Understanding Solder Reflow Profile
The solder reflow profile is a critical aspect of the electronic manufacturing process, specifically in surface mount technology (SMT). It refers to the precise temperature profile that solder paste and components are subjected to during the reflow soldering process. The reflow profile ensures proper melting and solidification of the solder, forming reliable electrical and mechanical connections between components and the printed circuit board (PCB).
Key Elements of a Solder Reflow Profile
A typical solder reflow profile consists of four main stages:
-
Preheat: The PCB and components are gradually heated to a temperature just below the melting point of the solder paste. This stage helps evaporate solvents and activate the flux in the solder paste.
-
Thermal Soak: The temperature is maintained at a stable level for a specific duration to ensure even heat distribution across the PCB and components. This stage also allows the components to reach thermal equilibrium.
-
Reflow: The temperature is rapidly increased above the melting point of the solder paste, causing the solder to melt and form connections between the components and the PCB pads.
-
Cooling: The PCB is cooled down at a controlled rate to allow the molten solder to solidify and form strong, reliable solder joints.
Each stage of the reflow profile has specific temperature ranges, ramp rates, and dwell times that must be carefully controlled to achieve optimal soldering results.
Factors Influencing Solder Reflow Profile
Several factors influence the design and implementation of a solder reflow profile:
Solder Paste Characteristics
The type of solder paste used, its composition, and its melting point temperature significantly impact the reflow profile. Common solder paste alloys include:
- Tin-Lead (SnPb): Traditionally used, but being phased out due to environmental concerns.
- Lead-Free (SAC): Tin-Silver-Copper alloys, such as SAC305, are widely used as lead-free alternatives.
The melting point of the solder paste determines the peak temperature and the duration of the reflow stage.
PCB and Component Characteristics
The PCB design, thickness, and thermal mass affect the heat transfer and temperature distribution during reflow. Components with different package sizes, thermal mass, and heat sensitivity also influence the reflow profile. The reflow profile must be tailored to accommodate the most heat-sensitive components while ensuring proper solder joint formation for all components.
Reflow Oven Capabilities
The type of reflow oven used, its heating zones, and its temperature control capabilities impact the reflow profile. Convection reflow ovens, which use forced hot air for heating, are the most common type used in SMT assembly. Other types include infrared (IR) and vapor phase reflow ovens.
Developing and Optimizing Solder Reflow Profile
Developing an optimal solder reflow profile involves several steps:
-
Gather information: Collect data on the solder paste, PCB, components, and reflow oven specifications.
-
Define target profile: Based on the collected information, define the target reflow profile, including temperature ranges, ramp rates, and dwell times for each stage.
-
Conduct profile testing: Use thermocouples attached to the PCB to measure the actual temperature profile during a test run in the reflow oven.
-
Analyze and adjust: Compare the measured profile with the target profile and make necessary adjustments to the oven settings to achieve the desired profile.
-
Validate and document: Conduct additional test runs to validate the optimized reflow profile and document the settings for future reference.
Regularly monitoring and maintaining the reflow profile ensures consistent soldering quality and minimizes defects such as solder bridges, incomplete melting, or thermal damage to components.
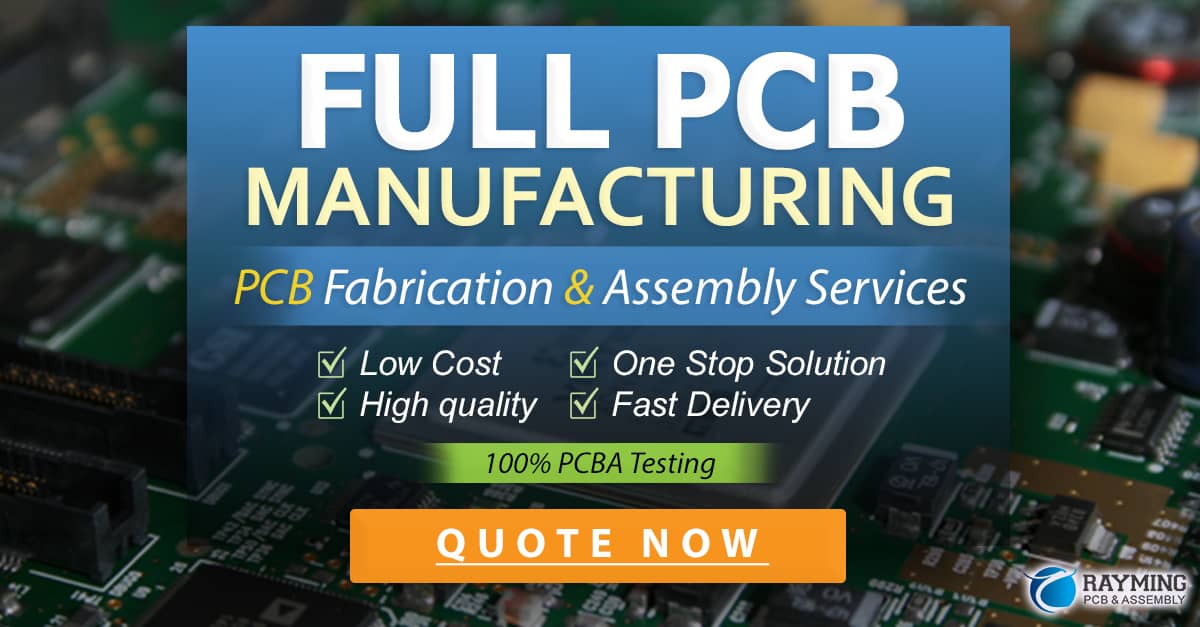
Common Solder Reflow Profile Guidelines
While specific reflow profiles vary based on the solder paste and PCB Assembly requirements, some general guidelines apply:
Preheat Stage
- The preheat ramp rate is typically between 2°C/second and 4°C/second.
- The preheat temperature is usually between 150°C and 180°C.
- The preheat duration is usually between 60 and 120 seconds.
Thermal Soak Stage
- The soak temperature is typically between 150°C and 200°C.
- The soak duration is usually between 60 and 180 seconds.
Reflow Stage
- The reflow peak temperature is typically between 20°C and 40°C above the solder paste melting point.
- The time above liquidus (TAL), which is the duration the solder is in a molten state, is typically between 30 and 90 seconds.
- The reflow ramp rate is usually between 2°C/second and 4°C/second.
Cooling Stage
- The cooling ramp rate is typically between -2°C/second and -6°C/second.
- The cooling stage aims to bring the PCB assembly to a temperature below 100°C.
These guidelines provide a starting point for developing a reflow profile, but the actual values may vary based on specific requirements and constraints.
Solder Reflow Profile Examples
To better understand solder reflow profiles, let’s examine a few examples based on common solder paste alloys:
SnPb Solder Reflow Profile
Stage | Temperature Range | Duration | Ramp Rate |
---|---|---|---|
Preheat | 25°C to 150°C | 60-90 sec | 2-3°C/sec |
Soak | 150°C to 180°C | 60-120 sec | 0.5-1°C/sec |
Reflow | 200°C to 225°C | 30-60 sec | 2-3°C/sec |
Peak | 225°C to 235°C | 10-20 sec | – |
Cooling | 235°C to 100°C | 60-120 sec | -2 to -4°C/sec |
Lead-Free (SAC305) Solder Reflow Profile
Stage | Temperature Range | Duration | Ramp Rate |
---|---|---|---|
Preheat | 25°C to 150°C | 60-120 sec | 2-3°C/sec |
Soak | 150°C to 200°C | 60-180 sec | 0.5-1°C/sec |
Reflow | 235°C to 255°C | 30-90 sec | 2-3°C/sec |
Peak | 255°C to 260°C | 10-30 sec | – |
Cooling | 260°C to 100°C | 60-180 sec | -2 to -6°C/sec |
These examples demonstrate the differences in temperature ranges and durations for different solder paste alloys. Lead-free solder alloys generally require higher peak temperatures and longer dwell times compared to SnPb solder.
Challenges and Considerations in Solder Reflow Profiling
Developing and maintaining an optimal solder reflow profile can be challenging due to various factors:
-
Component compatibility: PCB assemblies often include components with different heat sensitivities and thermal requirements. Balancing the reflow profile to accommodate all components without damaging the most sensitive ones can be difficult.
-
PCB design complexity: High-density PCB designs with large component counts and varying thermal masses can make it challenging to achieve even heat distribution during reflow.
-
Oven performance variability: Reflow ovens may have variations in temperature control and heat distribution across different zones and over time, requiring regular monitoring and calibration.
-
Solder paste variability: Solder paste composition and quality can vary between batches, affecting the reflow profile requirements.
-
Environmental factors: Ambient temperature, humidity, and air flow in the production environment can influence the reflow process and require profile adjustments.
To mitigate these challenges, manufacturers implement several best practices:
- Thorough testing and validation of reflow profiles for new PCB assemblies.
- Regular monitoring and maintenance of reflow ovens to ensure consistent performance.
- Use of profile optimization software and data logging tools to analyze and fine-tune reflow profiles.
- Proper storage and handling of solder paste to maintain its quality and consistency.
- Environmental control in the production area to minimize external influences on the reflow process.
Frequently Asked Questions (FAQ)
-
What is the purpose of a solder reflow profile?
A solder reflow profile defines the temperature profile that a PCB assembly goes through during the reflow soldering process. Its purpose is to ensure proper melting and solidification of the solder paste to form reliable solder joints between components and the PCB. -
What are the main stages of a solder reflow profile?
The four main stages of a solder reflow profile are: - Preheat: Gradual heating to a temperature just below the solder paste melting point.
- Thermal Soak: Maintaining a stable temperature for even heat distribution.
- Reflow: Rapid heating above the solder paste melting point to melt the solder.
-
Cooling: Controlled cooling to allow the molten solder to solidify.
-
How does the solder paste alloy affect the reflow profile?
The solder paste alloy, such as SnPb or lead-free SAC, determines the melting point temperature and the required peak temperature and dwell time during the reflow stage. Lead-free solder alloys generally require higher peak temperatures and longer dwell times compared to SnPb solder. -
What are some common challenges in developing and maintaining solder reflow profiles?
Common challenges include: - Accommodating components with different heat sensitivities and thermal requirements.
- Achieving even heat distribution in complex, high-density PCB designs.
- Dealing with reflow oven performance variability and solder paste inconsistencies.
-
Adapting to environmental factors like ambient temperature and humidity.
-
How can manufacturers ensure consistent and reliable solder reflow profiles?
Manufacturers can ensure consistent and reliable solder reflow profiles by: - Conducting thorough testing and validation for new PCB assemblies.
- Regularly monitoring and maintaining reflow ovens.
- Using profile optimization software and data logging tools.
- Properly storing and handling solder paste.
- Controlling the production environment to minimize external influences.
Conclusion
The solder reflow profile is a critical aspect of the SMT assembly process, ensuring proper solder joint formation and the overall reliability of electronic devices. By understanding the key elements, influencing factors, and best practices in developing and maintaining solder reflow profiles, manufacturers can optimize their soldering processes and produce high-quality PCB assemblies consistently.
As electronic designs continue to evolve with smaller components, higher densities, and more complex thermal requirements, the importance of accurate and well-controlled solder reflow profiles will only increase. Manufacturers must stay up-to-date with the latest technologies, techniques, and guidelines to meet the ever-growing demands of the electronics industry while ensuring the reliability and longevity of their products.
0 Comments