History of PCBs
The concept of printed circuit boards dates back to the early 20th century. In 1903, Albert Hanson, a German inventor, filed a patent for a method of creating conductive pathways on an insulating material. However, it wasn’t until the 1940s that PCBs began to gain widespread use in electronic devices.
During World War II, the demand for compact and reliable electronic equipment for military applications drove the development of PCBs. In 1947, the U.S. Army Signal Corps released a specification for printed wiring boards, which laid the foundation for modern PCB design and manufacturing.
Throughout the 1950s and 1960s, PCBs became increasingly popular in consumer electronics, such as radios and televisions. As electronic devices became more complex and miniaturized, PCBs evolved to accommodate higher component densities and more sophisticated circuit designs.
Types of PCBs
There are several types of printed circuit boards, each with its own unique characteristics and applications:
Single-Layer PCBs
Single-layer PCBs have conductive traces on only one side of the board. They are the simplest and most cost-effective type of PCB, suitable for basic electronic circuits with low component density.
Double-Layer PCBs
Double-layer PCBs have conductive traces on both sides of the board, allowing for more complex circuit designs and higher component density compared to single-layer PCBs. The two layers are connected through drilled holes called vias.
Multi-Layer PCBs
Multi-layer PCBs consist of three or more conductive layers separated by insulating layers. They offer the highest component density and are used in complex electronic devices, such as smartphones, computers, and medical equipment. The layers are interconnected using vias.
Flexible PCBs
Flexible PCBs are made of thin, flexible materials that can bend and twist without damaging the circuit. They are often used in wearable electronics, automotive applications, and devices that require a compact or irregular shape.
Rigid-Flex PCBs
Rigid-flex PCBs combine the benefits of rigid and flexible PCBs. They consist of rigid PCB sections connected by flexible PCB sections, allowing for three-dimensional circuit designs and improved reliability in applications that require both stability and flexibility.
PCB Manufacturing Process
The PCB manufacturing process involves several steps to create a functional printed circuit board:
-
Design: The PCB design is created using specialized software, such as Eagle or Altium Designer. The design includes the component layout, trace routing, and any necessary markings or labels.
-
Printing: The PCB design is printed onto a transparent film or directly onto the PCB substrate using a photoplotter or laser printer.
-
Etching: The printed PCB substrate is coated with a photoresist layer and exposed to UV light through the printed film. The exposed areas of the photoresist are then removed, leaving the desired trace pattern. The board is then immersed in an etching solution, which removes the unwanted copper, leaving only the conductive traces.
-
Drilling: Holes are drilled into the PCB for component leads and vias using a computer-controlled drill.
-
Plating: The drilled holes are plated with a conductive material, typically copper, to create electrical connections between layers in multi-layer PCBs.
-
Solder Mask Application: A solder mask, a protective coating that prevents solder from adhering to unwanted areas, is applied to the PCB surface. The solder mask also provides insulation and protection against environmental factors.
-
Silkscreen: A silkscreen layer is added to the PCB surface to display component labels, logos, and other markings.
-
Surface Finish: A surface finish, such as lead-free hot air solder leveling (HASL), immersion gold, or immersion silver, is applied to the exposed copper traces to prevent oxidation and improve solderability.
-
Assembly: Electronic components are placed onto the PCB and soldered to the corresponding pads, either through manual soldering or automated assembly processes.
-
Testing: The assembled PCB undergoes various tests, including visual inspection, electrical continuity tests, and functional tests, to ensure that it meets the required specifications and functions as intended.
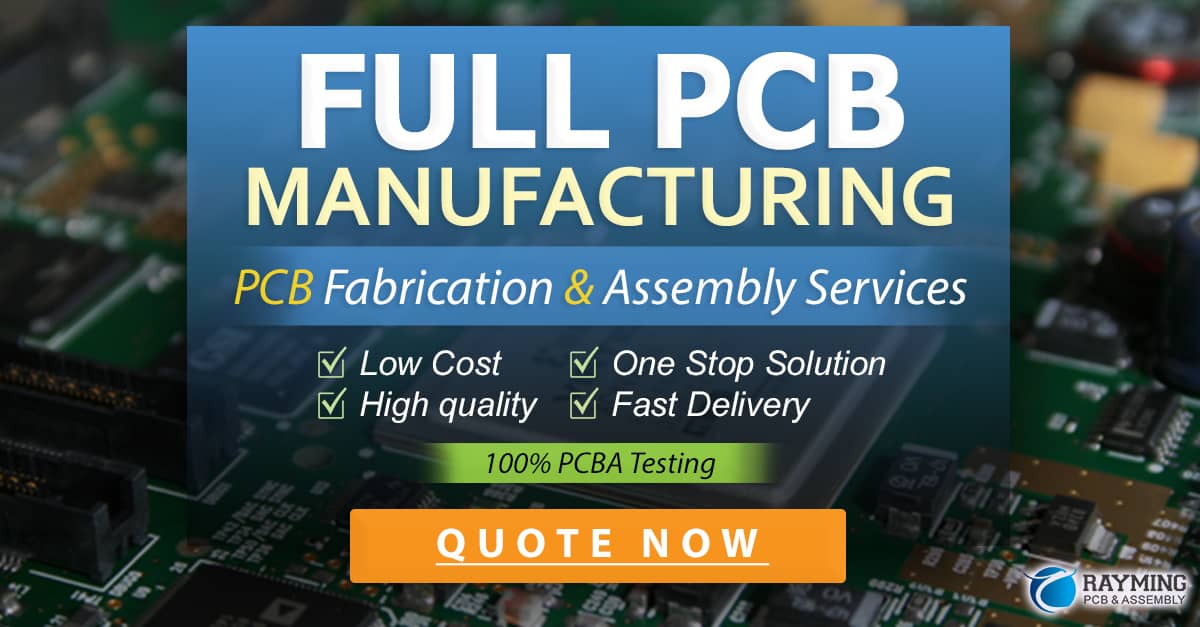
PCB Design Considerations
When designing a printed circuit board, several factors must be taken into account to ensure optimal performance, reliability, and manufacturability:
Component Placement
Components should be placed on the PCB in a logical and efficient manner, considering factors such as signal integrity, thermal management, and mechanical constraints. Proper component placement can minimize signal interference, reduce PCB size, and improve overall system performance.
Trace Routing
Trace routing involves creating the conductive paths that connect components on the PCB. Traces should be designed to minimize signal reflections, crosstalk, and electromagnetic interference (EMI). Factors such as trace width, spacing, and impedance must be carefully considered to ensure signal integrity and compliance with industry standards.
Power and Ground Planes
Power and ground planes are large copper areas on the PCB that provide a low-impedance path for power distribution and grounding. Proper design of power and ground planes is essential for minimizing voltage drops, reducing EMI, and ensuring stable power delivery to components.
Thermal Management
Thermal management is crucial for ensuring the long-term reliability and performance of electronic components. PCB designers must consider factors such as component power dissipation, ambient temperature, and airflow when designing the PCB layout. Techniques such as thermal vias, heatsinks, and proper component spacing can help manage heat and prevent component failure.
Manufacturing Constraints
PCB designers must also consider manufacturing constraints, such as minimum trace widths, spacing, and hole sizes, to ensure that the PCB can be reliably manufactured using standard processes. Designing within these constraints helps to minimize manufacturing defects and reduce production costs.
PCB Testing and Inspection
After the PCB manufacturing process, various testing and inspection methods are employed to ensure the quality and reliability of the final product:
Visual Inspection
Visual inspection is the first step in PCB testing and involves examining the board for any obvious defects, such as missing components, damaged traces, or solder bridges. This inspection can be performed manually or using automated optical inspection (AOI) systems.
Electrical Continuity Testing
Electrical continuity testing verifies that all the necessary electrical connections on the PCB are intact and that there are no short circuits or open connections. This testing is typically performed using a flying probe tester or a Bed-of-Nails Tester.
Functional Testing
Functional testing involves powering up the PCB and verifying that it performs its intended function. This testing may include input/output testing, signal integrity testing, and stress testing under various environmental conditions.
Boundary Scan Testing
Boundary scan testing, also known as JTAG testing, is a method for testing the interconnections between integrated circuits on a PCB. This testing method uses a special test access port (TAP) on the integrated circuits to control and monitor the inputs and outputs of the device, allowing for efficient testing of complex PCBs.
X-Ray Inspection
X-ray inspection is used to examine the internal structure of the PCB, particularly for multi-layer boards and components with hidden solder joints, such as ball grid array (BGA) packages. This non-destructive testing method can detect defects such as voids, cracks, and misaligned components.
Applications of PCBs
Printed circuit boards are used in a wide range of electronic devices and systems, spanning various industries:
Industry | Applications |
---|---|
Consumer Electronics | Smartphones, laptops, televisions, gaming consoles |
Automotive | Engine control units, infotainment systems, sensors |
Medical | Diagnostic equipment, monitoring devices, implantable devices |
Aerospace | Avionics, satellite systems, communication equipment |
Industrial | Process control systems, automation equipment, power electronics |
Military | Communication systems, navigation devices, weapon systems |
IoT and Wearables | Smart home devices, fitness trackers, smartwatches |
As electronic devices continue to evolve and new technologies emerge, the demand for high-quality, reliable PCBs will continue to grow. Advancements in PCB design and manufacturing, such as the use of advanced materials, embedded components, and 3D printing, will enable the development of even more complex and compact electronic systems.
FAQ
-
What is the difference between a PCB and a breadboard?
A breadboard is a prototyping tool used to build and test electronic circuits without the need for soldering. It consists of a plastic board with rows of interconnected sockets that allow components to be easily inserted and removed. In contrast, a PCB is a permanent, custom-designed board with etched conductive traces that interconnect electronic components through soldering. -
Can PCBs be recycled?
Yes, PCBs can be recycled. However, due to the complex mix of materials used in PCBs, including metals, plastics, and fiberglass, the recycling process is more complicated than recycling other materials. Specialized recycling facilities use various methods, such as mechanical separation, chemical processing, and thermal treatment, to recover valuable materials from PCBs, such as copper, gold, and silver. -
What is the difference between through-hole and surface-mount components?
Through-hole components have long leads that are inserted into drilled holes on the PCB and soldered to pads on the opposite side of the board. Surface-mount components, on the other hand, have small leads or pads that are soldered directly onto the surface of the PCB. Surface-mount components are generally smaller and allow for higher component density compared to through-hole components. -
What is the role of a solder mask on a PCB?
A solder mask is a protective coating applied to the surface of a PCB, covering the conductive traces while leaving the pads and other areas that require soldering exposed. The solder mask serves several purposes, including: - Preventing solder from adhering to unwanted areas during the soldering process
- Providing insulation between adjacent conductive traces
- Protecting the PCB from environmental factors, such as moisture and dust
-
Improving the aesthetic appearance of the PCB by providing a uniform color (often green or red)
-
What are vias in a PCB, and what is their purpose?
Vias are small holes drilled through a PCB that allow electrical connections between different layers of the board. They are used to route signals and power between components on different layers of a multi-layer PCB. There are several types of vias: - Through vias: These vias go through all layers of the PCB, connecting the top and bottom layers.
- Blind vias: These vias connect an outer layer to an inner layer but do not go through the entire board.
- Buried vias: These vias connect two or more inner layers but do not reach the outer layers of the PCB.
Vias are essential for creating compact, high-density PCB designs, as they allow for efficient use of board space and enable complex routing of signals and power.
Conclusion
Printed circuit boards are the foundation of modern electronic devices, providing a reliable and efficient means of interconnecting electronic components. From simple single-layer boards to complex multi-layer designs, PCBs have enabled the development of increasingly sophisticated and compact electronic systems.
As technology advances, the demand for high-quality, reliable PCBs will continue to grow. PCB designers and manufacturers must stay up-to-date with the latest design techniques, materials, and manufacturing processes to meet the evolving needs of the electronics industry.
By understanding the fundamentals of PCBs, including their history, types, manufacturing processes, and design considerations, engineers and enthusiasts can create innovative electronic devices that push the boundaries of what is possible.
0 Comments