Key PCB Cost Factors
The main factors that determine the cost of PCB fabrication and assembly include:
- Board Size and Complexity
- Number of Layers
- Material Selection
- Surface Finish
- Quantity and Turnaround Time
- Component Sourcing and Assembly
Let’s dive deeper into each of these factors and how they influence PCB costs.
1. Board Size and Complexity
The size and complexity of your PCB design play a significant role in determining the fabrication cost. Larger boards require more material and may be more challenging to manufacture, leading to higher costs. Additionally, complex designs with intricate traces, tight tolerances, and high-density layouts can increase the fabrication cost due to the need for advanced manufacturing techniques and specialized equipment.
Board Size | Relative Cost |
---|---|
Small (< 50 cm²) | Low |
Medium (50-200 cm²) | Medium |
Large (> 200 cm²) | High |
2. Number of Layers
The number of layers in your PCB directly impacts the fabrication cost. Each additional layer requires more material, processing time, and labor, resulting in higher costs. However, using multiple layers can also help reduce the overall board size and improve signal integrity, which may be necessary for certain applications.
Number of Layers | Relative Cost |
---|---|
1-2 | Low |
4-6 | Medium |
8+ | High |
3. Material Selection
The choice of PCB material affects both the performance and cost of your board. The most common PCB materials are:
- FR-4: A cost-effective, general-purpose material suitable for most applications.
- High-Tg FR-4: Offers better thermal stability and performance than standard FR-4, but at a higher cost.
- Polyimide: Provides excellent thermal stability and flexibility, ideal for high-temperature applications, but comes at a premium price.
- Aluminum: Used for metal-core PCBs (MCPCBs) to enhance thermal dissipation, but is more expensive than FR-4.
Material | Relative Cost |
---|---|
FR-4 | Low |
High-Tg FR-4 | Medium |
Polyimide | High |
Aluminum | High |
4. Surface Finish
The surface finish on your PCB not only protects the copper traces from oxidation but also affects the solderability and assembly process. Common surface finishes include:
- HASL (Hot Air Solder Leveling): A cost-effective, lead-free option suitable for most applications.
- ENIG (Electroless Nickel Immersion Gold): Offers excellent solderability and durability, but at a higher cost than HASL.
- OSP (Organic Solderability Preservative): A low-cost, lead-free option that provides temporary protection against oxidation.
- Immersion Silver: Provides good solderability and is a cost-effective alternative to ENIG.
Surface Finish | Relative Cost |
---|---|
OSP | Low |
HASL | Low |
Immersion Silver | Medium |
ENIG | High |
5. Quantity and Turnaround Time
The quantity of PCBs you order and the required turnaround time significantly influence the cost per unit. Larger quantities often result in lower per-unit costs due to economies of scale, as the fixed costs of setup and tooling are spread across more boards. Rush orders with shorter turnaround times may incur additional fees, as they require prioritization and may disrupt the manufacturer’s standard production schedule.
Quantity | Relative Cost per Unit |
---|---|
Low (< 100) | High |
Medium (100-1000) | Medium |
High (> 1000) | Low |
6. Component Sourcing and Assembly
The cost of components and the complexity of the assembly process also contribute to the overall cost of your PCB. Some factors to consider include:
- Component availability and lead times
- Component packaging (e.g., through-hole, surface mount)
- Manual vs. automated assembly
- Specialized assembly requirements (e.g., BGA, fine-pitch components)
Partnering with an experienced PCB assembly provider can help you navigate these factors and find cost-effective solutions for your project.
Frequently Asked Questions (FAQ)
-
Q: How can I reduce the cost of my PCB fabrication and assembly?
A: To reduce PCB costs, consider optimizing your design for manufacturability, using standard materials and components, ordering larger quantities, and allowing for longer turnaround times when possible. -
Q: What is the most cost-effective PCB material for general-purpose applications?
A: FR-4 is the most cost-effective and widely used PCB material for general-purpose applications. It offers good mechanical and electrical properties at a relatively low cost. -
Q: How does the number of layers affect the cost and performance of a PCB?
A: Increasing the number of layers in a PCB results in higher fabrication costs, as each additional layer requires more material and processing. However, using more layers can help reduce the overall board size, improve signal integrity, and accommodate more complex designs. -
Q: What is the difference between HASL and ENIG surface finishes, and which one is more cost-effective?
A: HASL (Hot Air Solder Leveling) is a cost-effective, lead-free surface finish suitable for most applications. ENIG (Electroless Nickel Immersion Gold) offers better solderability and durability but comes at a higher cost. The choice between the two depends on your specific requirements and budget. -
Q: How can I ensure the quality and reliability of my PCB while keeping costs under control?
A: To ensure PCB quality and reliability while managing costs, work with a reputable PCB fabrication and assembly provider that follows industry standards and best practices. Clearly communicate your requirements, and consider implementing quality control measures such as design reviews, inspections, and testing throughout the production process.
Conclusion
Understanding the factors that determine the cost of PCB fabrication and assembly is essential for making informed decisions and optimizing your PCB design and production process. By carefully considering board size and complexity, number of layers, material selection, surface finish, quantity and turnaround time, and component sourcing and assembly, you can balance cost, performance, and reliability to achieve the best results for your project.
When selecting a PCB fabrication and assembly partner, look for a provider with a proven track record of delivering high-quality PCBs while offering competitive pricing and support throughout the production process. By working closely with your chosen provider and staying informed about the latest industry trends and best practices, you can ensure the success of your PCB project while keeping costs under control.
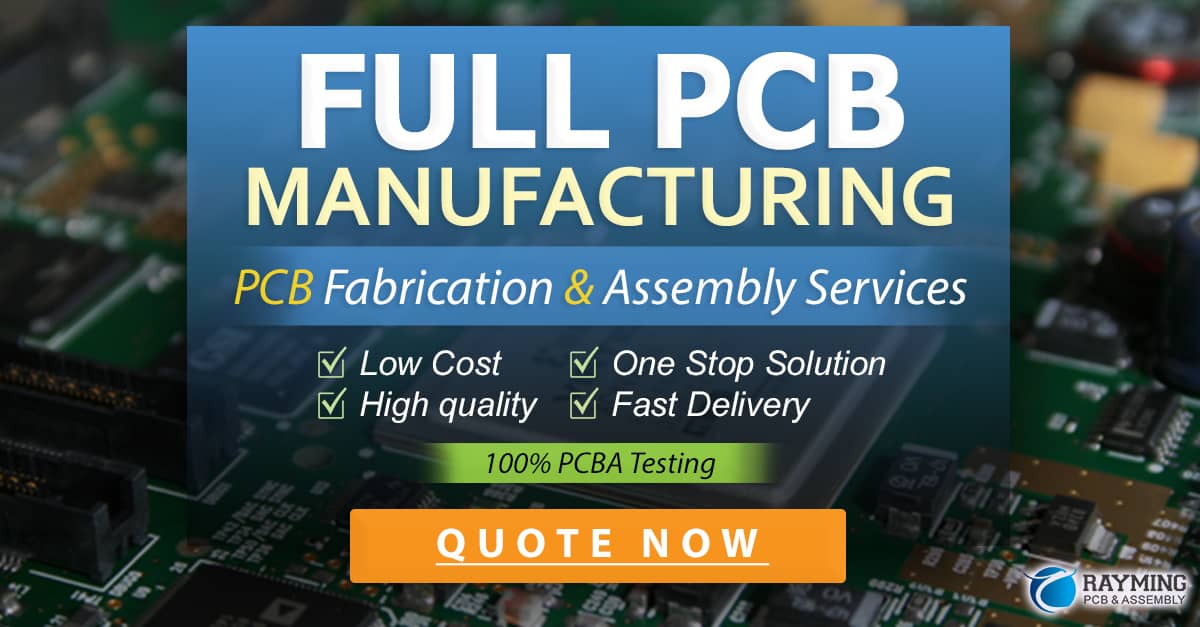
0 Comments