What is PCB Cross-Section Analysis?
PCB cross-section analysis involves cutting a small section of a PCB and examining its internal structure using microscopic imaging techniques. The process allows for a detailed view of the PCB’s layers, copper traces, vias, and other components. By analyzing the cross-section, engineers can assess the quality of the manufacturing process, identify any defects or irregularities, and ensure that the PCB meets the required specifications.
Benefits of PCB Cross-Section Analysis
-
Quality Control: PCB cross-section analysis is an essential tool for quality control in the electronics industry. It helps manufacturers identify and address any issues in the production process, ensuring that the final product meets the required standards.
-
Failure Analysis: In case of PCB Failures or malfunctions, cross-section analysis can help identify the root cause of the problem. By examining the internal structure of the PCB, engineers can pinpoint the specific component or area responsible for the failure and take corrective actions.
-
Material Evaluation: Cross-section analysis allows for the evaluation of the materials used in PCB manufacturing. It helps ensure that the materials meet the required specifications and are free from defects or inconsistencies.
-
Design Validation: By analyzing the cross-section of a PCB, engineers can validate the design and ensure that it meets the intended requirements. This helps in identifying any design flaws or potential issues before mass production.
Techniques Used in PCB Cross-Section Analysis
Several techniques are used in PCB cross-section analysis to obtain a detailed view of the internal structure. These techniques include:
Mechanical Sectioning
Mechanical sectioning involves cutting a small section of the PCB using a precision saw or cutting tool. The cut section is then mounted and polished to obtain a smooth surface for microscopic examination. This technique is commonly used for quick and cost-effective analysis.
Ion Milling
Ion milling is a more advanced technique that uses a focused ion beam to remove material from the PCB surface. It allows for precise control over the milling process and can create high-quality cross-sections with minimal damage to the surrounding areas.
Focused Ion Beam (FIB)
Focused Ion Beam (FIB) is a sophisticated technique that combines ion milling with high-resolution imaging. It uses a focused beam of ions to mill away material and create a cross-section while simultaneously capturing high-resolution images of the exposed area.
Comparison of Techniques
Technique | Advantages | Disadvantages |
---|---|---|
Mechanical Sectioning | Quick, cost-effective | Limited precision, potential damage to the sample |
Ion Milling | Precise control, minimal damage | Slower process, higher cost |
Focused Ion Beam (FIB) | High-resolution imaging, precise milling | Expensive equipment, requires specialized expertise |
Analyzing the Cross-Section
Once the cross-section is prepared, it is analyzed using microscopic imaging techniques. The most common methods used for cross-section analysis include:
Optical Microscopy
Optical microscopy uses visible light and a series of lenses to magnify the cross-section image. It provides a quick and easy way to examine the overall structure and identify any visible defects or irregularities.
Scanning Electron Microscopy (SEM)
Scanning Electron Microscopy (SEM) uses a focused beam of electrons to scan the cross-section surface and generate high-resolution images. SEM provides much higher magnification and resolution compared to optical microscopy, allowing for detailed analysis of fine features and material composition.
Energy Dispersive X-ray Spectroscopy (EDS)
Energy Dispersive X-ray Spectroscopy (EDS) is often used in conjunction with SEM to analyze the chemical composition of the materials in the cross-section. It helps identify the presence of any contaminants or unwanted elements that may affect the performance or reliability of the PCB.
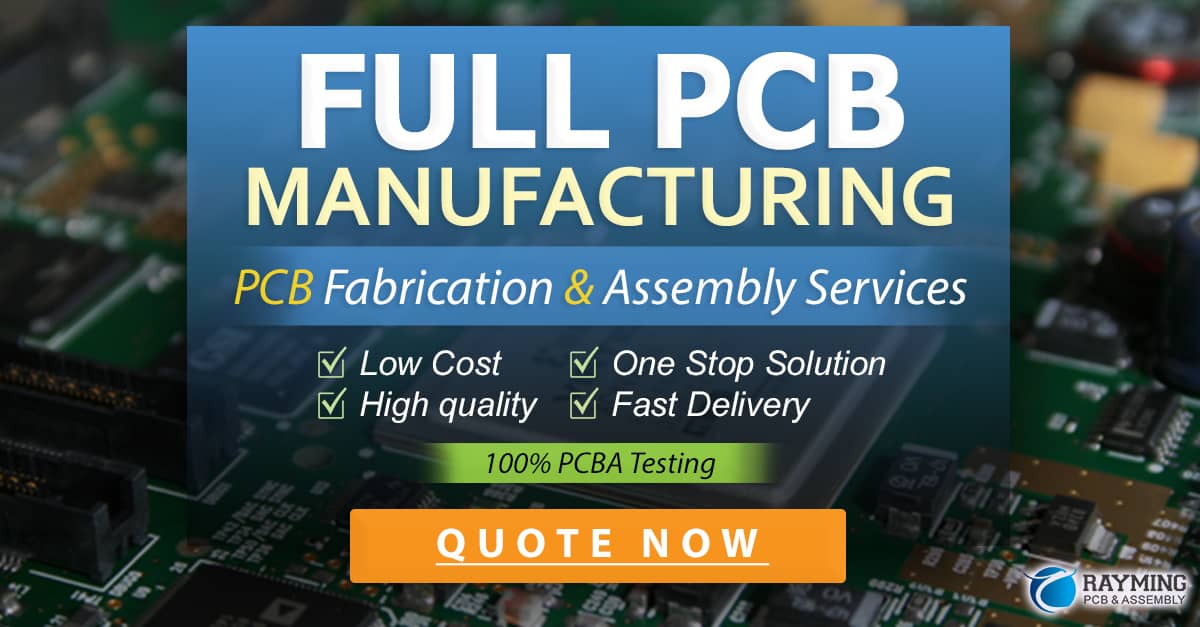
Common Defects and Issues Detected by Cross-Section Analysis
PCB cross-section analysis can reveal a wide range of defects and issues that may impact the quality and reliability of the PCB. Some common defects and issues include:
-
Voids: Voids are empty spaces or gaps within the PCB Layers or between components and the board. They can cause electrical disconnections, reduce thermal conductivity, and weaken the mechanical strength of the PCB.
-
Delamination: Delamination occurs when the layers of the PCB separate or fail to bond properly. It can lead to electrical failures, moisture ingress, and reduced mechanical integrity.
-
Copper Thickness Variations: Inconsistent copper thickness in the PCB Traces can cause signal integrity issues, increased resistance, and potential reliability problems.
-
Solder Joint Defects: Cross-section analysis can reveal solder joint defects such as insufficient solder, voids, or poor wetting, which can affect the electrical and mechanical connections between components and the PCB.
-
Plating Defects: Issues with the plating process, such as uneven plating thickness or voids in the plated through-holes, can compromise the electrical connectivity and reliability of the PCB.
Benefits of Regular PCB Cross-Section Analysis
Conducting regular PCB cross-section analysis offers several benefits for electronics manufacturers and product designers:
-
Early Defect Detection: By analyzing PCBs at various stages of the manufacturing process, defects can be identified and addressed early, reducing the risk of costly rework or product failures.
-
Process Optimization: Cross-section analysis provides valuable insights into the manufacturing process, allowing for continuous improvement and optimization. It helps identify areas where process adjustments can enhance quality and efficiency.
-
Improved Reliability: Regular cross-section analysis helps ensure the consistency and reliability of PCBs. By identifying and addressing potential issues, manufacturers can deliver products with higher reliability and longer service life.
-
Compliance with Standards: Cross-section analysis helps verify compliance with industry standards and customer requirements. It provides objective evidence of the PCB’s internal structure and quality, supporting quality assurance and regulatory compliance.
FAQ
-
Q: How often should PCB cross-section analysis be performed?
A: The frequency of PCB cross-section analysis depends on factors such as the complexity of the PCB, the manufacturing process, and the criticality of the application. It is typically performed at regular intervals during production, such as daily or weekly, and whenever there are changes in materials, processes, or suppliers. -
Q: Can PCB cross-section analysis be performed on finished products?
A: Yes, cross-section analysis can be performed on finished PCBs to investigate any issues or failures that may occur during the product’s lifecycle. However, it is a destructive testing method and requires sacrificing a sample of the finished product. -
Q: How are the results of PCB cross-section analysis documented and communicated?
A: The results of PCB cross-section analysis are typically documented in a detailed report that includes high-resolution images, measurements, and observations. The report is shared with relevant stakeholders, such as quality control teams, engineers, and customers, to facilitate discussion and decision-making. -
Q: Can PCB cross-section analysis detect all types of defects?
A: While PCB cross-section analysis is a powerful tool for identifying a wide range of defects, it may not detect all types of issues. Some defects, such as intermittent failures or signal integrity problems, may require additional testing methods or functional testing to be identified. -
Q: How can the results of PCB cross-section analysis be used for continuous improvement?
A: The results of PCB cross-section analysis provide valuable insights into the manufacturing process and product quality. By analyzing the data and trends over time, manufacturers can identify areas for improvement, implement corrective actions, and monitor the effectiveness of those actions. This continuous improvement approach helps enhance the overall quality and reliability of PCBs.
Conclusion
PCB cross-section analysis is a vital technology in the electronics industry, enabling manufacturers to ensure the quality, reliability, and performance of their products. By examining the internal structure of PCBs, engineers can identify defects, validate designs, and optimize manufacturing processes. Regular cross-section analysis helps detect issues early, reduce rework costs, and improve product reliability.
As electronic devices continue to advance in complexity and miniaturization, the importance of PCB cross-section analysis will only grow. Manufacturers that prioritize and invest in this technology will be well-positioned to deliver high-quality products, meet customer expectations, and maintain a competitive edge in the market.
0 Comments