Introduction to Kapton PCB
Kapton, a polyimide film developed by DuPont, has gained significant popularity in the electronics industry due to its exceptional properties. Kapton PCBs, also known as Polyimide PCBs, are printed circuit boards that utilize Kapton as the base material. These PCBs offer several advantages over traditional FR-4 PCBs, making them ideal for various applications, especially in harsh environments.
What is Kapton?
Kapton is a polyimide film that possesses a unique combination of properties, including:
- High thermal stability (up to 400°C)
- Excellent electrical insulation
- High mechanical strength and flexibility
- Resistance to chemicals and solvents
- Low dielectric constant and dissipation factor
These properties make Kapton an ideal material for PCBs in demanding applications.
Advantages of Kapton PCBs
Kapton PCBs offer several advantages over traditional FR-4 PCBs:
-
High-temperature resistance: Kapton PCBs can withstand temperatures up to 400°C, making them suitable for high-temperature applications such as aerospace, automotive, and industrial electronics.
-
Flexibility: The flexibility of Kapton allows for the creation of flexible PCBs that can conform to various shapes and sizes, enabling more compact and lightweight designs.
-
Excellent electrical insulation: Kapton has a high dielectric strength and low dielectric constant, ensuring excellent electrical insulation and reducing signal loss.
-
Chemical resistance: Kapton PCBs are resistant to most chemicals and solvents, making them suitable for use in harsh environments.
-
Dimensional stability: Kapton maintains its dimensional stability over a wide temperature range, ensuring the reliability and longevity of the PCB.
Kapton PCB Manufacturing Process
The manufacturing process for Kapton PCBs is similar to that of traditional FR-4 PCBs, with a few key differences:
1. Material Selection
The first step in manufacturing Kapton PCBs is selecting the appropriate Kapton film. There are several types of Kapton films available, each with different properties and thicknesses. The most commonly used Kapton films for PCBs are:
- Kapton HN: A general-purpose film with excellent balance of properties
- Kapton FN: A low-dielectric constant film for high-speed applications
- Kapton EN: A film with enhanced electrical and thermal properties
2. Lamination
The selected Kapton film is laminated to a copper foil using a high-temperature adhesive. The lamination process is carried out under high pressure and temperature to ensure a strong bond between the Kapton and copper layers.
3. Drilling
After lamination, the Kapton-copper laminate is drilled to create holes for through-hole components and vias. Drilling Kapton PCBs requires special care due to the material’s high thermal stability and toughness.
4. Patterning
The copper layer is then patterned using photolithography and etching processes. The desired circuit pattern is transferred to the copper layer using a photoresist and exposed to UV light. The unexposed areas are etched away, leaving the desired circuit pattern.
5. Surface Finishing
Once the circuit pattern is formed, the Kapton PCB undergoes surface finishing to protect the exposed copper and improve solderability. Common surface finishes for Kapton PCBs include:
- ENIG (Electroless Nickel Immersion Gold)
- ENEPIG (Electroless Nickel Electroless Palladium Immersion Gold)
- OSP (Organic Solderability Preservative)
6. Solder Mask and Silkscreen
A solder mask is applied to the Kapton PCB to protect the circuit pattern and prevent solder bridging. The solder mask is typically a high-temperature resistant polymer. Finally, a silkscreen layer is added to the PCB for component labeling and identification.
Applications of Kapton PCBs
Kapton PCBs find applications in various industries due to their unique properties:
Aerospace and Defense
Kapton PCBs are extensively used in aerospace and defense applications due to their ability to withstand extreme temperatures and harsh environments. Some common applications include:
- Satellite communication systems
- Avionics
- Missile guidance systems
- Radar systems
Automotive Electronics
The high-temperature resistance and flexibility of Kapton PCBs make them suitable for automotive electronics applications, such as:
- Engine control units (ECUs)
- Transmission control modules
- Exhaust gas sensors
- Brake systems
Industrial Electronics
Kapton PCBs are used in industrial electronics applications that require high reliability and resistance to harsh environments, such as:
- Oil and gas exploration equipment
- Power electronics
- Motor drives
- Renewable energy systems
Medical Devices
The biocompatibility and chemical resistance of Kapton make it suitable for use in medical devices, such as:
- Implantable devices
- Diagnostic equipment
- Surgical instruments
- Wearable health monitors
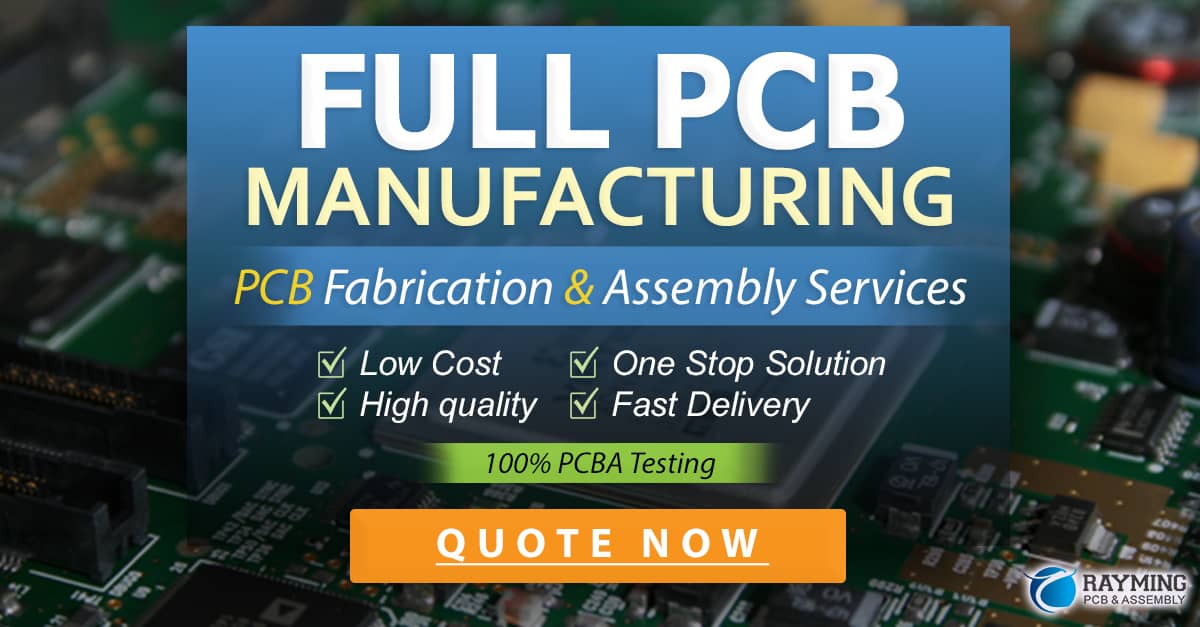
Choosing a Kapton PCB Manufacturer
When selecting a Kapton PCB manufacturer, there are several factors to consider:
1. Experience and Expertise
Choose a manufacturer with extensive experience in fabricating Kapton PCBs. They should have a deep understanding of the material properties and the manufacturing process to ensure high-quality PCBs.
2. Manufacturing Capabilities
Ensure that the manufacturer has the necessary equipment and facilities to handle Kapton PCB fabrication. This includes high-temperature lamination presses, laser drilling machines, and specialized surface finishing equipment.
3. Quality Control
A reliable Kapton PCB manufacturer should have stringent quality control measures in place to ensure the consistency and reliability of their products. Look for manufacturers with certifications such as ISO 9001, AS9100, and IATF 16949.
4. Technical Support
Choose a manufacturer that offers comprehensive technical support throughout the PCB design and manufacturing process. They should be able to provide guidance on material selection, design optimization, and manufacturing best practices.
5. Lead Time and Cost
Consider the manufacturer’s lead time and cost structure. While Kapton PCBs may have a higher initial cost compared to FR-4 PCBs, their superior performance and longevity can result in long-term cost savings.
Top Kapton PCB Manufacturers
Some of the leading Kapton PCB manufacturers in the industry include:
Manufacturer | Location | Certifications | Specialization |
---|---|---|---|
Dupont | USA | ISO 9001, AS9100 | Kapton film manufacturing |
Shengyi Technology | China | ISO 9001, IATF 16949 | High-temperature PCBs |
Nippon Mektron | Japan | ISO 9001, IATF 16949 | Flexible PCBs |
Flexcom | USA | ISO 9001, AS9100 | Aerospace and defense PCBs |
NCAB Group | Sweden | ISO 9001, AS9100 | High-reliability PCBs |
These manufacturers have a proven track record of delivering high-quality Kapton PCBs for various applications and industries.
Frequently Asked Questions (FAQ)
1. What is the maximum operating temperature for Kapton PCBs?
Kapton PCBs can withstand temperatures up to 400°C, making them suitable for high-temperature applications.
2. Can Kapton PCBs be used for flexible electronics?
Yes, Kapton PCBs are commonly used in flexible electronics due to their excellent mechanical strength and flexibility.
3. Are Kapton PCBs more expensive than traditional FR-4 PCBs?
Kapton PCBs typically have a higher initial cost compared to FR-4 PCBs due to the specialized materials and manufacturing processes involved. However, their superior performance and longevity can result in long-term cost savings.
4. How do I select the right Kapton film for my PCB application?
The selection of the Kapton film depends on the specific requirements of your application. Factors to consider include the required thermal stability, electrical properties, and mechanical strength. Consult with your Kapton PCB manufacturer for guidance on material selection.
5. What surface finishes are available for Kapton PCBs?
Common surface finishes for Kapton PCBs include ENIG (Electroless Nickel Immersion Gold), ENEPIG (Electroless Nickel Electroless Palladium Immersion Gold), and OSP (Organic Solderability Preservative). The choice of surface finish depends on the application requirements and the desired solderability and durability.
Conclusion
Kapton PCBs offer a unique combination of properties that make them ideal for various applications in harsh environments. With their high-temperature resistance, excellent electrical insulation, and mechanical flexibility, Kapton PCBs are widely used in aerospace, automotive, industrial, and medical electronics.
When selecting a Kapton PCB manufacturer, it is crucial to consider factors such as experience, manufacturing capabilities, quality control, technical support, lead time, and cost. By partnering with a reliable manufacturer, you can ensure the highest quality Kapton PCBs for your specific application needs.
As technology continues to advance, the demand for Kapton PCBs is expected to grow, driven by the increasing need for high-performance electronics in challenging environments. With their superior properties and versatility, Kapton PCBs are poised to play a significant role in shaping the future of the electronics industry.
0 Comments