What are Rigid PCBs?
Rigid PCBs are a type of printed circuit board characterized by their solid, inflexible substrate material. These boards are typically made from a combination of fiberglass and epoxy resin, which provides excellent mechanical stability and electrical insulation. The conductive traces and pads on rigid PCBs are usually made of copper, allowing for the efficient transfer of electrical signals between components.
Advantages of Rigid PCBs
Rigid PCBs offer several advantages over other types of printed circuit boards, such as flexible or flex-rigid PCBs. Some of the key benefits include:
-
Durability: The solid substrate material of rigid PCBs makes them highly resistant to physical stress, vibration, and impact, ensuring long-term reliability in demanding environments.
-
Thermal stability: Rigid PCBs can withstand higher operating temperatures compared to flexible PCBs, making them suitable for applications with elevated thermal requirements.
-
High-density layouts: The rigidity of the substrate allows for the creation of high-density layouts with fine pitch components and narrow trace widths, enabling the design of compact and complex electronic circuits.
-
Cost-effectiveness: Rigid PCBs are generally more cost-effective than flexible or flex-rigid PCBs, especially for high-volume production runs.
Rigid PCB Construction and Materials
Rigid PCBs are constructed using a multi-layer process, with each layer consisting of a dielectric substrate material and conductive copper traces. The most common substrate material used in rigid PCBs is FR-4, a composite made from woven fiberglass cloth impregnated with epoxy resin. Other substrate materials, such as ceramic or metal-core PCBs, may be used for specific applications requiring enhanced thermal dissipation or high-frequency performance.
Copper Layers and Trace Widths
The conductive traces on rigid PCBs are typically made of copper, with varying thicknesses depending on the desired current carrying capacity and signal integrity requirements. Standard copper thicknesses for rigid PCBs range from 0.5 oz/ft² to 3 oz/ft², with 1 oz/ft² being the most common. Trace widths can vary from a few mils (thousandths of an inch) to several millimeters, depending on the design constraints and manufacturing capabilities.
Solder Mask and Silkscreen
Rigid PCBs are often coated with a solder mask, a protective layer that covers the copper traces and pads, leaving only the areas intended for soldering exposed. The solder mask helps prevent accidental short circuits and provides a barrier against environmental factors such as moisture and contaminants. Additionally, a silkscreen layer is applied to the PCB surface to add text, logos, and component identifiers, aiding in the assembly and troubleshooting processes.
Rigid PCB Manufacturing Process
The manufacturing process for rigid PCBs involves several key steps, each contributing to the final quality and functionality of the board. These steps include:
-
Design and layout: The PCB design is created using specialized software, taking into account the component placement, signal routing, and manufacturing constraints.
-
Substrate preparation: The substrate material is cut to the desired size and shape, and any necessary holes or slots are drilled or punched.
-
Copper deposition: A thin layer of copper is deposited onto the substrate using electroless plating or electrodeposition techniques.
-
Photoresist application: A photosensitive resist material is applied to the copper surface and exposed to UV light through a photomask, which defines the desired trace and pad patterns.
-
Etching: The exposed copper areas are etched away using a chemical solution, leaving only the desired conductive patterns on the substrate.
-
Solder mask and silkscreen application: The solder mask and silkscreen layers are applied to the PCB surface using screen printing or photoimaging techniques.
-
Surface finish: A protective surface finish, such as HASL (Hot Air Solder Leveling), ENIG (Electroless Nickel Immersion Gold), or OSP (Organic Solderability Preservative), is applied to the exposed copper areas to enhance solderability and prevent oxidation.
-
Electrical testing: The manufactured PCBs undergo rigorous electrical testing to ensure proper functionality and adherence to design specifications.
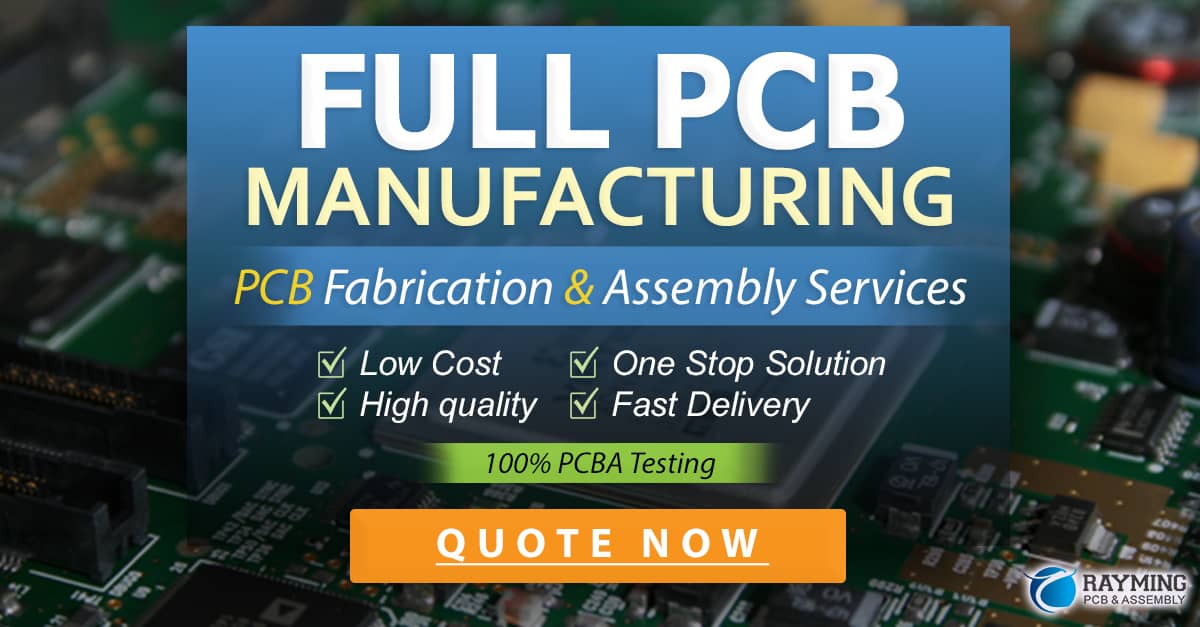
Rigid PCB Applications
Rigid PCBs find applications in a wide range of industries and products, thanks to their reliability, durability, and versatility. Some of the most common applications include:
-
Consumer electronics: Smartphones, tablets, laptops, and home appliances rely heavily on rigid PCBs for their internal circuitry.
-
Automotive: Modern vehicles incorporate numerous rigid PCBs for various systems, such as engine control, infotainment, and driver assistance.
-
Industrial equipment: Rigid PCBs are used in industrial automation, process control, and monitoring systems, where reliability and robustness are critical.
-
Medical devices: Diagnostic and therapeutic equipment, such as MRI machines, patient monitors, and surgical instruments, employ rigid PCBs for their electronic functionality.
-
Aerospace and defense: Rigid PCBs are essential components in avionics, satellite systems, and military equipment, where high performance and reliability are paramount.
Future Trends in Rigid PCBs
As technology advances and electronic devices become increasingly complex, rigid PCBs must adapt to meet the evolving demands of the industry. Some of the key trends shaping the future of rigid PCBs include:
-
Miniaturization: The ongoing push for smaller, more compact electronic devices drives the need for high-density PCB layouts with smaller components and tighter tolerances.
-
High-speed applications: The growing demand for high-speed data transmission and processing requires rigid PCBs with improved signal integrity and controlled impedance characteristics.
-
Advanced materials: The development of new substrate materials, such as high-frequency laminates and metal-core PCBs, enables the design of rigid PCBs for specialized applications with enhanced thermal and electrical performance.
-
Embedded components: The integration of passive components, such as resistors and capacitors, directly into the PCB substrate helps reduce board size and improve overall system performance.
-
Environmental sustainability: The increasing focus on environmental responsibility drives the adoption of lead-free and halogen-free materials in rigid PCB manufacturing, as well as the development of more eco-friendly production processes.
Frequently Asked Questions (FAQ)
-
What is the difference between rigid and flexible PCBs?
Rigid PCBs have a solid, inflexible substrate, while flexible PCBs use a thin, pliable substrate material that allows the board to bend and conform to various shapes. Rigid PCBs offer greater durability and thermal stability, while flexible PCBs are ideal for applications requiring flexibility or space-constrained designs. -
Can rigid PCBs be multi-layered?
Yes, rigid PCBs can be designed with multiple layers, allowing for more complex routing and higher component density. Multi-layer rigid PCBs are commonly used in applications requiring high functionality and compact form factors. -
What is the typical turnaround time for rigid PCB manufacturing?
The turnaround time for rigid PCB manufacturing varies depending on the complexity of the design, the chosen manufacturer, and the order quantity. Standard lead times can range from a few days to several weeks, with expedited options available for time-critical projects. -
How do I choose the right surface finish for my rigid PCB?
The choice of surface finish depends on factors such as the intended application, soldering requirements, and environmental conditions. Common surface finishes include HASL, ENIG, and OSP, each with its own advantages and limitations. Consult with your PCB manufacturer or design team to determine the most suitable surface finish for your specific needs. -
What are the key considerations when designing a rigid PCB layout?
When designing a rigid PCB layout, it is essential to consider factors such as component placement, signal routing, power distribution, thermal management, and manufacturability. Adhering to design guidelines and collaborating closely with your PCB manufacturer can help ensure a successful and cost-effective design.
Conclusion
Rigid PCBs are a fundamental component of modern electronics, providing a reliable and efficient means of interconnecting electronic components in a wide range of applications. By understanding the construction, materials, manufacturing processes, and applications of rigid PCBs, designers and engineers can create robust and high-performing electronic systems that meet the ever-evolving demands of the industry. As technology continues to advance, rigid PCBs will remain at the forefront of electronic design, adapting to new challenges and enabling the development of increasingly sophisticated and innovative devices.
Characteristic | Rigid PCBs | Flexible PCBs |
---|---|---|
Substrate Material | Solid, inflexible (e.g., FR-4) | Thin, pliable (e.g., polyimide) |
Durability | High | Moderate |
Thermal Stability | High | Moderate |
Component Density | High | Moderate |
Flexibility | Low | High |
Typical Applications | Consumer electronics, automotive, industrial equipment | Wearables, medical devices, aerospace |
Table 1: Comparison of key characteristics between rigid and flexible PCBs.
Surface Finish | Advantages | Disadvantages |
---|---|---|
HASL (Hot Air Solder Leveling) | Low cost, good solderability | Uneven surface, limited fine-pitch capability |
ENIG (Electroless Nickel Immersion Gold) | Flat surface, excellent solderability, long shelf life | Higher cost, potential for black pad formation |
OSP (Organic Solderability Preservative) | Low cost, flat surface, good for fine-pitch components | Limited shelf life, potential for poor solderability |
Table 2: Comparison of common surface finishes for rigid PCBs.
0 Comments