Key Aspects of PCB Design
Component Selection
Choosing the right components is crucial for the success of a PCB design. Factors to consider when selecting components include:
- Functionality: Ensure the chosen components fulfill the required functions of the circuit.
- Compatibility: Verify that the components are compatible with each other and the PCB manufacturing process.
- Availability: Select components that are readily available and have a reliable supply chain.
- Cost: Balance the cost of components with the overall budget of the project.
Schematic Design
A schematic diagram is a graphical representation of the electrical connections between components in a circuit. When creating a schematic, consider the following:
- Use standard symbols to represent components.
- Clearly label components and their values.
- Organize the schematic logically, grouping related components together.
- Verify the correctness of the connections and the overall circuit functionality.
PCB Layout
PCB layout involves physically arranging the components on the board and routing the electrical connections between them. Key aspects of PCB layout include:
Component Placement
- Place components in a logical order, considering signal flow and minimizing the distance between connected components.
- Ensure proper spacing between components to allow for manufacturing tolerances and to avoid interference.
- Consider the mechanical constraints of the enclosure and the placement of connectors and mounting holes.
Routing
- Use appropriate trace widths based on the current carrying requirements and the PCB manufacturing capabilities.
- Minimize the length of traces to reduce signal loss and interference.
- Avoid sharp angles and use smooth curves for traces to improve signal integrity.
- Properly route power and ground traces to provide a low-impedance path and minimize voltage drops.
PCB Stackup
The PCB stackup refers to the arrangement of copper layers and insulating materials in a multi-layer PCB.
Layer | Description |
---|---|
Top Layer | Components and routing |
Ground Plane | Provides a low-impedance ground reference |
Signal Layers | Internal layers for routing signals |
Power Plane | Distributes power to components |
Bottom Layer | Components and routing (for double-sided PCBs) |
Proper stackup design helps ensure signal integrity, power delivery, and EMI/EMC performance.
PCB Design Software
PCB design software tools assist in creating schematics, component libraries, and PCB layouts. Popular PCB design software includes:
- Altium Designer
- KiCad
- Eagle
- OrCAD
- Mentor Graphics PADS
These tools provide features such as schematic capture, component library management, PCB layout editors, design rule checking (DRC), and output file generation for manufacturing.
PCB Manufacturing
Once the PCB design is complete, the files are sent to a PCB manufacturer for fabrication. The manufacturing process involves several steps:
- PCB Fabrication: The copper layers are etched, drilled, and laminated based on the provided design files.
- Solder Mask Application: A protective coating is applied to the PCB to insulate the copper traces and prevent short circuits.
- Silkscreen Printing: Text and symbols are printed on the PCB for component identification and assembly instructions.
- Surface Finish: A protective finish, such as HASL (Hot Air Solder Leveling) or ENIG (Electroless Nickel Immersion Gold), is applied to the exposed copper pads to prevent oxidation and improve solderability.
- Electrical Testing: The manufactured PCBs undergo electrical testing to ensure they meet the specified requirements and are free from defects.
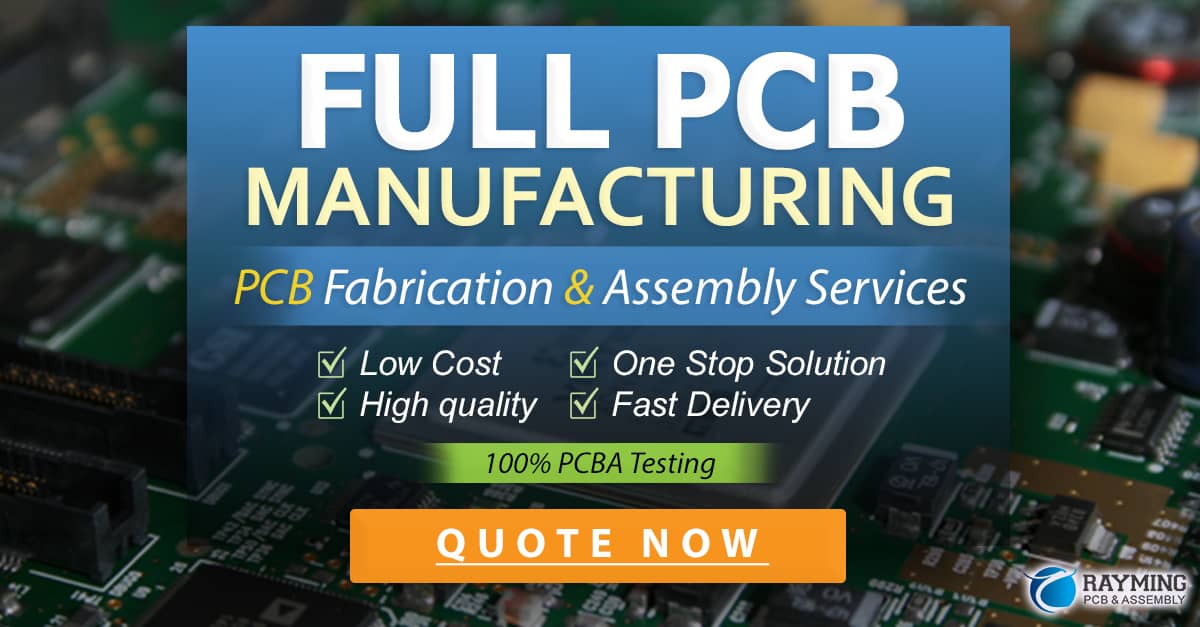
PCB Assembly
After the PCBs are manufactured, the components are assembled onto the board. PCB assembly can be done manually or using automated equipment, such as pick-and-place machines and reflow ovens.
The assembly process typically involves the following steps:
- Solder Paste Application: Solder paste is applied to the pads on the PCB where components will be placed.
- Component Placement: Components are placed on the PCB, either manually or using automated equipment.
- Reflow Soldering: The PCB is heated in a reflow oven, melting the solder paste and creating electrical connections between the components and the PCB.
- Inspection: The assembled PCBs are inspected for proper component placement, solder joint quality, and overall workmanship.
Design for Manufacturing (DFM)
Design for Manufacturing (DFM) is the practice of designing PCBs with consideration for the manufacturing process. DFM guidelines help ensure that the PCB can be manufactured reliably and cost-effectively. Some key DFM considerations include:
- Minimum trace width and spacing
- Minimum drill hole size
- Clearance between components and the board edge
- Solder mask and silkscreen guidelines
- Component placement and orientation
- Panelization for efficient manufacturing
By following DFM guidelines, designers can minimize manufacturing issues, improve yield, and reduce production costs.
Signal Integrity and EMI/EMC
Signal integrity and Electromagnetic Interference/Electromagnetic Compatibility (EMI/EMC) are critical aspects of PCB design.
Signal Integrity
Signal integrity refers to the quality of electrical signals transmitted through the PCB. Factors that can affect signal integrity include:
- Impedance matching: Ensuring that the characteristic impedance of the traces matches the impedance of the source and load.
- Crosstalk: Minimizing the coupling of signals between adjacent traces.
- Reflections: Avoiding reflections caused by impedance mismatches or unterminated traces.
Designers can use techniques such as controlled impedance routing, differential pair routing, and proper termination to maintain signal integrity.
EMI/EMC
EMI/EMC refers to the ability of the PCB to operate without causing or being affected by electromagnetic interference. To minimize EMI/EMC issues, designers can:
- Use proper grounding and shielding techniques.
- Separate sensitive analog and digital circuits.
- Use filters and suppressors on power lines and I/O connections.
- Follow regulatory guidelines for EMI/EMC compliance.
Thermal Management
Thermal management is the process of ensuring that the PCB and its components operate within their specified temperature ranges. Overheating can lead to component failure and reduced reliability.
Thermal management techniques include:
- Proper component placement to evenly distribute heat.
- Using thermal interface materials (TIMs) to improve heat transfer.
- Incorporating heatsinks and cooling fans to dissipate heat.
- Using PCB materials with good thermal conductivity.
Designers can use thermal simulation tools to analyze the thermal performance of the PCB and make necessary adjustments.
Testing and Verification
Before finalizing a PCB design, it is essential to perform thorough testing and verification to ensure that the board functions as intended and meets all requirements.
Testing and verification steps include:
- Design Rule Checking (DRC): Verifying that the PCB layout meets the specified design rules, such as minimum trace width and spacing.
- Electrical Rule Checking (ERC): Checking for potential electrical issues, such as short circuits or unconnected pins.
- Signal Integrity Analysis: Simulating and analyzing the behavior of critical signals to ensure proper signal integrity.
- Thermal Analysis: Verifying that the PCB and its components operate within acceptable temperature ranges.
- Prototype Testing: Building and testing a physical prototype of the PCB to validate its functionality and performance.
By conducting comprehensive testing and verification, designers can identify and address issues early in the development process, reducing the risk of costly redesigns and delays.
Frequently Asked Questions (FAQ)
- What is the difference between a schematic and a PCB layout?
-
A schematic is a graphical representation of the electrical connections between components, while a PCB layout is the physical arrangement of components and traces on the board.
-
What is the purpose of a ground plane in a PCB?
-
A ground plane provides a low-impedance reference for electrical signals and helps reduce electromagnetic interference (EMI) and crosstalk between traces.
-
What is the minimum trace width and spacing for a PCB?
-
The minimum trace width and spacing depend on the PCB manufacturing capabilities and the design requirements. Typical values range from 0.1 mm to 0.2 mm, but smaller dimensions are possible with advanced manufacturing processes.
-
What is the difference between HASL and ENIG surface finishes?
-
HASL (Hot Air Solder Leveling) is a surface finish that involves dipping the PCB in molten solder, while ENIG (Electroless Nickel Immersion Gold) is a surface finish that consists of a nickel layer followed by a thin gold layer. ENIG provides better flatness and solderability compared to HASL.
-
What is the purpose of a solder mask on a PCB?
- A solder mask is a protective coating applied to the PCB that covers the copper traces and prevents short circuits. It also provides insulation and protection against environmental factors such as moisture and corrosion.
Conclusion
PCB design and layout is a complex process that requires a thorough understanding of electronic circuits, PCB manufacturing, and signal integrity. By following best practices and using appropriate tools and techniques, designers can create reliable, high-performance PCBs that meet the requirements of their intended applications.
Effective communication between designers, manufacturers, and other stakeholders is essential for successful PCB design and development. By collaborating closely and adhering to industry standards and guidelines, teams can streamline the PCB design process, reduce development time and costs, and ensure the quality and reliability of the final product.
0 Comments