Introduction to PCB Manufacturing
Printed Circuit Boards (PCBs) are the backbone of modern electronics. These essential components are found in almost every electronic device, from smartphones and computers to medical equipment and aerospace systems. PCBs provide a stable platform for electronic components to be mounted and interconnected, enabling the efficient transmission of electrical signals. Among the various types of PCBs, rigid PCBs are the most common and widely used in the electronics industry.
Rigid PCBs are manufactured using a substrate material that is inflexible and maintains its shape under normal operating conditions. This rigidity ensures the stability and durability of the electronic circuits, making them suitable for a wide range of applications. The manufacturing process of rigid PCBs involves several critical steps, each requiring precision and expertise to ensure the highest quality standards are met.
In this comprehensive article, we will explore the world of rigid PCB manufacturing, delving into the various aspects of the process, from design and material selection to fabrication techniques and quality control measures. We will also discuss the key factors to consider when choosing a PCB manufacturer and highlight some of the leading rigid PCB Manufacturers and fabricators in the industry.
The Importance of Choosing the Right PCB Manufacturer
Selecting the right PCB manufacturer is a critical decision that can significantly impact the success of your electronic product. A reliable and experienced PCB manufacturer can ensure that your PCBs are designed and fabricated to the highest quality standards, meeting your specific requirements and industry regulations. On the other hand, choosing an unreliable or inexperienced manufacturer can lead to costly delays, subpar quality, and even product failures.
When evaluating potential PCB manufacturers, consider the following key factors:
-
Experience and Expertise: Look for a manufacturer with a proven track record in the industry, with experience in manufacturing PCBs for applications similar to yours. They should have a deep understanding of the latest technologies, materials, and fabrication techniques.
-
Quality Standards: Ensure that the manufacturer adheres to strict quality control measures and industry standards, such as IPC (Association Connecting Electronics Industries) and ISO (International Organization for Standardization) certifications. These certifications demonstrate the manufacturer’s commitment to quality and reliability.
-
Production Capabilities: Assess the manufacturer’s production capabilities, including their equipment, facilities, and capacity to handle your specific requirements. They should be able to accommodate your production volume, lead times, and any special requirements you may have.
-
Customer Support: Choose a manufacturer that offers excellent customer support, with responsive communication and a dedicated team to address your concerns and questions throughout the manufacturing process.
-
Cost and Value: While cost is an important consideration, it should not be the sole deciding factor. Look for a manufacturer that offers competitive pricing without compromising on quality and service. Consider the long-term value of partnering with a reliable manufacturer, as it can save you time, money, and headaches in the long run.
By carefully evaluating these factors and conducting thorough research, you can select a PCB manufacturer that aligns with your needs and ensures the success of your electronic product.
The Rigid PCB Manufacturing Process
The manufacturing process of rigid PCBs involves several critical steps, each requiring precision and expertise to ensure the highest quality standards are met. Let’s take a closer look at the key stages of the rigid PCB manufacturing process.
1. PCB Design and Layout
The first step in the rigid PCB manufacturing process is the design and layout of the PCB. This involves creating a detailed schematic of the electronic circuit, specifying the components, their placement, and the interconnections between them. The design is then translated into a physical layout, taking into account factors such as signal integrity, power distribution, and thermal management.
PCB design software, such as Altium Designer, Eagle, or KiCad, is used to create the schematic and layout files. These files are then sent to the PCB manufacturer for fabrication.
2. Material Selection
The choice of substrate material is critical in rigid PCB manufacturing, as it determines the PCB’s electrical, thermal, and mechanical properties. The most common substrate materials used in rigid PCBs are:
- FR-4: A glass-reinforced epoxy laminate, FR-4 is the most widely used substrate material for rigid PCBs. It offers good electrical insulation, mechanical strength, and thermal stability.
- High-Tg FR-4: A variant of FR-4 with improved thermal properties, High-Tg FR-4 is suitable for applications that require higher operating temperatures.
- Polyimide: A high-performance substrate material, polyimide offers excellent thermal stability, chemical resistance, and mechanical strength. It is often used in aerospace, military, and high-reliability applications.
- Aluminum: Aluminum substrates are used in applications that require high thermal conductivity, such as LED lighting and power electronics.
The choice of substrate material depends on the specific requirements of the application, such as the operating environment, temperature range, and electrical performance.
3. Copper Clad Lamination
Once the substrate material is selected, it is laminated with a thin layer of copper on one or both sides, depending on the design requirements. The copper layer serves as the conductive pathway for the electronic circuits.
The lamination process involves placing the substrate material and copper foil in a press, where they are subjected to high temperature and pressure. This bonds the copper foil to the substrate, creating a copper-clad laminate.
4. Drilling
After the copper-clad laminate is formed, holes are drilled through the board to accommodate through-hole components and to create vias for interconnecting different layers of the PCB. The drilling process is typically performed using computer-controlled drill machines, which ensure precise hole placement and size.
5. Copper Patterning
The next step in the rigid PCB manufacturing process is to create the desired copper pattern on the board. This is achieved through a process called photolithography, which involves the following steps:
- The copper-clad laminate is cleaned and coated with a light-sensitive photoresist material.
- The PCB layout artwork is used to create a photomask, which is placed on top of the photoresist-coated laminate.
- The laminate is exposed to UV light through the photomask, hardening the exposed areas of the photoresist.
- The unexposed areas of the photoresist are removed using a developer solution, revealing the copper layer beneath.
- The exposed copper is etched away using a chemical etching process, leaving behind the desired copper pattern.
6. Soldermask Application
A soldermask is a protective layer applied to the PCB to prevent accidental short circuits and to protect the copper traces from oxidation and damage. The soldermask is typically applied using a screen printing process, where a thin layer of the soldermask material is deposited onto the PCB and then cured using UV light.
Soldermasks are available in various colors, with green being the most common. Other colors, such as red, blue, and black, are also used for specific applications or for aesthetic purposes.
7. Silkscreen Printing
Silkscreen printing is used to add text, logos, and other markings to the PCB. This is typically done using a screen printing process, where ink is applied to the PCB through a fine mesh screen. The ink is then cured using UV light or heat.
Silkscreen markings are important for identifying components, providing assembly instructions, and adding branding or other information to the PCB.
8. Surface Finish
The final step in the rigid PCB manufacturing process is to apply a surface finish to the exposed copper areas of the PCB. The surface finish serves several purposes, including:
- Protecting the copper from oxidation and corrosion
- Enhancing the solderability of the copper pads
- Improving the electrical conductivity and reliability of the connections
Some common surface finishes used in rigid PCBs are:
- Hot Air Solder Leveling (HASL): A tin-lead alloy is applied to the copper pads and then leveled using hot air.
- Electroless Nickel Immersion Gold (ENIG): A layer of nickel is deposited onto the copper, followed by a thin layer of gold. ENIG provides excellent solderability and durability.
- Immersion Silver: A thin layer of silver is deposited onto the copper, providing good solderability and a lower cost alternative to ENIG.
- Immersion Tin: A thin layer of tin is deposited onto the copper, offering good solderability and a cost-effective option for less demanding applications.
The choice of surface finish depends on the specific requirements of the application, such as the soldering process, operating environment, and shelf life.
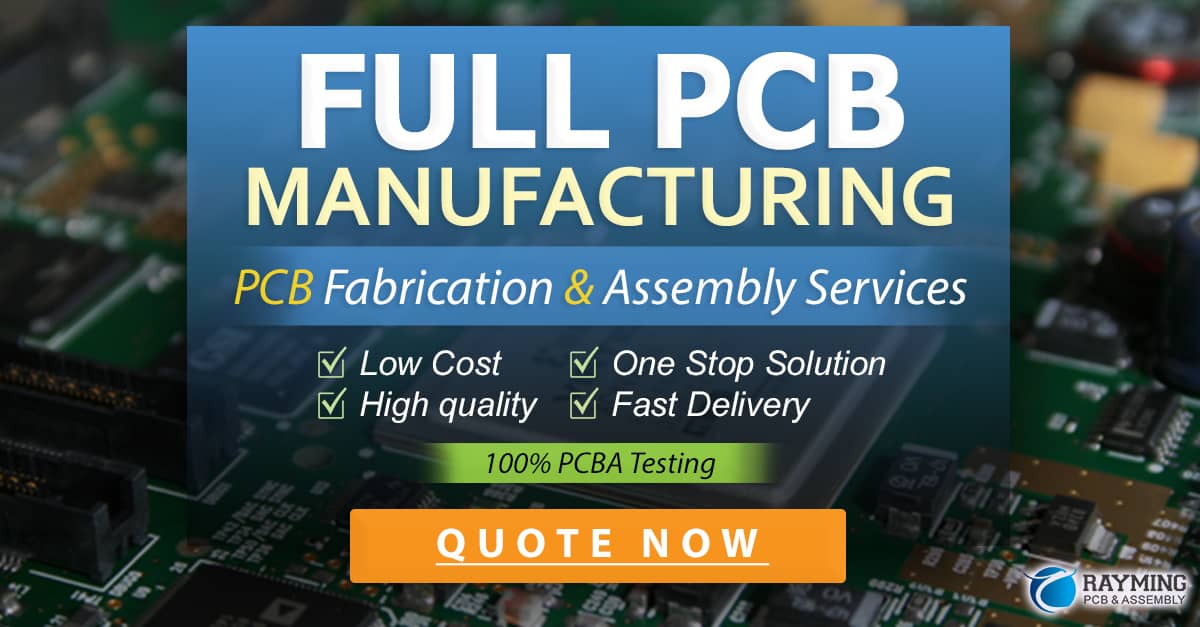
Quality Control in Rigid PCB Manufacturing
Ensuring the highest quality standards is critical in rigid PCB manufacturing, as even minor defects or inconsistencies can lead to product failures and costly recalls. PCB manufacturers employ various quality control measures throughout the manufacturing process to identify and address any issues before the PCBs are shipped to the customer.
Some of the key quality control techniques used in rigid PCB manufacturing include:
-
Automated Optical Inspection (AOI): AOI systems use high-resolution cameras and advanced image processing algorithms to inspect the PCBs for defects such as missing components, incorrect component placement, and solder bridging. AOI is typically performed after the soldering process and can quickly identify defects that may be difficult to detect with manual inspection.
-
X-ray Inspection: X-ray inspection is used to detect defects in hidden or obscured areas of the PCB, such as vias, ball grid arrays (BGAs), and flip-chip devices. X-ray systems can identify issues such as voids, cracks, and insufficient solder coverage.
-
Electrical Testing: Electrical testing is performed to ensure that the PCB functions as intended and meets the specified electrical requirements. This can include continuity testing, insulation resistance testing, and functional testing.
-
Visual Inspection: Manual visual inspection is still an important part of the quality control process, particularly for identifying cosmetic defects and ensuring conformance to customer specifications.
-
Statistical Process Control (SPC): SPC is a data-driven approach to quality control that involves monitoring key process parameters and using statistical methods to identify and correct any deviations from the desired values. This helps to ensure consistent quality throughout the manufacturing process.
By implementing these quality control measures, PCB manufacturers can deliver high-quality rigid PCBs that meet the demanding requirements of today’s electronic products.
Leading Rigid PCB Manufacturers and Fabricators
There are numerous rigid PCB manufacturers and fabricators worldwide, each with their own strengths and specialties. Some of the leading companies in the industry include:
-
Compeq Manufacturing Co., Ltd.: Based in Taiwan, Compeq is a global leader in PCB manufacturing, offering a wide range of rigid, flexible, and rigid-flex PCBs for various industries, including automotive, telecommunications, and consumer electronics.
-
Ibiden Co., Ltd.: A Japanese company, Ibiden is known for its high-quality rigid PCBs, particularly for high-end applications such as servers, 5G infrastructure, and automotive electronics.
-
Tripod Technology Corporation: Another Taiwanese manufacturer, Tripod Technology specializes in multi-layer rigid PCBs for applications such as networking, industrial control, and medical devices.
-
TTM Technologies, Inc.: TTM is a leading US-based PCB manufacturer, with a strong presence in the aerospace, defense, and automotive industries. They offer a wide range of PCB technologies, including rigid, flexible, and RF PCBs.
-
WUS Printed Circuit Co., Ltd.: WUS is a Chinese PCB manufacturer that has been rapidly expanding its global presence. They offer a diverse range of rigid PCB solutions, including high-density interconnect (HDI) and thick copper PCBs.
These are just a few examples of the many capable rigid PCB manufacturers and fabricators in the industry. When selecting a PCB manufacturer, it’s essential to carefully evaluate their capabilities, experience, and quality standards to ensure they can meet your specific requirements.
Frequently Asked Questions (FAQ)
-
What is the difference between a rigid PCB and a flexible PCB?
A rigid PCB is made from a solid, inflexible substrate material, typically FR-4, which maintains its shape under normal operating conditions. On the other hand, a flexible PCB is made from a thin, flexible substrate material, such as polyimide, which allows the PCB to bend and flex without damaging the circuits. -
What are the advantages of using a rigid PCB?
Rigid PCBs offer several advantages, including: - High mechanical strength and durability
- Excellent thermal stability
- Good electrical insulation properties
- Ability to support high-density component placement
-
Lower cost compared to flexible PCBs for most applications
-
What is the typical turnaround time for rigid PCB manufacturing?
The turnaround time for rigid PCB manufacturing varies depending on the complexity of the design, the manufacturing process, and the PCB manufacturer’s capacity. Generally, simple PCBs can be manufactured within 1-2 weeks, while more complex designs may take 3-4 weeks or longer. -
How do I choose the right surface finish for my rigid PCB?
The choice of surface finish depends on several factors, including the soldering process, operating environment, and shelf life requirements. HASL is a common and cost-effective option for general-purpose applications, while ENIG and immersion silver offer better solderability and durability for more demanding applications. -
What certifications should I look for when selecting a rigid PCB manufacturer?
When choosing a rigid PCB manufacturer, look for certifications that demonstrate their commitment to quality and reliability, such as: - ISO 9001: Quality management systems
- IPC-A-600: Acceptability of printed boards
- IPC-6012: Qualification and performance specification for rigid printed boards
- UL (Underwriters Laboratories) certification for safety and reliability
Conclusion
Rigid PCBs are the backbone of modern electronics, providing a stable and reliable platform for electronic components to be mounted and interconnected. The manufacturing process of rigid PCBs involves several critical steps, each requiring precision and expertise to ensure the highest quality standards are met.
Choosing the right PCB manufacturer is crucial for the success of your electronic product. By carefully evaluating factors such as experience, quality standards, production capabilities, and customer support, you can select a manufacturer that aligns with your needs and ensures the timely delivery of high-quality PCBs.
As the electronics industry continues to evolve, with ever-increasing demands for performance, reliability, and miniaturization, rigid PCB manufacturers and fabricators will play an increasingly important role in enabling the next generation of electronic products. By staying at the forefront of technology and continuously improving their processes and capabilities, these companies will continue to drive innovation and support the growth of the global electronics industry.
0 Comments