Why Use Blind Vias in PCB Design?
There are several reasons why blind vias are used in PCB design:
1. Space Savings
One of the main advantages of using blind vias is that they save space on the PCB. Since blind vias do not go all the way through the board, they free up space on the outer layers for components and other features. This is especially important in high-density designs where board real estate is at a premium.
2. Improved Signal Integrity
Blind vias can also improve signal integrity in high-speed designs. By reducing the length of the interconnect, blind vias minimize the parasitic capacitance and inductance that can degrade signal quality. This is particularly important in applications such as high-speed digital circuits, RF circuits, and mixed-signal designs.
3. Increased Routing Flexibility
Blind vias provide increased routing flexibility by allowing designers to route signals on inner layers of the PCB. This can be useful in situations where there is limited space on the outer layers or where certain signals need to be isolated from others to reduce crosstalk and interference.
4. Better Thermal Management
Blind vias can also be used for thermal management in high-power designs. By connecting to inner layers that are dedicated to heat dissipation, blind vias can help transfer heat away from components and prevent overheating.
Types of Blind Vias
There are two main types of blind vias:
-
Blind Via: A blind via starts at an outer layer and terminates at an inner layer, as described above.
-
Buried Via: A buried via connects two or more inner layers without being visible on either outer layer. Buried vias are typically used in conjunction with blind vias to create complex interconnects between multiple layers.
Here is a table comparing the characteristics of blind and buried vias:
Characteristic | Blind Via | Buried Via |
---|---|---|
Starts at | Outer layer | Inner layer |
Terminates at | Inner layer | Inner layer |
Visible on | One outer layer | Neither outer layer |
Typical uses | Space savings, signal integrity, routing | Complex interconnects between multiple layers |
Manufacturing Process for Blind Vias
The manufacturing process for blind vias is more complex than for through-hole vias and requires specialized equipment and techniques. Here is a general overview of the process:
-
Drilling: The first step is to drill the blind via holes using a laser or mechanical drill. The depth of the hole is carefully controlled to ensure that it terminates at the desired inner layer.
-
Plating: Next, the holes are plated with a conductive material, typically copper, to create an electrical connection between the outer layer and the inner layer. This is done using electroless or electrolytic plating processes.
-
Filling: After plating, the blind via holes are filled with a non-conductive material, such as epoxy resin, to provide structural support and prevent contamination. The filling process is typically done using a screen printing or vacuum lamination technique.
-
Capping: Finally, the outer layer of the PCB is capped with a thin layer of copper to cover the blind via and create a smooth surface for further processing, such as solder mask application and component assembly.
Here is a table summarizing the key steps in the blind via manufacturing process:
Step | Description |
---|---|
Drilling | Drill blind via holes using laser or mechanical drill |
Plating | Plate holes with conductive material to create electrical connection |
Filling | Fill holes with non-conductive material for structural support |
Capping | Cap outer layer with thin layer of copper for smooth surface |
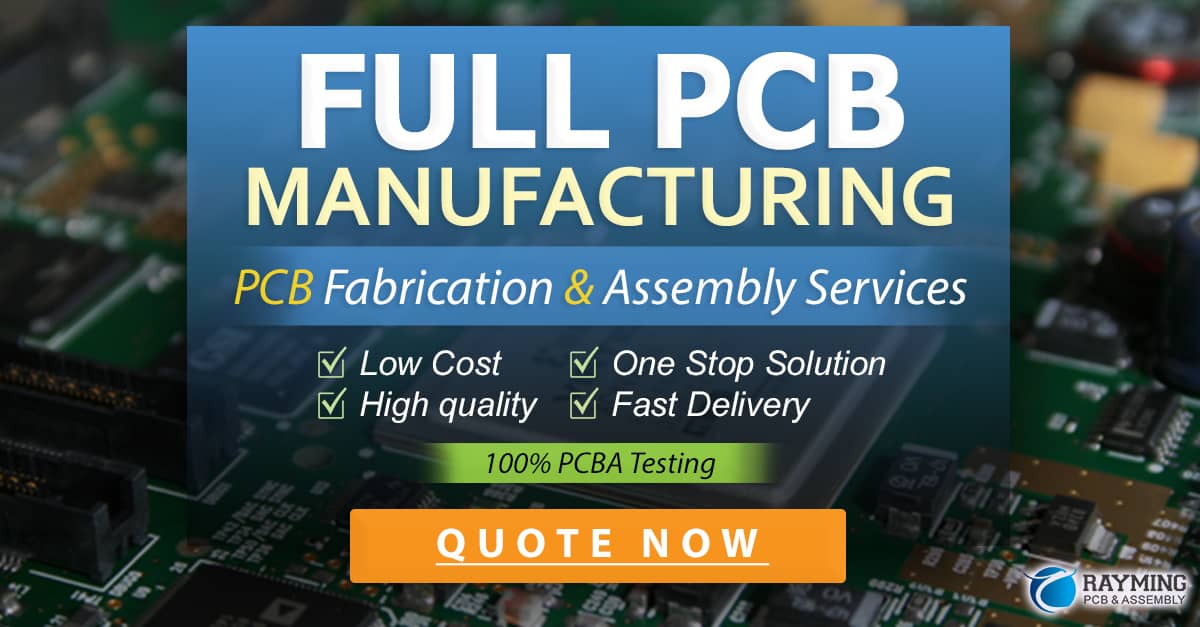
Design Considerations for Blind Vias
When designing PCBs with blind vias, there are several important considerations to keep in mind:
1. Via Size and Spacing
The size and spacing of blind vias are critical parameters that affect the manufacturability and reliability of the PCB. The minimum via size and spacing are determined by the capabilities of the manufacturing process and the design rules for the specific PCB fabricator. Designers must ensure that the via size and spacing meet these requirements to avoid manufacturing defects and reliability issues.
2. Layer Stack-Up
The layer stack-up of the PCB must be carefully designed to accommodate blind vias. The number and arrangement of layers, as well as the thickness of each layer, will affect the depth and placement of blind vias. Designers must work closely with the PCB fabricator to ensure that the layer stack-up is optimized for the specific design requirements.
3. Via Positioning
The positioning of blind vias on the PCB is also important for ensuring proper functionality and reliability. Blind vias should be placed as close as possible to the components they are connecting to minimize the length of the interconnect and reduce parasitic effects. However, designers must also ensure that there is sufficient clearance between vias and other features on the board to avoid short circuits and other defects.
4. Cost Considerations
Finally, designers must consider the cost implications of using blind vias in their PCB designs. Because the manufacturing process for blind vias is more complex and requires specialized equipment, the cost of fabricating PCBs with blind vias is typically higher than for standard through-hole designs. Designers must weigh the benefits of using blind vias against the added cost and determine whether the improved performance and space savings justify the expense.
Frequently Asked Questions (FAQ)
-
What is the difference between a blind via and a buried via?
A blind via starts at an outer layer and terminates at an inner layer, while a buried via connects two or more inner layers without being visible on either outer layer. -
What are the advantages of using blind vias in PCB design?
The main advantages of using blind vias are space savings, improved signal integrity, increased routing flexibility, and better thermal management. -
What is the manufacturing process for blind vias?
The manufacturing process for blind vias involves drilling the via holes, plating them with a conductive material, filling them with a non-conductive material, and capping the outer layer with a thin layer of copper. -
What are some important design considerations for blind vias?
Important design considerations for blind vias include via size and spacing, layer stack-up, via positioning, and cost. -
Are blind vias more expensive than through-hole vias?
Yes, the manufacturing process for blind vias is more complex and requires specialized equipment, making them more expensive than standard through-hole vias. Designers must weigh the benefits of using blind vias against the added cost.
Conclusion
Blind vias are an important interconnect technology used in modern PCB designs to save space, improve signal integrity, increase routing flexibility, and enhance thermal management. By understanding the different types of blind vias, their manufacturing process, and key design considerations, PCB designers can effectively incorporate blind vias into their designs to achieve optimal performance and reliability. While blind vias come with added cost and complexity compared to standard through-hole vias, their benefits make them an essential tool in the designer’s toolkit for creating high-density, high-performance electronic products.
0 Comments