What is PCB Soldermask and Why Remove It?
Soldermask, also known as solder resist or solder stop mask, is a thin lacquer-like layer of polymer applied to the copper traces of a printed circuit board (PCB). Its primary purpose is to prevent solder from bridging between conductors and creating short circuits during the soldering process. Soldermask also provides protection against oxidation and contamination of the copper traces.
However, there are situations where you may need to remove the soldermask from specific areas of a PCB or from the entire board. Some common reasons for PCB Soldermask Removal include:
- Troubleshooting and repairing damaged or defective traces
- Modifying or reworking the PCB design
- Exposing copper for additional soldering or component placement
- Improving electrical conductivity for certain connections
- Aesthetic reasons, such as creating a retro or bare-bones look
Types of Soldermask
There are two main types of soldermask used on PCBs:
Soldermask Type | Description |
---|---|
Liquid photoimageable soldermask (LPI) | Applied as a liquid and then cured using UV light. Most common type. Usually green in color but available in other colors like red, blue, yellow, black, and white. |
Dry film soldermask | Applied as a thin, dry film and then heat cured. Less common. Typically used for special applications or low-volume production. |
The type of soldermask used can affect the choice of removal method, as some techniques may work better for one type than the other.
PCB Soldermask Removal Methods
There are several methods you can use to strip away soldermask from a PCB, each with its own pros and cons. The most appropriate removal technique will depend on factors such as the type and age of the soldermask, the size of the area to be removed, the tools and materials available, and your skill level.
Method 1: Mechanical Abrasion
One of the simplest ways to remove soldermask is through physical abrasion using tools like sandpaper, abrasive pads, or a fiberglass scratch brush pen. This method is best suited for removing small areas of soldermask.
Tools and Materials Needed
- Fine grit sandpaper (200 grit or higher) or abrasive pads
- Fiberglass scratch brush pen
- Isopropyl alcohol for cleaning
- Cotton swabs or lint-free wipes
- Safety glasses and dust mask
Step-by-Step Instructions
- Put on safety glasses and a dust mask to protect yourself from debris.
- Clean the area of the PCB you will be working on with isopropyl alcohol and let it dry completely.
- For small areas, use a fiberglass scratch brush pen to gently scrape away the soldermask. Go slowly and apply light pressure to avoid damaging the copper traces.
- For slightly larger areas, use fine grit sandpaper or an abrasive pad to sand off the soldermask. Use a circular motion and light pressure.
- Periodically wipe away the sanded material with a cotton swab or lint-free cloth.
- Continue abrading until the desired amount of copper is exposed. Be careful not to sand too deeply or you may damage the traces.
- Clean the PCB again with isopropyl alcohol to remove any debris.
Pros
- Inexpensive
- Uses common tools most people already have
- Good for small areas or minor modifications
Cons
- Time-consuming and labor-intensive for large areas
- Risk of damaging traces or pads if you sand too aggressively
- Leaves some residue behind
- Inconsistent results
Method 2: Chemical Removal
For removing soldermask from larger areas or entire PCBs, chemical removal is a more efficient option. This method uses solvents to dissolve and strip away the polymer coating. The two most common chemical options are acetone and soldermask remover solutions.
Option 1: Acetone
Acetone is an organic solvent that can soften and dissolve many types of polymers, including some soldermasks. It is inexpensive and readily available at most hardware stores and pharmacies.
Tools and Materials Needed
- Pure acetone (not nail polish remover which contains additives)
- Non-reactive container large enough to submerge PCB
- Nitrile gloves, safety glasses, respirator
- Ventilated work area
- Stiff-bristled brush
- Paper towels or rags
- Isopropyl alcohol for cleanup
Step-by-Step Instructions
- Protect yourself with gloves, glasses and a respirator rated for solvents. Work in a well-ventilated area as acetone fumes are toxic.
- Pour enough acetone into the container so that the PCB can be fully submerged without touching the bottom or sides. Do not use metal containers.
- Immerse the PCB in the acetone bath. Let soak for 10-20 minutes. The acetone will start to soften and dissolve the mask.
- Remove the PCB from the acetone and immediately begin scrubbing with the stiff brush to loosen the softened soldermask. Scrub gently to avoid damaging traces.
- Re-immerse the board in the acetone and continue alternating between soaking and scrubbing until bare copper is revealed. Change out the acetone if it becomes murky with dissolved mask.
- When the desired amount of soldermask is removed, wipe down the PCB with a rag or paper towel to remove the dissolved residue.
- Clean the board with fresh acetone or isopropyl alcohol to remove traces of solvent. Use cotton swabs to removed any stubborn bits of residual mask.
- Allow the PCB to dry thoroughly before continuing work. Dispose of used acetone as hazardous waste.
Pros
- Inexpensive
- Fairly quick acting for removing large areas
- Can dissolve stubborn, aged soldermask
Cons
- Toxic fumes require protective equipment and ventilation
- May not work on some soldermasks
- Can damage certain components if exposed
- Requires post-removal cleanup
Option 2: Commercial Soldermask Remover
For a safer and more consistent chemical removal option, you can use a commercial soldermask remover solution designed specifically for stripping PCBs. These products contain a blend of solvents optimized to break down the polymers in soldermask.
Tools and Materials Needed
- Soldermask remover solution (e.g. Soldermask Removal 270 from MG Chemicals)
- Non-reactive container large enough to submerge PCB
- Nitrile gloves, safety glasses, respirator
- Ventilated work area
- Stiff-bristled brush
- Rag or paper towels
- Isopropyl alcohol for cleanup
Step-by-Step Instructions
- Put on gloves, glasses and a respirator. Work in a well-ventilated area. While safer than pure acetone, mask remover solutions still have strong fumes.
- Pour the soldermask remover into the container to a depth that will cover the PCB.
- Immerse the PCB in the solution and let soak according to the manufacturer’s instructions, typically 5-20 minutes depending on the age and type of mask.
- Remove the board and scrub it with the brush using a light circular motion. The dissolving soldermask should come off easily.
- Re-immerse the board and continue alternating between soaking and scrubbing as needed until the desired copper is exposed.
- Wipe off the board with a paper towel to remove loosened mask. Use a swab to get into tight spots.
- Rinse the PCB with water and a small amount of detergent to neutralize any remaining solution. Then do a final wipe-down with isopropyl alcohol.
- Let the board dry completely. Dispose of the used remover as hazardous waste as directed by the manufacturer.
Pros
- Designed specifically for PCB soldermask removal
- Works quickly and consistently
- Can remove most types of masks in a single application
- Safer than pure acetone
Cons
- More expensive than acetone
- Strong odor still requires ventilation and PPE
- May attack certain components and plastics
Method 3: Laser Ablation
For high-precision, no-contact removal of soldermask, laser ablation is the most advanced technique. This method uses a focused beam of light to vaporize the soldermask material from the surface of the copper without the use of chemicals or abrasives.
Tools and Materials Needed
- Laser engraving/cutting machine with appropriate wavelength for soldermask (e.g. CO2 or fiber laser)
- Fume extraction system
- Laser-safe work surface
- Protective eyewear
Step-by-Step Instructions
- Put on laser-safe protective eyewear. Ensure the laser machine is properly ventilated with a fume extractor to remove vaporized material and smell.
- Place the PCB into the laser machine and focus the laser onto the surface of the board. Most machines have an auto-focus feature.
- Using the machine’s control software, set up the desired pattern for soldermask removal. This can be done by importing a vector file or creating the pattern directly in the software.
- Adjust the laser power and speed settings according to the manufacturer’s recommendations for the specific type and color of soldermask being removed. This will likely require some trial-and-error testing on scrap boards to dial in the optimal settings.
- Run the laser job and let the machine finish the ablation process. The laser will vaporize the soldermask in the programmed pattern, leaving the underlying copper exposed.
- Remove the PCB from the machine and inspect the results. Clean the board with compressed air or a soft brush to remove any debris.
Pros
- Fastest and most precise method, especially for intricate patterns
- No chemicals or physical contact required
- Consistent and repeatable results
- Can selectively remove mask while leaving mask intact elsewhere
Cons
- Requires expensive specialized equipment
- Steep learning curve to determine optimal settings
- High energy consumption
- Vaporized material requires extra ventilation
Tips for Successful PCB Soldermask Removal
Regardless of the removal method you choose, here are some general tips to keep in mind for safe and effective soldermask stripping:
- Always wear appropriate personal protective equipment (PPE) such as gloves, eyewear, and a respirator.
- Work in a well-ventilated area, especially when using chemical solvents.
- Start with the least aggressive method and work up as needed to minimize the risk of damaging the PCB.
- Test your chosen removal method on a small, inconspicuous area or a scrap board first to gauge its effectiveness and dial in the technique.
- Go slowly and gently to avoid overcutting, abrading, or dissolving the copper traces underneath the mask.
- Clean the PCB thoroughly with isopropyl alcohol after mask removal to remove any residue or contaminants.
- If in doubt, consult with a professional PCB fabrication or rework service for guidance on the best removal approach for your specific situation.
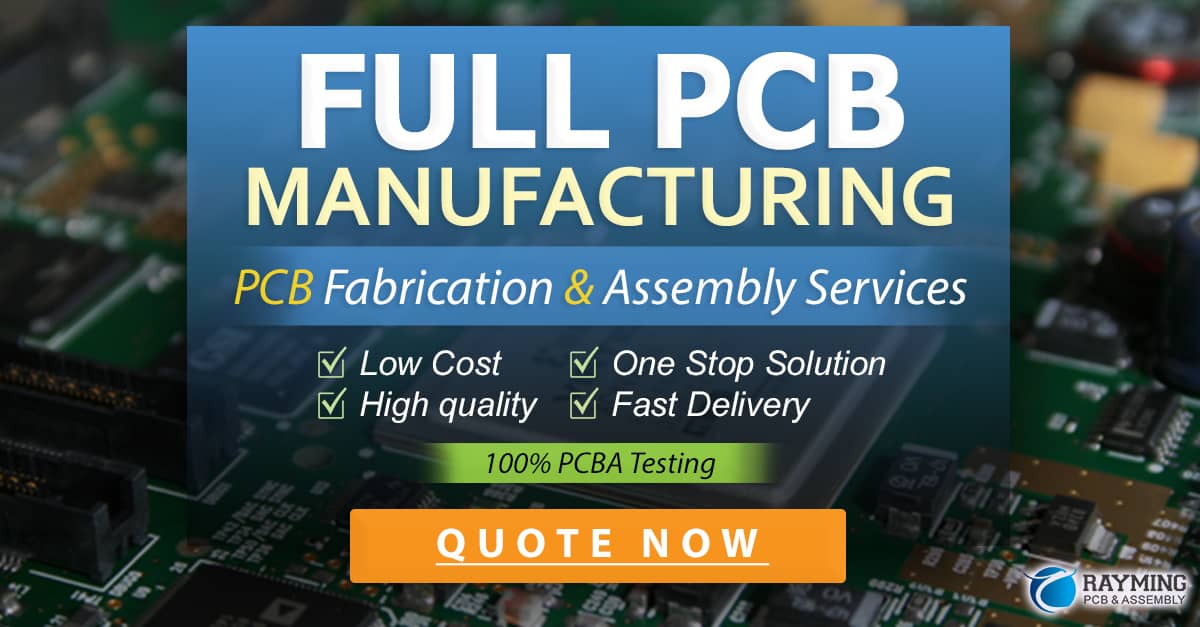
FAQ
Can I use a knife or blade to scrape off soldermask?
While it may be tempting to use a sharp tool like an X-Acto knife or razor blade, this is not recommended for removing soldermask. The risk of slipping and damaging the delicate traces is very high. Stick to the abrasive, chemical, or laser methods discussed above.
Will nail polish remover work for dissolving soldermask?
Nail polish remover often contains acetone but is not pure acetone. It has additional ingredients like fragrances, colorants, and moisturizing agents that can leave residue on the PCB or interact negatively with the components. For chemical removal, use only pure acetone or a dedicated soldermask remover solution.
Is it necessary to remove all the soldermask?
Not in most cases. Typically, you only need to remove the soldermask from specific areas where you need to access the copper for repairs, modifications, or improved conductivity. Removing the mask from the entire board is usually unnecessary and will reduce the protection for the traces.
What’s the best way to remove soldermask from small surface-mount pads?
For precise removal of soldermask on small SMD pads, laser ablation is the ideal method as it can vaporize the mask material without the risk of physical damage from abrasion or chemical undercutting. If you don’t have access to a laser, careful use of a fiberglass scratch brush pen or the tip of a safety pin can also work.
Can I reapply soldermask after removing it?
Yes, soldermask can be reapplied to a PCB after removal, either as a liquid or dry film. However, applying and curing new soldermask is a tricky process that requires specialized equipment and expertise to get proper adhesion and cosmetic results. In most cases, it’s best to leave soldermask reapplication to the professionals.
0 Comments