Introduction to Nelco and PCB Fabrication
Nelco is a leading manufacturer and fabricator of printed circuit boards (PCBs). With over 40 years of experience in the industry, Nelco has established itself as a trusted partner for businesses in need of high-quality, reliable PCBs for their electronic products and systems.
PCB fabrication is the process of creating printed circuit boards, which are essential components in virtually all modern electronic devices. PCBs provide the electrical connections and mechanical support for electronic components such as transistors, resistors, and integrated circuits.
The Importance of Choosing the Right PCB Fabricator
Selecting the right PCB fabricator is crucial for ensuring the quality, reliability, and performance of your electronic products. A reputable PCB fabricator like Nelco can provide:
- High-quality materials and manufacturing processes
- Strict quality control and testing procedures
- Experienced engineers and technicians
- Competitive pricing and fast turnaround times
- Excellent customer support and communication
Choosing a subpar PCB fabricator can lead to issues such as:
- Poor quality PCBs that fail prematurely
- Delays in production and delivery
- Increased costs due to rework or replacements
- Damage to your company’s reputation
Nelco’s PCB Fabrication Capabilities
Nelco offers a wide range of PCB fabrication capabilities to meet the diverse needs of its customers. Some of these capabilities include:
1. Multilayer PCBs
Multilayer PCBs consist of multiple layers of conductive copper and insulating material, allowing for more complex and compact designs. Nelco can fabricate multilayer PCBs with up to 40 layers, suitable for applications such as:
- High-speed digital systems
- Telecommunications equipment
- Medical devices
- Aerospace and defense systems
2. High Density Interconnect (HDI) PCBs
HDI PCBs feature finer trace widths, smaller vias, and higher connection pad density compared to traditional PCBs. This enables the creation of more compact and high-performance electronic devices. Nelco’s HDI PCB capabilities include:
- Microvias (laser-drilled holes)
- Blind and buried vias
- Fine pitch BGAs and CSPs
- Thin core and prepreg materials
3. Flexible and Rigid-Flex PCBs
Flexible PCBs are made from thin, flexible materials that allow the PCB to bend and conform to different shapes. Rigid-flex PCBs combine both rigid and flexible sections, offering the benefits of both types in a single board. Nelco can fabricate flexible and rigid-flex PCBs for applications such as:
- Wearable electronics
- Mobile devices
- Automotive electronics
- Aerospace and military systems
4. Metal Core PCBs
Metal core PCBs (MCPCBs) use a metal base, typically aluminum, as the substrate instead of the traditional FR-4 material. This provides better thermal conductivity, allowing for more efficient heat dissipation. Nelco’s MCPCB capabilities are ideal for applications such as:
- High-power LED lighting
- Automotive electronics
- Power converters and inverters
5. Specialized PCB Materials
In addition to standard FR-4 material, Nelco can fabricate PCBs using a variety of specialized materials to meet specific requirements, such as:
- High-frequency materials (e.g., Rogers, Isola)
- High-temperature materials (e.g., polyimide)
- Halogen-free materials
- Controlled impedance materials
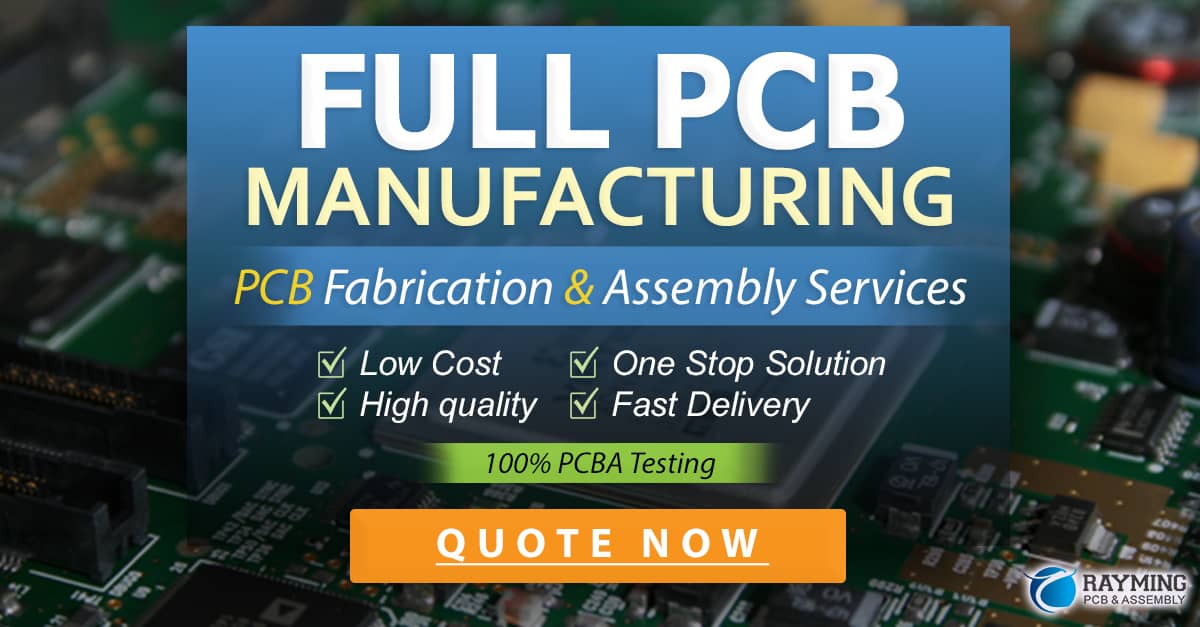
Nelco’s PCB Fabrication Process
Nelco follows a strict PCB fabrication process to ensure the highest quality and reliability of its products. The key steps in this process include:
- Design and Engineering Review
- Review customer-provided design files (e.g., Gerber, ODB++)
- Check for design rule violations and manufacturability issues
-
Provide feedback and recommendations for design optimization
-
Material Selection and Preparation
- Select appropriate materials based on customer requirements and specifications
-
Prepare materials (e.g., cutting, cleaning, surface treatment)
-
Inner Layer Fabrication
- Print and etch inner layer circuits
-
Inspect inner layers for defects and accuracy
-
Lamination and Drilling
- Laminate inner layers with prepreg and copper foil
-
Drill through-holes and vias
-
Plating and Outer Layer Fabrication
- Plate through-holes and vias with copper
-
Print and etch outer layer circuits
-
Solder Mask and Silkscreen Application
- Apply solder mask to protect the PCB surface
-
Print silkscreen legends and markings
-
Surface Finish Application
-
Apply appropriate surface finish (e.g., HASL, ENIG, OSP)
-
Electrical Testing and Inspection
- Perform electrical testing (e.g., continuity, isolation, HiPot)
-
Inspect PCBs for visual defects and workmanship issues
-
Cutting and Packaging
- Cut PCBs to final size and shape
- Package PCBs for shipping and protection
Nelco’s Quality Control and Testing
Nelco maintains a strict quality control and testing program to ensure that its PCBs meet the highest standards of quality and reliability. Some of the key elements of this program include:
- ISO 9001:2015 certified quality management system
- IPC-A-600 and IPC-6012 compliance for workmanship and acceptance criteria
- 100% electrical testing of all PCBs
- Automated optical inspection (AOI) for detecting surface defects
- X-ray inspection for inner layer and via defects
- Microsectioning and cross-sectioning for structural analysis
- Ionic contamination testing (ROSE) for cleanliness
- Thermal stress testing and thermal cycling
- Accelerated life testing and reliability testing
Test/Inspection | Standard/Method | Purpose |
---|---|---|
Visual inspection | IPC-A-600 | Detect surface defects and workmanship issues |
Electrical testing | IPC-9252, IPC-TM-650 | Verify continuity, isolation, and functionality |
Automated optical inspection (AOI) | IPC-A-610 | Detect surface defects automatically |
X-ray inspection | IPC-TM-650 2.6.5 | Detect inner layer and via defects |
Microsectioning | IPC-TM-650 2.1.1 | Analyze PCB structure and layer registration |
Ionic contamination testing | IPC-TM-650 2.3.25 | Measure cleanliness of PCB surface |
Thermal stress testing | IPC-TM-650 2.6.7.2 | Evaluate PCB reliability under thermal stress |
Accelerated life testing | IPC-TM-650 2.6.26 | Predict PCB lifetime under accelerated conditions |
Nelco’s Customer Support and Service
Nelco prides itself on providing excellent customer support and service throughout the PCB fabrication process. Some of the ways Nelco supports its customers include:
- Dedicated account managers for each customer
- Regular communication and status updates
- Rapid response to technical inquiries and support requests
- Flexibility in accommodating design changes and revisions
- Assistance with PCB design and DFM (Design for Manufacturability) optimization
- Expedited production and delivery options
- Comprehensive documentation and certificates of compliance
- Worldwide shipping and logistics support
Case Studies and Success Stories
Nelco has helped numerous customers across various industries successfully bring their electronic products to market. Here are a few examples:
1. Medical Device Manufacturer
A leading medical device manufacturer partnered with Nelco to develop a new, compact, and high-performance PCB for their next-generation diagnostic equipment. Nelco’s HDI PCB capabilities and experience with medical-grade materials enabled the customer to create a device that was smaller, faster, and more reliable than their previous generation.
2. Automotive Electronics Supplier
An automotive electronics supplier needed a PCB fabricator that could provide high-volume production of PCBs for their advanced driver assistance systems (ADAS). Nelco’s robust manufacturing processes, strict quality control, and ability to scale production helped the customer meet their tight deadlines and quality requirements.
3. Aerospace and Defense Contractor
An aerospace and defense contractor required specialized PCBs for their satellite communication systems. Nelco’s expertise in high-frequency materials, controlled impedance, and rigid-flex PCBs allowed the customer to create PCBs that could withstand the harsh environments of space and provide reliable performance.
Frequently Asked Questions (FAQ)
- What is the minimum order quantity (MOQ) for PCBs at Nelco?
-
Nelco’s MOQ varies depending on the specific PCB type and requirements, but typically ranges from 1-100 pieces for prototypes and small production runs, and 100-1000+ pieces for larger production volumes.
-
What file formats does Nelco accept for PCB design?
-
Nelco accepts industry-standard file formats such as Gerber (RS-274X), ODB++, and IPC-2581. We also work with native CAD files from popular PCB design software such as Altium Designer, Cadence Allegro, and Mentor Graphics PADS.
-
How long does it take to fabricate a typical PCB order at Nelco?
-
Lead times vary depending on the complexity of the PCB, the quantity ordered, and the current production schedule. Standard lead times range from 5-15 working days, but expedited options are available for urgent orders.
-
Does Nelco offer PCB assembly services in addition to fabrication?
-
Yes, Nelco offers turnkey PCB assembly services, including SMT (surface mount technology) and through-hole assembly, component procurement, and testing. We can provide full turnkey solutions from PCB fabrication to final product assembly.
-
How does Nelco ensure the confidentiality and security of customer data and intellectual property?
- Nelco has strict confidentiality and non-disclosure agreements in place with all employees and partners. We employ secure data storage and transmission practices, and have access controls and monitoring systems to prevent unauthorized access to customer data and intellectual property.
Conclusion
Nelco is a premier PCB manufacturer and fabricator, offering a wide range of capabilities and services to meet the needs of customers across various industries. With its commitment to quality, reliability, and customer support, Nelco is the ideal partner for businesses looking to bring their electronic products to market successfully.
By choosing Nelco as your PCB fabricator, you can benefit from:
- Advanced PCB fabrication capabilities, including multilayer, HDI, flexible, and rigid-flex PCBs
- Strict quality control and testing procedures to ensure the highest standards of quality and reliability
- Experienced engineers and technicians who can provide guidance and support throughout the PCB fabrication process
- Competitive pricing and fast turnaround times to help you meet your budget and time-to-market goals
- Excellent customer service and support, with dedicated account managers and regular communication
Contact Nelco today to learn more about how we can help you with your PCB fabrication needs and take your electronic products to the next level.
0 Comments