What is a PCB Via?
Before diving into Through-hole vias specifically, let’s first understand what a PCB via is. A via is a small hole drilled through a PCB to create an electrical connection between different layers of the board. Vias can be used to route signals, power, or ground planes from one layer to another, enabling more complex circuit designs and efficient use of board space.
Types of PCB Vias
There are several types of vias used in PCB design, each with its own characteristics and applications:
- Through-hole vias
- Blind vias
- Buried vias
- Micro vias
- Via-in-pad
In this article, we will focus on through-hole vias.
What is a Through Hole Via?
A through-hole via is a type of via that goes through all layers of a PCB, from the top layer to the bottom layer. The hole is drilled through the entire board and then plated with a conductive material, typically copper, to create an electrical connection between the layers.
Structure of a Through Hole Via
A through-hole via consists of the following components:
- Drilled hole: A hole is drilled through all layers of the PCB using a drill bit of a specific diameter.
- Plating: The drilled hole is plated with a conductive material, usually copper, to create an electrical connection between the layers.
- Annular ring: The annular ring is the copper pad surrounding the via hole on the top and bottom layers of the PCB. It ensures a reliable connection between the via and the copper traces on the board.
- Solder mask: A solder mask is applied to the PCB, covering the annular ring and the surrounding area, leaving only the via hole exposed.
Manufacturing Process of Through Hole Vias
The manufacturing process of through-hole vias involves several steps:
- Drilling: Holes are drilled through all layers of the PCB using a drill bit of the appropriate diameter.
- Deburring: The drilled holes are deburred to remove any rough edges or debris.
- Cleaning: The board is cleaned to remove any contaminants or drilling residue.
- Plating: The drilled holes are plated with a conductive material, typically copper, using an electroplating process.
- Solder mask application: A solder mask is applied to the board, covering the annular ring and surrounding area, leaving only the via hole exposed.
Advantages of Through Hole Vias
Through-hole vias offer several advantages in PCB design:
- Strength: Through-hole vias provide mechanical strength to the PCB, as they go through all layers of the board.
- Reliability: The plated hole creates a reliable electrical connection between the layers, reducing the risk of signal integrity issues.
- Ease of assembly: Through-hole vias are compatible with through-hole components, making the assembly process easier and more reliable.
- Heat dissipation: Through-hole vias can be used as thermal vias to dissipate heat from components on the board.
Disadvantages of Through Hole Vias
Despite their advantages, through-hole vias also have some disadvantages:
- Board space: Through-hole vias require more board space compared to other types of vias, as they go through all layers of the PCB.
- Routing limitations: The presence of through-hole vias can limit the routing options on inner layers of the board, as they occupy space on all layers.
- High-speed design challenges: Through-hole vias can introduce signal integrity issues in high-speed designs due to their longer signal paths and potential for impedance mismatches.
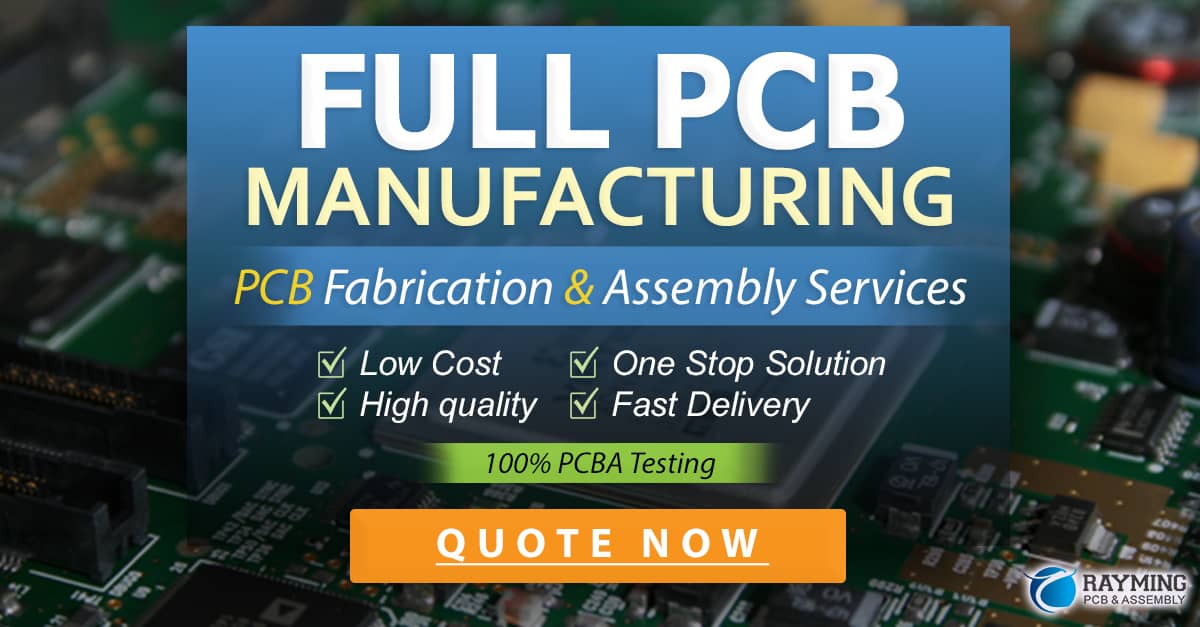
Applications of Through Hole Vias
Through-hole vias are widely used in various PCB applications, such as:
- Single-layer and double-layer boards: Through-hole vias are the primary means of interconnecting layers in simple PCB designs.
- Multilayer boards: Although blind and buried vias are more common in complex multilayer boards, through-hole vias are still used for certain connections, such as power and ground planes.
- Through-hole component mounting: Through-hole vias are used to mount through-hole components on the board, providing mechanical stability and electrical connectivity.
- Thermal management: Through-hole vias can be used as thermal vias to dissipate heat from components, improving the overall thermal performance of the PCB.
Through Hole Via Design Considerations
When designing through-hole vias, several factors must be considered to ensure optimal performance and manufacturability:
- Via diameter: The diameter of the via hole should be chosen based on the current carrying requirements, the thickness of the PCB, and the manufacturing capabilities of the PCB fabricator.
- Annular ring size: The annular ring should be large enough to provide a reliable connection between the via and the copper traces on the board, while also considering the manufacturing tolerances.
- Via-to-via spacing: The spacing between vias should be sufficient to prevent signal integrity issues and ensure manufacturability.
- Via-to-trace spacing: The spacing between vias and copper traces should be adequate to prevent short circuits and maintain signal integrity.
- Via filling: In some cases, through-hole vias may be filled with a non-conductive material to improve mechanical strength and prevent solder wicking during the assembly process.
Through Hole Via Manufacturing Challenges
Manufacturing through-hole vias can present some challenges, such as:
- Drilling accuracy: Ensuring the drilled holes are precisely located and have the correct diameter is crucial for proper via formation and connectivity.
- Plating uniformity: Achieving uniform plating thickness throughout the via hole is essential for reliable electrical connections and signal integrity.
- Solder mask application: Ensuring the solder mask is properly applied around the via hole is important to prevent solder bridging and short circuits during the assembly process.
Frequently Asked Questions (FAQs)
- What is the difference between a through-hole via and a blind via?
-
A through-hole via goes through all layers of the PCB, while a blind via starts on an outer layer and ends on an inner layer, without going through the entire board.
-
Can through-hole vias be used in high-speed PCB designs?
-
While through-hole vias can be used in high-speed designs, they may introduce signal integrity issues due to their longer signal paths and potential for impedance mismatches. In such cases, blind or buried vias may be preferred.
-
How are through-hole vias manufactured?
-
Through-hole vias are manufactured by drilling holes through all layers of the PCB, deburring and cleaning the holes, plating them with a conductive material (usually copper), and applying a solder mask around the via hole.
-
What are thermal vias, and how do they relate to through-hole vias?
-
Thermal vias are through-hole vias that are used to dissipate heat from components on the PCB. They provide a low-resistance thermal path from the component to the PCB’s copper layers, helping to improve the overall thermal performance of the board.
-
What factors should be considered when designing through-hole vias?
- When designing through-hole vias, factors such as via diameter, annular ring size, via-to-via spacing, via-to-trace spacing, and via filling should be considered to ensure optimal performance and manufacturability.
Conclusion
Through-hole vias are essential components in PCB design, providing a reliable means of interconnecting different layers of a board. By understanding the basics of through-hole vias, their manufacturing process, advantages, disadvantages, and design considerations, PCB designers can create more efficient and reliable circuit boards. While through-hole vias may have some limitations in high-speed designs and complex multilayer boards, they remain an important tool in the PCB designer’s arsenal, offering strength, reliability, and compatibility with through-hole components.
Via Type | Description | Advantages | Disadvantages |
---|---|---|---|
Through-hole via | Goes through all layers of the PCB | Strength, reliability, ease of assembly, heat dissipation | Board space, routing limitations, high-speed design challenges |
Blind via | Starts on an outer layer and ends on an inner layer | Saves board space, improves routing flexibility | Higher cost, manufacturing complexity |
Buried via | Connects inner layers without reaching the outer layers | Saves board space, improves routing flexibility | Higher cost, manufacturing complexity |
Micro via | Small-diameter via used in high-density designs | Saves board space, enables high-density routing | Higher cost, manufacturing complexity |
Via-in-pad | Via is located within a component pad | Saves board space, improves routing flexibility | Solder wicking, manufacturing complexity |
As PCB designs continue to evolve and become more complex, the choice of via type and the optimization of via design will remain critical factors in creating high-performance, reliable, and cost-effective circuit boards. By staying up-to-date with the latest via technologies and design best practices, PCB designers can overcome the challenges posed by modern electronics and deliver innovative solutions to meet the ever-growing demands of the industry.
0 Comments