What is PCB Prototyping?
PCB prototyping is the process of creating a preliminary version of a printed circuit board (PCB) design to test and validate its functionality before mass production. It involves fabricating one or a small number of PCBs based on the initial design, allowing engineers to identify and address any issues or improvements needed.
PCB prototyping is a crucial step in the development of electronic devices, as it helps ensure the final product meets the desired specifications and performs reliably. By creating prototypes, designers can catch and fix problems early on, saving time and money in the long run.
Why is PCB Prototyping Important?
PCB prototyping offers several key benefits:
-
Design Validation: Prototypes allow designers to test their PCB layout and verify that it functions as intended. This helps identify any design flaws or potential improvements before committing to large-scale production.
-
Cost Savings: Catching and fixing issues during the prototyping stage is much more cost-effective than discovering problems after mass production has begun. Prototyping helps minimize the risk of costly rework or product recalls.
-
Iterative Improvement: Prototyping enables designers to refine and optimize their PCB design through multiple iterations. Each prototype can incorporate feedback and enhancements, leading to a better final product.
-
Tangible Testing: Having a physical prototype allows for hands-on testing and evaluation of the PCB’s performance, durability, and compatibility with other components. This provides valuable insights that computer simulations alone cannot offer.
-
Faster Time-to-Market: By thoroughly testing and refining the design through prototyping, companies can accelerate their product development process and bring their products to market faster.
8 Key Considerations for PCB Prototyping
To ensure successful PCB prototyping, there are several important factors to keep in mind:
1. Design for Manufacturability (DFM)
When designing your PCB Prototype, it’s essential to consider the manufacturability of your design. This means adhering to industry standards and best practices to ensure your PCB can be efficiently and reliably produced.
Some key DFM considerations include:
- Choosing appropriate trace widths and spacings
- Avoiding sharp corners and acute angles in traces
- Providing adequate clearance around holes and components
- Using standard component sizes and packages
- Minimizing the number of unique parts and materials
- Clearly labeling and documenting your design files
By designing with manufacturability in mind, you can avoid potential production issues and delays down the line.
2. Component Selection and Availability
Carefully select the components for your PCB prototype, taking into account their availability, cost, and lead times. Using readily available, industry-standard components can help streamline the prototyping process and ensure a smoother transition to mass production.
When selecting components, consider:
- Choosing parts with multiple supplier options to minimize supply chain risks
- Verifying component compatibility with your PCB design and manufacturing process
- Avoiding obsolete or end-of-life components
- Considering the environmental and operating conditions your PCB will face
- Balancing cost with performance and reliability requirements
3. Layer Stack-Up and Material Choice
The layer stack-up and material choice for your PCB prototype can significantly impact its performance, reliability, and manufacturability. Consider factors such as:
- The number of layers needed to accommodate your design
- The dielectric constant and thickness of the insulating material
- The copper weight and thickness for each layer
- The surface finish (e.g., HASL, ENIG, OSP) for component attachment and solderability
- Any special requirements, such as controlled impedance or high-frequency performance
Work closely with your PCB manufacturer to determine the optimal layer stack-up and materials for your specific application.
4. Via and Hole Placement
Proper via and hole placement is crucial for ensuring the integrity and reliability of your PCB prototype. Consider the following:
- Minimize the number of vias to reduce manufacturing complexity and cost
- Place vias in accessible locations for easy inspection and repair
- Ensure adequate spacing between vias and other features to avoid manufacturing issues
- Use appropriate via sizes and hole diameters for your chosen manufacturing process
- Consider via-in-pad design for high-density layouts, if supported by your manufacturer
5. Silkscreen and Labeling
Clear and accurate silkscreen and labeling on your PCB prototype can greatly facilitate assembly, testing, and troubleshooting. Consider including:
- Component reference designators
- Polarity and orientation markers
- Test points and probe locations
- Company logo and product information
- Revision number and date code
- Any necessary warning or handling labels
Ensure that your silkscreen and labeling comply with industry standards and are legible at the chosen font size.
6. Testing and Validation
Thorough testing and validation of your PCB prototype are essential to ensure it meets your design requirements and performs reliably. Consider the following testing strategies:
- In-circuit testing (ICT) to verify component placement and connectivity
- Functional testing to validate the PCB’s operation under various conditions
- Boundary scan testing for complex digital circuits
- Environmental testing (e.g., temperature, humidity, vibration) to assess durability
- Electromagnetic compatibility (EMC) testing to ensure regulatory compliance
Develop a comprehensive test plan that covers all critical aspects of your PCB prototype’s performance.
7. Documentation and Version Control
Maintaining accurate documentation and version control throughout the PCB prototyping process is crucial for tracking changes, communicating with stakeholders, and ensuring a smooth transition to production. Key documents to maintain include:
- Schematic diagrams
- Bill of Materials (BOM)
- PCB layout files
- Assembly drawings
- Test plans and reports
- Revision history and change logs
Use a robust version control system to manage your design files and ensure that all team members are working with the latest versions.
8. Manufacturer Selection and Communication
Choosing the right PCB Prototype Manufacturer and maintaining clear communication throughout the process can significantly impact the success of your project. Consider the following when selecting a manufacturer:
- Experience and expertise in PCB prototyping
- Quality control processes and certifications
- Manufacturing capabilities and technology
- Turnaround time and pricing
- Customer support and communication channels
Establish a strong working relationship with your chosen manufacturer and provide them with all necessary design files, specifications, and requirements. Regularly communicate with them to ensure that your prototype is progressing as planned and to address any issues that may arise.
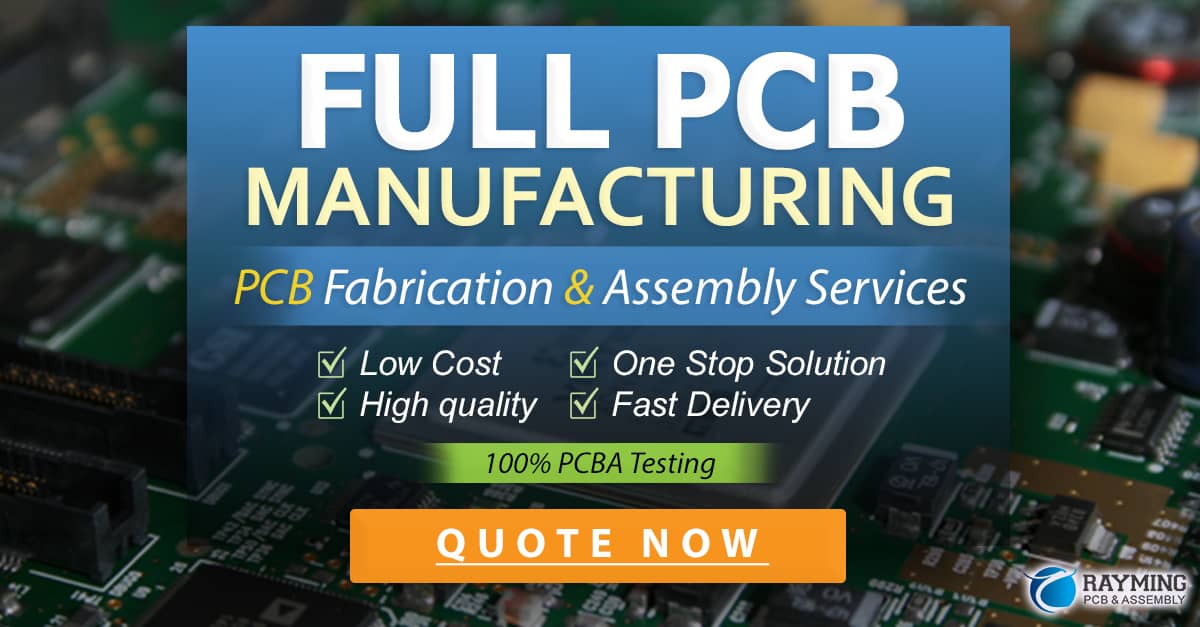
Frequently Asked Questions (FAQ)
1. How long does PCB prototyping typically take?
The time required for PCB prototyping can vary depending on the complexity of the design, the chosen manufacturer, and the specific manufacturing processes involved. However, most PCB prototyping services offer turnaround times ranging from 24 hours to 2 weeks.
2. How much does PCB prototyping cost?
PCB prototyping costs depend on factors such as the size and complexity of the design, the number of layers, the chosen materials, and the quantity of prototypes ordered. Prices can range from a few dollars to several hundred dollars per prototype. Many manufacturers offer online quoting tools to help estimate costs based on your specific requirements.
3. What files do I need to provide for PCB prototyping?
To begin the PCB prototyping process, you’ll typically need to provide your manufacturer with a set of design files, including:
- Gerber files: These are the industry-standard files that describe the layout of your PCB, including the copper layers, solder mask, and silkscreen.
- Drill files: These specify the location, size, and type of holes required for your PCB.
- Bill of Materials (BOM): This is a list of all the components used in your design, including their reference designators, part numbers, and quantities.
- Assembly drawings: These provide instructions for assembling your PCB, including component placement and orientation.
4. Can I request changes to my PCB prototype after submitting my design?
Most PCB prototype manufacturers will allow you to request changes to your design after submission, but this may incur additional costs and delay the turnaround time. It’s best to thoroughly review and finalize your design before submitting it for prototyping to minimize the need for changes.
5. What should I do if my PCB prototype doesn’t work as expected?
If your PCB prototype doesn’t function as intended, first carefully review your design files and documentation for any errors or discrepancies. If you can’t identify the issue, consult with your manufacturer or an experienced PCB designer for guidance. They may be able to help you troubleshoot the problem or suggest modifications to your design to improve its performance.
Conclusion
PCB prototyping is a vital step in the development of electronic devices, allowing designers to test and refine their designs before committing to large-scale production. By carefully considering factors such as design for manufacturability, component selection, layer stack-up, via placement, silkscreen, testing, documentation, and manufacturer selection, you can ensure a successful PCB prototyping process that leads to a high-quality, reliable final product.
As technology continues to advance and electronic devices become increasingly complex, the importance of thorough PCB prototyping will only continue to grow. By staying up-to-date with industry best practices and working closely with experienced manufacturers, designers can navigate the challenges of PCB prototyping and bring their innovative ideas to life.
0 Comments