Introduction to PCB Design
Printed Circuit Board (PCB) design is a crucial aspect of electronics manufacturing. A well-designed PCB not only ensures the proper functioning of the electronic device but also enhances its aesthetic appeal. In this article, we will explore the essential steps and techniques involved in creating a professional and visually appealing PCB design.
Understanding the Basics of PCB Design
PCB Layers and Materials
PCBs are typically composed of multiple layers of conductive and insulating materials. The most common materials used in PCB manufacturing are:
Material | Description |
---|---|
FR-4 | A flame-retardant composite material widely used as the base substrate for PCBs. |
Copper | A highly conductive metal used for creating the conductive traces and pads on the PCB. |
Solder Mask | A protective layer applied over the copper traces to prevent short circuits and improve the PCB’s appearance. |
Silkscreen | A printed layer used for adding text, logos, and component markings on the PCB surface. |
PCB Design Software
To create a professional PCB design, you’ll need to use specialized software tools. Some popular PCB design software options include:
- Altium Designer
- Eagle CAD
- KiCad
- OrCAD
These software tools provide a wide range of features and capabilities, allowing you to create complex PCB designs with ease.
Planning Your PCB Design
Schematic Capture
The first step in PCB design is to create a schematic diagram of your electronic circuit. The schematic captures the logical connections between components and serves as a blueprint for the PCB layout. When creating a schematic, consider the following:
- Use clear and consistent component symbols
- Assign unique reference designators to each component
- Provide detailed information about component values and part numbers
Component Placement
Once you have completed the schematic, you can start placing components on the PCB layout. Consider the following factors when placing components:
- Group related components together to minimize trace lengths
- Place heat-generating components away from sensitive components
- Ensure proper clearance between components for manufacturing and assembly
Routing and Trace Width
After placing the components, you need to route the traces that connect them. When routing traces, keep in mind:
- Use appropriate trace widths based on the current carrying requirements
- Maintain proper spacing between traces to avoid signal interference
- Avoid sharp angles and use smooth curves for trace routing
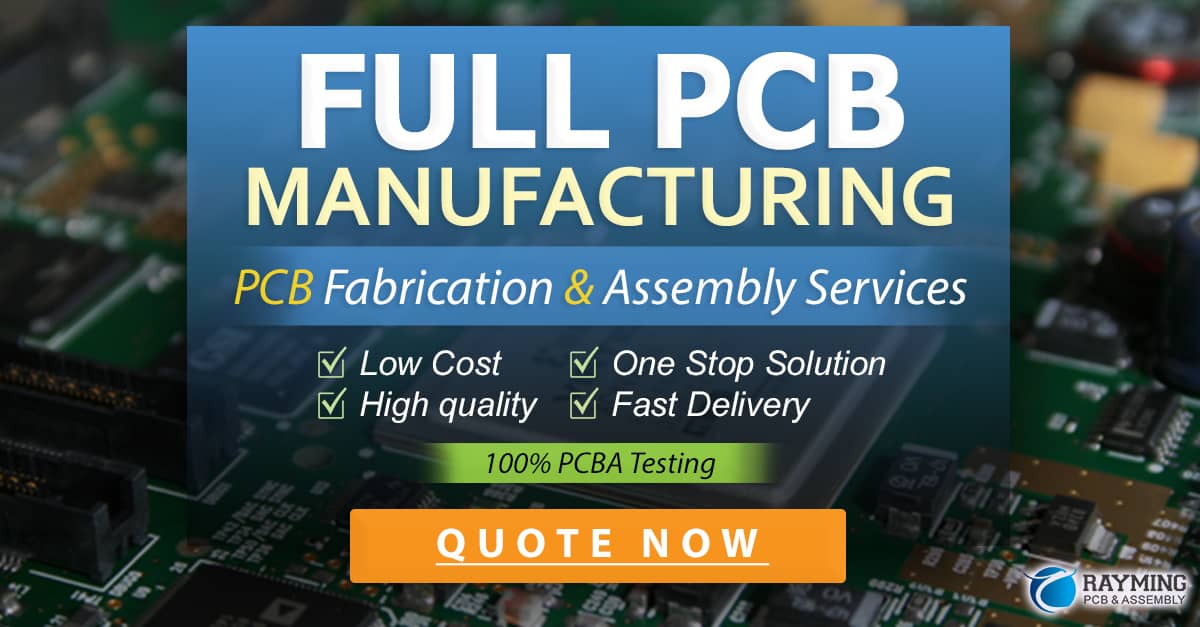
Enhancing the Visual Appeal of Your PCB
Choosing a Color Scheme
The color scheme of your PCB can greatly impact its visual appeal. Consider the following tips when selecting colors:
- Use contrasting colors for the solder mask and silkscreen layers
- Choose colors that complement the overall design and branding of your product
- Ensure the colors are easily distinguishable for assembly and inspection purposes
Creating Unique Shapes and Patterns
To make your PCB design stand out, you can incorporate unique shapes and patterns. Some ideas include:
- Using curved or angled board outlines
- Incorporating decorative copper fills or hatched polygons
- Adding artistic silkscreen graphics or logos
Optimizing Text and Labels
Clear and legible text and labels are essential for a professional PCB design. Consider the following guidelines:
- Use a consistent font style and size for component labels and markings
- Ensure text is easily readable against the background color
- Place labels and markings in a way that does not interfere with component placement or trace routing
PCB Manufacturing Considerations
Design for Manufacturing (DFM)
To ensure your PCB design can be manufactured efficiently and reliably, follow these Design for Manufacturing (DFM) guidelines:
- Adhere to the minimum trace width and spacing requirements specified by your PCB manufacturer
- Provide sufficient clearance around mounting holes and board edges
- Avoid placing components or traces too close to the board edge
Panelization and Tooling
If you’re producing multiple PCBs, consider panelization to optimize the manufacturing process. Panelization involves grouping multiple PCB designs into a single panel for fabrication. When panelizing your design, keep in mind:
- Include appropriate tooling holes and fiducial markers for automated assembly
- Provide sufficient spacing between individual PCBs to allow for depaneling
- Verify the panel size and layout with your PCB manufacturer
Testing and Verification
Design Rule Checking (DRC)
Before sending your PCB design for manufacturing, perform a Design Rule Check (DRC) to ensure it meets the specified design rules. DRC helps identify potential issues such as:
- Trace width and spacing violations
- Unconnected or shorted traces
- Component clearance and overlap issues
Prototype and Testing
Once your PCB design is finalized and manufactured, it’s essential to test and verify its functionality. Consider the following steps:
- Visually inspect the PCB for any manufacturing defects or assembly issues
- Perform electrical continuity tests to ensure proper connections
- Conduct functional testing to validate the PCB’s performance against the design specifications
Frequently Asked Questions (FAQ)
1. What is the typical turnaround time for PCB manufacturing?
The turnaround time for PCB manufacturing varies depending on the complexity of the design, the chosen manufacturing options, and the manufacturer’s workload. Typically, standard PCB orders can take anywhere from a few days to a couple of weeks. Rush services may be available for faster turnaround times, but they often come at a higher cost.
2. How can I ensure my PCB design is compatible with the components I plan to use?
To ensure compatibility between your PCB design and the selected components, follow these steps:
- Carefully review the component datasheets and application notes to understand their dimensions, pinouts, and recommended footprints
- Use the correct footprint libraries provided by the component manufacturers or create custom footprints based on their specifications
- Verify the component footprints in your PCB design software to ensure they match the actual component dimensions
3. What are the common file formats used for PCB design?
The most common file formats used in PCB design include:
- Gerber files: Industry-standard format for PCB Fabrication data
- Drill files: Specifies the locations and sizes of drilled holes on the PCB
- Bill of Materials (BOM): A list of all components used in the PCB design
- Pick and Place files: Provides information for automated component placement during assembly
4. How do I choose the right PCB Thickness for my design?
The choice of PCB thickness depends on several factors, such as:
- The mechanical requirements of your application (e.g., durability, stiffness)
- The number of layers required for your design
- The components used and their mounting requirements
- The PCB manufacturing capabilities of your chosen fabrication house
Common PCB thicknesses range from 0.6mm to 2.0mm, with 1.6mm being a popular choice for many applications. Consult with your PCB manufacturer to determine the most suitable thickness for your specific design.
5. What are the benefits of using a 4-layer PCB over a 2-layer PCB?
Using a 4-layer PCB offers several advantages over a 2-layer PCB:
- Improved signal integrity: The additional layers allow for dedicated power and ground planes, reducing noise and improving signal quality
- Better EMI/EMC performance: The power and ground planes help shield sensitive signals from electromagnetic interference (EMI) and improve electromagnetic compatibility (EMC)
- Increased routing space: With more layers available, you have greater flexibility in routing traces and avoiding congestion
- Enhanced thermal management: The power and ground planes can help distribute heat more evenly across the PCB, improving thermal performance
However, 4-layer PCBs are more expensive to manufacture compared to 2-layer PCBs. The choice between the two depends on the specific requirements and constraints of your design.
Conclusion
Designing a professional and visually appealing PCB requires a combination of technical expertise and creative flair. By understanding the basics of PCB design, planning your layout carefully, and incorporating unique visual elements, you can create PCBs that are both functional and aesthetically pleasing.
Remember to consider manufacturability, test your design thoroughly, and collaborate closely with your PCB manufacturer to ensure the best possible outcome. With practice and attention to detail, you can master the art of PCB design and bring your electronic ideas to life.
0 Comments