What is a Polyimide PCB?
A polyimide printed circuit board (PCB) is a type of PCB that uses polyimide as the base material instead of the more common FR-4 (flame retardant-4) material. Polyimide is a high-performance polymer known for its excellent thermal stability, mechanical strength, and chemical resistance.
Polyimide PCBs are ideal for applications that require high reliability and durability in harsh environments, such as aerospace, military, and medical industries. They can withstand extreme temperatures, ranging from -269°C to +400°C, and are resistant to many chemicals and solvents.
Types of Polyimide PCBs
There are several types of polyimide PCBs, each with unique properties and applications:
1. Kapton® Polyimide PCBs
Kapton® is a registered trademark of DuPont™ and is one of the most widely used polyimide films for PCBs. Kapton® polyimide PCBs offer excellent electrical insulation, high heat resistance, and good dimensional stability. They are commonly used in aerospace, automotive, and medical applications.
2. Upilex® Polyimide PCBs
Upilex® is a polyimide film developed by Ube Industries, Ltd. It has similar properties to Kapton® but with even higher heat resistance and dimensional stability. Upilex® polyimide PCBs are often used in high-temperature applications, such as power electronics and LED lighting.
3. Flexible Polyimide PCBs
Flexible polyimide PCBs are made by laminating thin layers of polyimide film with copper traces. They are lightweight, flexible, and can be bent or folded to fit into tight spaces. Flexible polyimide PCBs are used in wearable electronics, medical devices, and aerospace applications.
4. Rigid-Flex Polyimide PCBs
Rigid-flex polyimide PCBs combine the benefits of both rigid and flexible PCBs. They consist of rigid PCB sections connected by flexible polyimide sections, allowing for a more compact and reliable design. Rigid-flex polyimide PCBs are used in applications that require high density and reliability, such as smartphones, tablets, and medical devices.
Benefits of Polyimide PCBs
Polyimide PCBs offer several advantages over traditional FR-4 PCBs:
1. High Temperature Resistance
Polyimide PCBs can withstand extreme temperatures, ranging from -269°C to +400°C, making them suitable for high-temperature applications such as aerospace, automotive, and power electronics.
Material | Temperature Range |
---|---|
FR-4 | -55°C to +125°C |
Polyimide | -269°C to +400°C |
2. Excellent Mechanical Strength
Polyimide films have high tensile strength and low coefficient of thermal expansion (CTE), which results in PCBs with excellent mechanical strength and dimensional stability. This makes polyimide PCBs less prone to warping and cracking under stress.
3. Chemical Resistance
Polyimide PCBs are resistant to many chemicals and solvents, including acids, bases, and organic solvents. This makes them suitable for applications in harsh chemical environments, such as chemical processing and medical devices.
4. High Electrical Insulation
Polyimide films have high dielectric strength and low dielectric constant, which provides excellent electrical insulation for PCBs. This helps to reduce signal loss and cross-talk between traces, improving the overall performance of the circuit.
Property | Polyimide | FR-4 |
---|---|---|
Dielectric Constant | 3.5 | 4.7 |
Dielectric Strength (kV/mm) | 280 | 20 |
5. Lightweight and Flexible
Polyimide PCBs, especially flexible and rigid-flex variants, are lightweight and can be bent or folded to fit into tight spaces. This makes them ideal for applications where weight and space are critical, such as aerospace and wearable electronics.
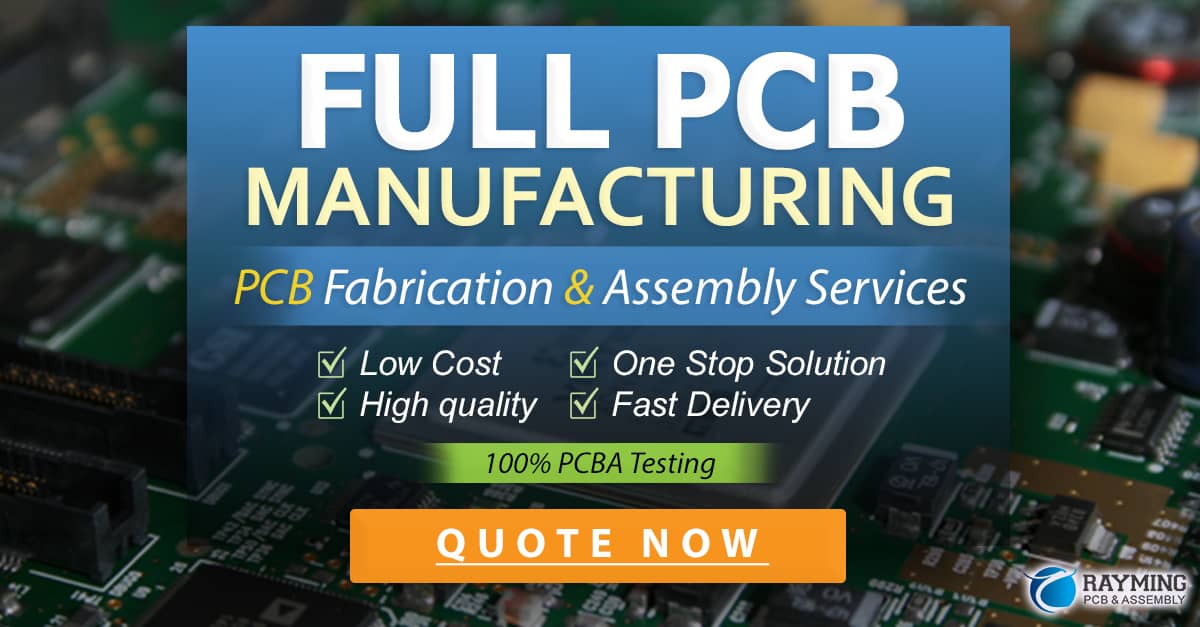
Applications of Polyimide PCBs
Polyimide PCBs find applications in various industries due to their unique properties:
1. Aerospace
Polyimide PCBs are used in satellites, aircraft, and spacecraft due to their ability to withstand extreme temperatures, vibrations, and radiation. They are used in communication systems, guidance systems, and power electronics.
2. Automotive
In the automotive industry, polyimide PCBs are used in engine control units, sensors, and battery management systems. They can withstand the high temperatures and vibrations present in automotive environments.
3. Medical Devices
Polyimide PCBs are used in medical devices such as pacemakers, implantable defibrillators, and hearing aids. They are biocompatible, reliable, and can withstand sterilization processes.
4. Power Electronics
Polyimide PCBs are used in power electronics applications such as solar inverters, wind turbines, and electric vehicle chargers. They can handle high currents and temperatures without degrading.
5. Wearable Electronics
Flexible polyimide PCBs are used in wearable electronics such as smartwatches, fitness trackers, and medical monitoring devices. They are lightweight, flexible, and can conform to the shape of the human body.
FAQ
1. Are polyimide PCBs more expensive than FR-4 PCBs?
Yes, polyimide PCBs are generally more expensive than FR-4 PCBs due to the higher cost of polyimide materials and the specialized manufacturing processes required. However, the higher cost is often justified by the superior performance and reliability of polyimide PCBs in demanding applications.
2. Can polyimide PCBs be soldered using standard methods?
Yes, polyimide PCBs can be soldered using standard methods such as reflow soldering and wave soldering. However, due to the high temperature resistance of polyimide, higher soldering temperatures may be required compared to FR-4 PCBs.
3. Are polyimide PCBs environmentally friendly?
Polyimide PCBs are generally considered more environmentally friendly than FR-4 PCBs, as they do not contain halogenated flame retardants, which can be harmful to the environment. However, the disposal of polyimide PCBs should still be done in accordance with local regulations to minimize environmental impact.
4. How do I choose between different types of polyimide PCBs?
The choice between different types of polyimide PCBs depends on the specific requirements of your application. Factors to consider include temperature range, mechanical stress, chemical exposure, and space constraints. Consult with a PCB manufacturer or design engineer to determine the most suitable type of polyimide PCB for your project.
5. Can polyimide PCBs be used in consumer electronics?
While polyimide PCBs are more commonly used in industrial and specialized applications, they can also be used in consumer electronics where high reliability and durability are required. Examples include smartphones, tablets, and high-end audio equipment. However, the higher cost of polyimide PCBs may limit their use in cost-sensitive consumer applications.
Conclusion
Polyimide PCBs offer a high-performance alternative to traditional FR-4 PCBs, with superior thermal stability, mechanical strength, and chemical resistance. They are available in various types, including Kapton®, Upilex®, flexible, and rigid-flex variants, each with unique properties and applications.
While polyimide PCBs are more expensive than FR-4 PCBs, their benefits make them the preferred choice for demanding applications in industries such as aerospace, automotive, medical devices, power electronics, and wearable electronics. As technology advances and the demand for reliable and durable PCBs grows, polyimide PCBs are expected to find even broader applications in the future.
0 Comments