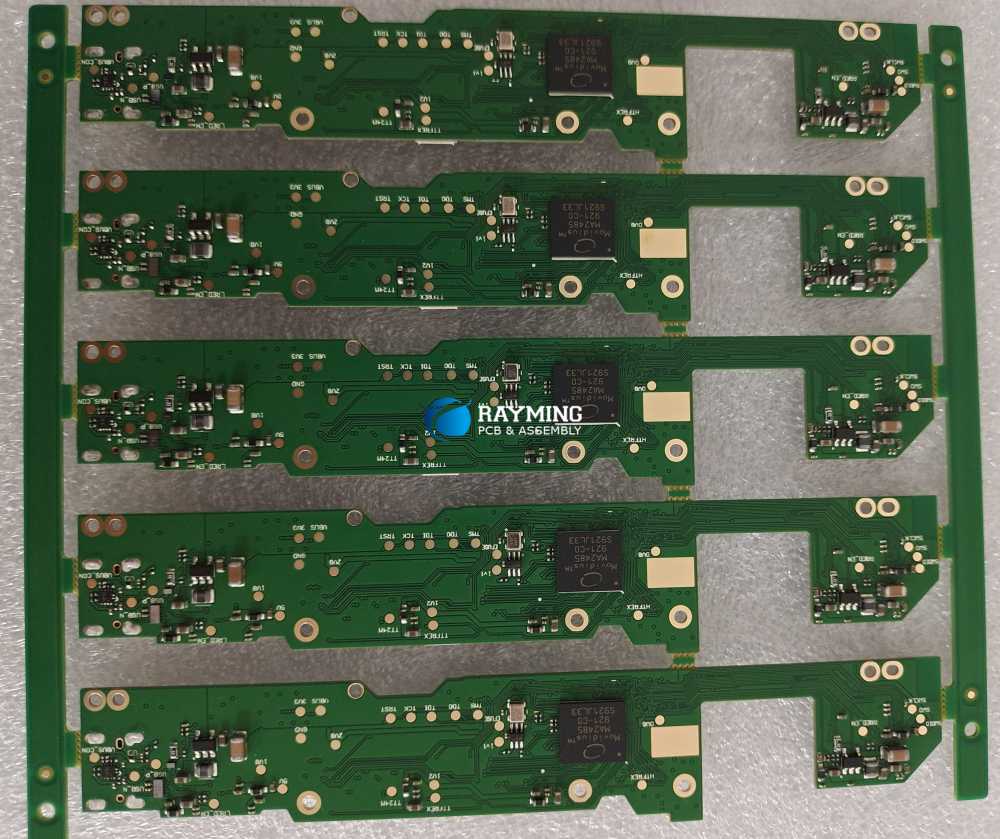
As electronics products become more complex and markets more competitive, manufacturers need flexible, high-speed and precise SMT assembly to stay ahead. Investing in advanced pick and place systems from leading manufacturers coupled with smart software can significantly improve productivity, efficiency, quality and costs. The right solution depends on production volumes, line complexity, changeover needs and other factors. By partnering with experienced pick and place vendors and leveraging emerging Industry 4.0 technologies, electronics manufacturers can transform into intelligent smart factories of the future.
FQA
What are the key benefits of automated pick and place machines?
Some of the main benefits of using pick and place automation are:
- Dramatically increased production speed and throughput
- Improved placement precision and accuracy
- Reduction in human errors during manual assembly
- Ability to handle very small components like 01005 chips
- Flexible, programmable, changeover with minimal downtime
- Consistent product quality and reliability
- Efficient handling of high mix, low to mid volume production
- Reduced manufacturing costs and optimized SMT line utilization
What factors should be considered when selecting a pick and place system?
Important factors to consider when selecting pick and place equipment include:
- Production volumes, mix and changeover needs
- Component sizes – range to be handled
- Placement speed/throughput targets
- Placement accuracy and precision required
- Types of feeder and storage systems needed
- Software capabilities for optimization, changeover, traceability etc
- Budget constraints
- Available floor space and line layout options
- Prior vendor experience and local support availability
- Options for connectivity and integration into production environment
Getting technical guidance from experienced SMT equipment vendors is highly recommended during selection.
How can electronics manufacturers transform towards smart factory and Industry 4.0?
Some ways electronics manufacturers can leverage smart technologies for Industry 4.0 production are:
- Using pick and place systems with connectivity, data capture and analytics features
- Implementing optimization software powered by AI/ML algorithms
- Digital twin simulation prior to physical setup and ramp-up
- Adopting automated material handling systems like AGVs
- Integrating machines, ERP and MES software for end-to-end traceability
- Implementing dashboards and analytics for yield improvement
- Leveraging IoT sensors, augmented reality tools and wearables
- Connecting equipment to cloud-based monitoring platforms
- Training personnel on emerging technologies like cobots, additive mfg
Continuous improvement of processes, culture and workforce skills is key to digital transformation.
What are some emerging trends in electronics assembly automation?
Some emerging trends shaping the future of electronics assembly automation are:
- Growing use of collaborative robots (cobots) working alongside operators
- Adoption of augmented/virtual reality for programming, changeover, maintenance
- Wide uptake of industry 4.0 digital twin, simulation and cloud tools
- Artificial intelligence and machine learning becoming ubiquitous
- Additive manufacturing supplementing SMT assembly in some applications
- More focus on automated optical, solder paste inspection
- Miniaturization driving need for advanced placement systems
- Higher demand for flexible, modular and reconfigurable lines
Electronics manufacturing is evolving rapidly under Industry 4.0 transformation. With the latest innovations in automation, electronics producers can build the intelligent factories of the future.
How can pick and place machine downtime be minimized?
Some ways to maximize uptime and minimize downtime of pick and place machines are:
- Implementing preventive and predictive maintenance routines
- Quick tooling/feeder changeover procedures and kits
- Operator training for routine maintenance and troubleshooting
- Spare parts inventory management and sourcing
- Utilizing software analytics to catch early signs of issues
- Monitoring vibration, temperature, other parameters
- Regular calibration and servicing by technicians
- Having 24/7 technical support contracts with machine vendors
- Capturing machine data to analyze root causes of downtime
- Planning production schedules to accommodate maintenance
With robust maintenance strategies and data-driven analytics, electronics manufacturers can optimize pick and place machine availability and OEE.
What safety measures should be taken when operating pick and place machines?
Some important safety practices when using pick and place machines:
- Only trained operators should operate the machines
- Safety guards should be kept enabled to avoid contact with moving parts
- Proper anti-static procedures should be followed for ESD-sensitive components
- Safe material handling practices should be used for transporting PCBs
- Servicing should only be done after isolating power to the machine
- Any warning symbols/alarms should be addressed before continuing operation
- Emergency stop buttons must be clearly identified and accessible
- Documentation like manuals and safety labels should be read and followed
- Good housekeeping should be maintained around the machines
- Personnel should wear required PPE items
Strictly following the equipment vendor safety guidelines is highly recommended for maximum safety.
0 Comments