Understanding PCB Thickness
PCB thickness refers to the distance between the top and bottom surfaces of the board. It is typically measured in either millimeters (mm) or mils (thousandths of an inch). The thickness of a PCB plays a significant role in its mechanical strength, electrical properties, and overall functionality.
Common PCB Thickness Measurements
PCB thickness is commonly expressed in either metric or imperial units. Here are some standard measurements:
Metric (mm) | Imperial (mils) |
---|---|
0.4 mm | 15.75 mils |
0.6 mm | 23.62 mils |
0.8 mm | 31.50 mils |
1.0 mm | 39.37 mils |
1.2 mm | 47.24 mils |
1.6 mm | 62.99 mils |
2.0 mm | 78.74 mils |
It’s important to note that these are just a few examples, and PCB thickness can vary depending on the specific requirements of the project.
Factors Influencing PCB Thickness Choice
When designing a PCB, several factors come into play when determining the appropriate thickness. Let’s explore some of these factors in detail.
Application Requirements
The intended application of the PCB is a primary consideration when selecting the thickness. Different applications have varying demands in terms of mechanical strength, weight, and space constraints.
For example, in automotive or aerospace applications, where the PCB is subjected to vibrations and harsh environmental conditions, a thicker board may be necessary to ensure robustness and reliability. On the other hand, in consumer electronics or wearable devices, where lightweight and compact design is crucial, thinner PCBs are often preferred.
Layer Count
The number of layers in a PCB also influences the thickness choice. As the layer count increases, the overall thickness of the board typically increases as well. This is because each additional layer requires an insulating substrate and copper foil, adding to the total thickness.
Here’s a general guide to the relationship between layer count and PCB thickness:
Layer Count | Typical Thickness Range |
---|---|
1-2 layers | 0.4 mm – 0.8 mm |
4 layers | 0.8 mm – 1.6 mm |
6-8 layers | 1.2 mm – 2.0 mm |
10+ layers | 2.0 mm and above |
It’s worth noting that these are rough estimates, and the actual thickness may vary based on the specific design requirements and manufacturing capabilities.
Copper Weight
Copper weight, expressed in ounces per square foot (oz/ft²), refers to the thickness of the copper foil used on the PCB. The choice of copper weight affects the current carrying capacity and the overall thickness of the board.
Common copper weights include:
- 0.5 oz/ft² (17.5 μm)
- 1 oz/ft² (35 μm)
- 2 oz/ft² (70 μm)
- 3 oz/ft² (105 μm)
Thicker copper weights provide better current carrying capacity and improved thermal dissipation but also contribute to the overall thickness of the PCB.
Manufacturing Capabilities
The manufacturing capabilities of the PCB fabricator also play a role in determining the achievable thickness. Different manufacturers have varying equipment and processes, which can limit the minimum and maximum thickness they can reliably produce.
It’s crucial to consult with the PCB manufacturer early in the design process to ensure that the desired thickness is feasible and aligns with their manufacturing capabilities. This can help avoid potential issues and delays during production.
Implications of PCB Thickness
The chosen PCB thickness has several implications on the performance, manufacturability, and cost of the board. Let’s explore these aspects further.
Mechanical Strength and Durability
Thicker PCBs generally offer better mechanical strength and durability compared to thinner boards. They are less susceptible to bending, warping, and damage during handling and assembly. This is particularly important in applications where the PCB is subjected to physical stress or vibrations.
However, it’s worth noting that the mechanical strength of a PCB is not solely determined by its thickness. Other factors, such as the material composition, reinforcement, and design features, also contribute to the overall mechanical integrity of the board.
Electrical Performance
PCB thickness can impact the electrical performance of the board, particularly at high frequencies. Thinner PCBs tend to have better high-frequency performance due to reduced dielectric losses and improved impedance control.
In high-speed digital circuits or RF applications, where signal integrity is critical, thinner PCBs are often preferred. They allow for tighter control over impedance matching and minimize signal reflections, ensuring reliable signal transmission.
On the other hand, thicker PCBs may be necessary for power electronics or high-current applications. The increased thickness provides better thermal dissipation and allows for wider traces to handle higher currents without excessive heating.
Manufacturing Cost
PCB thickness also has an impact on manufacturing costs. Generally, thinner PCBs are more economical to manufacture compared to thicker boards. This is because thinner boards require less material and can be produced more efficiently.
However, the cost savings from using thinner PCBs should be balanced against the specific requirements of the application. In some cases, the added cost of a thicker board may be justified if it ensures better performance, reliability, and longevity of the end product.
Assembly Considerations
The thickness of the PCB can influence the assembly process and the compatibility with certain components. Thicker boards may require special considerations for component placement and soldering.
For example, when using through-hole components on a thick PCB, longer leads may be necessary to ensure proper soldering and mechanical stability. Surface-mount components, on the other hand, are generally more compatible with a wider range of PCB thicknesses.
It’s important to consider the assembly requirements and component compatibility when selecting the PCB thickness to ensure a smooth and reliable manufacturing process.
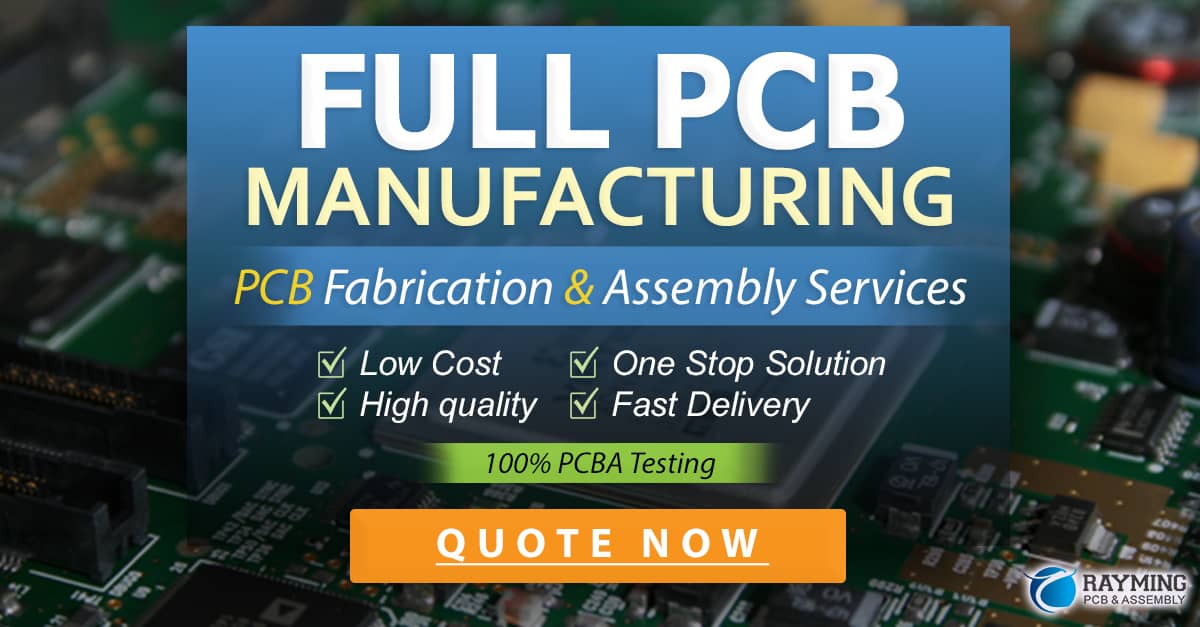
Standard PCB Thickness in Different Industries
Different industries and applications have varying standards and preferences for PCB thickness. Let’s take a look at some common industry practices.
Consumer Electronics
In consumer electronics, such as smartphones, tablets, and laptops, thin and lightweight PCBs are highly desirable. These devices often use PCBs with thicknesses ranging from 0.4 mm to 1.0 mm to achieve compact and portable designs.
Automotive Electronics
Automotive electronics require robust and reliable PCBs that can withstand harsh environmental conditions, vibrations, and temperature extremes. In this industry, thicker PCBs, typically ranging from 1.2 mm to 2.0 mm, are commonly used to ensure the necessary mechanical strength and durability.
Industrial Electronics
Industrial electronics encompass a wide range of applications, from process control systems to power electronics. The PCB thickness in this industry varies depending on the specific requirements of each application.
For general-purpose industrial electronics, PCBs with thicknesses between 1.0 mm and 1.6 mm are commonly used. However, in high-power or high-voltage applications, thicker PCBs up to 3.0 mm or more may be necessary to accommodate larger components and provide adequate insulation.
Aerospace and Defense
In the aerospace and defense industry, PCBs are subjected to stringent requirements for reliability, durability, and performance. PCBs used in these applications often have thicknesses ranging from 1.6 mm to 2.5 mm to meet the demanding environmental and operational conditions.
Additionally, aerospace and defense applications may require specialized PCB materials and construction techniques, such as high-temperature laminates or metal-backed PCBs, to ensure optimal performance and reliability.
Frequently Asked Questions (FAQ)
-
What is the most common PCB thickness?
The most common PCB thickness varies depending on the industry and application. However, in general, PCBs with thicknesses ranging from 1.0 mm to 1.6 mm are widely used across different sectors due to their balance between mechanical strength and manufacturing cost. -
Can I use a thinner PCB to save cost?
While using a thinner PCB can indeed result in cost savings, it’s essential to consider the specific requirements of your application. If the PCB needs to withstand mechanical stress, vibrations, or high-current loads, a thinner board may not be suitable. It’s important to strike a balance between cost and performance to ensure the reliability and longevity of the end product. -
How does PCB thickness affect signal integrity?
PCB thickness can impact signal integrity, particularly at high frequencies. Thinner PCBs generally have better high-frequency performance due to reduced dielectric losses and improved impedance control. They allow for tighter control over impedance matching and minimize signal reflections, ensuring reliable signal transmission. However, the specific impact on signal integrity depends on various factors, such as the PCB material, trace geometry, and routing techniques. -
Can I mix different PCB thicknesses in the same design?
Yes, it is possible to have different PCB thicknesses within the same design. This approach is known as a “rigid-flex” or “multi-thickness” PCB. It involves combining rigid PCB sections of different thicknesses with flexible PCB sections to achieve specific mechanical or electrical requirements. However, designing and manufacturing multi-thickness PCBs requires careful planning and coordination with the PCB fabricator to ensure compatibility and reliability. -
How do I determine the appropriate PCB thickness for my project?
Determining the appropriate PCB thickness for your project involves considering several factors, including: - The intended application and its specific requirements
- Mechanical strength and durability needs
- Electrical performance and signal integrity considerations
- Component compatibility and assembly requirements
- Manufacturing capabilities and cost constraints
It’s recommended to consult with experienced PCB designers and manufacturers early in the design process to discuss your specific requirements and obtain guidance on selecting the most suitable PCB thickness for your project.
Conclusion
PCB thickness is a critical aspect of PCB design that greatly influences the mechanical, electrical, and thermal properties of the board. Understanding the standard PCB thicknesses and the factors that affect thickness choice is essential for designers and engineers to make informed decisions.
When selecting the appropriate PCB thickness, it’s crucial to consider the intended application, layer count, copper weight, and manufacturing capabilities. The chosen thickness has implications on the mechanical strength, electrical performance, manufacturing cost, and assembly considerations of the PCB.
Different industries and applications have varying standards and preferences for PCB thickness, ranging from thin and lightweight boards in consumer electronics to thicker and more robust boards in automotive and aerospace applications.
By carefully evaluating the specific requirements of the project and consulting with experienced PCB manufacturers, designers can select the optimal PCB thickness that balances performance, reliability, and cost-effectiveness. This ensures the successful development and production of high-quality electronic devices.
0 Comments