Understanding BGA (Ball Grid Array) Technology
Ball Grid Array (BGA) is a type of surface-mount packaging used for integrated circuits (ICs) that utilizes a grid of solder balls to connect the chip to the printed circuit board (PCB). This technology has become increasingly popular in recent years due to its numerous advantages over traditional packaging methods, such as:
- Higher pin count density
- Better electrical and thermal performance
- Reduced package size
- Improved reliability
How BGA Packages Work
A BGA package consists of an IC chip mounted on a substrate, with a grid of solder balls on the bottom side of the substrate. These solder balls are used to connect the chip to the PCB, providing both electrical and mechanical connections.
The BGA package is placed on the PCB and heated in a reflow oven, causing the solder balls to melt and form a strong bond between the package and the board. This process is known as solder reflow.
Advantages of BGA Packages
BGA packages offer several advantages over other packaging methods, such as:
- Higher pin count density: BGA packages can accommodate a large number of pins in a small area, making them ideal for high-density applications.
- Better electrical performance: The short, uniform length of the solder balls reduces inductance and capacitance, resulting in better signal integrity and faster signal propagation.
- Improved thermal performance: The large number of solder balls provides a low-resistance thermal path, allowing for better heat dissipation from the chip.
- Reduced package size: BGA packages are smaller than other packaging methods, such as quad flat packages (QFPs), allowing for more compact designs.
- Enhanced reliability: The solder balls provide a strong mechanical connection between the package and the PCB, reducing the risk of connection failures due to vibration or thermal stress.
What is BGA Reballing?
BGA reballing is the process of replacing the solder balls on a BGA package. This process is typically performed when the original solder balls have become damaged or worn out, or when the package needs to be removed from the PCB for repair or replacement.
Reasons for BGA Reballing
There are several reasons why a BGA package may require reballing:
- Solder ball damage: The solder balls can become damaged due to mechanical stress, thermal cycling, or exposure to harsh environments. Damaged solder balls can cause intermittent or complete connection failures.
- Solder ball wear: Over time, the solder balls can wear out due to repeated thermal cycles or mechanical stress. This can lead to poor connections and reduced reliability.
- Package removal: If a BGA package needs to be removed from the PCB for repair or replacement, the solder balls will be destroyed in the process. Reballing is necessary to restore the package’s ability to be soldered to the PCB.
- Manufacturing defects: In some cases, BGA packages may have manufacturing defects that require reballing to correct.
The BGA Reballing Process
The BGA reballing process typically involves the following steps:
- Package removal: The BGA package is carefully removed from the PCB using a hot air station or other specialized equipment.
- Solder ball removal: The remaining solder balls and residue are removed from the package using a soldering iron, solder wick, or other tools.
- Pad cleaning: The pads on the package substrate are cleaned to remove any oxidation or contamination.
- Solder ball placement: New solder balls are placed on the pads using a stencil or other precision placement methods.
- Reflow: The package is heated in a reflow oven to melt the solder balls and form a strong bond with the pads.
- Inspection: The reballed package is inspected for proper solder ball placement, alignment, and connection quality.
Equipment and Materials Used in BGA Reballing
BGA reballing requires specialized equipment and materials, including:
- Hot air station or reflow oven for removing and soldering the package
- Soldering iron and solder wick for removing solder residue
- Solder balls of the appropriate size and composition
- Stencils or other precision placement tools for applying new solder balls
- Flux for improving solder wettability and preventing oxidation
- Cleaning agents for removing contaminants from the package and PCB
Challenges in BGA Reballing
While BGA reballing is a well-established process, it presents several challenges that must be addressed to ensure successful results:
Precision and Accuracy
One of the main challenges in BGA reballing is achieving the necessary precision and accuracy in solder ball placement. The solder balls must be placed on the pads with a high degree of accuracy to ensure proper alignment and connection with the PCB.
This requires the use of specialized equipment, such as stencils or automated placement machines, as well as skilled operators who can perform the process consistently and reliably.
Thermal Management
Another challenge in BGA reballing is managing the thermal profile of the package during the reflow process. The package must be heated to the appropriate temperature to melt the solder balls and form a strong bond, but excessive heat can damage the package or the PCB.
This requires careful control of the reflow oven temperature and duration, as well as the use of thermal protection measures such as heat sinks or shielding.
Contamination Control
Contamination is another significant challenge in BGA reballing. Any contaminants on the package or PCB, such as dirt, dust, or oxidation, can interfere with the solder bond and cause connection failures.
To prevent contamination, the reballing process must be performed in a clean environment, using high-quality materials and cleaning agents. The package and PCB must be thoroughly cleaned before reballing, and the process must be performed with care to avoid introducing new contaminants.
Package Handling and Protection
BGA packages are delicate and can be easily damaged during the reballing process. The package must be handled carefully to avoid cracking or chipping the substrate, damaging the solder pads, or dislodging components.
This requires the use of specialized handling equipment, such as vacuum tweezers or suction cups, as well as protective measures such as anti-static mats and grounding straps.
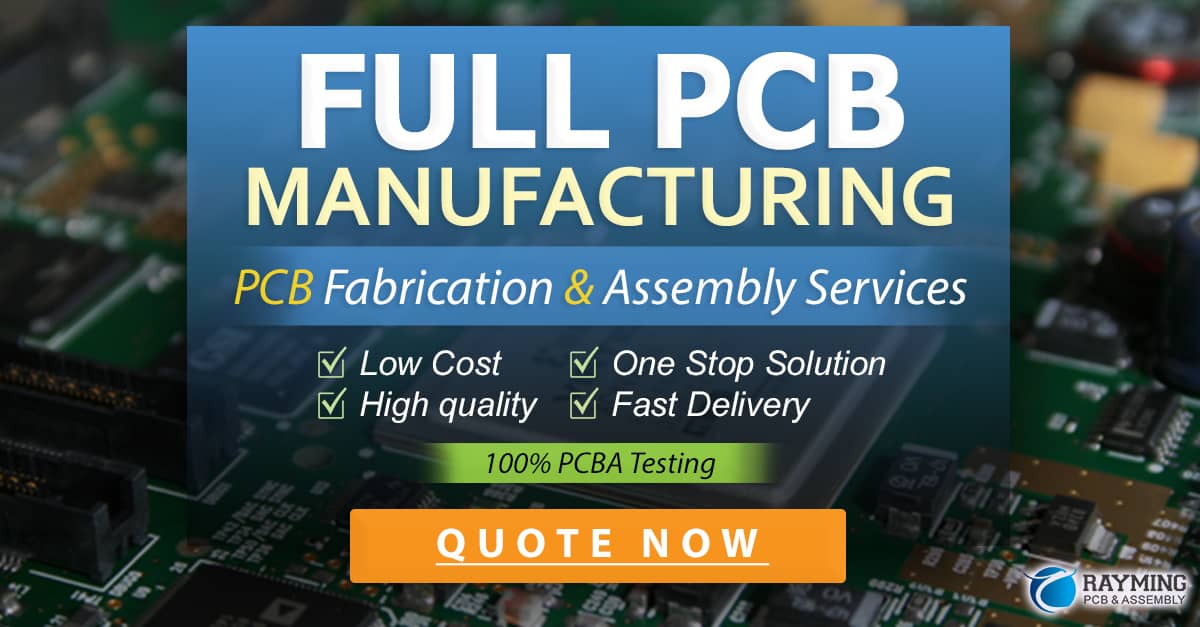
Importance of Proper BGA Reballing
Proper BGA reballing is essential for ensuring the reliability and performance of electronic devices. Poorly performed reballing can result in a range of problems, including:
- Intermittent or complete connection failures
- Reduced signal integrity and performance
- Increased risk of thermal or mechanical stress failures
- Shortened device lifespan and increased maintenance costs
To avoid these problems, it is important to choose a qualified and experienced BGA reballing service provider who uses high-quality equipment and materials and follows best practices for precision, thermal management, contamination control, and package handling.
Conclusion
BGA reballing is a critical process for maintaining and repairing electronic devices that use BGA packages. By replacing damaged or worn solder balls, reballing restores the package’s ability to form strong, reliable connections with the PCB.
However, reballing presents several challenges, including precision and accuracy, thermal management, contamination control, and package handling. Proper equipment, materials, and techniques are essential for achieving successful results and ensuring the long-term reliability and performance of the device.
As electronic devices continue to become more complex and miniaturized, the importance of BGA reballing will only continue to grow. By understanding the process, challenges, and best practices involved in reballing, engineers, technicians, and managers can make informed decisions about when and how to perform this critical maintenance and repair procedure.
Frequently Asked Questions (FAQ)
1. What is the difference between BGA and other package types?
BGA packages differ from other types, such as quad flat packages (QFPs), in several ways:
- BGA packages use a grid of solder balls to connect to the PCB, while QFPs use pins.
- BGA packages have a higher pin count density, allowing for more connections in a smaller area.
- BGA packages have better electrical and thermal performance due to the shorter, more uniform connections.
- BGA packages are smaller and more compact than QFPs.
2. Can all BGA packages be reballed?
In general, most BGA packages can be reballed, provided they are not severely damaged or contaminated. However, some packages may be more challenging to reball than others, depending on factors such as:
- Package size and pin count
- Substrate material and construction
- Solder ball composition and size
- Presence of underfill or other adhesives
Before attempting to reball a BGA package, it is important to assess its condition and suitability for the process.
3. How much does BGA reballing cost?
The cost of BGA reballing can vary widely depending on factors such as:
- Package type and complexity
- Equipment and materials required
- Labor and overhead costs
- Geographic location and market conditions
In general, BGA reballing can cost anywhere from a few dollars to several hundred dollars per package, depending on these factors. It is important to obtain quotes from multiple service providers and compare the costs and benefits before making a decision.
4. How long does BGA reballing take?
The time required for BGA reballing can also vary depending on the package type, complexity, and other factors. In general, the process can take anywhere from a few minutes to several hours per package, depending on the specific steps involved and the equipment and techniques used.
Some factors that can affect the reballing time include:
- Package removal and cleaning
- Solder ball placement and alignment
- Reflow temperature and duration
- Inspection and testing
It is important to allow sufficient time for the reballing process to ensure optimal results and avoid rushing or cutting corners.
5. Can I perform BGA reballing myself?
While it is possible for skilled technicians to perform BGA reballing themselves, it is generally not recommended for several reasons:
- BGA reballing requires specialized equipment and materials that can be expensive to acquire and maintain.
- The process requires a high degree of precision, accuracy, and consistency that can be difficult to achieve without proper training and experience.
- Improper reballing can result in damage to the package or PCB, leading to costly repairs or replacements.
- Many manufacturers and suppliers will not warranty or support devices that have been reballed by unauthorized parties.
For these reasons, it is generally best to entrust BGA reballing to qualified and experienced professionals who have the necessary equipment, skills, and certifications to perform the process reliably and effectively.
0 Comments