What is Heavy Copper PCB?
Heavy Copper PCBs are printed circuit boards that use thicker copper traces than standard PCBs. While a typical PCB uses 1-2 oz. copper (35-70 μm thick), heavy copper PCBs use copper traces ranging from 3 oz. to 20 oz. (105-700 μm thick). The thicker copper allows for higher current carrying capacity, better heat dissipation, and improved mechanical strength.
Applications of Heavy Copper PCBs
Heavy copper PCBs are used in various applications that require high current handling or better thermal management, such as:
- Power electronics (e.g., inverters, converters, motor drives)
- Automotive electronics (e.g., electric vehicle battery management systems)
- Industrial controls (e.g., welding equipment, large motors)
- Telecommunications (e.g., base stations, high-power amplifiers)
- Aerospace and defense (e.g., radar systems, avionics)
Heavy Copper PCB Manufacturing Process
The manufacturing process for heavy copper PCBs is similar to standard PCBs but with some additional steps and considerations due to the thicker copper.
1. PCB Design
Designing a heavy copper PCB requires taking into account the specific requirements of the application, such as current carrying capacity, thermal management, and mechanical strength. The designer must also consider the manufacturability of the board, as thicker copper traces may require adjustments to the design rules.
2. Material Selection
The base material for heavy copper PCBs is typically FR-4, a glass-reinforced epoxy laminate. However, other materials like aluminum or ceramic may be used for better thermal conductivity. The copper foil thickness is chosen based on the current carrying and heat dissipation requirements.
3. Lamination
The copper foil is laminated onto the base material using heat and pressure. For heavy copper PCBs, the lamination process may require higher temperatures and pressures to ensure proper bonding between the thick copper foil and the base material.
4. Drilling
Holes are drilled through the laminated board for vias, component leads, and mounting. Heavy copper PCBs may require specialized drills and drilling parameters to accommodate the thicker copper.
5. Plating
The drilled holes are plated with copper to create electrical connections between layers. Heavy copper PCBs may require longer plating times or special plating chemistries to ensure uniform coverage of the thick copper traces.
6. Patterning
The copper foil is patterned using photolithography and etching to create the desired circuit layout. Heavy copper PCBs may require longer etching times or special etching chemistries due to the thicker copper.
7. Solder Mask and Silkscreen
A solder mask is applied to protect the copper traces from oxidation and prevent solder bridging. Silkscreen is used to print component designators, logos, and other markings on the board.
8. Surface Finish
A surface finish, such as HASL (Hot Air Solder Leveling), ENIG (Electroless Nickel Immersion Gold), or OSP (Organic Solderability Preservative), is applied to the exposed copper to improve solderability and protect against oxidation.
9. Electrical Testing
The finished heavy copper PCB undergoes electrical testing to ensure proper functionality and adherence to specifications.
Advantages of Heavy Copper PCBs
Heavy copper PCBs offer several advantages over standard PCBs:
-
Higher current carrying capacity: Thicker copper traces can handle higher currents without overheating or suffering from voltage drops.
-
Better heat dissipation: The increased copper volume helps to spread heat more effectively, reducing hot spots and improving overall thermal management.
-
Improved mechanical strength: Thicker copper provides better mechanical support for components and connectors, reducing the risk of damage from vibration or mechanical stress.
-
Lower resistance: The increased cross-sectional area of the thicker copper traces results in lower electrical resistance, which can improve efficiency and reduce power losses.
-
Better EMI/RFI shielding: The thicker copper can provide better shielding against electromagnetic and radio frequency interference.
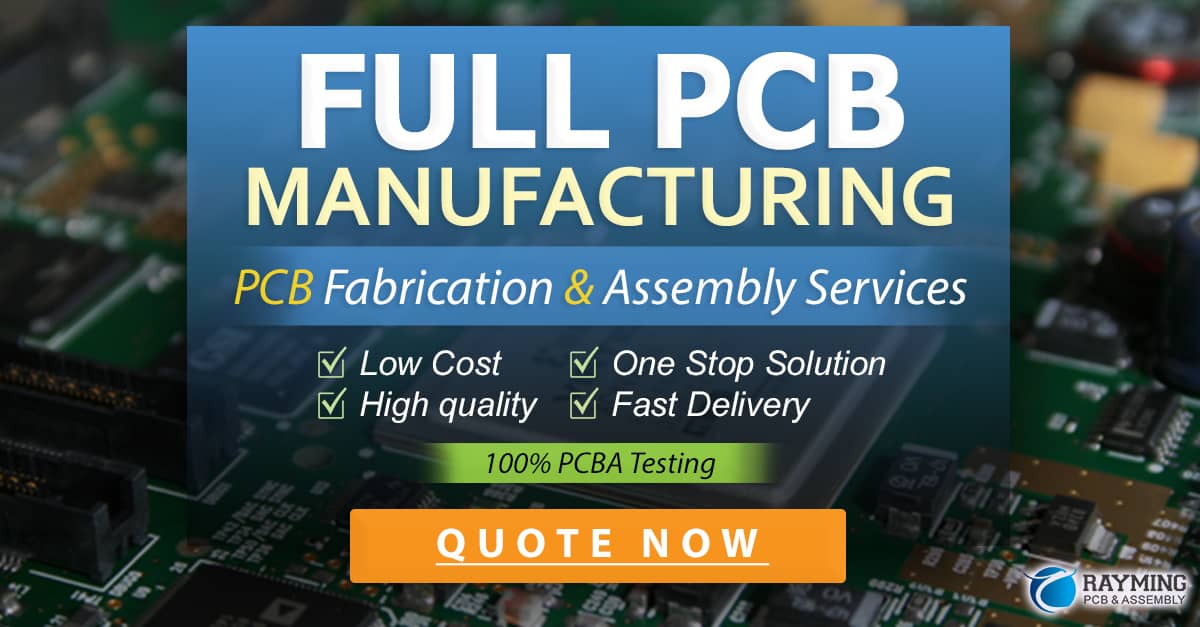
Challenges in Heavy Copper PCB Manufacturing
Manufacturing heavy copper PCBs presents some unique challenges compared to standard PCBs:
-
Increased material costs: Thicker copper foil and specialized base materials can increase the overall cost of the PCB.
-
Longer processing times: Thicker copper may require longer etching, plating, and drilling times, which can impact production throughput.
-
Special equipment and processes: Heavy copper PCBs may require specialized equipment and processes, such as high-pressure laminators, heavy-duty drills, and custom etching chemistries.
-
Design limitations: Thicker copper traces may limit the minimum trace width and spacing, requiring adjustments to the PCB design rules.
-
Thermal expansion mismatch: The difference in thermal expansion between the thick copper and the base material can cause stress and warpage, particularly during reflow soldering.
FAQ
1. What is the maximum copper thickness available for heavy copper PCBs?
The maximum copper thickness for heavy copper PCBs is typically 20 oz. (700 μm), although some specialized manufacturers may offer even thicker copper options.
2. Can heavy copper PCBs be used for high-frequency applications?
Heavy copper PCBs are generally not well-suited for high-frequency applications due to the increased skin effect and dielectric losses associated with thicker copper. For high-frequency applications, it is generally better to use standard or even thin copper PCBs with carefully controlled impedances.
3. Are heavy copper PCBs more expensive than standard PCBs?
Yes, heavy copper PCBs are generally more expensive than standard PCBs due to the increased material costs and specialized manufacturing processes required.
4. Can heavy copper PCBs be made with flexible substrates?
Yes, heavy copper Flexible PCBs are available, although they are less common than rigid heavy copper PCBs. Flexible heavy copper PCBs are often used in applications that require high current carrying capacity and flexibility, such as battery pack interconnects or power distribution in wearable devices.
5. Are there any special considerations for soldering heavy copper PCBs?
Soldering heavy copper PCBs may require adjustments to the reflow profile to ensure proper wetting and avoid thermal stress. The increased thermal mass of the thick copper can make it more difficult to achieve the desired temperature ramp rates and soak times. Additionally, the thermal expansion mismatch between the copper and the base material can cause warpage or delamination if not properly controlled.
Conclusion
Heavy copper PCBs offer unique advantages for applications that require high current carrying capacity, improved thermal management, and increased mechanical strength. However, manufacturing heavy copper PCBs presents some challenges, such as increased material costs, longer processing times, and design limitations. By understanding the properties and manufacturing processes of heavy copper PCBs, designers and engineers can make informed decisions about when and how to use them in their projects. As power electronics and other high-current applications continue to evolve, heavy copper PCBs will likely play an increasingly important role in enabling new technologies and innovations.
0 Comments