Introduction to PCB Inner Layers
Printed Circuit Boards (PCBs) are essential components in modern electronics. They provide a platform for mounting and interconnecting electronic components to create functional circuits. While the outer layers of a PCB are visible and often feature component footprints and labels, the inner layers play a crucial role in the overall functionality and performance of the board. In this article, we will dive deep into the concept of PCB inner layers, their purpose, manufacturing process, and design considerations.
What are PCB Inner Layers?
PCB inner layers, also known as internal layers or buried layers, are the conductive layers sandwiched between the outer layers of a Multi-Layer PCB. These layers are not visible from the outside and are buried within the PCB Stack-Up. The inner layers are responsible for carrying signals, power, and ground connections between components on different layers of the board.
Types of PCB Inner Layers
There are two main types of PCB inner layers:
-
Signal Layers: These layers are used for routing signals between components on the PCB. They are designed to carry high-speed or sensitive signals with minimal interference and crosstalk.
-
Power and Ground Layers: These layers are dedicated to providing stable power and ground connections to the components on the PCB. They help in reducing electromagnetic interference (EMI) and ensuring proper power distribution.
Importance of PCB Inner Layers
Increased Routing Density
One of the primary advantages of using inner layers in a PCB is the increased routing density. With multiple layers available for routing, designers can accommodate more complex circuits and a higher number of components on a single board. This is particularly important in applications where space is limited, such as in smartphones, wearables, and IoT devices.
Improved Signal Integrity
PCB inner layers play a crucial role in maintaining signal integrity. By carefully designing the signal layers and controlling the impedance of the traces, designers can minimize signal reflections, crosstalk, and other signal integrity issues. This is essential for high-speed digital circuits, where signal integrity is critical for reliable operation.
Better Power Distribution
Dedicated power and ground layers in a PCB help in providing a low-impedance path for power distribution. By using wide copper pours and strategically placing power and ground vias, designers can ensure stable power delivery to all components on the board. This reduces voltage drops, minimizes ground bounces, and improves overall power integrity.
Enhanced Electromagnetic Compatibility (EMC)
PCB inner layers can be used to implement EMC strategies, such as shielding and grounding. By placing ground layers between signal layers, designers can create a Faraday cage effect, reducing electromagnetic interference (EMI) and improving the board’s electromagnetic compatibility. This is particularly important in applications that are sensitive to EMI, such as medical devices and automotive electronics.
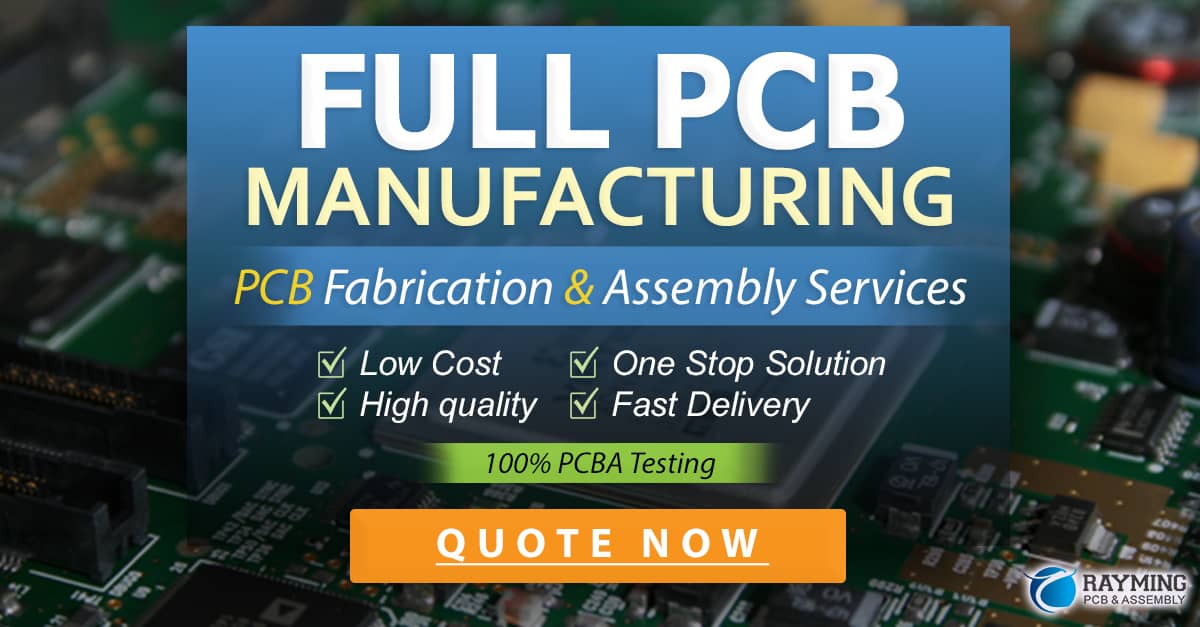
Manufacturing Process of PCB Inner Layers
The manufacturing process of PCB inner layers involves several steps, including:
-
Layer Stackup Design: The first step is to design the layer stackup, which defines the number, thickness, and arrangement of the inner layers. This is based on the electrical and mechanical requirements of the PCB.
-
Inner Layer Patterning: The inner layer copper foils are patterned using a photolithography process. The desired circuit pattern is transferred onto the copper foil using a photomask and UV light exposure.
-
Etching: After patterning, the unwanted copper is removed using a chemical etching process, leaving behind the desired Circuit Traces.
-
Lamination: The patterned inner layers are sandwiched between insulating layers, typically made of prepreg (pre-impregnated) material. The stack-up is then laminated under high pressure and temperature to form a solid, multi-layer PCB.
-
Drilling and Plating: After lamination, holes are drilled through the PCB to create vias and component mounting holes. These holes are then plated with copper to establish electrical connections between layers.
-
Outer Layer Processing: Finally, the outer layers of the PCB are processed, including applying solder mask, silkscreen, and surface finish.
Design Considerations for PCB Inner Layers
Designing PCB inner layers requires careful consideration of various factors to ensure optimal performance and manufacturability. Some key design considerations include:
Signal Integrity
-
Trace Width and Spacing: The width and spacing of traces on the inner layers should be carefully designed to maintain the desired impedance and minimize crosstalk. High-speed signals may require thinner traces and larger spacing to reduce interference.
-
Via Placement: Vias are used to connect traces on different layers. Proper via placement is crucial for maintaining signal integrity and minimizing stub effects.
-
Impedance Control: Controlling the impedance of traces on the inner layers is essential for high-speed signals. This involves selecting the appropriate dielectric material, copper thickness, and trace geometry.
Power Integrity
-
Power Plane Design: Power planes on the inner layers should be designed to provide a low-impedance path for power distribution. This includes using wide copper pours and placing power vias strategically.
-
Decoupling Capacitors: Decoupling capacitors should be placed close to the power pins of components to minimize power supply noise and ensure stable power delivery.
Thermal Management
-
Copper Thickness: The thickness of the copper on the inner layers affects the thermal conductivity of the PCB. Thicker copper layers can help dissipate heat more effectively.
-
Thermal Vias: Thermal vias can be used to transfer heat from the inner layers to the outer layers or to a heatsink. They help in improving the overall thermal performance of the PCB.
Manufacturability
-
Minimum Feature Size: The minimum feature size, such as trace width and spacing, should be within the capabilities of the PCB manufacturer. Pushing the limits too far can lead to manufacturing issues and reduced yield.
-
Layer Registration: Proper layer registration is critical for ensuring accurate alignment of features on different layers. Misalignment can cause short circuits or open connections.
FAQ
What is the purpose of inner layers in a PCB?
Inner layers in a PCB serve multiple purposes, including increasing routing density, improving signal integrity, providing better power distribution, and enhancing electromagnetic compatibility. They allow for more complex circuits to be implemented in a smaller form factor while maintaining optimal performance.
How many inner layers can a PCB have?
The number of inner layers in a PCB can vary depending on the complexity of the circuit and the manufacturing capabilities. PCBs can have anywhere from 2 to over 40 layers, with 4, 6, and 8-Layer PCBs being common configurations. High-density PCBs used in advanced applications may have even more layers.
What materials are used for PCB inner layers?
PCB inner layers are typically made of copper foil laminated onto an insulating substrate material. The most common substrate materials are FR-4 (Flame Retardant 4), which is a glass-reinforced epoxy laminate, and polyimide for high-temperature applications. The copper foil thickness can vary, with common thicknesses being 0.5 oz, 1 oz, and 2 oz per square foot.
How are inner layers connected to outer layers in a PCB?
Inner layers are connected to outer layers in a PCB through vias. Vias are conductive holes drilled through the PCB and plated with copper. They allow signals and power to pass through different layers of the board. There are different types of vias, such as Through-hole vias, blind vias, and buried vias, each serving specific purposes in connecting layers.
What are the challenges in designing and manufacturing PCB inner layers?
Designing and manufacturing PCB inner layers come with several challenges. Signal integrity issues, such as impedance mismatch, crosstalk, and signal reflections, need to be carefully addressed. Power integrity concerns, including voltage drops and ground bounces, must be minimized. Thermal management is crucial to prevent overheating and ensure reliable operation. Manufacturability aspects, such as minimum feature sizes and layer registration, should also be considered to avoid production issues and maintain high yields.
Conclusion
PCB inner layers are the hidden heroes of modern electronics. They provide the necessary interconnections, power distribution, and signal routing capabilities that enable the functioning of complex circuits in a compact form factor. Understanding the types, importance, manufacturing process, and design considerations of PCB inner layers is crucial for engineers and designers working on advanced electronic projects.
By carefully designing the inner layers, considering factors such as signal integrity, power integrity, thermal management, and manufacturability, engineers can create high-performance PCBs that meet the demanding requirements of today’s applications. As technology continues to advance, the role of PCB inner layers will become even more critical in enabling the next generation of electronic devices.
Key Takeaways
- PCB inner layers are the conductive layers sandwiched between the outer layers of a multi-layer PCB.
- They serve important functions, including increasing routing density, improving signal integrity, providing better power distribution, and enhancing electromagnetic compatibility.
- The manufacturing process of PCB inner layers involves layer stackup design, patterning, etching, lamination, drilling, plating, and outer layer processing.
- Designing PCB inner layers requires careful consideration of signal integrity, power integrity, thermal management, and manufacturability aspects.
- As technology advances, the role of PCB inner layers will continue to be crucial in enabling high-performance electronic devices.
Term | Definition |
---|---|
PCB Inner Layer | The conductive layers sandwiched between the outer layers of a multi-layer PCB. |
Signal Layer | A PCB inner layer used for routing signals between components. |
Power and Ground Layer | PCB inner layers dedicated to providing stable power and ground connections. |
Via | A conductive hole drilled through the PCB and plated with copper to connect different layers. |
Prepreg | Pre-impregnated material used as insulating layers in PCB lamination. |
Impedance Control | Designing traces to maintain a specific impedance for high-speed signals. |
Decoupling Capacitor | A capacitor placed close to power pins to minimize power supply noise. |
Thermal Via | A via used to transfer heat from inner layers to outer layers or a heatsink. |
By understanding the concepts, manufacturing process, and design considerations of PCB inner layers, engineers and designers can create robust and reliable electronic products that push the boundaries of innovation.
0 Comments