Why is PCB trace width Clearance Important?
Preventing Short Circuits
One of the primary reasons for maintaining adequate PCB trace width clearance is to prevent short circuits. When traces are placed too close to each other or other conductive features, there is a risk of unintended electrical connections. These short circuits can cause the PCB to malfunction or even damage the components on the board. By ensuring sufficient clearance between traces, designers can minimize the chances of short circuits occurring.
Signal Integrity
Trace width clearance also plays a significant role in maintaining signal integrity on a PCB. When traces are placed too close together, they can experience crosstalk, which is the unwanted coupling of signals between adjacent traces. Crosstalk can lead to signal distortion, noise, and other issues that can compromise the performance of the PCB. By providing adequate spacing between traces, designers can reduce the impact of crosstalk and ensure that signals remain clean and reliable.
Manufacturing Considerations
Another important reason for maintaining proper PCB trace width clearance is to ensure manufacturability. PCB fabrication processes have certain limitations in terms of the minimum feature sizes they can produce. If traces are placed too close together or too close to other features, it can be difficult or impossible to manufacture the board reliably. This can lead to increased production costs, lower yields, and longer lead times. By adhering to the minimum clearance requirements specified by the PCB manufacturer, designers can ensure that their boards can be produced efficiently and with high quality.
Factors Affecting PCB Trace Width Clearance
Several factors influence the determination of appropriate PCB trace width clearance. These include:
Signal Characteristics
The characteristics of the signals traveling through the traces have a significant impact on the required clearance. High-speed signals, such as those found in digital circuits, require greater clearance to minimize crosstalk and maintain signal integrity. On the other hand, low-speed signals or power traces may not require as much clearance. The frequency, rise time, and voltage level of the signals must be considered when determining the appropriate clearance.
Board Layer and Material
The layer on which the traces are located and the material of the PCB also affect the required clearance. Inner layers of a multi-layer PCB typically have tighter clearance requirements compared to the outer layers. This is because the inner layers are sandwiched between other layers, which provides additional insulation and reduces the risk of short circuits. The dielectric constant and thickness of the PCB material also influence the clearance requirements. Higher dielectric constant materials and thinner boards generally require greater clearance to maintain signal integrity.
Manufacturing Process
The manufacturing process used to fabricate the PCB also plays a role in determining the trace width clearance. Different PCB manufacturers may have varying capabilities and limitations in terms of the minimum feature sizes they can produce. Some advanced manufacturing processes, such as high-density interconnect (HDI) or micro-via technology, allow for tighter clearances compared to standard processes. It is essential to consult with the PCB manufacturer and adhere to their specific design guidelines to ensure manufacturability.
Electrical Requirements
The electrical requirements of the circuit also impact the trace width clearance. For example, high-voltage circuits may require greater clearance to prevent arcing or breakdown of the insulation between traces. Similarly, circuits with high current requirements may need wider traces and greater clearance to handle the increased current flow without overheating or causing voltage drops.
Determining Appropriate PCB Trace Width Clearance
To determine the appropriate PCB trace width clearance for a given design, designers typically refer to industry standards and guidelines. Two commonly used standards are the IPC-2221 and the IPC-2152.
IPC-2221 Standard
The IPC-2221 standard, titled “Generic Standard on Printed Board Design,” provides general guidelines for PCB design, including recommendations for trace width clearance. This standard offers a set of tables that specify the minimum clearance requirements based on the voltage level and the type of conductors involved (e.g., trace-to-trace, trace-to-pad, trace-to-via).
Voltage (V) | Trace-to-Trace (mm) | Trace-to-Pad (mm) | Trace-to-Via (mm) |
---|---|---|---|
0-50 | 0.13 | 0.20 | 0.20 |
51-100 | 0.25 | 0.30 | 0.30 |
101-150 | 0.40 | 0.50 | 0.50 |
151-250 | 0.60 | 0.80 | 0.80 |
The above table shows an example of the minimum clearance requirements specified in the IPC-2221 standard for different voltage levels and conductor types.
IPC-2152 Standard
The IPC-2152 standard, titled “Standard for Determining Current-Carrying Capacity in Printed Board Design,” focuses on the current-carrying capacity of PCB traces and provides guidelines for trace width and clearance based on the current requirements. This standard takes into account factors such as the thickness of the copper, the temperature rise, and the maximum allowable current density.
Current (A) | Trace Width (mm) | Clearance (mm) |
---|---|---|
0.5 | 0.25 | 0.20 |
1.0 | 0.50 | 0.30 |
2.0 | 1.00 | 0.50 |
3.0 | 1.50 | 0.80 |
The above table shows an example of the recommended trace width and clearance based on the current requirements, as specified in the IPC-2152 standard.
It is important to note that these standards provide general guidelines, and the actual clearance requirements may vary depending on the specific design, manufacturing process, and other factors. Designers should always consult with the PCB manufacturer and follow their specific design rules and guidelines to ensure the best results.
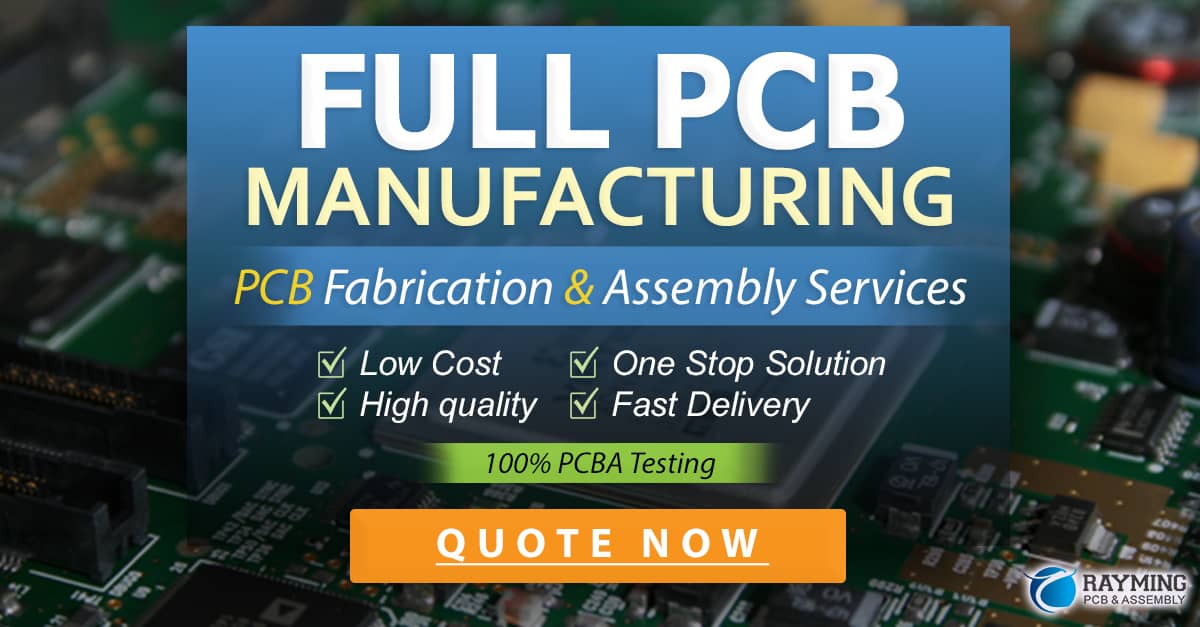
Best Practices for PCB Trace Width Clearance
To optimize PCB trace width clearance and ensure a reliable and manufacturable design, consider the following best practices:
- Understand the signal characteristics and electrical requirements of your circuit and select appropriate trace widths and clearances accordingly.
- Follow the guidelines provided by industry standards, such as IPC-2221 and IPC-2152, as a starting point for determining the minimum clearance requirements.
- Consult with your PCB manufacturer and adhere to their specific design rules and guidelines. Different manufacturers may have varying capabilities and limitations.
- Use PCB design software that includes design rule checking (DRC) features to automatically verify trace width clearance and other design rules.
- Consider using wider traces and greater clearances for critical signals or high-voltage/high-current circuits to ensure reliable operation.
- Keep high-speed signals away from each other and from other traces to minimize crosstalk and signal integrity issues.
- Use ground planes and proper grounding techniques to provide shielding and reduce the impact of crosstalk.
- Perform signal integrity simulations and analysis to verify the performance of your design and make necessary adjustments to trace width clearance and other parameters.
FAQ
-
What is the minimum trace width clearance required for a 50V signal?
According to the IPC-2221 standard, the minimum trace-to-trace clearance for a 50V signal is 0.13mm, while the minimum trace-to-pad and trace-to-via clearance is 0.20mm. -
Can I use tighter trace width clearances than the recommended values?
While it is possible to use tighter clearances, it is generally not recommended unless you have verified with your PCB manufacturer that they can reliably produce the design with the desired clearances. Using tighter clearances increases the risk of short circuits, signal integrity issues, and manufacturing defects. -
What happens if I don’t maintain proper PCB trace width clearance?
Failing to maintain proper PCB trace width clearance can lead to various problems, such as short circuits, signal integrity issues, crosstalk, and manufacturing defects. These issues can cause the PCB to malfunction, damage components, or fail to meet performance requirements. -
How do I determine the appropriate trace width clearance for my design?
To determine the appropriate trace width clearance for your design, consider factors such as the signal characteristics, electrical requirements, board layer and material, and manufacturing process. Refer to industry standards like IPC-2221 and IPC-2152 as a starting point, and consult with your PCB manufacturer for their specific design guidelines. -
Can I use different trace width clearances on different layers of the PCB?
Yes, it is common to use different trace width clearances on different layers of a multi-layer PCB. Inner layers typically have tighter clearance requirements compared to outer layers due to the additional insulation provided by the surrounding layers. However, it is important to ensure that the clearances on all layers meet the minimum requirements specified by the PCB manufacturer and industry standards.
Conclusion
PCB trace width clearance is a critical aspect of PCB design that ensures the proper functioning, reliability, and manufacturability of the board. Maintaining appropriate clearance between traces and other features on the PCB helps prevent short circuits, signal integrity issues, and manufacturing defects. Designers must consider various factors such as signal characteristics, electrical requirements, board layer and material, and manufacturing process when determining the appropriate trace width clearance.
By following industry standards, such as IPC-2221 and IPC-2152, and consulting with PCB manufacturers, designers can establish the minimum clearance requirements for their specific design. Adhering to best practices, such as using appropriate trace widths, following design rules, and performing signal integrity analysis, can further optimize the design and ensure a successful PCB implementation.
As PCB technology continues to advance, with higher frequencies, smaller feature sizes, and more complex designs, understanding and properly implementing PCB trace width clearance becomes increasingly important. By staying informed about the latest guidelines, standards, and best practices, PCB designers can create reliable, high-performance boards that meet the ever-growing demands of modern electronics.
0 Comments