Introduction to Double-sided SMT Assembly
Double-sided SMT (Surface Mount Technology) assembly is a process used in the manufacturing of printed circuit boards (PCBs) where electronic components are mounted on both sides of the board. This technique has become increasingly popular in the electronics industry due to its ability to create more compact and efficient designs while reducing manufacturing costs.
In this article, we will explore the intricacies of double-sided SMT Assembly, including its benefits, challenges, and the various processes involved in creating a Double-Sided PCB.
Benefits of Double-Sided SMT Assembly
Double-sided SMT assembly offers several advantages over traditional single-sided PCB manufacturing:
-
Increased component density: By utilizing both sides of the PCB, designers can incorporate more components into a smaller space, resulting in more compact and efficient designs.
-
Improved performance: Double-sided SMT assembly allows for shorter trace lengths between components, which can lead to improved signal integrity and reduced electromagnetic interference (EMI).
-
Cost-effectiveness: Although the initial setup costs for double-sided SMT assembly may be higher, the overall cost per unit is often lower due to the increased efficiency and reduced material usage.
Challenges of Double-Sided SMT Assembly
Despite its many benefits, double-sided SMT assembly also presents some unique challenges:
-
Alignment: Ensuring proper alignment between the components on both sides of the PCB can be difficult, requiring precise registration marks and specialized equipment.
-
Thermal management: As components are placed on both sides of the board, heat dissipation becomes a more significant concern. Designers must carefully consider the placement of components and the use of thermal vias to prevent overheating.
-
Soldering complexity: Double-sided SMT assembly requires a more complex soldering process, as both sides of the board must be soldered without damaging the components on the opposite side.
The Double-Sided SMT Assembly Process
The double-sided SMT assembly process consists of several key steps, each of which requires specialized equipment and expertise.
Step 1: PCB Design and Preparation
The first step in double-sided SMT assembly is designing the PCB layout using computer-aided design (CAD) software. The designer must carefully consider the placement of components on both sides of the board, ensuring proper spacing and alignment.
Once the design is finalized, the PCB is fabricated, and any necessary surface finishes, such as solder mask and silkscreen, are applied.
Step 2: Solder Paste Application
Solder paste, a mixture of tiny solder particles suspended in a flux medium, is applied to the PCB’s contact pads using a stencil printing process. The stencil, a thin metal sheet with openings that correspond to the contact pads, is aligned with the PCB, and solder paste is spread across the stencil using a squeegee.
Step 3: Component Placement
After the solder paste is applied, the PCB is ready for component placement. This process is typically performed using a pick-and-place machine, which uses a combination of vacuum nozzles and precision positioning systems to place components onto the board.
In double-sided SMT assembly, components are first placed on one side of the board, typically the side with the most components or the side that will be soldered first.
Step 4: Reflow Soldering
Once the components are placed, the PCB undergoes a reflow soldering process. The board is passed through a reflow oven, which heats the solder paste to a specific temperature profile, causing the solder to melt and form a permanent connection between the components and the contact pads.
In double-sided SMT assembly, the reflow soldering process is performed twice, once for each side of the board. The side with the fewest components or the most heat-sensitive components is typically soldered first.
Step 5: Inspection and Testing
After the soldering process is complete, the PCB undergoes a thorough inspection and testing process to ensure proper functionality and quality. This may include visual inspections, automated optical inspection (AOI), X-ray inspection, and electrical testing.
Any defects or issues identified during the inspection and testing process are addressed, and the PCB is reworked if necessary.
Advanced Techniques in Double-Sided SMT Assembly
As the demand for more complex and compact electronic devices grows, manufacturers are continuously developing new techniques to improve the efficiency and reliability of double-sided SMT assembly.
Pin-in-Paste Technology
Pin-in-Paste (PiP) is a technique that allows through-hole components to be soldered onto a double-sided PCB using the same reflow soldering process used for surface mount components. In this method, solder paste is applied to the through-holes, and the through-hole components are inserted before the reflow soldering process.
PiP technology eliminates the need for a separate Wave Soldering process for through-hole components, reducing manufacturing time and costs.
Embedded Components
Embedded components are another advanced technique used in double-sided SMT assembly. In this method, passive components, such as resistors and capacitors, are embedded within the layers of the PCB substrate itself, rather than being mounted on the surface.
Embedding components can help to further reduce the size and thickness of the PCB while improving electrical performance and reducing EMI.
3D Printing for PCB Prototyping
3D printing technology is increasingly being used in the PCB prototyping process, allowing designers to quickly and cost-effectively create functional prototypes of double-sided PCBs.
By using conductive and insulating materials, 3D printers can create PCBs with embedded components and complex geometries, enabling designers to test and refine their designs before committing to full-scale production.
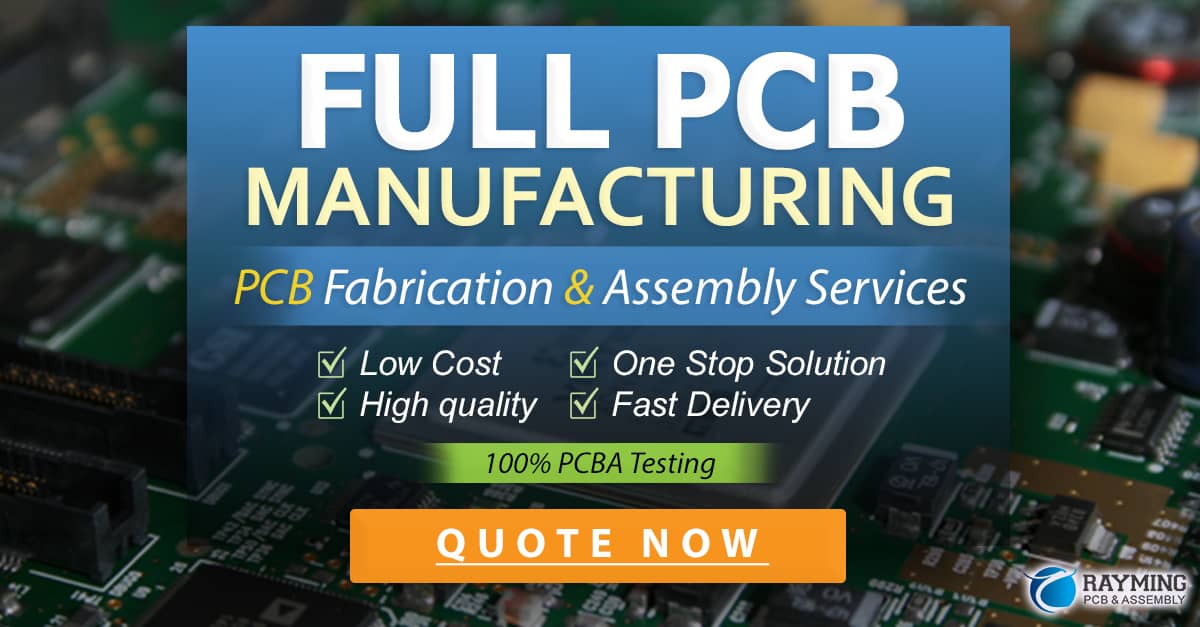
Conclusion
Double-sided SMT assembly is a powerful technique that enables the creation of compact, high-performance electronic devices. By understanding the benefits, challenges, and processes involved in double-sided SMT assembly, designers and manufacturers can create innovative products that meet the ever-evolving demands of the electronics industry.
As new technologies and techniques continue to emerge, the possibilities for double-sided SMT assembly will only continue to grow, driving the development of even more advanced and efficient electronic devices.
Frequently Asked Questions (FAQ)
1. What is the difference between single-sided and double-sided SMT assembly?
Single-sided SMT assembly involves mounting components on only one side of the PCB, while double-sided SMT assembly mounts components on both sides of the board. Double-sided assembly allows for higher component density and improved performance but requires more complex manufacturing processes.
2. Can through-hole components be used in double-sided SMT assembly?
Yes, through-hole components can be used in double-sided SMT assembly using Pin-in-Paste (PiP) technology. In this method, solder paste is applied to the through-holes, and the through-hole components are inserted before the reflow soldering process, allowing them to be soldered along with the surface mount components.
3. What are the main challenges associated with double-sided SMT assembly?
The main challenges in double-sided SMT assembly include ensuring proper alignment between components on both sides of the board, managing heat dissipation, and navigating the complexities of the double-sided soldering process.
4. How does the reflow soldering process work in double-sided SMT assembly?
In double-sided SMT assembly, the reflow soldering process is performed twice, once for each side of the board. The side with the fewest components or the most heat-sensitive components is typically soldered first. The PCB is passed through a reflow oven, which heats the solder paste to a specific temperature profile, causing the solder to melt and form a permanent connection between the components and the contact pads.
5. What role does 3D printing play in double-sided SMT assembly?
3D printing technology is increasingly being used in the PCB prototyping process for double-sided SMT assembly. By using conductive and insulating materials, 3D printers can create functional prototypes of double-sided PCBs with embedded components and complex geometries, allowing designers to test and refine their designs before committing to full-scale production.
0 Comments