Introduction to FR4 PCB
FR4 (Flame Retardant 4) is a type of printed circuit board (PCB) material that has gained immense popularity in the electronics industry due to its excellent mechanical, electrical, and thermal properties. FR4 PCBs are widely used in various applications, ranging from consumer electronics to aerospace and military equipment. In this comprehensive guide, we will delve into the world of FR4 PCBs, exploring their composition, manufacturing process, advantages, and applications. By the end of this article, you will have a thorough understanding of FR4 PCBs and their significance in the ever-evolving electronics landscape of 2024.
What is FR4 PCB?
FR4 is a composite material composed of woven fiberglass cloth impregnated with an epoxy resin binder. The “FR” in FR4 stands for “Flame Retardant,” indicating its inherent ability to resist the spread of flames and self-extinguish when exposed to fire. The number “4” represents the specific grade of flame retardancy, which is the highest among the FR series (FR-1, FR-2, FR-3, and FR-4).
Composition of FR4 PCB
The key components of an FR4 PCB are:
-
Fiberglass Cloth: The base material of FR4 is a woven fiberglass cloth, which provides excellent mechanical strength and dimensional stability to the PCB.
-
Epoxy Resin: The fiberglass cloth is impregnated with an epoxy resin binder, which acts as an insulating material and helps to bond the layers of the PCB together.
-
Copper Foil: A thin layer of copper foil is laminated onto one or both sides of the FR4 substrate, serving as the conductive layer for electrical connections.
Properties of FR4 PCB
FR4 PCBs exhibit several desirable properties that make them suitable for a wide range of applications:
Property | Description |
---|---|
High Mechanical Strength | FR4 PCBs have excellent mechanical strength, making them resistant to bending, twisting, and impact. |
Flame Retardancy | The epoxy resin used in FR4 PCBs is designed to be flame-retardant, minimizing the risk of fire hazards. |
Electrical Insulation | FR4 provides excellent electrical insulation, preventing short circuits and ensuring reliable signal transmission. |
Thermal Stability | FR4 PCBs can withstand high temperatures, making them suitable for applications with elevated operating temperatures. |
Moisture Resistance | The epoxy resin in FR4 PCBs offers good moisture resistance, protecting the board from humidity-related issues. |
Manufacturing Process of FR4 PCB
The manufacturing process of FR4 PCBs involves several steps, each of which is critical to ensuring the quality and reliability of the final product.
Step 1: Material Preparation
The first step in the manufacturing process is to prepare the FR4 substrate. The fiberglass cloth is impregnated with the epoxy resin and partially cured to form a prepreg (pre-impregnated) material. The prepreg is then cut to the desired size and shape.
Step 2: Lamination
The prepreg layers are stacked together with the copper foil and subjected to high pressure and temperature in a lamination press. This process bonds the layers together, forming a solid, multilayer FR4 board.
Step 3: Drilling
After lamination, holes are drilled through the FR4 board to accommodate components and vias (vertical interconnect access). The drilling process is typically carried out using high-speed, computer-controlled drilling machines.
Step 4: Plating
The drilled holes are then plated with copper to create electrical connections between the layers of the PCB. This process is known as through-hole plating and ensures reliable connectivity within the board.
Step 5: Patterning
The desired circuit pattern is then transferred onto the copper layer using a photolithographic process. A photosensitive resist is applied to the copper surface, and the circuit pattern is exposed using UV light. The exposed areas are then developed, and the unwanted copper is etched away, leaving behind the desired circuit traces.
Step 6: Solder Mask and Silkscreen
A solder mask, typically green in color, is applied to the PCB to protect the copper traces from oxidation and prevent solder bridges during the assembly process. A silkscreen layer is then added to provide text and symbols for component placement and identification.
Step 7: Surface Finish
The exposed copper areas, such as pads and through-holes, are coated with a surface finish to enhance solderability and protect the copper from oxidation. Common surface finishes include Hot Air Solder Leveling (HASL), Immersion Gold (ENIG), and Immersion Silver.
Step 8: Cutting and Profiling
Finally, the FR4 panel is cut and profiled to the desired shape and size using a routing machine or a Laser Cutter. The individual PCBs are then separated and ready for assembly.
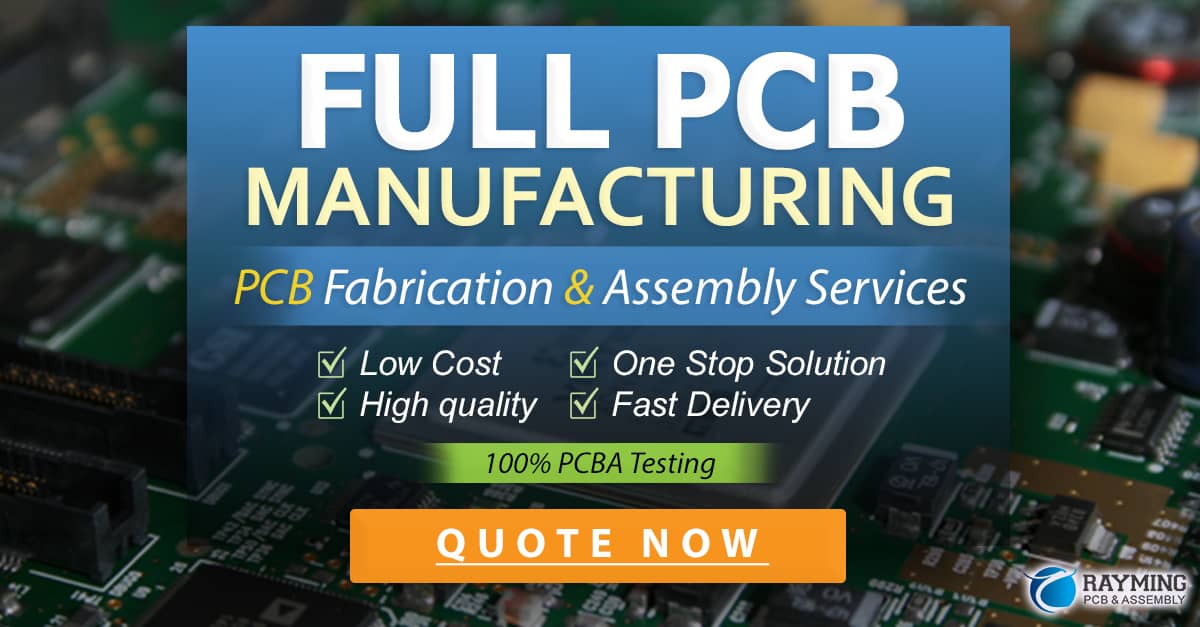
Advantages of FR4 PCB
FR4 PCBs offer several advantages over other PCB materials, making them a popular choice for a wide range of applications.
1. Cost-effective
FR4 is a relatively inexpensive material compared to other high-performance PCB substrates, such as polyimide or ceramic. The widespread availability and high volume production of FR4 contribute to its cost-effectiveness.
2. Versatile
FR4 PCBs can be used in a wide range of applications, from simple single-layer boards to complex multilayer designs. They can accommodate various component types, including surface-mount devices (SMDs) and through-hole components.
3. Reliable
The excellent mechanical, electrical, and thermal properties of FR4 make it a highly reliable choice for PCBs. FR4 boards can withstand harsh environmental conditions and maintain their performance over an extended period.
4. Easy to manufacture
The manufacturing process for FR4 PCBs is well-established and standardized, making it easy for PCB Fabricators to produce high-quality boards consistently.
5. Good thermal stability
FR4 PCBs have a glass transition temperature (Tg) of around 130°C to 140°C, which means they can maintain their mechanical and electrical properties at elevated temperatures.
Applications of FR4 PCB
FR4 PCBs find applications in a wide range of industries and products, including:
- Consumer electronics: Smartphones, laptops, tablets, televisions, and home appliances.
- Automotive electronics: Engine control units, infotainment systems, and advanced driver assistance systems (ADAS).
- Industrial electronics: Process control systems, automation equipment, and power electronics.
- Medical devices: Diagnostic equipment, patient monitoring systems, and implantable devices.
- Aerospace and defense: Avionics, radar systems, and military communication equipment.
- Telecommunications: Routers, switches, and base stations for wireless networks.
FR4 PCB vs. Other PCB Materials
While FR4 is the most widely used PCB material, there are other substrates available for specific applications. Some common alternatives to FR4 include:
1. High Tg FR4
High Tg FR4 is a variant of standard FR4 that offers improved thermal stability, with a glass transition temperature of up to 170°C. This makes it suitable for applications that require higher operating temperatures, such as automotive and aerospace electronics.
2. Polyimide
Polyimide is a high-performance polymer that offers excellent thermal stability, with a Tg of up to 260°C. Polyimide PCBs are used in applications that demand high temperature resistance, such as aerospace and military electronics.
3. Ceramic
Ceramic PCBs are made from alumina (Al2O3) or aluminum nitride (AlN) substrates and offer excellent thermal conductivity and electrical insulation properties. They are used in high-power applications, such as LED lighting and power electronics.
4. Metal Core
Metal core PCBs (MCPCBs) feature a metal substrate, typically aluminum, which provides excellent thermal dissipation. MCPCBs are used in applications that generate significant heat, such as high-power LED lighting and automotive electronics.
Future Trends in FR4 PCB
As the electronics industry continues to evolve, FR4 PCBs are expected to adapt to new challenges and requirements. Some of the future trends in FR4 PCB technology include:
1. High-Speed Materials
With the increasing demand for high-speed data transmission, there is a growing need for FR4 materials that can support higher signal frequencies. Manufacturers are developing low-loss, high-speed FR4 variants that can accommodate data rates of up to 56 Gbps and beyond.
2. Embedded Components
Embedded component technology, where passive components are integrated within the layers of the PCB, is gaining traction as a way to reduce board size and improve signal integrity. FR4 PCBs with embedded capacitors and resistors are expected to become more prevalent in the coming years.
3. Advanced Packaging Techniques
As electronic devices continue to shrink in size, advanced packaging techniques, such as chip-on-board (COB) and package-on-package (PoP), are becoming increasingly important. FR4 PCBs will need to adapt to these packaging techniques to enable the development of compact, high-density electronic assemblies.
4. Environmentally Friendly Materials
There is a growing emphasis on environmentally friendly materials in the electronics industry. FR4 PCB manufacturers are exploring the use of halogen-free flame retardants and bio-based epoxy resins to reduce the environmental impact of PCB production.
Frequently Asked Questions (FAQ)
-
Q: What does FR4 stand for?
A: FR4 stands for “Flame Retardant 4,” indicating the material’s ability to resist the spread of flames and self-extinguish when exposed to fire. -
Q: Can FR4 PCBs be used for high-frequency applications?
A: Standard FR4 PCBs have limitations when it comes to high-frequency applications. However, specialized high-speed FR4 variants are being developed to support higher signal frequencies and data rates. -
Q: Are FR4 PCBs suitable for high-temperature applications?
A: Standard FR4 PCBs have a glass transition temperature (Tg) of around 130°C to 140°C. For higher temperature applications, high Tg FR4 or alternative materials like polyimide or ceramic can be used. -
Q: How do I choose the right thickness for my FR4 PCB?
A: The choice of FR4 PCB Thickness depends on several factors, including the number of layers, component sizes, and mechanical requirements. Common thicknesses range from 0.8mm to 1.6mm, but thinner or thicker boards can be fabricated based on specific needs. -
Q: What is the typical lead time for FR4 PCB fabrication?
A: Lead times for FR4 PCB fabrication vary depending on the complexity of the design, the PCB manufacturer, and the order quantity. Typical lead times range from a few days to several weeks. Many PCB manufacturers offer expedited services for faster turnaround times.
Conclusion
FR4 PCBs have been a mainstay in the electronics industry for decades, and their importance continues to grow as new technologies and applications emerge. The exceptional mechanical, electrical, and thermal properties of FR4, combined with its cost-effectiveness and versatility, make it an ideal choice for a wide range of products, from consumer electronics to aerospace and defense systems.
As we look ahead to 2024 and beyond, FR4 PCBs are poised to evolve and adapt to the changing needs of the electronics landscape. With the development of high-speed materials, embedded component technology, and environmentally friendly alternatives, FR4 PCBs will continue to play a crucial role in enabling the next generation of electronic devices and systems.
By understanding the fundamentals of FR4 PCBs, their manufacturing process, advantages, and applications, engineers and designers can make informed decisions when selecting materials and designing PCBs for their projects. As the electronics industry continues to push the boundaries of innovation, FR4 PCBs will undoubtedly remain a key enabler of technological progress.
0 Comments