1. Proper PCB Design for BGA Packages
The first step in ensuring successful BGA Soldering is to design the PCB with the specific requirements of BGA packages in mind. Some key considerations include:
1.1. Pad Size and Pitch
The pad size and pitch of the BGA package must match the corresponding pads on the PCB. The pad size should be slightly larger than the diameter of the BGA balls to allow for proper solder joint formation. The pitch, which is the distance between the centers of adjacent pads, must be accurately maintained to ensure proper alignment during the soldering process.
1.2. Solder Mask Design
The solder mask design around the BGA pads is crucial for preventing solder bridging and ensuring proper solder joint formation. The solder mask opening should be slightly smaller than the pad size to prevent solder from spreading beyond the pad area.
1.3. Via Placement
Vias near the BGA pads can cause soldering issues due to the difference in thermal expansion between the PCB and the BGA package. It is recommended to avoid placing vias directly under the BGA pads and to use via-in-pad design techniques when necessary.
2. Stencil Design and Solder Paste Application
Proper stencil design and solder paste application are essential for achieving reliable BGA solder joints. The stencil aperture size and shape should be optimized based on the BGA pad size and pitch to ensure the correct amount of solder paste is deposited on each pad. The solder paste should be evenly applied using a high-quality solder paste printer with precise control over the printing parameters, such as squeegee pressure, speed, and separation distance.
3. BGA Package Handling and Placement
BGA packages are sensitive to mechanical stress and contamination, which can lead to soldering defects. Proper handling and placement techniques should be employed to minimize the risk of damage to the BGA package and ensure accurate alignment with the PCB pads. Some best practices include:
- Using ESD-safe handling equipment and work surfaces
- Avoiding excessive mechanical stress during package handling and placement
- Using vision systems to verify package alignment before soldering
- Employing automated pick-and-place equipment for consistent and accurate package placement
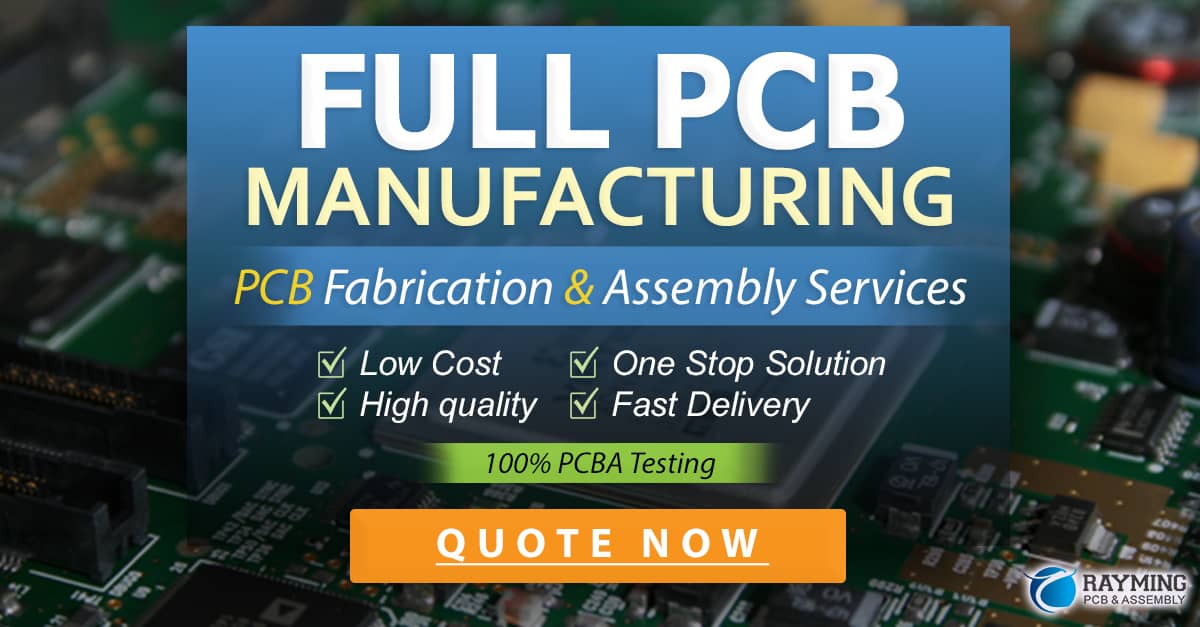
4. Reflow Soldering Profile Optimization
The reflow soldering profile plays a critical role in achieving reliable BGA solder joints. The profile must be optimized based on the specific requirements of the BGA package, PCB, and solder paste. Key parameters to consider include:
- Preheat rate and temperature
- Soak time and temperature
- Peak temperature and time above liquidus (TAL)
- Cooling rate
A well-designed reflow profile ensures that the solder paste melts evenly, the BGA balls collapse uniformly, and the solder joints form properly without defects such as voiding or head-in-pillow (HIP).
5. Nitrogen Reflow Soldering
Nitrogen reflow soldering involves using nitrogen gas to create an inert atmosphere during the soldering process. This technique offers several benefits for BGA soldering, including:
- Reduced oxidation of the solder joints, leading to improved wetting and joint strength
- Minimized solder balling and bridging defects
- Enhanced solder joint appearance and consistency
Nitrogen reflow soldering is particularly beneficial for Lead-Free Soldering processes, which are more susceptible to oxidation and defects compared to traditional lead-based solders.
6. Underfill Application
Underfill is a polymeric material that is applied between the BGA package and the PCB after soldering. The primary purpose of underfill is to enhance the mechanical strength and reliability of the BGA solder joints by redistributing the stress caused by the difference in thermal expansion between the package and the PCB. Underfill also protects the solder joints from environmental factors such as moisture and contamination.
There are two main types of underfill application methods:
- Capillary underfill: The underfill material is dispensed along the edges of the BGA package and is drawn underneath the package by capillary action.
- No-flow underfill: The underfill material is applied to the PCB before the BGA package is placed, and the soldering process is performed simultaneously with the underfill cure.
The choice of underfill material and application method depends on the specific requirements of the BGA package and the end-use application.
7. Inspection and Testing
After the BGA soldering process is complete, it is essential to perform thorough inspection and testing to verify the quality and reliability of the solder joints. Some common inspection and testing methods include:
- Visual inspection using microscopes or high-resolution cameras to check for defects such as bridging, voiding, or misalignment
- X-ray inspection to detect internal defects such as voids or cracks in the solder joints
- Electrical testing to verify the continuity and functionality of the BGA interconnections
- Thermal cycling and mechanical stress testing to assess the long-term reliability of the solder joints under various environmental conditions
Regular inspection and testing help identify and correct any soldering issues early in the manufacturing process, reducing the risk of field failures and product returns.
8. Rework and Repair Techniques
Despite best efforts, BGA soldering defects may still occur, requiring rework or repair. Proper rework and repair techniques are crucial for maintaining the integrity of the PCB and the BGA package while correcting the soldering issues. Some key considerations for BGA Rework and repair include:
- Using specialized rework equipment, such as hot air or infrared systems, to remove the defective BGA package without damaging the PCB
- Cleaning the PCB pads thoroughly to remove any residual solder or contamination before replacing the BGA package
- Applying fresh solder paste or flux to the PCB pads before placing the new BGA package
- Utilizing the appropriate reflow profile and underfill application method for the reworked BGA package
Proper training and experience are essential for performing successful BGA rework and repair, as improper techniques can lead to further damage or reliability issues.
9. Continuous Process Improvement
Achieving consistent and reliable BGA soldering requires a commitment to continuous process improvement. This involves regularly monitoring and analyzing the soldering process parameters, inspection and testing results, and field performance data to identify areas for optimization. Some strategies for continuous improvement include:
- Implementing statistical process control (SPC) techniques to monitor and control the critical soldering parameters
- Conducting root cause analysis (RCA) to identify and eliminate the sources of soldering defects
- Investing in employee training and education to ensure that best practices are followed consistently
- Collaborating with suppliers and customers to optimize the design and manufacturing processes for BGA assemblies
By continuously improving the BGA soldering process, manufacturers can enhance product quality, reduce costs, and increase customer satisfaction.
Frequently Asked Questions (FAQ)
1. What are the most common BGA soldering defects?
The most common BGA soldering defects include:
– Bridging: Solder connecting adjacent pads or balls, causing short circuits
– Voiding: Trapped air or gases within the solder joint, reducing joint strength and reliability
– Head-in-pillow (HIP): Incomplete collapse of the BGA ball onto the PCB pad, resulting in a weak or open connection
– Misalignment: BGA package not properly aligned with the PCB pads, leading to poor solder joint formation
2. How can I prevent BGA soldering defects?
To prevent BGA soldering defects, consider the following:
– Ensure proper PCB design, including pad size, pitch, and solder mask layout
– Optimize the stencil design and solder paste application process
– Use appropriate BGA package handling and placement techniques
– Develop and maintain a well-controlled reflow soldering profile
– Implement nitrogen reflow soldering to reduce oxidation and improve joint quality
– Apply underfill material to enhance solder joint strength and reliability
3. What equipment is needed for BGA rework and repair?
BGA rework and repair typically require specialized equipment, such as:
– Hot air or infrared rework stations for removing and replacing BGA packages
– High-magnification microscopes or cameras for visual inspection
– Soldering Irons and tips designed for BGA rework
– Stencils and solder paste dispensers for applying fresh solder paste or flux
– Reflow ovens or heating systems for soldering the reworked BGA package
4. How can I optimize the reflow soldering profile for BGA packages?
To optimize the reflow soldering profile for BGA packages, consider the following factors:
– Use the solder paste manufacturer’s recommended profile as a starting point
– Adjust the preheat rate and temperature to ensure gradual and even heating of the PCB and components
– Optimize the soak time and temperature to activate the solder paste flux and minimize thermal shock
– Control the peak temperature and time above liquidus (TAL) to ensure complete solder melting and wetting without damaging the components
– Adjust the cooling rate to minimize thermal stress and prevent solidification defects
5. What are the benefits of using underfill for BGA packages?
The benefits of using underfill for BGA packages include:
– Enhanced mechanical strength and reliability of the solder joints
– Reduced stress caused by the difference in thermal expansion between the package and the PCB
– Protection of the solder joints from environmental factors, such as moisture and contamination
– Improved thermal conductivity and heat dissipation from the BGA package to the PCB
– Increased resistance to vibration and mechanical shock, particularly in harsh operating conditions
In conclusion, achieving reliable BGA soldering on PCBs in SMT Assembly requires a comprehensive approach that addresses various aspects of the design, manufacturing, and quality control processes. By implementing the nine ways discussed in this article, manufacturers can significantly improve the quality and reliability of their BGA assemblies, ultimately leading to better product performance and customer satisfaction.
Parameter | Recommended Value |
---|---|
Pad Size | 1.1 – 1.2 times the BGA ball diameter |
Pitch | Matched to the BGA package pitch |
Solder Mask Opening | 80-90% of the pad size |
Stencil Thickness | 0.1 – 0.15 mm (4-6 mils) |
Solder Paste Print Speed | 25-50 mm/s |
Reflow Peak Temperature | 235-245°C (lead-free solder) |
Time Above Liquidus (TAL) | 60-90 seconds |
Cooling Rate | 1-4°C/second |
Table 1. Recommended parameters for BGA soldering on PCBs in SMT assembly.
By carefully controlling these parameters and following the best practices outlined in this article, manufacturers can achieve consistent and reliable BGA soldering results, minimizing defects and ensuring the long-term performance of their products.
0 Comments