Understanding the Basics of PCB Design
Before diving into the process of building a circuit board, it’s essential to understand the fundamentals of PCB design. A PCB is a flat board made of insulating material, such as fiberglass or plastic, with conductive traces printed on its surface. These traces connect various electronic components, forming a complete circuit.
Types of PCBs
There are three main types of PCBs:
- Single-sided PCBs: These boards have conductive traces on only one side of the insulating material.
- Double-sided PCBs: These boards have conductive traces on both sides of the insulating material, allowing for more complex circuits and denser component placement.
- Multi-layer PCBs: These boards consist of multiple layers of insulating material and conductive traces, enabling even more complex designs and higher component density.
PCB Design Software
To create a PCB, you’ll need to use specialized software that allows you to design the circuit schematic and layout the components on the board. Some popular PCB design software options include:
These software tools provide a user-friendly interface for designing your circuit and generating the necessary files for manufacturing.
Step 1: Create Your Circuit Schematic
The first step in building a DIY PCB is to create a schematic diagram of your circuit. A schematic is a visual representation of the electronic components and their interconnections.
Choosing Components
When selecting components for your circuit, consider factors such as:
- Voltage and current ratings
- Package size and type
- Availability and cost
- Functionality and performance
Be sure to choose components that are compatible with your PCB design software and can be easily sourced.
Drawing the Schematic
Using your chosen PCB design software, create a new schematic document and begin placing the components. Most software tools provide libraries of common components, making it easy to find and place the parts you need.
Connect the components using wires or nets, following the logical flow of your circuit. Be sure to label all components and nets clearly to avoid confusion during the layout process.
Step 2: Design the PCB Layout
Once your schematic is complete, it’s time to design the physical layout of your PCB. This involves arranging the components on the board and routing the conductive traces between them.
Component Placement
When placing components on the board, consider the following factors:
- Functional grouping: Place related components close together to minimize trace lengths and improve signal integrity.
- Mechanical constraints: Ensure that components do not interfere with mounting holes, connectors, or other mechanical features.
- Thermal considerations: Position heat-generating components, such as voltage regulators, away from sensitive components to avoid thermal issues.
Trace Routing
After placing the components, route the conductive traces between them according to the connections defined in your schematic. Keep these guidelines in mind:
- Trace width: Choose appropriate trace widths based on the current carrying requirements of your circuit. Wider traces can handle higher currents.
- Trace spacing: Maintain sufficient spacing between traces to avoid short circuits and minimize crosstalk.
- Via placement: Use vias (plated holes) to connect traces on different layers of the board when necessary.
Design Rule Check (DRC)
Before finalizing your PCB layout, run a Design Rule Check (DRC) to ensure that your design meets the manufacturing requirements and constraints. The DRC will highlight any issues, such as trace spacing violations or unconnected nets, allowing you to fix them before proceeding.
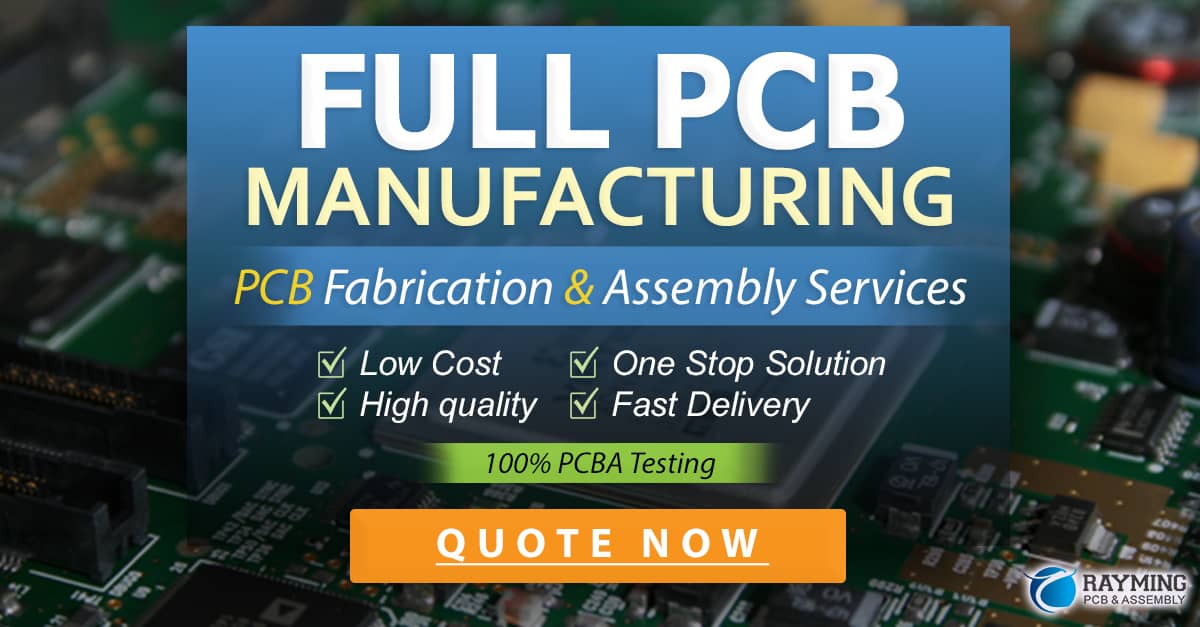
Step 3: Generate Manufacturing Files
With your PCB layout complete, it’s time to generate the files needed for manufacturing. These files provide the necessary information for fabricating your board.
Gerber Files
Gerber files are the industry standard for PCB fabrication. They contain the information required to create the conductive traces, solder mask, and silkscreen layers of your board. Most PCB design software can generate Gerber files automatically.
Drill Files
In addition to Gerber files, you’ll need to generate drill files that specify the location and size of the holes in your board. These holes are used for mounting components and creating vias.
BOM and Assembly Files
To aid in the assembly process, generate a Bill of Materials (BOM) that lists all the components used in your design, along with their quantities and part numbers. Additionally, create assembly files that show the placement of each component on the board.
Step 4: Fabricate and Assemble Your PCB
With your manufacturing files ready, it’s time to fabricate and assemble your PCB.
PCB Fabrication
You can choose to fabricate your PCB in-house using a PCB Milling machine or send your files to a professional PCB manufacturing service. Professional services offer higher quality and reliability, as well as the ability to produce more complex designs.
When selecting a PCB manufacturer, consider factors such as:
- Turnaround time
- Cost
- Minimum order quantity
- Supported PCB specifications (layers, materials, etc.)
PCB Assembly
Once your PCB is fabricated, it’s time to assemble the components. You can choose to assemble the board manually or use a pick-and-place machine for automated assembly.
If assembling manually, follow these steps:
- Apply solder paste to the pads on the board using a stencil or syringe.
- Place the components on the board according to the assembly files.
- Reflow the solder paste using a reflow oven or hot air gun.
- Inspect the board for any soldering defects or misplaced components.
Step 5: Test and Debug Your PCB
After assembling your PCB, it’s crucial to test and debug it to ensure proper functionality.
Visual Inspection
Begin by visually inspecting the board for any obvious issues, such as:
- Solder bridges or shorts
- Unsoldered or misaligned components
- Damaged traces or pads
Power-On Testing
Apply power to your board and verify that it powers on correctly without any smoke or unusual odors. Use a multimeter to check the voltage levels at various points on the board.
Functional Testing
Test the functionality of your circuit by applying input signals and measuring the output. Compare the results with your expected values based on the schematic design.
Debugging
If you encounter any issues during testing, use a combination of visual inspection, multimeter measurements, and oscilloscope analysis to identify the root cause. Common debugging techniques include:
- Checking for continuity between traces and components
- Verifying component values and orientations
- Probing signals with an oscilloscope to identify timing or noise issues
Once you’ve identified and fixed any problems, reassemble the board and repeat the testing process to ensure proper functionality.
FAQ
-
What tools do I need to build a DIY PCB?
To build a DIY PCB, you’ll need a computer with PCB design software, a printer for creating templates, a PCB milling machine or access to a PCB fabrication service, soldering tools (soldering iron, solder, flux), and basic electronic testing equipment (multimeter, oscilloscope). -
Can I make a PCB without using a PCB design software?
While it’s theoretically possible to design a simple PCB by hand, using PCB design software is highly recommended. These software tools automate many of the complex tasks involved in PCB design, such as component placement, trace routing, and design rule checking, making the process much faster and less error-prone. -
How much does it cost to fabricate a PCB?
The cost of PCB fabrication varies depending on factors such as the board size, complexity, number of layers, and quantity. Professional PCB manufacturing services typically charge based on the board area and the number of boards ordered. Small, simple boards can cost as little as a few dollars each, while larger, more complex boards can cost several hundred dollars or more. -
What are the advantages of making my own PCBs?
Making your own PCBs offers several advantages, including: - Cost savings compared to purchasing pre-made boards
- Ability to customize the design to your specific requirements
- Faster turnaround time for prototyping and testing
-
Opportunity to learn and develop PCB design and fabrication skills
-
How long does it take to build a DIY PCB?
The time required to build a DIY PCB depends on the complexity of the design and your level of experience. A simple, single-sided board can be designed, fabricated, and assembled in a few hours, while a complex, multi-layer board may take several days or even weeks. With practice and experience, you can streamline the process and reduce the time required to build your own PCBs.
Conclusion
Building your own circuit boards can be a fun and rewarding experience for anyone interested in electronics and DIY projects. By following the key steps outlined in this guide, you can create Custom PCBs tailored to your specific needs and bring your electronic designs to life.
Remember to start with a clear schematic, design a functional and manufacturable PCB layout, generate accurate manufacturing files, and carefully assemble and test your board. With practice and patience, you’ll soon be creating professional-quality PCBs in the comfort of your own home or workshop.
Happy PCB building!
0 Comments