Understanding PCB Copper Weight
What is PCB Copper Weight?
PCB copper weight refers to the thickness of the copper layer deposited on the surface of a printed circuit board substrate. It is a measure of the amount of copper used in the construction of the PCB, typically expressed in ounces per square foot (oz/ft² or simply oz). The most common copper weights used in PCB manufacturing are 0.5 oz, 1 oz, 2 oz, and 3 oz, although other weights may be used for specific applications.
How is PCB Copper Weight Measured?
The copper weight in a PCB is determined by the thickness of the copper foil laminated to the substrate material. The thickness is measured in ounces per square foot, which represents the weight of copper if it were to be evenly distributed across a one-square-foot area. To calculate the thickness in mils (thousandths of an inch), multiply the copper weight by 1.37. For example, a 1 oz copper weight translates to a thickness of approximately 1.37 mils or 35 microns.
Copper Weight (oz/ft²) | Thickness (mils) | Thickness (microns) |
---|---|---|
0.5 | 0.69 | 17.5 |
1 | 1.37 | 35 |
2 | 2.74 | 70 |
3 | 4.11 | 105 |
Factors Influencing PCB Copper Weight Selection
When designing a PCB, selecting the appropriate copper weight involves considering various factors that impact the board’s performance, manufacturability, and cost. Some of the key factors include:
Current Carrying Capacity
The copper weight directly affects the current carrying capacity of a PCB. Thicker copper layers can handle higher currents without experiencing excessive heating or voltage drop. The IPC-2152 standard provides guidelines for determining the appropriate copper weight based on the required current carrying capacity and the allowable temperature rise.
Signal Integrity
In high-speed and high-frequency applications, signal integrity is a critical concern. Thicker copper layers can help minimize signal loss and maintain signal integrity by reducing resistance and inductance. However, thicker copper can also increase capacitance, which may lead to signal distortion. Careful consideration of copper weight is necessary to strike a balance between signal integrity and other design requirements.
Thermal Management
Copper’s excellent thermal conductivity makes it an ideal material for dissipating heat generated by components on a PCB. Thicker copper layers provide better thermal management by efficiently spreading heat away from hot spots and preventing localized temperature rise. This is particularly important for power-dense designs or applications operating in high-temperature environments.
Manufacturing Constraints
The choice of copper weight also depends on the manufacturing capabilities and constraints of the PCB fabricator. Thinner copper layers (e.g., 0.5 oz) are easier to etch and require less processing time, making them more cost-effective for high-volume production. Thicker copper layers (e.g., 3 oz or more) may require specialized equipment and processes, increasing manufacturing complexity and cost.
Cost Considerations
As copper is a commodity, its price can fluctuate based on market conditions. The cost of a PCB is directly impacted by the amount of copper used, with thicker copper layers resulting in higher material costs. However, this cost increase should be weighed against the benefits of using thicker copper, such as improved performance, reliability, and reduced overall system cost.
PCB Copper Weight and Manufacturing Processes
The copper weight of a PCB influences various aspects of the manufacturing process, from the initial design stage to the final assembly and testing. Let’s explore how copper weight affects some of the key manufacturing processes:
PCB Design and Layout
When designing a PCB, the copper weight must be specified in the design files, typically in the form of a copper pour or fill. The designer must ensure that the chosen copper weight is compatible with the desired trace widths, spacing, and other design rules. Thicker copper layers may require wider traces and larger clearances to maintain manufacturability and reliability.
Etching and Plating
The etching process, which removes unwanted copper to create the desired circuit patterns, is directly affected by the copper weight. Thicker copper layers require longer etching times and may necessitate adjustments to the etching chemistry and parameters. Similarly, the plating process, used to deposit additional copper on specific areas (e.g., through-holes, vias), must be optimized for the chosen copper weight to ensure proper coverage and adhesion.
Drilling and Routing
The copper weight also impacts the drilling and routing processes used to create holes and cutouts in the PCB. Thicker copper layers may require more powerful drilling equipment and longer drill cycles to penetrate the material. The routing process, which cuts the PCB to its final shape, must also account for the copper weight to ensure clean and accurate cuts without causing delamination or other defects.
Soldermask and Silkscreen Application
The soldermask and silkscreen layers, which provide insulation and component identification on the PCB surface, must be compatible with the chosen copper weight. Thicker copper layers may require adjustments to the soldermask and silkscreen application processes to ensure proper coverage and adhesion. The copper weight can also affect the final appearance and legibility of the silkscreen markings.
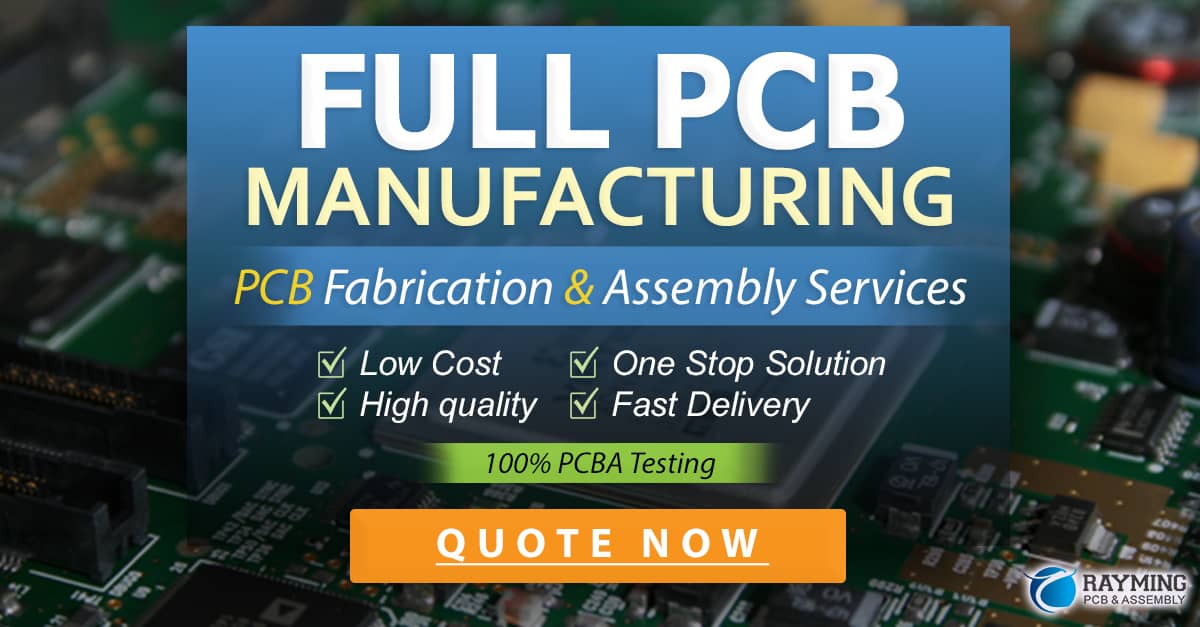
Frequently Asked Questions (FAQ)
-
Q: What is the most common copper weight used in PCB manufacturing?
A: The most common copper weight used in PCB manufacturing is 1 oz/ft², which corresponds to a thickness of approximately 35 microns or 1.37 mils. -
Q: Can different copper weights be used on the same PCB?
A: Yes, different copper weights can be used on different layers of the same PCB. This is known as a “mixed-weight” or “hybrid” design and is often used to optimize performance, manufacturability, and cost. -
Q: How does copper weight affect the impedance of a PCB trace?
A: The copper weight influences the impedance of a PCB trace by affecting its cross-sectional area and resistance. Thicker copper layers result in lower trace impedance, which can be beneficial for high-current or high-speed applications. -
Q: What are the challenges associated with using very thick copper weights (e.g., 4 oz or more)?
A: Very thick copper weights can pose challenges in terms of manufacturability, cost, and design complexity. They may require specialized etching and plating processes, longer manufacturing times, and higher material costs. Designers must also account for the increased thickness when defining trace widths, spacings, and other design rules. -
Q: How can I determine the appropriate copper weight for my PCB design?
A: Determining the appropriate copper weight involves considering factors such as current carrying capacity, signal integrity, thermal management, manufacturing constraints, and cost. Consulting with experienced PCB designers, manufacturers, and referring to industry standards (e.g., IPC-2152) can help guide the selection process.
Conclusion
PCB copper weight is a critical factor that influences the performance, reliability, manufacturability, and cost of printed circuit boards. Understanding the concept of copper weight, its measurement, and the factors that influence its selection is essential for designing and manufacturing high-quality PCBs. By carefully considering the current carrying capacity, signal integrity, thermal management, manufacturing constraints, and cost implications, designers can make informed decisions about the appropriate copper weight for their specific applications.
As PCB technology continues to evolve, with increasing demands for higher speeds, greater power densities, and improved reliability, the role of copper weight in PCB design and manufacturing will only become more significant. By staying informed about the latest developments and best practices in PCB copper weight selection and optimization, designers and manufacturers can stay ahead of the curve and deliver cutting-edge products that meet the ever-growing needs of the electronics industry.
0 Comments