Introduction to PCB Through Holes
Printed Circuit Boards (PCBs) are essential components in modern electronics, providing a platform for mounting and connecting various electronic components. One of the key features of PCBs is the presence of through holes, which play a crucial role in the assembly and functionality of electronic devices. In this article, we will delve into the world of PCB through holes, exploring their types, manufacturing processes, advantages, and applications.
What are PCB Through Holes?
PCB through holes, also known as Plated Through Holes (PTHs), are small holes drilled through the layers of a PCB to create electrical connections between different layers or to allow the insertion of component leads. These holes are typically plated with a conductive material, such as copper, to ensure reliable electrical connectivity.
Types of PCB Through Holes
There are several types of through holes used in PCB design and manufacturing:
-
Standard Through Holes: These are the most common type of through holes, used for mounting and connecting through-hole components. They are drilled through all layers of the PCB and plated with copper.
-
Blind Vias: Blind vias are through holes that start from one surface of the PCB and terminate at an inner layer, without reaching the opposite surface. They are used to create connections between the surface and inner layers.
-
Buried Vias: Buried vias are through holes that connect inner layers of the PCB without reaching either surface. They are used to create connections between internal layers, providing more routing options and reducing the overall size of the PCB.
-
Microvias: Microvias are small-diameter through holes, typically less than 0.15mm in diameter. They are used in high-density PCB designs to create fine-pitch connections and to minimize the area occupied by the holes.
Manufacturing Process of PCB Through Holes
The manufacturing process of PCB through holes involves several steps to ensure precision, reliability, and conductivity. Let’s explore each step in detail:
1. Drilling
The first step in creating through holes is drilling. The PCB is placed on a specialized drilling machine equipped with high-speed drill bits. The machine reads the drill file, which contains information about the hole sizes and locations, and accurately drills the holes through the designated layers of the PCB.
2. Deburring and Cleaning
After drilling, the PCB undergoes a deburring process to remove any rough edges or debris around the holes. This step is crucial to ensure proper plating adhesion and to prevent short circuits. The PCB is then thoroughly cleaned to remove any contaminants or dust particles.
3. Electroless Copper Deposition
To make the through holes conductive, a thin layer of copper is deposited onto the hole walls using an electroless plating process. This process involves immersing the PCB in a copper solution that contains a reducing agent. The copper ions in the solution are attracted to the hole walls and form a uniform layer of copper.
4. Electroplating
After the electroless copper deposition, the PCB undergoes an electroplating process to increase the thickness of the copper layer inside the through holes. The PCB is placed in an electrolytic bath containing copper sulfate solution, and an electric current is applied. The copper ions in the solution are attracted to the cathode (the PCB) and deposit onto the hole walls, forming a thicker and more conductive layer.
5. Solder Mask Application
Once the through holes are plated, a solder mask is applied to the PCB surface. The solder mask is a protective layer that covers the copper traces and prevents solder from adhering to unintended areas during the soldering process. The solder mask is usually applied using screen printing or photoimaging techniques.
6. Surface Finish
The final step in the manufacturing process is the application of a surface finish to the exposed copper areas, including the through holes. The surface finish protects the copper from oxidation and enhances the solderability of the PCB. Common surface finishes include Hot Air Solder Leveling (HASL), Electroless Nickel Immersion Gold (ENIG), and Immersion Silver.
Advantages of PCB Through Holes
PCB through holes offer several advantages in electronic design and manufacturing:
-
Reliable Electrical Connections: Through holes provide a secure and reliable means of connecting components and different layers of the PCB. The plated copper ensures low resistance and high conductivity, minimizing signal loss and improving overall circuit performance.
-
Mechanical Stability: Through-hole components are inserted into the holes and soldered in place, providing a strong mechanical connection. This stability is particularly important in applications that are subject to vibration or physical stress.
-
Compatibility with Through-Hole Components: Many electronic components, such as connectors, switches, and some types of capacitors and resistors, are available in through-hole packages. PCB through holes allow for the easy mounting and connection of these components.
-
Simplified Assembly: Through-hole components are easier to handle and insert manually compared to surface-mount components. This simplifies the assembly process, especially for low-volume production or prototyping.
-
Heat Dissipation: Through holes can act as thermal vias, providing a path for heat to dissipate from components to the PCB substrate or other layers. This helps in managing the thermal performance of the PCB and prevents overheating of components.
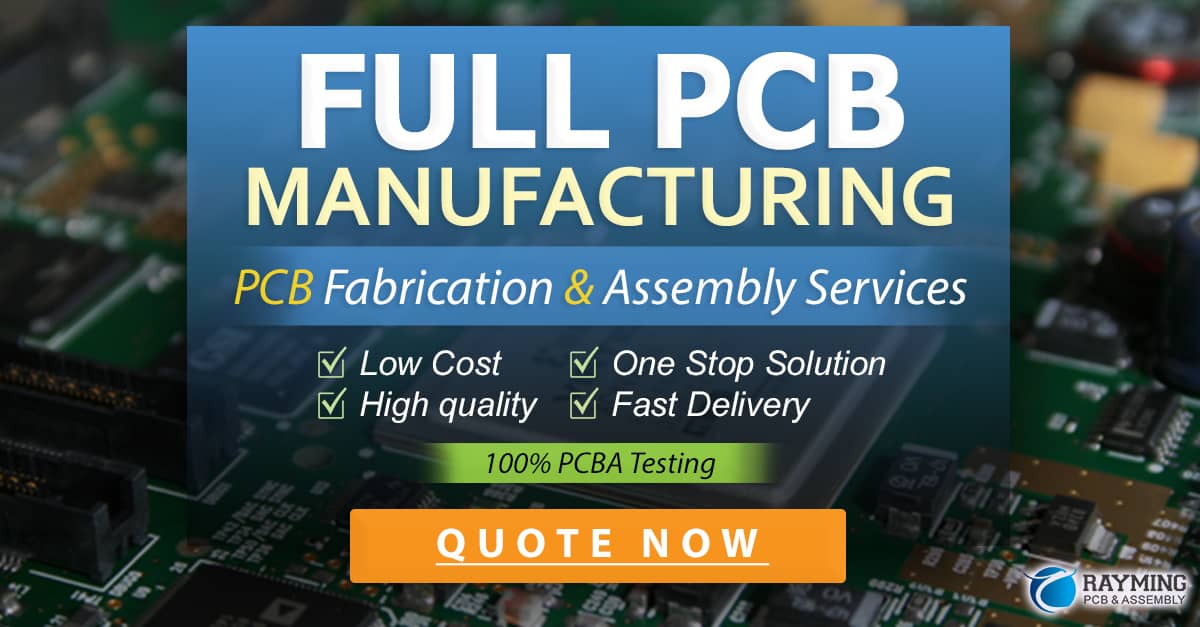
Applications of PCB Through Holes
PCB through holes find applications in various industries and electronic products:
-
Consumer Electronics: Through holes are commonly used in consumer electronic devices, such as smartphones, tablets, laptops, and home appliances. They provide reliable connections for components like connectors, switches, and audio jacks.
-
Industrial Electronics: In industrial settings, PCBs with through holes are used in control systems, sensors, and communication devices. The robust mechanical stability provided by through holes is essential in harsh environments.
-
Automotive Electronics: Through holes are used in Automotive PCBs for applications like engine control units, infotainment systems, and safety features. The ability to withstand vibration and temperature variations is crucial in automotive electronics.
-
Medical Devices: Medical equipment, such as patient monitors, diagnostic devices, and imaging systems, relies on PCBs with through holes for reliable and safe operation. The use of through holes ensures secure connections and minimizes the risk of device failure.
-
Aerospace and Defense: In aerospace and defense applications, PCBs with through holes are used in avionics, communication systems, and military equipment. The high reliability and durability provided by through holes are essential in these critical applications.
Frequently Asked Questions (FAQ)
-
What is the difference between through holes and vias?
Through holes are drilled through all layers of the PCB and are used for mounting and connecting components. Vias, on the other hand, are used to create electrical connections between different layers of the PCB and may not necessarily go through all layers (e.g., blind and buried vias). -
Can through holes be used for surface-mount components?
While through holes are primarily used for through-hole components, they can be used in combination with surface-mount components. This is known as a mixed-technology PCB, where both through-hole and surface-mount components are used on the same board. -
What is the minimum diameter of a through hole?
The minimum diameter of a through hole depends on the PCB manufacturing capabilities and the specific requirements of the design. Typically, the minimum diameter ranges from 0.2mm to 0.5mm, but smaller diameters (microvias) can be achieved using advanced manufacturing techniques. -
How does the aspect ratio affect through hole plating?
The aspect ratio of a through hole is the ratio of its depth to its diameter. Higher aspect ratios (deeper and narrower holes) can be challenging to plate uniformly. PCB Manufacturers specify maximum aspect ratios for reliable plating, typically in the range of 8:1 to 10:1. -
What is the purpose of solder mask on through holes?
The solder mask applied to the PCB surface helps to prevent solder from adhering to unintended areas during the soldering process. It also provides insulation and protection for the copper traces. In the case of through holes, the solder mask ensures that solder only flows into the holes and does not bridge adjacent pads or traces.
Conclusion
PCB through holes are a fundamental aspect of PCB design and manufacturing, enabling reliable electrical connections and component mounting. Understanding the types of through holes, their manufacturing process, advantages, and applications is essential for anyone involved in electronic product development.
From standard through holes to microvias, each type serves a specific purpose in PCB design. The manufacturing process, involving drilling, plating, and surface finishing, ensures the quality and functionality of the through holes.
Through holes offer advantages such as reliable electrical connections, mechanical stability, compatibility with through-hole components, simplified assembly, and heat dissipation. They find applications in various industries, including consumer electronics, industrial electronics, automotive, medical devices, aerospace, and defense.
As PCB technology continues to advance, innovations in through hole design and manufacturing will drive the development of more compact, high-performance, and reliable electronic devices. By mastering the concepts and techniques related to PCB through holes, designers and manufacturers can creATE PCBs that meet the ever-increasing demands of modern electronics.
0 Comments