Introduction to Via holes and PCBs
A via hole, also known simply as a via, is a small opening or hole drilled through a printed circuit board (PCB) that allows electrical current to pass from one layer of the board to another. Vias are essential features in multi-layer PCBs as they enable interconnectivity between different copper layers, allowing for more complex circuit designs and routing within a compact board space.
PCBs are the backbone of modern electronics, providing a platform for mounting and connecting various electronic components. These boards are made from insulating materials, such as fiberglass or composite epoxy, with conductive copper tracks etched onto their surface to form the desired circuit pattern. In multi-layer PCBs, several layers of copper tracks are stacked and separated by insulating layers, with via holes drilled through the board to establish electrical connections between the layers.
Types of Via Holes
There are several types of via holes used in PCB design, each serving a specific purpose and having its own characteristics. The most common types include:
Through-hole Vias
Through-hole vias are the most basic type of via, consisting of a hole drilled completely through the PCB, from the top layer to the bottom layer. These vias are typically plated with a conductive material, such as copper, to create an electrical connection between the layers. Through-hole vias are reliable and have excellent mechanical strength, making them suitable for high-power applications or when components need to be soldered directly to the board.
Blind Vias
Blind vias are partially drilled holes that start from either the top or bottom layer of the PCB and terminate at an inner layer, without passing through the entire board thickness. These vias are used to connect an outer layer to one or more inner layers, providing more flexibility in routing and enabling higher component density on the outer layers. Blind vias are commonly used in high-density interconnect (HDI) PCBs.
Buried Vias
Buried vias are similar to blind vias but are located entirely within the inner layers of the PCB, without extending to either the top or bottom surface. These vias connect two or more inner layers, allowing for more complex routing and reducing the overall board size. Buried vias are typically used in advanced PCB designs with high layer counts and demanding signal integrity requirements.
Micro Vias
Micro vias, also known as laser vias, are small, high-precision vias created using laser drilling techniques. These vias have a diameter of less than 150 microns and are used to connect adjacent layers in high-density PCBs. Micro vias enable finer pitch connections and are essential for advanced packaging technologies, such as chip-scale packaging (CSP) and Ball Grid Arrays (BGAs).
Via-in-pad
Via-in-pad is a design technique where a via hole is placed directly within a component pad, allowing for a more compact PCB layout and improved signal integrity. This technique is particularly useful in BGA Packages, where the limited space between balls requires efficient routing. Via-in-pad designs require careful consideration of the via fill material and the potential for solder wicking during the assembly process.
Via Hole Manufacturing Process
The manufacturing process for via holes involves several steps, which may vary depending on the type of via and the specific PCB fabrication techniques used. The general process for creating through-hole vias is as follows:
-
Drilling: Via holes are mechanically drilled through the PCB using high-speed, computer-controlled drill machines. The drill bit size and the drilling parameters are determined by the via diameter and the board material.
-
Deburring and cleaning: After drilling, the via holes are deburred to remove any rough edges or debris that may interfere with the subsequent plating process. The holes are then cleaned using a chemical solution to remove any remaining contaminants.
-
Electroless copper deposition: A thin layer of copper is chemically deposited onto the walls of the via holes and the surface of the PCB. This layer acts as a conductive seed for the subsequent electroplating process.
-
Copper electroplating: The PCB is immersed in an electrolytic bath containing copper ions. An electric current is applied, causing the copper ions to deposit onto the walls of the via holes and the surface of the board, forming a thicker, more conductive layer.
-
Inspection and testing: The plated via holes are inspected for consistency, conductivity, and adherence to the specified dimensions. Electrical tests may be performed to ensure proper connectivity between layers.
For blind, buried, and micro vias, the manufacturing process may involve additional steps, such as laser drilling, sequential lamination, or specialized plating techniques.
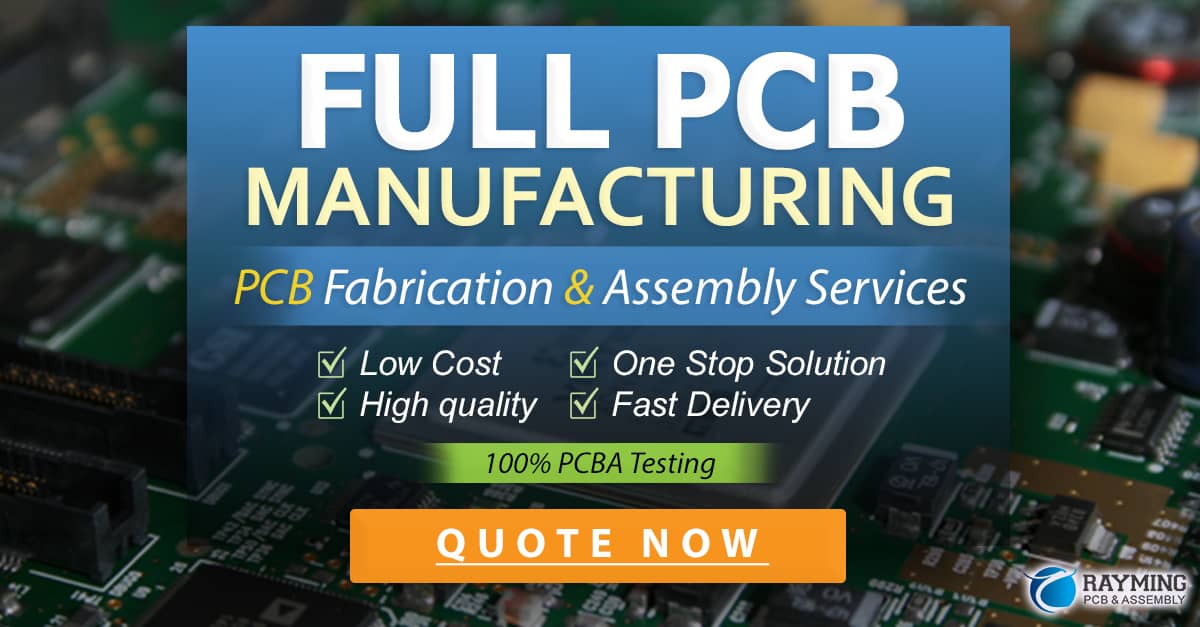
Design Considerations for Via Holes
When designing a PCB with via holes, several factors must be considered to ensure optimal performance, manufacturability, and reliability. Some key design considerations include:
Via size and pitch
The via size and pitch (the distance between adjacent vias) should be chosen based on the PCB’s layer count, the required current carrying capacity, and the available space for routing. Smaller vias allow for higher density and finer pitch connections but may be more challenging to manufacture and have limited current carrying capacity. Larger vias offer better electrical and thermal performance but consume more board space.
Via placement
Via placement should be strategically planned to minimize the impact on signal integrity and to avoid interference with components and other board features. Vias should be placed as close as possible to the connected components to reduce the length of the connecting traces and minimize parasitic effects, such as inductance and capacitance.
Via shielding and grounding
In high-speed or sensitive analog circuits, via shielding and grounding techniques may be employed to reduce electromagnetic interference (EMI) and improve signal integrity. This can involve the use of ground vias, which are connected to the ground plane, or the placement of vias in specific patterns to create a shielding effect.
Via Filling and capping
Via filling and capping are techniques used to improve the mechanical strength, thermal performance, and signal integrity of vias. Via filling involves filling the via hole with a non-conductive material, such as epoxy, to prevent solder wicking and to provide a flat surface for component mounting. Via capping involves covering the top and/or bottom of the via with a conductive material, such as copper or gold, to improve electrical performance and to prevent contamination.
Via aspect ratio
The via aspect ratio is the ratio of the via’s depth to its diameter. High aspect ratio vias, where the depth is much greater than the diameter, can be challenging to manufacture and may suffer from poor plating uniformity or voids. It is essential to consider the achievable aspect ratios based on the chosen manufacturing process and to design vias accordingly.
Via Hole Impact on Signal Integrity
Via holes can have a significant impact on signal integrity in high-speed PCBs, as they introduce discontinuities in the signal path and can cause reflections, crosstalk, and other parasitic effects. Some of the key signal integrity considerations related to via holes include:
Impedance matching
Vias can cause impedance mismatches in the signal path, leading to reflections and degraded signal quality. To minimize this effect, the via geometry should be designed to match the impedance of the connecting traces as closely as possible. This can involve adjusting the via diameter, the antipad size (the clearance around the via), and the use of via stubs (the unused portion of the via below the target layer).
Via stubs
Via stubs can act as resonant cavities, causing signal reflections and degrading signal quality at high frequencies. To mitigate this effect, designers can use techniques such as back-drilling, where the unused portion of the via is removed by drilling from the back side of the board, or by using blind or buried vias to avoid creating stubs altogether.
Crosstalk
Vias can contribute to crosstalk between adjacent signals, especially when they are placed too close together or when they pass through shared reference planes. To minimize crosstalk, designers can use techniques such as via shielding, where ground vias are placed adjacent to signal vias, or by optimizing via placement and spacing to reduce coupling.
Return path discontinuities
Vias can cause discontinuities in the return path of a signal, leading to increased inductance and degraded signal quality. To maintain a continuous return path, designers should place ground vias adjacent to signal vias and ensure that the reference planes are properly connected by vias where necessary.
Via Hole Reliability Considerations
Via holes are critical to the overall reliability of a PCB, as they are subject to mechanical, thermal, and electrical stresses during the manufacturing process and in operation. Some key reliability considerations for via holes include:
Thermal cycling
PCBs are subject to thermal cycling during the assembly process and in operation, which can cause stress on the via holes due to the different thermal expansion coefficients of the PCB materials and the plated copper. This stress can lead to via cracking or delamination, which can cause electrical failures. To mitigate this risk, designers should use appropriate via fill materials and ensure that the Via plating is of sufficient thickness and quality.
Mechanical stress
Via holes can be subject to mechanical stress during the PCB manufacturing process, particularly during drilling and lamination. This stress can cause via deformation or breakage, leading to electrical failures. To minimize mechanical stress, designers should follow recommended via design guidelines and use appropriate drill parameters and lamination processes.
Electromigration
Electromigration is a phenomenon where the flow of electrical current can cause the gradual migration of metal atoms, leading to the formation of voids or hillocks in the via plating. This can cause increased resistance or even open circuits over time. To mitigate electromigration, designers should ensure that the via plating is of sufficient thickness and that the current density through the vias is kept within acceptable limits.
Solder wicking
During the soldering process, molten solder can wick up into the via holes, causing a reduction in the effective via diameter and potentially leading to electrical failures. To prevent solder wicking, designers can use via fill materials, such as epoxy or non-conductive ink, or apply solder mask over the via holes.
Via Hole Testing and Inspection
To ensure the quality and reliability of via holes, various testing and inspection techniques are employed during the PCB manufacturing process and after assembly. Some common via hole testing and inspection methods include:
Automated Optical Inspection (AOI)
AOI uses cameras and image processing algorithms to inspect the PCB for defects, including via hole issues such as missing or incomplete plating, hole size variations, and misalignment. AOI can quickly scan the entire board and identify potential problems, but it may not detect internal defects or subtle variations.
X-ray Inspection
X-ray inspection uses X-ray imaging to examine the internal structure of the PCB, including the via holes. This technique can detect issues such as voids in the via plating, insufficient plating thickness, or solder wicking. X-ray inspection is particularly useful for examining buried or obscured vias that cannot be easily inspected by other methods.
Electrical Testing
Electrical testing involves applying electrical signals to the PCB and measuring the response to verify proper connectivity and performance. This can include Continuity Testing, where the resistance between connected points is measured to ensure that the via holes are properly plated and connected, and high-voltage testing, where a high voltage is applied to the board to detect any insulation breakdowns or leakage currents.
Microsectioning
Microsectioning is a destructive testing technique where a small cross-section of the PCB is cut and polished to expose the internal structure of the via holes. This allows for detailed examination of the via plating quality, thickness, and uniformity using microscopy techniques. Microsectioning is typically used for failure analysis or quality control purposes on a sample basis.
Frequently Asked Questions (FAQ)
1. What is the difference between a through-hole via and a blind via?
A through-hole via is a hole drilled completely through the PCB, from the top layer to the bottom layer, and is plated to create an electrical connection. A blind via, on the other hand, starts from either the top or bottom layer and terminates at an inner layer, without passing through the entire board thickness.
2. What is the purpose of via filling?
Via filling is the process of filling the via hole with a non-conductive material, such as epoxy, to prevent solder wicking during the assembly process and to provide a flat surface for component mounting. This technique can also improve the mechanical strength and thermal performance of the via.
3. How do vias affect signal integrity in high-speed PCBs?
Vias can introduce discontinuities in the signal path, leading to reflections, crosstalk, and other parasitic effects that can degrade signal quality. To minimize these effects, designers must carefully consider via placement, geometry, and shielding techniques, and use strategies such as impedance matching and stub reduction.
4. What is the difference between electroless and electrolytic copper plating in via holes?
Electroless copper plating is a chemical process that deposits a thin layer of copper onto the walls of the via hole and the surface of the PCB, serving as a conductive seed layer. Electrolytic copper plating is an electrochemical process that uses an electric current to deposit a thicker layer of copper onto the electroless layer, providing the bulk of the via’s conductivity.
5. What is via aspect ratio, and why is it important?
The via aspect ratio is the ratio of the via’s depth to its diameter. High aspect ratio vias, where the depth is much greater than the diameter, can be challenging to manufacture and may suffer from poor plating uniformity or voids. Designers must consider the achievable aspect ratios based on the chosen manufacturing process and design vias accordingly to ensure reliability and performance.
Conclusion
Via holes are essential features in multi-layer PCBs, enabling electrical connections between layers and allowing for more complex and compact circuit designs. Understanding the different types of vias, their manufacturing processes, and the key design considerations is crucial for creating reliable, high-performance PCBs.
When designing via holes, it is important to consider factors such as via size, placement, shielding, and aspect ratio, as well as the potential impact on signal integrity and reliability. By carefully considering these factors and employing appropriate testing and inspection techniques, designers can ensure that their PCBs meet the required performance and reliability standards.
As PCB technology continues to evolve, with increasing demands for higher speeds, greater densities, and more advanced packaging techniques, the role of via holes in enabling these advancements will remain critical. Staying up-to-date with the latest via hole technologies, design strategies, and manufacturing processes will be essential for PCB designers and manufacturers alike in pushing the boundaries of electronic design.
Via Type | Description | Advantages | Disadvantages |
---|---|---|---|
Through-hole | Drilled through the entire board thickness | – Reliable – Good mechanical strength – Suitable for high-power applications |
– Consumes more board space – Limited routing flexibility |
Blind | Starts from the top or bottom layer and terminates at an inner layer | – Allows for higher component density on outer layers – Provides more routing flexibility |
– More complex manufacturing process – Limited to connecting outer layers to inner layers |
Buried | Located entirely within the inner layers | – Enables complex routing – Reduces board size |
– Requires advanced manufacturing techniques – Limited access for testing and inspection |
Micro | Small, high-precision vias created by laser drilling | – Enables fine-pitch connections – Essential for advanced packaging technologies |
– Limited current carrying capacity – Requires specialized manufacturing equipment |
0 Comments