What is Flex Board Manufacturing?
Flex board manufacturing, also known as flexible printed circuit board (PCB) manufacturing, is a process of creating electronic circuits on flexible substrates. These substrates are typically made of polyimide or polyester materials, which allow the board to bend and flex without breaking the electrical connections.
Flex boards offer several advantages over traditional Rigid PCBs, including:
- Increased durability and reliability
- Reduced weight and space requirements
- Improved electrical performance
- Enhanced design flexibility
Types of Flex Boards
There are three main types of flex boards:
- Single-sided flex boards
- Consist of a single layer of conductive material on a flexible substrate
-
Used in simple, low-density applications
-
Double-sided flex boards
- Have conductive layers on both sides of the flexible substrate
-
Offer higher component density and more complex routing compared to single-sided boards
-
Multi-layer flex boards
- Consist of multiple layers of conductive material separated by insulating layers
- Used in high-density, complex applications that require advanced electrical performance
The Flex Board Manufacturing Process
The flex board manufacturing process involves several key steps:
1. Design and Layout
The first step in flex board manufacturing is designing the circuit layout using specialized software. The design must consider the unique properties of flexible substrates, such as bend radius and material thickness.
2. Material Selection
Choosing the appropriate flexible substrate and conductive materials is crucial for the performance and reliability of the final product. Common substrate materials include:
- Polyimide (PI)
- Polyethylene terephthalate (PET)
- Polyethylene naphthalate (PEN)
Conductive materials are typically copper foils, which come in various thicknesses and grades.
3. Lamination
The flexible substrate and conductive layers are laminated together using heat and pressure. This process ensures a strong bond between the layers and prevents delamination during use.
4. Patterning
The desired circuit pattern is transferred onto the laminated board using photolithography. This process involves applying a photoresist layer, exposing it to UV light through a photomask, and developing the resist to reveal the desired pattern.
5. Etching
The exposed copper is etched away using a chemical solution, leaving only the desired circuit pattern on the flexible substrate.
6. Drilling and Cutting
Holes for through-hole components and vias are drilled into the board using specialized equipment. The board is then cut to its final shape using a die-cutting process or laser cutting.
7. Surface Finishing
A surface finish, such as gold plating or solder mask, is applied to protect the copper traces and improve solderability.
8. Assembly and Testing
The flexible board is populated with components using standard surface-mount or through-hole assembly techniques. The assembled board is then tested for functionality and reliability.
Advantages of Flex Board Manufacturing
Flex board manufacturing offers several advantages over traditional rigid PCB manufacturing:
- Increased Reliability
- Flex boards can withstand vibration, shock, and thermal stress better than rigid boards
-
Reduced risk of component failure due to mechanical stress
-
Space and Weight Savings
- Flex boards can be bent and folded to fit into tight spaces
-
Reduced overall system weight due to the use of lightweight substrate materials
-
Improved Electrical Performance
- Shorter signal paths and reduced parasitic inductance and capacitance
-
Better high-frequency performance and reduced electromagnetic interference (EMI)
-
Enhanced Design Flexibility
- Ability to create three-dimensional designs and integrate multiple circuit functions into a single board
- Simplified assembly and reduced connector requirements
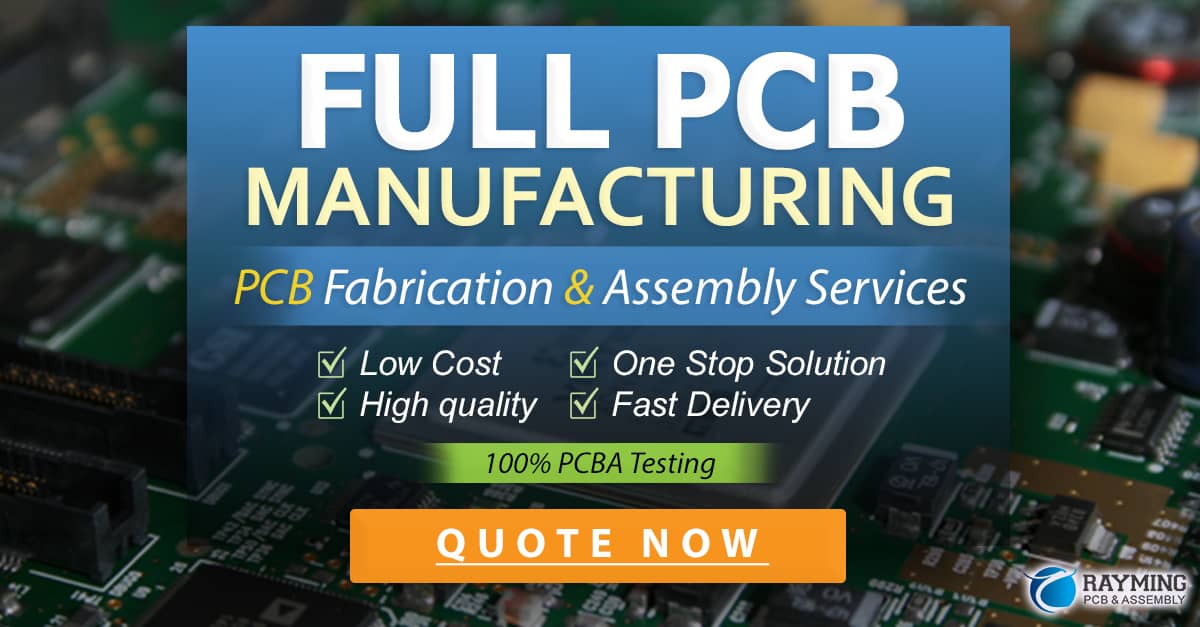
Applications of Flex Boards
Flex boards are used in a wide range of industries and applications, including:
- Consumer Electronics
- Smartphones, tablets, and wearable devices
-
Digital cameras and portable media players
-
Medical Devices
- Implantable devices, such as pacemakers and hearing aids
-
Diagnostic equipment and patient monitoring systems
-
Automotive Electronics
- In-vehicle infotainment systems and dashboard displays
-
Sensors and control modules
-
Aerospace and Defense
- Avionics systems and satellite communications
-
Military-grade electronics and ruggedized devices
-
Industrial Automation
- Robotics and machine vision systems
- Process control and data acquisition equipment
Choosing a Flex Board Manufacturer
When selecting a flex board manufacturer, consider the following factors:
- Experience and Expertise
- Look for a manufacturer with a proven track record in flex board fabrication
-
Ensure they have experience with your specific application and industry
-
Manufacturing Capabilities
- Verify that the manufacturer has the necessary equipment and processes to meet your requirements
-
Consider their ability to handle high-volume production and quick-turn prototyping
-
Quality Control and Certifications
- Choose a manufacturer with strict quality control processes and relevant certifications (e.g., ISO 9001, IPC)
-
Ask about their testing and inspection procedures to ensure product reliability
-
Customer Support and Communication
- Select a manufacturer that offers responsive customer support and clear communication
- Ensure they are willing to work closely with you throughout the design and manufacturing process
Frequently Asked Questions (FAQ)
- What is the difference between flex boards and rigid PCBs?
-
Flex boards are made of flexible substrate materials, allowing them to bend and flex without breaking. Rigid PCBs are made of solid, non-flexible materials and are used in applications where mechanical stability is required.
-
Can flex boards be used in high-temperature environments?
-
Yes, certain flexible substrate materials, such as polyimide, can withstand high temperatures (up to 200°C or more). However, the specific temperature rating depends on the material and construction of the flex board.
-
How do I choose the right flex board material for my application?
-
The choice of flex board material depends on several factors, including the operating environment, required flexibility, and cost. Consult with your flex board manufacturer to select the most suitable material for your specific application.
-
Are flex boards more expensive than rigid PCBs?
-
In general, flex boards are more expensive than rigid PCBs due to the specialized materials and manufacturing processes involved. However, the overall system cost may be lower due to reduced assembly and connector requirements.
-
What are the common challenges in flex board manufacturing?
- Common challenges include maintaining consistent material properties during the manufacturing process, ensuring proper adhesion between layers, and managing the mechanical stress on components during flexing. Experienced flex board manufacturers have developed processes to mitigate these challenges and ensure reliable product performance.
Conclusion
Flex board manufacturing is a rapidly growing industry that offers numerous advantages over traditional rigid PCB manufacturing. With their increased reliability, space and weight savings, improved electrical performance, and enhanced design flexibility, flex boards are becoming increasingly popular in a wide range of industries and applications.
When selecting a flex board manufacturer, it is essential to consider factors such as experience, manufacturing capabilities, quality control, and customer support. By partnering with a reputable and experienced manufacturer, you can ensure that your flex board project is completed on time, within budget, and to the highest quality standards.
As technology continues to advance and the demand for smaller, lighter, and more flexible electronic devices grows, the importance of flex board manufacturing will only continue to increase. By staying informed about the latest developments and trends in this exciting field, you can position yourself and your organization to take full advantage of the many benefits that flex boards have to offer.
Flex Board Type | Advantages | Disadvantages |
---|---|---|
Single-sided | – Simple and low-cost – Suitable for low-density applications |
– Limited routing and component placement options – Not suitable for complex designs |
Double-sided | – Increased component density and routing options – Improved electrical performance |
– More expensive than single-sided boards – Requires more advanced manufacturing processes |
Multi-layer | – Highest component density and routing options – Best electrical performance |
– Most expensive and complex to manufacture – Longer lead times and higher minimum order quantities |
0 Comments