Understanding the Application and Environment
Before diving into the design process, it is essential to have a clear understanding of the intended application and the environment in which the flexible circuit will operate. Consider factors such as:
- Temperature range
- Humidity levels
- Mechanical stresses
- Chemical exposure
- Electromagnetic interference (EMI)
By knowing the specific requirements and constraints of your application, you can make informed decisions throughout the design process and select materials and components that can withstand the expected conditions.
Choosing the Right Materials
The choice of materials is critical in Flexible Circuit Design. The most common base material for flex circuits is polyimide, which offers excellent thermal stability, chemical resistance, and mechanical strength. Other materials, such as polyester and fluoropolymers, may be used depending on the specific requirements of the application.
When selecting materials, consider the following properties:
- Dielectric constant
- Dissipation factor
- Thermal conductivity
- Coefficient of thermal expansion (CTE)
- Flexibility and durability
Additionally, choose copper foils and adhesives that are compatible with the base material and can withstand the expected mechanical and environmental stresses.
Determining the Number of Layers
Flexible circuits can be designed with a single layer or multiple layers, depending on the complexity of the circuit and the space constraints. Single-layer flex circuits are the simplest and most cost-effective option, suitable for low-density designs with few components.
Multi-layer flex circuits, on the other hand, allow for higher component density and more complex routing. They consist of multiple conductive layers separated by insulating layers, enabling the integration of more functionality in a smaller footprint.
When deciding on the number of layers, consider the following factors:
- Circuit complexity
- Component density
- Signal integrity requirements
- Shielding and grounding needs
- Manufacturing costs
Keep in mind that increasing the number of layers also increases the manufacturing complexity and cost, so it is essential to strike a balance between functionality and affordability.
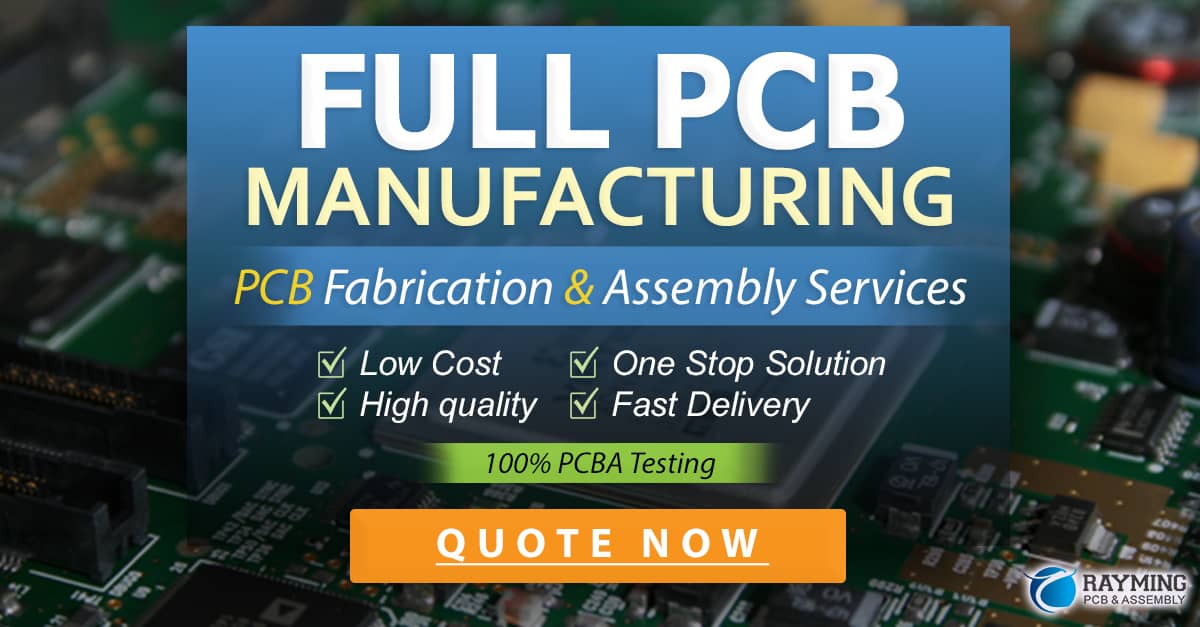
Designing for Flexibility
One of the key advantages of flexible circuits is their ability to bend and flex without compromising electrical performance. However, designing for flexibility requires careful consideration of several factors, such as:
- Bend radius: Determine the minimum bend radius the circuit needs to accommodate and ensure that the chosen materials and components can withstand the required bending.
- Stress relief: Incorporate stress relief features, such as curved traces and strain relief cutouts, to minimize stress concentration points and prevent damage to the circuit during flexing.
- Conductor width and spacing: Use appropriate conductor widths and spacing to maintain signal integrity and prevent short circuits or open circuits during bending.
- Adhesive selection: Choose adhesives that provide good bonding strength and flexibility to prevent delamination or cracking during flexing.
By designing with flexibility in mind, you can ensure that your flex circuit will perform reliably even under repeated bending and flexing.
Signal Integrity and EMI Considerations
Maintaining signal integrity and minimizing electromagnetic interference (EMI) are crucial aspects of flexible circuit design. High-speed signals and sensitive analog circuits are particularly susceptible to signal degradation and noise.
To ensure signal integrity and minimize EMI, consider the following techniques:
- Controlled impedance: Use controlled impedance design techniques, such as stripline or microstrip, to maintain consistent impedance along the signal path and minimize reflections.
- Grounding and shielding: Implement proper grounding and shielding strategies, such as ground planes and shielded traces, to reduce EMI and crosstalk.
- Termination and filtering: Use appropriate termination and filtering techniques to minimize signal reflections and attenuate high-frequency noise.
- Trace routing: Route traces carefully to minimize crosstalk and avoid long parallel runs of high-speed signals.
By addressing signal integrity and EMI concerns early in the design process, you can ensure that your flexible circuit will perform reliably and meet the required specifications.
Thermal Management
Thermal management is an essential consideration in flexible circuit design, particularly for applications that generate significant heat or operate in high-temperature environments. Proper thermal management helps to prevent component overheating, which can lead to reduced performance, reliability issues, and even circuit failure.
Consider the following thermal management techniques:
- Thermal vias: Use thermal vias to provide a low-resistance path for heat dissipation from components to the ground plane or external heat sinks.
- Heatsinks and heat spreaders: Incorporate heatsinks or heat spreaders to efficiently distribute and dissipate heat generated by high-power components.
- Thermal interface materials: Use thermal interface materials, such as thermal adhesives or thermal pads, to improve heat transfer between components and heatsinks or the circuit substrate.
- Component placement: Carefully place components to minimize thermal interactions and ensure adequate airflow for cooling.
By implementing effective thermal management strategies, you can ensure that your flexible circuit operates within the specified temperature range and maintains long-term reliability.
Manufacturing Considerations
Designing a flexible circuit that is manufacturable and cost-effective is essential for successful production. Consider the following manufacturing aspects during the design process:
- Design for manufacturing (DFM): Follow DFM guidelines provided by your manufacturing partner to ensure that your design can be efficiently and reliably manufactured. This includes considerations such as minimum feature sizes, clearances, and tolerances.
- Panelization: Design your flex circuit to be panelized efficiently, maximizing the number of circuits per panel to reduce manufacturing costs.
- Stiffeners and support: Incorporate stiffeners and support structures where necessary to facilitate handling and assembly of the flex circuit.
- Connector and component placement: Position connectors and components in a way that allows for easy assembly and minimizes stress on the circuit during installation and use.
By collaborating closely with your manufacturing partner and considering manufacturing requirements throughout the design process, you can avoid costly design revisions and ensure a smooth transition to production.
Testing and Validation
Thorough testing and validation are critical to ensuring the reliability and performance of your flexible circuit. Develop a comprehensive testing plan that covers various aspects, such as:
- Continuity and isolation testing: Verify that all connections are intact and there are no short circuits or open circuits.
- Functional testing: Test the circuit under real-world operating conditions to ensure that it performs as expected.
- Environmental testing: Subject the circuit to temperature cycling, humidity, and vibration tests to validate its robustness and reliability in the intended environment.
- Signal integrity testing: Perform signal integrity measurements, such as time-domain reflectometry (TDR) and eye diagram analysis, to verify that the circuit meets the required signal quality standards.
By conducting rigorous testing and validation, you can identify and address any issues early in the development process, reducing the risk of field failures and ensuring customer satisfaction.
Collaboration and Communication
Designing a successful flexible circuit requires close collaboration and effective communication among all stakeholders, including designers, engineers, manufacturers, and end-users. Foster a collaborative environment that encourages open communication and iterative feedback throughout the design process.
Consider the following best practices for collaboration and communication:
- Clearly define requirements and specifications upfront to ensure that all stakeholders are aligned on the project goals and constraints.
- Regularly review design progress and solicit feedback from relevant stakeholders to identify potential issues and opportunities for improvement.
- Maintain clear and concise documentation, including design files, bill of materials (BOM), and assembly instructions, to facilitate smooth communication and avoid misunderstandings.
- Work closely with your manufacturing partner to optimize the design for manufacturability and cost-effectiveness, leveraging their expertise and experience.
By fostering a collaborative and communicative environment, you can streamline the design process, minimize errors, and ultimately deliver a high-quality flexible circuit that meets the needs of your application.
Frequently Asked Questions (FAQ)
- What are the advantages of using flexible circuits over traditional rigid PCBs?
-
Flexible circuits offer several advantages, including improved reliability, reduced weight and space, enhanced flexibility, and the ability to conform to various shapes and sizes. They can also withstand higher mechanical stresses and provide better shock and vibration resistance compared to rigid PCBs.
-
What materials are commonly used in flexible circuit design?
-
The most common base material for flex circuits is polyimide, which offers excellent thermal stability, chemical resistance, and mechanical strength. Other materials, such as polyester and fluoropolymers, may be used depending on the specific requirements of the application. Copper foils and adhesives are also carefully selected to ensure compatibility and performance.
-
How do I determine the appropriate number of layers for my flexible circuit?
-
The number of layers in a flexible circuit depends on factors such as circuit complexity, component density, signal integrity requirements, shielding and grounding needs, and manufacturing costs. Single-layer flex circuits are suitable for low-density designs, while multi-layer circuits offer higher component density and more complex routing capabilities. It is essential to strike a balance between functionality and affordability when deciding on the number of layers.
-
What are some key considerations for designing flexible circuits for reliability?
-
To ensure reliability in flexible circuit design, consider factors such as bend radius, stress relief features, conductor width and spacing, and adhesive selection. Incorporate stress relief features, such as curved traces and strain relief cutouts, to minimize stress concentration points. Use appropriate conductor widths and spacing to maintain signal integrity and prevent short circuits or open circuits during bending. Choose adhesives that provide good bonding strength and flexibility to prevent delamination or cracking.
-
How can I address signal integrity and EMI concerns in my flexible circuit design?
- To maintain signal integrity and minimize EMI, employ techniques such as controlled impedance design, proper grounding and shielding, appropriate termination and filtering, and careful trace routing. Use controlled impedance design techniques, such as stripline or microstrip, to maintain consistent impedance along the signal path. Implement ground planes and shielded traces to reduce EMI and crosstalk. Use termination and filtering techniques to minimize signal reflections and attenuate high-frequency noise. Route traces carefully to minimize crosstalk and avoid long parallel runs of high-speed signals.
Conclusion
Designing flexible circuits requires careful consideration of multiple factors to ensure optimal performance, reliability, and manufacturability. By understanding the application and environment, choosing the right materials, determining the appropriate number of layers, designing for flexibility, addressing signal integrity and EMI concerns, implementing thermal management techniques, considering manufacturing aspects, conducting thorough testing and validation, and fostering collaboration and communication, you can successfully design flexible circuits that meet the unique requirements of your application.
As technology continues to advance and the demand for smaller, lighter, and more flexible electronic devices grows, the importance of flexible circuit design will only increase. By staying up-to-date with the latest design techniques, materials, and manufacturing processes, and by collaborating closely with experienced partners, you can unlock the full potential of flexible circuits and drive innovation in your products and applications.
Factor | Considerations |
---|---|
Application and Environment | Temperature range, humidity levels, mechanical stresses, chemical exposure, electromagnetic interference (EMI) |
Materials Selection | Base material (polyimide, polyester, fluoropolymers), copper foils, adhesives, dielectric constant, dissipation factor, thermal conductivity, CTE, flexibility, durability |
Number of Layers | Circuit complexity, component density, signal integrity requirements, shielding and grounding needs, manufacturing costs |
Designing for Flexibility | Bend radius, stress relief features, conductor width and spacing, adhesive selection |
Signal Integrity and EMI | Controlled impedance design, grounding and shielding, termination and filtering, trace routing |
Thermal Management | Thermal vias, heatsinks and heat spreaders, thermal interface materials, component placement |
Manufacturing Considerations | Design for manufacturing (DFM), panelization, stiffeners and support, connector and component placement |
Testing and Validation | Continuity and isolation testing, functional testing, environmental testing, signal integrity testing |
Collaboration and Communication | Clear requirements and specifications, regular design reviews, concise documentation, collaboration with manufacturing partners |
By carefully considering these nine factors and leveraging the expertise of experienced partners, you can design flexible circuits that meet the unique demands of your application, ensuring optimal performance, reliability, and manufacturability.
0 Comments