What is Soldermask Made Of?
Soldermask is typically made of a photosensitive polymer that is applied to the PCB surface in liquid form. The most common types of soldermask are:
-
Liquid Photoimageable Soldermask (LPISM): This is the most widely used type of soldermask. It is applied as a liquid and then exposed to UV light through a photomask, which hardens the exposed areas.
-
Dry Film Soldermask (DFSM): This type of soldermask comes in the form of a dry film that is laminated onto the PCB surface. It is then exposed to UV light and developed, similar to LPISM.
-
Epoxy Liquid Soldermask: This soldermask is a two-part epoxy that is screen printed onto the PCB surface and then cured with heat.
Properties of Soldermask
Soldermask must have several key properties to effectively protect the PCB and facilitate the soldering process:
- High electrical insulation resistance
- Good adhesion to the PCB surface
- Resistance to chemicals and solvents used in the PCB manufacturing process
- Ability to withstand high temperatures during soldering
- Excellent coverage and uniformity
- Compatibility with various surface finishes (e.g., HASL, ENIG, OSP)
Soldermask Application Process
The soldermask application process typically involves the following steps:
-
PCB Cleaning: The PCB surface is thoroughly cleaned to remove any contaminants that could affect soldermask adhesion.
-
Soldermask Application: The soldermask is applied to the PCB surface using either screen printing (for liquid soldermask) or lamination (for dry film soldermask).
-
Exposure: The soldermask-coated PCB is exposed to UV light through a photomask, which hardens the exposed areas.
-
Development: The unexposed areas of the soldermask are removed using a developer solution, leaving only the hardened soldermask on the PCB surface.
-
Curing: The PCB is heated to fully cure the soldermask and improve its adhesion and durability.
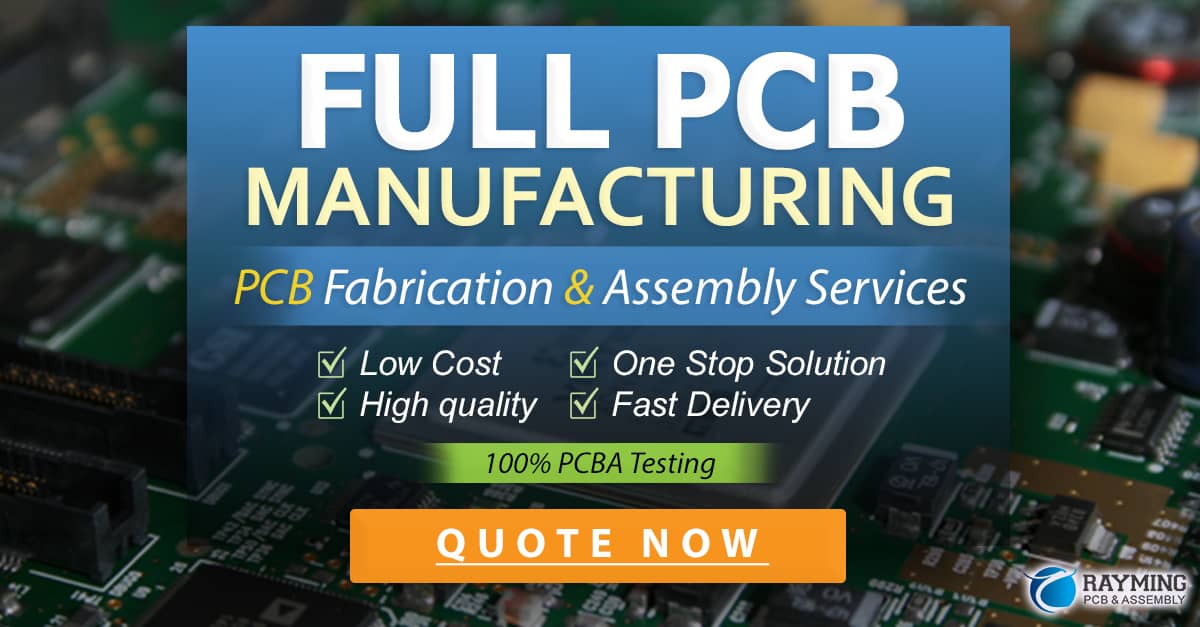
Soldermask Colors
Soldermask is available in a variety of colors, with green being the most common. Other popular colors include:
- Blue
- Red
- Yellow
- Black
- White
The choice of soldermask color is often based on aesthetic preferences, but it can also serve functional purposes. For example, white soldermask is sometimes used to improve the visibility of the silkscreen legend, while black soldermask can help with heat dissipation.
Silkscreen Legend
The silkscreen legend is the text and symbols printed on top of the soldermask to provide information about the PCB, such as component designators, polarity markers, and company logos. The silkscreen is typically applied using a screen printing process and is usually white in color, although other colors can be used for specific applications.
Soldermask and Surface Finishes
Soldermask is compatible with various surface finishes used on PCBs, such as:
-
Hot Air Solder Leveling (HASL): A tin-lead alloy is applied to the exposed copper areas and then leveled using hot air.
-
Electroless Nickel Immersion Gold (ENIG): A layer of nickel is deposited on the exposed copper, followed by a thin layer of gold.
-
Organic Solderability Preservative (OSP): A thin, organic coating is applied to the exposed copper to prevent oxidation.
The choice of surface finish depends on factors such as the intended application, soldering process, and environmental requirements.
Soldermask Design Considerations
When designing a PCB with soldermask, several factors must be considered:
-
Soldermask Clearance: The soldermask opening around pads and vias must be large enough to allow for proper soldering. The clearance is typically 0.05-0.1 mm larger than the pad or via diameter.
-
Soldermask Sliver: This refers to the minimum width of soldermask between two adjacent pads or traces. A minimum sliver width of 0.1-0.15 mm is recommended to ensure adequate insulation and prevent bridging.
-
Soldermask Registration: The alignment between the soldermask and the underlying copper features must be accurate to ensure proper coverage and prevent exposing unintended areas.
-
Soldermask Thickness: The typical thickness of soldermask ranges from 0.01 to 0.03 mm. Thicker soldermask provides better insulation and durability but can affect the PCB’s dimensional tolerances.
Advantages of Using Soldermask
Using soldermask on PCBs offers several advantages:
-
Protection: Soldermask protects the copper traces and pads from oxidation, scratches, and other damage during handling and assembly.
-
Insulation: The high electrical insulation resistance of soldermask prevents short circuits between adjacent traces and pads.
-
Solderability: Soldermask improves the solderability of the exposed pads by preventing solder from flowing onto unintended areas.
-
Aesthetics: Colored soldermask enhances the visual appearance of the PCB and can help with branding and identification.
-
Durability: Soldermask increases the overall durability of the PCB by protecting the copper from environmental factors such as moisture and chemicals.
Disadvantages of Using Soldermask
While soldermask offers many benefits, there are also some potential disadvantages to consider:
-
Cost: Applying soldermask adds an extra step to the PCB manufacturing process, which can increase production costs.
-
Design Complexity: Incorporating soldermask into the PCB design can add complexity, especially when considering factors such as clearances and registration.
-
Thermal Management: Soldermask can affect the PCB’s thermal management by insulating the copper traces and pads, which can lead to higher operating temperatures in some cases.
-
Rework Challenges: Removing soldermask for rework or repair can be difficult and may damage the underlying copper features.
Soldermask and High-Frequency PCBs
In high-frequency PCB designs, soldermask can have a significant impact on the board’s electrical performance. The dielectric constant (Dk) and dissipation factor (Df) of the soldermask material can affect the impedance and signal integrity of the PCB.
To minimize the impact of soldermask on high-frequency performance, designers can:
- Use low-loss soldermask materials with a stable Dk and low Df.
- Minimize the soldermask thickness to reduce its effect on impedance.
- Use soldermask relief around critical traces and pads to maintain consistent impedance.
Soldermask and Flexible PCBs
Flexible PCBs require special considerations when it comes to soldermask. The soldermask used on flexible PCBs must be able to withstand repeated bending and flexing without cracking or delaminating.
Polyimide-based soldermasks are commonly used for flexible PCBs due to their excellent mechanical properties and flexibility. These soldermasks are applied in thin layers (typically 0.005-0.01 mm) to minimize the impact on the PCB’s flexibility.
Soldermask and Environmental Regulations
Soldermask materials must comply with various environmental regulations, such as the Restriction of Hazardous Substances (RoHS) directive and the Registration, Evaluation, Authorization, and Restriction of Chemicals (REACH) regulation.
RoHS-compliant soldermasks are free from restricted substances such as lead, cadmium, and mercury. REACH-compliant soldermasks do not contain substances of very high concern (SVHC) above the specified threshold.
PCB Manufacturers and designers must ensure that the soldermask materials used in their products meet these environmental regulations to avoid non-compliance issues and potential legal consequences.
Frequently Asked Questions (FAQ)
-
Q: What is the primary purpose of soldermask on a PCB?
A: The primary purpose of soldermask is to protect the copper traces and pads from oxidation, prevent short circuits, and provide a surface for applying the silkscreen legend. -
Q: What are the most common types of soldermask?
A: The most common types of soldermask are Liquid Photoimageable Soldermask (LPISM), Dry Film Soldermask (DFSM), and Epoxy Liquid Soldermask. -
Q: What is the typical thickness of soldermask on a PCB?
A: The typical thickness of soldermask ranges from 0.01 to 0.03 mm, with thicker soldermask providing better insulation and durability but potentially affecting the PCB’s dimensional tolerances. -
Q: Can soldermask affect the electrical performance of high-frequency PCBs?
A: Yes, the dielectric constant (Dk) and dissipation factor (Df) of the soldermask material can affect the impedance and signal integrity of high-frequency PCBs. -
Q: Are there any special considerations for soldermask on flexible PCBs?
A: Yes, the soldermask used on flexible PCBs must be able to withstand repeated bending and flexing without cracking or delaminating. Polyimide-based soldermasks are commonly used for this application due to their excellent mechanical properties and flexibility.
In conclusion, soldermask is an essential component of modern PCBs, providing protection, insulation, and improved solderability. Understanding the properties, application process, design considerations, and environmental regulations related to soldermask is crucial for PCB designers and manufacturers to ensure the production of high-quality, reliable, and compliant PCBs.
0 Comments