Introduction to Solder Paste printing
Solder paste printing is a crucial step in the Surface Mount Technology (SMT) assembly process. It involves applying a precise amount of solder paste onto the pads of a Printed Circuit Board (PCB) before placing the electronic components. The quality of the solder paste printing process directly affects the reliability and functionality of the final assembLED PCB.
What is Solder Paste?
Solder paste is a gray, putty-like material composed of tiny solder particles suspended in a flux medium. The solder particles are typically made of a tin-lead (SnPb) alloy or lead-free alternatives such as tin-silver-copper (SAC). The flux helps to remove oxides from the metal surfaces, promotes wetting, and aids in the formation of a strong solder joint.
Solder paste is classified by its particle size and alloy composition. The particle size is indicated by a number, such as Type 3 or Type 4, with smaller numbers representing larger particle sizes. The alloy composition determines the melting point and mechanical properties of the solder joint.
Solder Paste Properties
To achieve high-quality solder joints, the solder paste must have the following properties:
- Printability: The paste should have a consistent viscosity and flow characteristics to ensure even distribution through the stencil apertures.
- Tack strength: The paste should have sufficient adhesive strength to hold the components in place during the placement process.
- Slump resistance: The paste should maintain its shape and not spread or slump excessively after printing.
- Flux activity: The flux should effectively remove oxides and promote wetting of the solder to the pad and component surfaces.
Solder Paste Printing Process
The solder paste printing process involves several steps, each of which must be carefully controlled to ensure consistent results.
Step 1: Stencil Preparation
The first step is to create a stencil with apertures that match the pads on the PCB. The stencil is typically made of stainless steel and is laser-cut or electroformed to achieve precise aperture dimensions. The stencil thickness, aperture size, and shape are determined based on the solder paste type, PCB design, and component requirements.
Step 2: Solder Paste Printing
The PCB is placed in a fixture, and the stencil is aligned over it. Solder paste is then applied to the stencil and spread across the surface using a squeegee blade. As the squeegee moves across the stencil, it forces the paste through the apertures and onto the pads of the PCB. The speed, pressure, and angle of the squeegee are critical factors in achieving a consistent and uniform print.
Step 3: Inspection
After printing, the PCB is inspected to ensure that the solder paste has been applied correctly. This is typically done using automated optical inspection (AOI) systems that can detect defects such as bridging, insufficient paste, or misalignment. If defects are found, the PCB may need to be cleaned and reprinted.
Step 4: Component Placement
Once the solder paste has been printed and inspected, the electronic components are placed onto the pads. This is done using pick-and-place machines that can accurately position the components at high speeds. The adhesive properties of the solder paste help to hold the components in place during this process.
Step 5: Reflow Soldering
After component placement, the PCB undergoes a reflow soldering process. The board is heated in a controlled manner, causing the solder paste to melt and form a permanent electrical and mechanical connection between the components and the PCB pads. The reflow profile, which defines the temperature and duration of the heating stages, must be carefully optimized for the specific solder paste and components used.
Factors Affecting Solder Paste Printing Quality
Several factors can influence the quality of the solder paste printing process:
-
Stencil design: The stencil aperture size, shape, and pitch must be optimized for the specific PCB design and solder paste type. Inadequate aperture design can lead to defects such as insufficient paste, bridging, or poor release.
-
Solder paste properties: The solder paste must have the appropriate rheological properties, such as viscosity and thixotropy, to ensure consistent printing and avoid defects such as slumping or bridging.
-
Printing parameters: The squeegee speed, pressure, and angle must be optimized to achieve a uniform and consistent print. Insufficient or excessive pressure can result in defects such as insufficient paste or bridging.
-
PCB and stencil condition: The PCB and stencil must be clean and free from contamination to ensure proper paste release and adhesion. Warped or damaged boards can lead to inconsistent printing results.
-
Environmental factors: Temperature and humidity can affect the rheological properties of the solder paste and lead to defects such as slumping or drying out. Proper storage and handling of the solder paste are essential to maintain its quality.
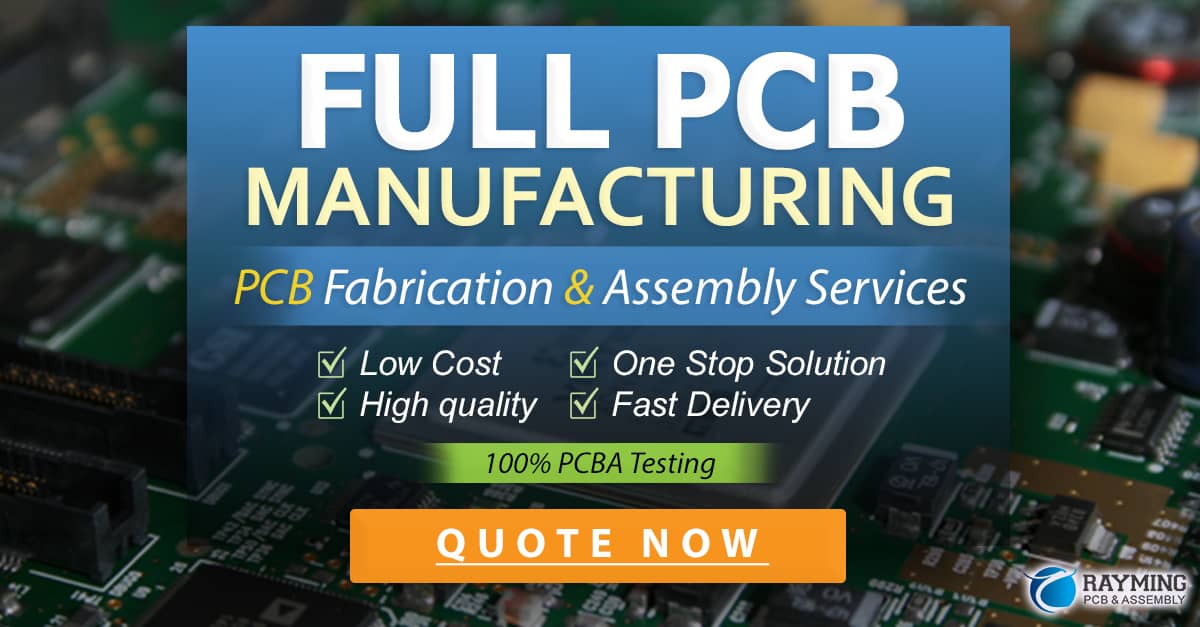
Common Solder Paste Printing Defects
Despite careful process control, various defects can occur during solder paste printing. Some common defects include:
-
Insufficient paste: This occurs when not enough solder paste is deposited on the pad, leading to weak or open solder joints.
-
Bridging: This happens when solder paste spreads and connects adjacent pads, causing short circuits.
-
Poor release: This occurs when the solder paste does not release cleanly from the stencil apertures, resulting in inconsistent or incomplete prints.
-
Misalignment: This happens when the stencil is not properly aligned with the PCB, causing the solder paste to be deposited in the wrong locations.
-
Slumping: This occurs when the solder paste spreads or flows excessively after printing, leading to bridging or insufficient paste height.
To minimize these defects, it is essential to regularly monitor and optimize the solder paste printing process. This involves using statistical process control (SPC) techniques to track key parameters such as paste volume, height, and alignment, and making adjustments as needed to maintain process stability.
Best Practices for Solder Paste Printing
To achieve consistent, high-quality solder paste printing results, consider the following best practices:
-
Use high-quality solder paste: Select a solder paste with the appropriate particle size, alloy composition, and rheological properties for your specific application.
-
Optimize stencil design: Work with your stencil supplier to develop an optimal stencil design that balances aperture size, shape, and pitch with the solder paste properties and PCB design.
-
Control printing parameters: Establish and maintain optimal squeegee speed, pressure, and angle settings for your specific solder paste and PCB combination.
-
Maintain cleanliness: Regularly clean the stencil, squeegee blades, and PCB surfaces to prevent contamination and ensure consistent printing results.
-
Monitor and inspect: Use Automated Inspection systems to monitor the solder paste print quality and detect defects early in the process. Regularly collect and analyze process data to identify trends and make proactive adjustments.
-
Train operators: Provide thorough training to operators on the solder paste printing process, including techniques for setting up, running, and troubleshooting the equipment.
-
Store solder paste properly: Follow the manufacturer’s recommendations for storing and handling solder paste to maintain its quality and performance.
Conclusion
Solder paste printing is a critical step in the SMT Assembly process that directly impacts the quality and reliability of the final assembled PCB. By understanding the solder paste properties, printing process, and common defects, manufacturers can optimize their processes to achieve consistent, high-quality results. Implementing best practices such as stencil optimization, parameter control, and regular monitoring and inspection can help to minimize defects and improve overall process efficiency.
FAQs
-
What is the shelf life of solder paste?
Solder paste typically has a shelf life of 6 to 12 months when stored at the recommended temperature (usually 0-10°C). However, this can vary depending on the specific paste formulation and storage conditions. Always refer to the manufacturer’s guidelines for the most accurate information. -
How often should I clean my stencil?
Stencils should be cleaned regularly to prevent paste buildup and contamination. The exact frequency depends on factors such as the paste type, print volume, and environmental conditions. As a general rule, stencils should be cleaned every 4-8 hours of continuous printing or whenever print quality begins to degrade. -
Can I reuse solder paste?
It is generally not recommended to reuse solder paste, as it can lead to contamination and degraded performance. Solder paste that has been exposed to air for extended periods or has been mixed with cleaning solvents should be discarded. Always use fresh solder paste for the best results. -
What is the optimal stencil thickness?
The optimal stencil thickness depends on factors such as the PCB design, component pitch, and solder paste type. In general, stencils range from 0.100mm to 0.150mm (4 to 6 mils) thick, with thinner stencils used for finer pitch components. Consult with your stencil supplier to determine the best thickness for your specific application. -
How do I troubleshoot solder paste printing defects?
Troubleshooting solder paste printing defects involves a systematic approach of identifying the root cause and implementing corrective actions. This may include adjusting printing parameters, cleaning or replacing the stencil, checking paste quality, or modifying the stencil design. Regularly monitoring process data and using statistical process control techniques can help to identify and resolve issues quickly.
Solder Paste Type | Particle Size | Alloy Composition | Melting Point |
---|---|---|---|
Type 3 | 25-45 µm | Sn63/Pb37 | 183°C |
Type 4 | 20-38 µm | Sn62/Pb36/Ag2 | 179°C |
Type 5 | 15-25 µm | Sn96.5/Ag3.0/Cu0.5 | 217°C |
Type 6 | 5-15 µm | Sn42/Bi57.6/Ag0.4 | 138°C |
The table above shows some common solder paste types and their properties. The particle size, alloy composition, and melting point can vary depending on the specific application requirements.
0 Comments