What is PCB Manufacturing?
PCB manufacturing is the process of designing and fabricating printed circuit boards (PCBs). PCBs are flat boards made of insulating materials like fiberglass, with conductive copper traces printed on the surface to connect electronic components. They are essential building blocks in virtually all modern electronic devices, from smartphones and laptops to industrial equipment and aerospace systems.
The PCB manufacturing process involves several key steps:
1. PCB Design
2. PCB Fabrication
3. PCB Assembly
4. Testing and Inspection
PCB Design Process
The PCB design process starts with creating a schematic diagram that defines the electrical connections between components. This schematic is then translated into a physical layout using EDA (electronic design automation) software. The layout specifies the location and routing of copper traces, the placement of components and drilled holes, and the addition of text labels and identifiers.
Some key considerations during PCB design include:
– Selecting the right materials (FR-4, polyimide, etc.)
– Defining the number of layers
– Specifying trace width and spacing to handle expected current
– Implementing EMI shielding and ESD protection
– Optimizing component placement for manufacturing
PCB Design Software
Popular PCB design software includes:
Software | Vendor |
---|---|
Altium Designer | Altium |
Eagle | Autodesk |
OrCAD | Cadence |
KiCad | Open Source |
PCB Fabrication Process
Once the PCB design is finalized, fabrication can begin. The fabrication process creates the Bare PCB – the physical board without any components attached yet.
Key steps in PCB fabrication include:
Step 1: Material Selection and Cutting
- The base material, usually FR-4 fiberglass, is selected and cut to the required dimensions.
- For multi-layer boards, a stack-up of alternating core and prepreg layers is built.
Step 2: Drilling
- Holes are drilled through the board to accommodate through-hole components and vias that connect traces on different layers.
- Drilling is done by high-speed CNC machines with small-diameter drill bits.
Step 3: Patterning and Etching
- Copper foil is laminated onto the board, then coated with a light-sensitive resist.
- The resist is exposed to a pattern of light that hardens it where copper traces should remain.
- The unhardened resist is chemically removed, exposing the copper underneath.
- That exposed copper is etched away using chemicals like ferric chloride, leaving only the desired traces.
- The hardened resist is then stripped off, revealing the final copper pattern.
Step 4: Plating and Finishing
- Exposed copper is electroplated with a thin layer of copper to reinforce the traces.
- Holes are plated with copper to create conductive vias between layers.
- A soldermask layer is applied and cured, covering the copper traces but leaving pads and holes exposed. This protects the traces and prevents solder bridges. The soldermask gives PCBs their characteristic green color.
- A silkscreen layer is printed to add text labels and identifiers.
- The copper is coated with a surface finish like HASL (hot air solder leveling), ENIG (electroless nickel immersion gold), or OSP (organic solderability preservatives) to prevent oxidation and enhance solderability.
Step 5: Cutting and Profiling
- Boards are cut out of the panel by routing, V-scoring, or punching.
- An electrical test may be performed to check for shorts or opens.
PCB Assembly Process
With the bare PCB fabricated, electronic components can be attached to create a functional circuit board. PCB assembly is typically done in one of two ways:
Through-Hole Assembly (THA)
- Components with long metal leads are inserted into holes drilled in the board.
- The leads are soldered to pads on the opposite side, either manually or by a wave soldering machine.
- Through-hole components are bigger and heavier but offer strong mechanical bonds.
Surface Mount Assembly (SMA)
- Components are mounted directly onto pads on the surface of the board.
- A solder paste (a mix of tiny solder balls and flux) is applied to the pads using a stencil.
- Components are placed onto the solder paste, held in place by the tackiness of the flux.
- The board is run through a reflow oven, which melts the solder, bonding the components to the pads.
- Surface mount components are smaller and lighter and allow for higher density designs.
Mixed assembly techniques that use both through-hole and surface mount components are also common.
Automated assembly lines with pick-and-place machines, reflow ovens, and inspection systems enable high-speed, high-precision PCB assembly. However, some products may require manual assembly for large or oddly shaped components, or for lower volumes where automation is not cost-effective.
Testing and Inspection
Throughout the manufacturing process, various tests and inspections are performed to ensure quality:
- Automated optical inspection (AOI) uses cameras to check for missing components, proper alignment, and solder defects.
- X-ray inspection allows checking for voids, bridges, and proper connections under BGA packages and other hidden areas.
- In-circuit testing (ICT) uses a “bed of nails” fixture to make electrical contact with test points and component leads, checking for shorts, opens, and proper resistance, capacitance, and inductance values.
- Functional testing applies power to the board and tests its operation against specifications.
Types of PCBs
PCBs come in various types based on their structure and manufacturing process:
Single Layer PCBs
- Have conductive copper traces on one side only.
- The other side is usually a plain substrate material.
- Cheapest and simplest to manufacture but limited in complexity.
Double Layer PCBs
- Have copper traces on both top and bottom sides.
- Traces on opposite sides are connected by vias.
- More complex and flexible in layout than single layer.
Multi-Layer PCBs
- Have three or more layers of copper traces.
- Inner layers are sandwiched between insulating layers.
- Offers the highest density and complexity.
- Used for advanced electronics like smartphones, computers, etc.
Rigid PCBs
- Made from solid substrate materials like FR-4 fiberglass.
- Cannot be bent or flexed.
- The standard type for most electronics.
Flexible PCBs
- Made from flexible materials like polyimide.
- Can be bent and twisted to fit in tight spaces or movable parts.
- Often used in cameras, printers, and wearable electronics.
Rigid-Flex PCBs
- Combine rigid and flexible sections in one board.
- Allow 3D configurations and space savings.
- Used in aerospace, military, and medical devices.
PCB Materials
The choice of materials is critical in PCB manufacturing, affecting the board’s electrical, mechanical, and thermal properties. Common materials include:
Substrates
- FR-4: A composite of fiberglass and epoxy resin. The most common base material, offering good mechanical and electrical properties and low cost.
- Polyimide: A flexible polymer that can withstand high temperatures. Used for flexible PCBs.
- Teflon: Has low dielectric loss, making it suitable for high-frequency RF applications.
- Ceramic: Offers excellent thermal conductivity and stability at high temperatures. Used in LED lighting and power electronics.
Copper Foils
- Electrodeposited (ED) copper: The standard foil type, offering good adhesion and conductivity.
- Rolled-annealed (RA) copper: Offers higher elongation and fatigue resistance for flexible PCBs.
Soldermasks
- LPI (liquid photoimageable): The most common type, applied as a liquid and cured by UV light.
- Dry film: Applied as a film and laminated onto the board.
Silkscreens
- Epoxy ink: The standard type, offering good durability and readability.
- UV curable ink: Cures faster under UV light, allowing for finer detail printing.
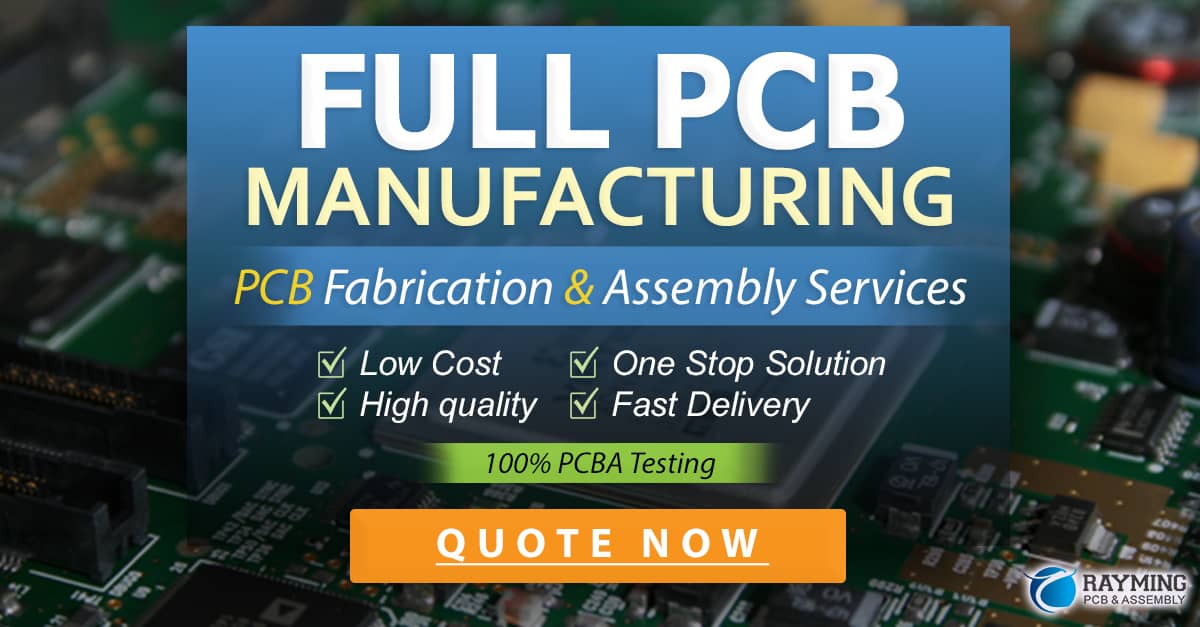
PCB Manufacturing Standards and Certifications
To ensure quality and reliability, PCB Manufacturers often adhere to industry standards and certifications:
-
IPC (Association Connecting Electronics Industries): Publishes the most widely used standards for PCB design, fabrication, and assembly, such as IPC-A-610 for acceptability of electronic assemblies and IPC-6012 for qualification and performance of rigid PCBs.
-
UL (Underwriters Laboratories): Offers safety certifications for PCBs used in specific applications, such as UL 94 for flammability rating.
-
ISO (International Organization for Standardization): Provides quality management standards like ISO 9001 that many PCB manufacturers are certified to.
-
RoHS (Restriction of Hazardous Substances): A directive that restricts the use of certain hazardous materials in electronics. Many PCBs are manufactured to be RoHS compliant.
Frequently Asked Questions (FAQ)
1. What is the typical turnaround time for PCB manufacturing?
Turnaround time varies depending on the complexity of the board and the manufacturer’s capacity. Simple 2-layer boards can often be manufactured in 1-2 days, while complex multi-layer boards may take several weeks. Many manufacturers offer expedited services for faster turnaround at a higher cost.
2. How much does PCB Manufacturing Cost?
The cost of PCB manufacturing depends on factors like the number of layers, board size, quantity, and special requirements. Simple 2-layer boards in small quantities may cost a few dollars each, while large, complex boards can cost hundreds of dollars each. Most manufacturers offer discounts for higher quantities.
3. What files are needed for PCB manufacturing?
The main file needed is the Gerber file, which is a standard format that describes the layout of each layer of the PCB. Drill files are also needed to specify the location and size of holes. Sometimes, additional files like the Bill of Materials (BOM) and assembly drawings are also required.
4. What is the minimum order quantity for PCB manufacturing?
Many PCB manufacturers have a minimum order quantity (MOQ) to make production economically viable. The MOQ varies by manufacturer but can range from 5 to 100 pieces for prototype runs. Some manufacturers specialize in low-volume production and may have no MOQ.
5. How are PCBs shipped and packaged?
PCBs are typically shipped in ESD (electrostatic discharge) safe packaging to protect them from static damage. Single boards may be shipped in individual ESD bags, while larger quantities may be stacked and vacuum-sealed in moisture barrier bags. The packaging should also protect the boards from physical damage during transit.
0 Comments