What is a Printed Wiring Board (PWB)?
A Printed Wiring Board, also known as a Printed Circuit Board (PCB), is a flat board made of insulating material with conductive copper traces printed on its surface. PWBs are used to mechanically support and electrically connect electronic components using conductive pathways etched from copper sheets laminated onto a non-conductive substrate.
PWBs are essential in almost all modern electronic devices, from simple consumer electronics like digital clocks and calculators to complex industrial equipment, medical devices, and aerospace systems. They provide a reliable and efficient method of interconnecting electronic components, allowing for the creation of compact, high-performance electronic circuits.
History of Printed Wiring Boards
The concept of printed wiring boards dates back to the early 20th century. In 1903, German inventor Albert Hanson filed a patent for a “printed wire” method of electrical interconnection. However, it wasn’t until the 1920s that the first practical PWBs were developed.
In 1925, Charles Ducas of the United States patented a method of electroplating circuit patterns onto an insulated surface. This process, known as “additive PCB manufacturing,” laid the foundation for modern PWB production techniques.
During World War II, the demand for compact, reliable electronic systems for military applications drove the development of PWB technology. In the 1940s, the U.S. Army Signal Corps introduced the “Auto-Sembly” process, which used a copper foil-clad laminate and a subtractive etching process to create circuit patterns.
The 1950s and 1960s saw significant advancements in PWB manufacturing, including the introduction of through-hole technology and double-sided boards. In the 1970s, multi-layer PWBs and surface-mount technology (SMT) became prevalent, enabling the production of more complex, high-density circuits.
Today, PWBs are an integral part of the electronics industry, with ongoing advancements in materials, manufacturing processes, and design technologies to meet the ever-increasing demands for performance, reliability, and miniaturization.
PWB Materials
PWBs are composed of several key materials, each serving a specific purpose in the board’s construction and functionality.
Substrate Materials
The substrate is the non-conductive base material of a PWB, providing mechanical support and electrical insulation between the conductive layers. Common substrate materials include:
-
FR-4: A composite material made of woven fiberglass cloth impregnated with an epoxy resin. FR-4 is the most widely used substrate material due to its excellent mechanical and electrical properties, as well as its cost-effectiveness.
-
Polyimide: A high-performance polymer known for its exceptional thermal stability, chemical resistance, and flexibility. Polyimide is often used in applications requiring high reliability and the ability to withstand harsh environments.
-
PTFE (Polytetrafluoroethylene): A synthetic fluoropolymer with excellent dielectric properties and low loss at high frequencies. PTFE is commonly used in high-frequency and microwave applications.
-
Ceramic: Alumina and other ceramic materials are used in PWBs for high-temperature, high-power, and high-frequency applications due to their excellent thermal conductivity and dielectric properties.
Conductive Materials
The conductive layers of a PWB are typically made of copper, chosen for its excellent electrical conductivity, thermal conductivity, and ease of processing. Copper foils are laminated onto the substrate material and then etched to create the desired circuit patterns.
The thickness of the copper foil is expressed in ounces per square foot (oz/ft²) or microns (µm). Common copper foil thicknesses range from 0.5 oz/ft² (18 µm) to 4 oz/ft² (140 µm), with 1 oz/ft² (35 µm) being the most widely used.
Solder Mask
Solder mask is a thin, protective layer applied over the copper traces on a PWB, leaving only the exposed pads and other areas that require soldering. The solder mask serves several purposes:
-
Insulation: It provides electrical insulation between the copper traces, preventing short circuits.
-
Protection: The solder mask protects the copper traces from oxidation, corrosion, and mechanical damage.
-
Solder control: By selectively exposing the pads, the solder mask helps control the flow of molten solder during the assembly process, preventing solder bridges and other defects.
Solder mask is typically applied as a liquid photopolymer and then cured using UV light. The most common Solder Mask Colors are green and blue, although other colors, such as red, yellow, and black, are also available.
Silkscreen
Silkscreen, also known as legend or nomenclature, is the text and graphics printed on the surface of a PWB to provide information about the board’s components, connectors, and other features. The silkscreen is typically applied using a screen printing process and is usually white, although other colors are available.
The silkscreen serves several purposes:
-
Component identification: It labels the components and their respective values, making it easier for technicians to assemble, test, and debug the board.
-
Orientation markings: The silkscreen often includes orientation markings, such as pin 1 indicators and polarity symbols, to ensure correct component placement.
-
Branding and logos: Manufacturers may include their company logo, product name, or other branding elements on the silkscreen.
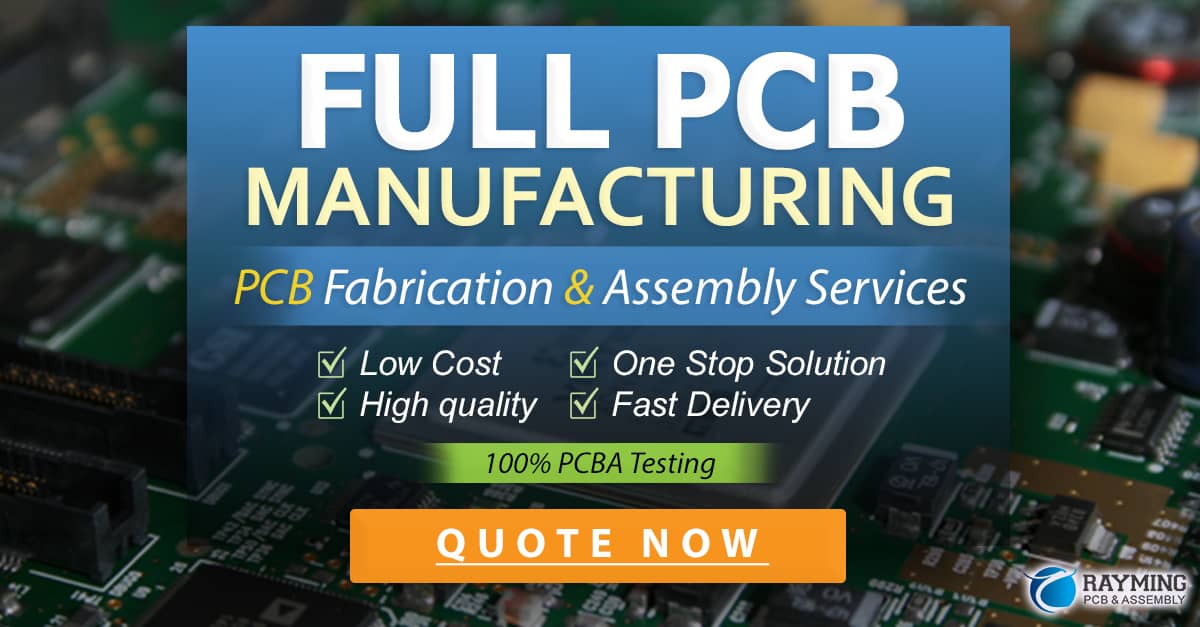
PWB Manufacturing Process
The manufacturing process for PWBs involves several key steps, each contributing to the creation of a high-quality, reliable board.
Design and Layout
The first step in PWB manufacturing is the design and layout of the circuit. This process involves creating a schematic diagram that represents the electrical connections between components, followed by the creation of a physical layout that determines the placement of components and routing of the copper traces.
PWB design software, such as Altium Designer, Eagle, and KiCad, is used to create the schematic and layout files. The designer must consider various factors, such as signal integrity, power distribution, thermal management, and manufacturing constraints, to ensure the board’s optimal performance and manufacturability.
Fabrication
Once the design is complete, the fabrication process begins. The primary steps in PWB fabrication include:
-
Inner layer processing: For Multi-layer Boards, the inner layers are printed and etched first. Copper foil is laminated onto the substrate material, and the desired circuit patterns are transferred using a photolithographic process. The unwanted copper is then etched away, leaving only the circuit traces.
-
Lamination: The inner layers are stacked and aligned, with insulating prepreg material placed between each layer. The stack is then subjected to heat and pressure in a lamination press, bonding the layers together to form a solid board.
-
Drilling: Holes are drilled through the board to accommodate through-hole components and provide electrical connections between layers. Modern PWB manufacturing uses computer numerical control (CNC) drilling machines for high precision and speed.
-
Plating: The drilled holes are plated with copper to create electrical connections between layers. This process involves depositing a thin layer of copper onto the hole walls using an electroless plating process, followed by an electrolytic plating process to build up the desired thickness.
-
Outer layer processing: The outer layers of the board are printed and etched using the same photolithographic process as the inner layers.
-
Solder mask application: The solder mask is applied to the board and cured using UV light. Openings in the solder mask are created to expose the pads and other areas requiring soldering.
-
Surface finish: A surface finish, such as HASL (Hot Air Solder Leveling), ENIG (Electroless Nickel Immersion Gold), or OSP (Organic Solderability Preservative), is applied to the exposed copper to prevent oxidation and enhance solderability.
-
Silkscreen printing: The silkscreen is applied to the board using a screen printing process.
-
Electrical testing: The completed board undergoes electrical testing to ensure proper functionality and connectivity.
Assembly
After fabrication, the PWB is ready for assembly. The assembly process involves placing and soldering components onto the board. There are two primary assembly technologies:
-
Through-hole technology (THT): THT components have long leads that are inserted through holes in the board and soldered to pads on the opposite side. THT assembly is typically performed manually or using semi-automatic insertion machines.
-
Surface-mount technology (SMT): SMT components have small leads or terminations that are soldered directly onto pads on the surface of the board. SMT Assembly is highly automated, using pick-and-place machines to accurately place components, followed by a reflow soldering process to form the solder joints.
After assembly, the board undergoes further testing and inspection to ensure proper functionality and quality.
PWB Design Considerations
Designing a successful PWB requires careful consideration of various factors to ensure optimal performance, reliability, and manufacturability.
Signal Integrity
Signal integrity refers to the quality of the electrical signals transmitted through the PWB. Factors that can affect signal integrity include:
-
Impedance control: Maintaining consistent impedance along the signal path is crucial for minimizing reflections and ensuring proper signal transmission. This is achieved through careful design of trace widths, spacing, and layer stackup.
-
Crosstalk: Crosstalk occurs when signals from one trace couple onto adjacent traces, causing interference and signal distortion. Crosstalk can be minimized through proper trace spacing, the use of ground planes, and other shielding techniques.
-
EMI/EMC: Electromagnetic interference (EMI) and electromagnetic compatibility (EMC) refer to the board’s ability to operate without causing or being affected by electromagnetic disturbances. Proper grounding, shielding, and filtering techniques can help mitigate EMI/EMC issues.
Power Distribution
Efficient power distribution is essential for ensuring stable operation of the electronic components on the PWB. Key considerations include:
-
Power plane design: The use of dedicated power planes helps distribute power evenly across the board, minimizing voltage drops and ensuring a stable supply to all components.
-
Decoupling capacitors: Decoupling capacitors are placed near power-consuming components to provide a local source of charge and minimize power supply noise.
-
Voltage regulation: Voltage Regulators are used to maintain stable voltage levels for sensitive components, such as processors and memory devices.
Thermal Management
Proper thermal management is critical for ensuring the long-term reliability and performance of the PWB and its components. Factors to consider include:
-
Component placement: Components should be placed in a manner that allows for adequate heat dissipation, with high-power components spaced apart and located near the board edges when possible.
-
Copper pours: The use of copper pours, or large areas of copper on the board, can help distribute heat and improve thermal performance.
-
Thermal vias: Thermal vias are used to transfer heat from components to the opposite side of the board or to internal copper layers, helping to dissipate heat more effectively.
Manufacturing Considerations
Designing a PWB with manufacturability in mind helps ensure a smooth and cost-effective production process. Key considerations include:
-
Design for manufacturing (DFM): DFM guidelines provide recommendations for minimum trace widths, spacing, hole sizes, and other parameters to ensure compatibility with the manufacturing process.
-
Panelization: PWBs are often designed as part of a larger panel to maximize production efficiency. Proper panelization techniques, such as the use of Breakaway Tabs or mousebites, help ensure easy separation of individual boards after fabrication.
-
Testing and inspection: Incorporating test points and other features that facilitate automated testing and inspection can help streamline the manufacturing process and improve overall quality control.
PWB Testing and Inspection
Thorough testing and inspection are essential for ensuring the quality and reliability of PWBs. Various methods are employed at different stages of the manufacturing process.
Automated Optical Inspection (AOI)
AOI systems use high-resolution cameras and image processing algorithms to inspect the PWB for manufacturing defects, such as:
-
Solder bridges: Unintended connections between adjacent pads or traces caused by excess solder.
-
Open circuits: Missing or incomplete connections between pads and traces.
-
Component placement errors: Incorrect placement or orientation of components on the board.
AOI is typically performed immediately after the solder mask application and silkscreen printing stages, as well as after component assembly.
X-Ray Inspection
X-ray inspection is used to examine solder joints and other internal features of the PWB that are not visible from the surface. This method is particularly useful for inspecting:
-
Ball Grid Array (BGA) packages: BGAs have an array of solder balls underneath the component, which are difficult to inspect using other methods.
-
Plated through-holes: X-ray inspection can reveal voids or other defects in the copper plating inside the holes.
-
Multi-layer boards: X-ray imaging can be used to inspect the internal layers of the board for proper alignment and continuity.
In-Circuit Testing (ICT)
ICT is a form of electrical testing that verifies the proper assembly and functionality of the PWB and its components. ICT systems use a bed-of-nails fixture to make contact with test points on the board, allowing for the measurement of:
-
Component values: Resistors, capacitors, and inductors are measured to ensure they are within the specified tolerance.
-
Diode and transistor functionality: The electrical characteristics of semiconductor devices are tested to verify proper operation.
-
Connectivity: Continuity between pins and pads is checked to ensure proper connections and the absence of short circuits.
ICT is typically performed after the assembly process and can help identify component placement errors, missing or incorrect components, and manufacturing defects.
Frequently Asked Questions (FAQs)
1. What is the difference between a Printed Wiring Board (PWB) and a Printed Circuit Board (PCB)?
A: Printed Wiring Board (PWB) and Printed Circuit Board (PCB) are essentially the same things. Both terms refer to a flat board made of insulating material with conductive copper traces printed on its surface, used to mechanically support and electrically connect electronic components. The term PWB is more commonly used in the United States, while PCB is more prevalent in Europe and Asia.
2. What are the advantages of using PWBs in electronic devices?
A: PWBs offer several advantages in electronic devices:
-
Compact design: PWBs allow for the dense packaging of electronic components, enabling the creation of smaller, more compact devices.
-
Reliability: The use of copper traces and robust manufacturing processes ensures reliable electrical connections between components, reducing the risk of failures.
-
Consistency: Automated manufacturing processes enable the production of consistent, high-quality PWBs with minimal variations between boards.
-
Cost-effectiveness: PWBs are cost-effective for mass production, as the automated manufacturing processes minimize labor costs and material waste.
3. What is the difference between through-hole technology (THT) and surface-mount technology (SMT)?
A: Through-hole technology (THT) and surface-mount technology (SMT) are two different methods of assembling components onto a PWB.
THT components have long leads that are inserted through holes in the board and soldered to pads on the opposite side. THT assembly is typically performed manually or using semi-automatic insertion machines.
SMT components have small leads or terminations that are soldered directly onto pads on the surface of the board. SMT assembly is highly automated, using pick-and-place machines to accurately place components, followed by a reflow soldering process to form the solder joints.
SMT allows for smaller component sizes and higher component density compared to THT, enabling the creation of more compact and complex PWBs.
4. What factors should be considered when designing a PWB?
A: When designing a PWB, several key factors should be considered to ensure optimal performance, reliability, and manufacturability:
-
Signal integrity: Maintaining consistent impedance, minimizing crosstalk, and addressing EMI/EMC concerns are essential for ensuring proper signal transmission.
-
Power distribution: Efficient power distribution, including the use of power planes, decoupling capacitors, and voltage regulation, is crucial for stable operation of the electronic components.
-
Thermal management: Proper component placement, the use of copper pours, and thermal vias help ensure adequate heat dissipation and long-term reliability.
-
Manufacturing considerations: Adhering to design for manufacturing (DFM) guidelines, proper panelization, and incorporating features for testing and inspection help streamline the production process and improve overall quality control.
5. What testing and inspection methods are used to ensure PWB quality?
A: Several testing and inspection methods are employed at different stages of the PWB manufacturing process to ensure quality and reliability:
-
Automated Optical Inspection (AOI): AOI systems use high-resolution cameras and image processing algorithms to inspect the PWB for manufacturing defects, such as solder bridges, open circuits, and component placement errors.
-
X-ray Inspection: X-ray imaging is used to examine solder joints and other internal features of the PWB, particularly for Ball Grid Array (BGA) packages, plated through-holes, and multi-layer boards.
-
In-Circuit Testing (ICT): ICT is a form of electrical testing that verifies the proper assembly and functionality of the PWB and its components, checking for correct component values, semiconductor functionality, and connectivity.
These methods help identify and address manufacturing defects, ensuring the production of high-quality, reliable PW
0 Comments