Introduction to Box Build PCB Assembly
Box build PCB assembly is a comprehensive manufacturing process that combines printed circuit board (PCB) assembly with the integration of various components, such as wiring, connectors, and enclosures, to create a fully functional electronic product. This process involves a series of steps, from the initial design and fabrication of the PCB to the final testing and packaging of the completed device.
Key Components of Box Build PCB Assembly
- Printed Circuit Board (PCB)
- Electronic components (resistors, capacitors, ICs, etc.)
- Wiring and connectors
- Enclosures or boxes
- Mounting hardware
Advantages of Box Build PCB Assembly
- Streamlined manufacturing process
- Reduced overall costs
- Improved product quality and reliability
- Faster time-to-market
- Customizable to specific requirements
The Box Build PCB Assembly Process
The box build PCB assembly process consists of several stages, each requiring specific expertise and attention to detail. The following sections will outline the key steps involved in this process.
Step 1: PCB Design and Fabrication
The first step in box build PCB assembly is designing and fabricating the printed circuit board. This involves creating a schematic diagram and a PCB layout using specialized software, such as Altium Designer or Eagle. The design must consider factors like component placement, signal integrity, and thermal management.
Once the design is finalized, the PCB is fabricated using a combination of photolithography, etching, and plating processes. The resulting board serves as the foundation for the entire electronic device.
Step 2: Component Procurement and Inspection
With the PCB fabricated, the next step is to procure the necessary electronic components. This may involve sourcing components from various suppliers and ensuring that they meet the required specifications, such as tolerance, temperature rating, and package type.
Upon receipt, the components undergo a rigorous inspection process to verify their quality and functionality. This may include visual inspection, automated optical inspection (AOI), and X-ray inspection for hidden defects.
Step 3: PCB Assembly
The PCB assembly stage involves mounting the electronic components onto the printed circuit board. This can be done using various techniques, depending on the component type and the production volume:
- Through-hole assembly: Components with wire leads are inserted into drilled holes on the PCB and soldered in place.
- Surface mount assembly: Components with flat terminals are placed directly onto solder pads on the PCB surface and soldered using reflow or wave soldering processes.
Automated assembly lines, featuring pick-and-place machines and soldering ovens, are often used to achieve high-speed, high-precision assembly. Manual assembly may be necessary for certain components or low-volume production runs.
Step 4: Box Integration and Wiring
After the PCB is assembled, it is integrated into the enclosure or box. This involves mounting the PCB securely within the enclosure using standoffs, screws, or other hardware. Any necessary wiring, such as power cables, data cables, or external connectors, is also installed at this stage.
Proper cable management and strain relief techniques are essential to ensure the reliability and longevity of the final product. Cable ties, clamps, and grommets may be used to organize and protect the wiring.
Step 5: Testing and Quality Control
Before the final product is packaged and shipped, it must undergo thorough testing and quality control procedures. This may include:
- Functional testing: Verifying that the device performs its intended functions correctly.
- In-circuit testing (ICT): Checking the electrical connections and component values on the PCB.
- Burn-in testing: Running the device under stress conditions to identify any potential failures.
- Environmental testing: Exposing the device to various temperature, humidity, and vibration conditions to ensure its durability.
Any defects or issues identified during testing are addressed through rework or repair processes. Only devices that pass all quality control checks are approved for final packaging and shipment.
Step 6: Packaging and Shipping
The final step in the box build PCB assembly process is packaging the completed device for shipment to the customer. This may involve placing the device in a protective anti-static bag, foam inserts, or custom-designed packaging to prevent damage during transit.
Proper labeling, including product identification, serial numbers, and regulatory markings, is applied to the packaging. The packaged devices are then shipped to the customer using the appropriate transportation method, such as air, ground, or sea freight.
Choosing a Box Build PCB Assembly Service Provider
When selecting a box build PCB assembly service provider, several key factors should be considered to ensure a successful partnership.
Technical Capabilities
The service provider should have the necessary technical capabilities to handle your specific box build PCB assembly requirements. This includes:
- Experience with various PCB technologies (e.g., rigid, flexible, high-density interconnect)
- Proficiency in different assembly techniques (e.g., through-hole, surface mount, mixed technology)
- Ability to work with a wide range of component packages and sizes
- Expertise in box integration and wiring
- Access to advanced testing and inspection equipment
Quality Management System
A robust quality management system is essential for ensuring consistent, high-quality output. Look for a service provider with certifications such as ISO 9001, AS9100, or IPC-A-610, which demonstrate their commitment to quality and adherence to industry standards.
Supply Chain Management
An effective supply chain management strategy is crucial for maintaining a smooth and efficient box build PCB assembly process. The service provider should have established relationships with reliable component suppliers and be able to manage inventory levels, lead times, and component obsolescence issues.
Scalability and Flexibility
Your chosen service provider should be able to accommodate your production volume requirements, whether you need small-batch prototypes or large-scale mass production. They should also be flexible enough to adapt to changes in your design or production schedule as needed.
Communication and Support
Clear and open communication is key to a successful box build PCB Assembly Partnership. Look for a service provider that is responsive, proactive, and willing to collaborate closely with your team. They should offer comprehensive support, from initial design consultation to post-delivery technical assistance.
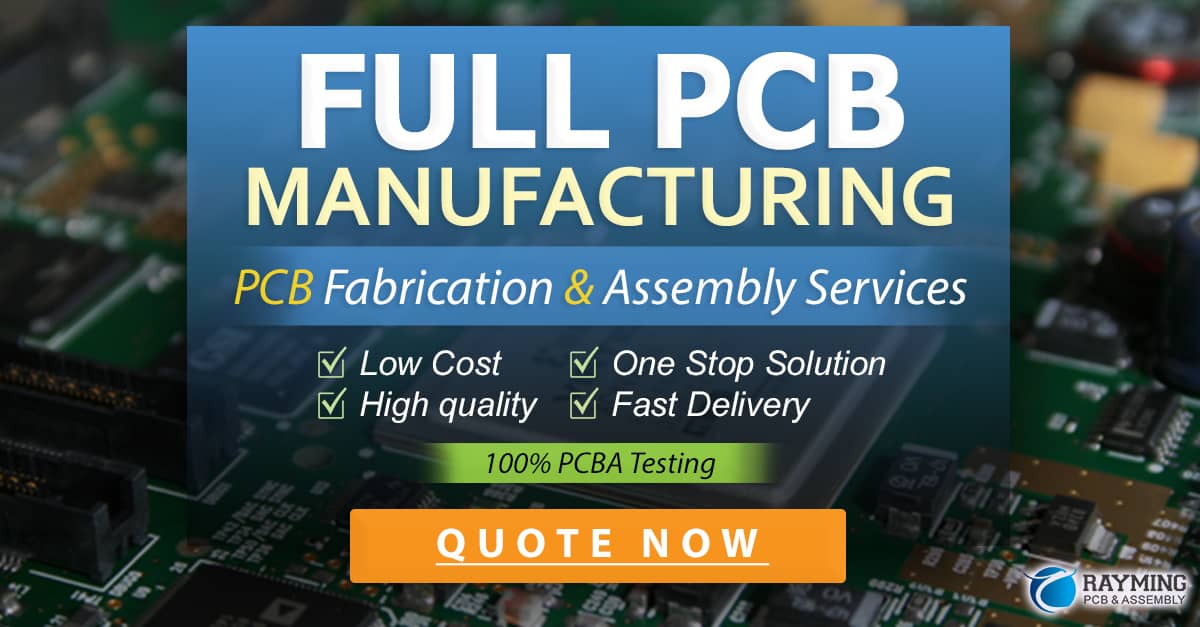
Common Applications of Box Build PCB Assembly
Box build PCB assembly services are utilized across a wide range of industries and applications, including:
- Consumer electronics (e.g., smartphones, tablets, wearables)
- Automotive electronics (e.g., infotainment systems, sensors, control modules)
- Medical devices (e.g., diagnostic equipment, patient monitoring systems, implantables)
- Industrial automation and control systems
- Aerospace and defense equipment
- Telecommunications infrastructure
- Internet of Things (IoT) devices
Each application may have specific requirements in terms of performance, reliability, and regulatory compliance, which must be carefully considered during the box build PCB assembly process.
Frequently Asked Questions (FAQ)
1. What is the difference between box build PCB assembly and regular PCB assembly?
Box build PCB assembly goes beyond the basic assembly of components onto a printed circuit board. It includes the integration of the assembled PCB into an enclosure or box, along with the necessary wiring, connectors, and mounting hardware. The result is a fully functional electronic product, ready for use.
2. How long does the box build PCB assembly process typically take?
The lead time for box build PCB assembly can vary depending on factors such as the complexity of the design, the availability of components, and the production volume. Simple designs with readily available components may take a few weeks, while more complex projects could require several months. It is essential to discuss your specific timeline requirements with your chosen service provider.
3. Can box build PCB assembly services handle both small and large production volumes?
Yes, most box build PCB assembly service providers are equipped to handle a wide range of production volumes, from small-batch prototypes to high-volume mass production. However, it is important to verify that your chosen provider has the capacity and scalability to meet your specific needs.
4. What certifications should I look for in a box build PCB assembly service provider?
Key certifications to look for include ISO 9001 (quality management), AS9100 (aerospace quality management), and IPC-A-610 (acceptability of electronic assemblies). These certifications demonstrate the provider’s commitment to quality, reliability, and adherence to industry standards. Additional certifications may be relevant depending on your specific industry or application.
5. How can I ensure the quality and reliability of my box build PCB assembly project?
To ensure the quality and reliability of your project, work closely with your chosen service provider throughout the entire process. Provide clear and comprehensive design documentation, including bill of materials (BOM), schematics, and PCB layout files. Discuss your quality requirements and testing procedures upfront, and maintain open communication to address any issues or concerns promptly. Additionally, consider conducting on-site audits or inspections to verify the provider’s capabilities and compliance with your standards.
Conclusion
Box build PCB assembly is a complex and multi-faceted process that requires expertise, attention to detail, and close collaboration between the customer and the service provider. By understanding the key steps involved, from PCB design and fabrication to final testing and packaging, you can better navigate the process and ensure a successful outcome for your electronic product.
When selecting a box build PCB assembly service provider, carefully consider factors such as technical capabilities, quality management, supply chain management, scalability, and communication. By partnering with a reputable and experienced provider, you can leverage their expertise to bring your product to market efficiently, reliably, and cost-effectively.
As the demand for electronic devices continues to grow across various industries, box build PCB assembly will remain a critical service for bringing innovative products to life. By staying informed about the latest trends, technologies, and best practices in this field, you can position your organization to succeed in an increasingly competitive market.
Industry | Application Examples |
---|---|
Consumer Electronics | Smartphones, tablets, wearables, smart home devices |
Automotive | Infotainment systems, sensors, control modules, electric vehicle components |
Medical Devices | Diagnostic equipment, patient monitoring systems, implantables, surgical tools |
Industrial Automation | Control systems, sensors, communication devices, robotics |
Aerospace and Defense | Avionics, communication systems, surveillance equipment, satellites |
Telecommunications | Routers, switches, base stations, optical networks |
Internet of Things (IoT) | Smart sensors, gateways, edge computing devices, asset tracking systems |
0 Comments