Introduction to PCB Mechanical Layers
Printed Circuit Boards (PCBs) are essential components in modern electronics. They provide a platform for mounting and interconnecting electronic components, allowing for the creation of complex circuits in a compact and organized manner. While the primary focus of PCB design is often on the electrical aspects, such as component placement and routing, mechanical layers play a crucial role in ensuring the overall functionality, reliability, and manufacturability of the board.
What are Mechanical Layers?
Mechanical layers in a PCB are non-conductive layers that serve structural and informational purposes. These layers do not carry electrical signals but rather provide mechanical support, protection, and guidance during the manufacturing process and assembly of the PCB.
Mechanical layers are typically added to the PCB design to convey important information to the manufacturing team, such as the board outline, drilling locations, component placement, and assembly instructions. They help ensure that the PCB is fabricated and assembled correctly, meeting the desired specifications and requirements.
Types of PCB Mechanical Layers
There are several types of mechanical layers commonly used in PCB design. Each layer serves a specific purpose and contributes to the overall functionality and manufacturability of the board. Let’s explore some of the most common mechanical layers:
1. Board Outline Layer
The board outline layer, also known as the PCB outline layer or mechanical 1 layer, defines the physical shape and size of the PCB. It specifies the outer perimeter of the board, including any cutouts, notches, or irregular shapes. This layer acts as a guide for the PCB manufacturer to cut the board to the desired dimensions.
The board outline layer is typically drawn using a solid line in the PCB design software. It is essential to ensure that the outline is accurate and follows the required specifications, as any discrepancies can lead to manufacturing issues or incompatibility with the intended enclosure or mounting requirements.
2. Drill Layer
The drill layer, also referred to as the drill drawing or mechanical 2 layer, contains information about the location, size, and type of holes to be drilled in the PCB. These holes serve various purposes, such as mounting components, providing electrical connections between layers (vias), or allowing for mechanical fastening.
The drill layer specifies the coordinates and diameters of each hole on the PCB. It also includes information about the type of hole, such as through holes, Blind Vias, or Buried Vias. The drill layer is used by the PCB manufacturer to create the necessary holes in the board using specialized drilling equipment.
3. Silkscreen Layer
The silkscreen layer, also known as the legend or overlay, is a non-conductive layer that contains textual and graphical information printed on the surface of the PCB. This layer is used to provide visual indicators, labels, and instructions for assembly and troubleshooting purposes.
Common elements found on the silkscreen layer include:
– Component designators (e.g., R1, C2, U3)
– Component outlines and polarity markers
– Logo and branding information
– Test points and Fiducial Markers
– Assembly instructions or warnings
The silkscreen layer is typically printed using white or black ink on the top and/or bottom surfaces of the PCB. It is important to ensure that the silkscreen information is legible, properly aligned, and does not interfere with the soldering or assembly process.
4. Solder Mask Layer
The solder mask layer, also known as the solder resist or solder stop layer, is a non-conductive coating applied to the copper traces and pads on the PCB. Its primary purpose is to protect the copper from oxidation and prevent Solder Bridges or short circuits during the soldering process.
The solder mask layer is typically applied as a liquid photoimageable polymer that is exposed and developed to create openings for the pads and holes where soldering will occur. The solder mask layer also provides electrical insulation between adjacent traces and pads, improving the reliability and performance of the PCB.
In addition to its protective function, the solder mask layer also serves an aesthetic purpose. It is available in various colors, with green being the most common. The choice of solder mask color can be based on visual preferences, industry standards, or specific requirements such as high-contrast for better visibility or UV resistance for outdoor applications.
5. Fabrication Drawing Layer
The fabrication drawing layer, also known as the fab drawing or mechanical 3 layer, contains detailed information about the PCB manufacturing process. This layer includes specifications, notes, and instructions for the PCB manufacturer to ensure that the board is fabricated correctly.
Some of the information commonly found in the fabrication drawing layer includes:
– Material specifications (e.g., PCB substrate, copper weight)
– Layer stackup information
– Finishing requirements (e.g., surface plating, soldermask color)
– Tolerances and dimensions
– Special instructions or requirements
The fabrication drawing layer is typically not included in the final PCB but is used by the manufacturer during the fabrication process. It is essential to provide clear and accurate information in this layer to avoid manufacturing errors and ensure the desired quality and specifications are met.
Importance of PCB Mechanical Layers
Mechanical layers in PCB design serve several critical functions that contribute to the overall success of the electronic product. Let’s explore some of the key reasons why mechanical layers are important:
1. Manufacturing Accuracy
Mechanical layers provide essential information to the PCB manufacturer, ensuring that the board is fabricated accurately according to the desired specifications. The board outline layer defines the physical shape and size of the PCB, while the drill layer specifies the location and size of holes. These layers guide the manufacturing process, reducing the chances of errors and inconsistencies.
Without accurate mechanical layers, the PCB manufacturer may face challenges in producing boards that meet the required dimensions, hole placements, and tolerances. This can lead to issues such as improper fit in the enclosure, misaligned components, or difficulty in assembly.
2. Assembly and Soldering
The silkscreen layer and solder mask layer play crucial roles in the assembly and soldering process of PCBs. The silkscreen layer provides visual guidance for component placement, polarity, and orientation. It helps the assembly team correctly position components on the board, reducing the likelihood of assembly errors.
The solder mask layer, on the other hand, protects the copper traces and pads from oxidation and prevents solder bridges or short circuits during the soldering process. It ensures that solder only adheres to the exposed pads and holes, creating reliable electrical connections.
Without these mechanical layers, the assembly process would be more challenging and prone to errors, leading to potential functionality issues or even damage to the components or the board itself.
3. Communication and Documentation
Mechanical layers serve as a means of communication between the PCB designer, manufacturer, and assembly team. They provide a common language and understanding of the board’s physical characteristics, requirements, and instructions.
The fabrication drawing layer, in particular, contains detailed information about the PCB manufacturing process, including material specifications, layer stackup, and special instructions. This layer acts as a comprehensive guide for the manufacturer, ensuring that all necessary information is conveyed and understood.
Clear and accurate mechanical layers help streamline the communication process, reducing the chances of misinterpretation or miscommunication. They also serve as documentation for future reference, troubleshooting, or modifications.
4. Quality and Reliability
The use of appropriate mechanical layers contributes to the overall quality and reliability of the PCB. By providing accurate and detailed information, mechanical layers help ensure that the board is manufactured and assembled to the desired standards.
For example, the drill layer specifies the precise location and size of holes, ensuring proper electrical connections and mechanical stability. The solder mask layer protects the copper traces from damage and prevents short circuits, enhancing the board’s reliability and longevity.
Mechanical layers also help in identifying and resolving potential issues early in the design and manufacturing process. By reviewing and verifying the mechanical layers, designers and manufacturers can catch and address any discrepancies or errors before the board goes into production, saving time and resources.
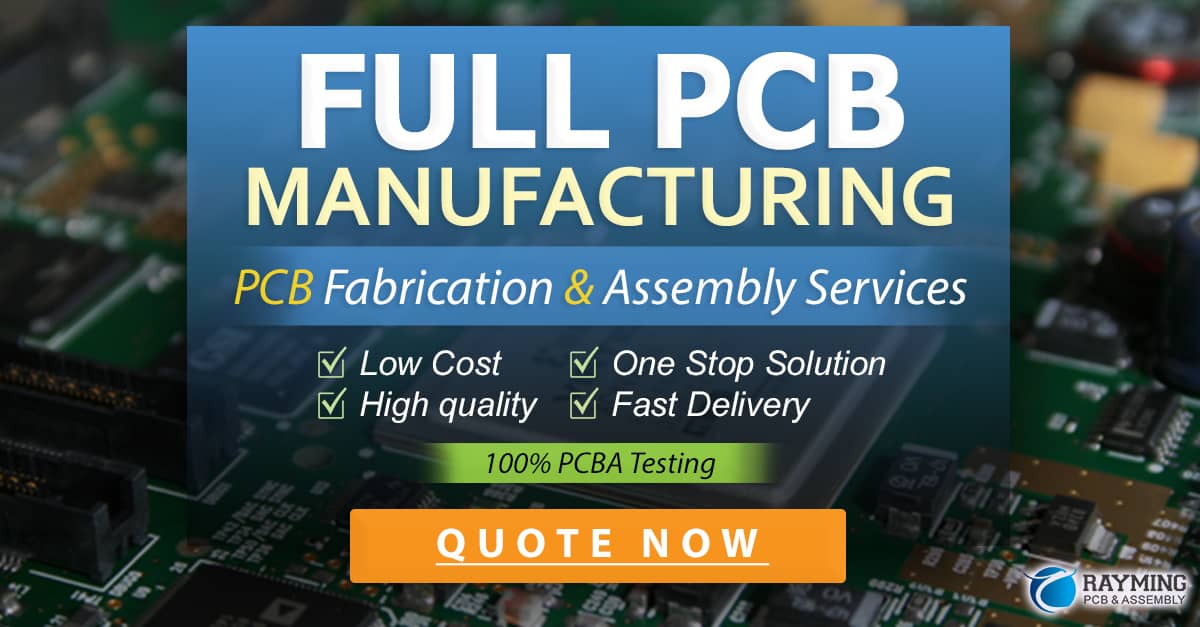
Best Practices for PCB Mechanical Layers
To ensure the effectiveness and accuracy of mechanical layers in PCB design, it is important to follow certain best practices. Here are some key considerations:
1. Adhere to Design Guidelines
When creating mechanical layers, it is crucial to adhere to the design guidelines provided by the PCB manufacturer or industry standards. These guidelines specify recommended practices for layer creation, such as minimum line widths, clearances, and tolerances.
Following the design guidelines helps ensure that the mechanical layers are compatible with the manufacturing processes and equipment. It reduces the chances of manufacturing issues or delays due to non-conforming designs.
2. Use Appropriate Software Tools
Using appropriate PCB design software tools can greatly simplify the creation and management of mechanical layers. These tools often provide dedicated features and libraries for mechanical layer creation, such as automatic board outline generation, hole sizing, and silkscreen placement.
PCB design software also offers design rule checking (DRC) capabilities, which help validate the mechanical layers against predefined rules and constraints. DRC tools can identify potential issues such as insufficient clearances, overlapping elements, or missing information, allowing designers to catch and resolve problems early in the design process.
3. Maintain Consistency and Clarity
Consistency and clarity are essential when creating mechanical layers. Use clear and concise labeling, and follow a consistent naming convention for layers, components, and other elements. This helps avoid confusion and ensures that all stakeholders involved in the PCB manufacturing and assembly process can easily understand and interpret the mechanical layers.
When creating the silkscreen layer, ensure that the text and graphics are legible and properly aligned. Use appropriate font sizes and styles, and consider the limitations of the silkscreen printing process, such as minimum line widths and spacing.
4. Collaborate and Communicate
Effective collaboration and communication among the PCB design team, manufacturers, and assembly partners are crucial for the successful implementation of mechanical layers. Engage in open and frequent communication to clarify requirements, address concerns, and ensure that all parties are aligned.
Provide detailed documentation and instructions along with the mechanical layers to minimize the chances of misinterpretation or errors. Seek feedback from the manufacturing and assembly teams to identify any potential issues or improvements that can be made to the mechanical layers.
5. Perform Thorough Reviews and Verification
Before finalizing the mechanical layers and sending them for manufacturing, perform thorough reviews and verification. Check the layers for accuracy, completeness, and conformance to design guidelines and requirements.
Use design rule checking tools to validate the mechanical layers and identify any potential issues. Conduct visual inspections to ensure that all elements are properly placed and aligned.
Consider generating 3D models or rendered images of the PCB based on the mechanical layers to visualize the final board and catch any potential issues related to component placement, clearances, or mechanical interferences.
FAQ
1. What is the purpose of the board outline layer in PCB design?
The board outline layer, also known as the PCB outline layer or mechanical 1 layer, defines the physical shape and size of the PCB. It specifies the outer perimeter of the board, including any cutouts, notches, or irregular shapes. This layer acts as a guide for the PCB manufacturer to cut the board to the desired dimensions.
2. What information is included in the drill layer of a PCB?
The drill layer, also referred to as the drill drawing or mechanical 2 layer, contains information about the location, size, and type of holes to be drilled in the PCB. It specifies the coordinates and diameters of each hole on the board and includes information about the type of hole, such as through holes, blind vias, or buried vias. The drill layer is used by the PCB manufacturer to create the necessary holes in the board using specialized drilling equipment.
3. What is the purpose of the silkscreen layer in PCB design?
The silkscreen layer, also known as the legend or overlay, is a non-conductive layer that contains textual and graphical information printed on the surface of the PCB. It provides visual indicators, labels, and instructions for assembly and troubleshooting purposes. Common elements found on the silkscreen layer include component designators, component outlines and polarity markers, logo and branding information, test points, and fiducial markers.
4. Why is the solder mask layer important in PCB manufacturing?
The solder mask layer, also known as the solder resist or solder stop layer, is a non-conductive coating applied to the copper traces and pads on the PCB. Its primary purpose is to protect the copper from oxidation and prevent solder bridges or short circuits during the soldering process. The solder mask layer also provides electrical insulation between adjacent traces and pads, improving the reliability and performance of the PCB.
5. What are some best practices for creating mechanical layers in PCB design?
Some best practices for creating mechanical layers in PCB design include:
– Adhering to design guidelines provided by the PCB manufacturer or industry standards.
– Using appropriATE PCB design software tools that offer dedicated features and libraries for mechanical layer creation.
– Maintaining consistency and clarity in labeling, naming conventions, and visual elements.
– Collaborating and communicating effectively with the PCB design team, manufacturers, and assembly partners.
– Performing thorough reviews and verification of the mechanical layers before finalizing and sending them for manufacturing.
Conclusion
Mechanical layers in PCB design play a vital role in ensuring the proper manufacturing, assembly, and functionality of printed circuit boards. These non-conductive layers provide essential information and guidance for the physical aspects of the board, including its shape, size, holes, and visual indicators.
By understanding the different types of mechanical layers, such as the board outline layer, drill layer, silkscreen layer, solder mask layer, and fabrication drawing layer, PCB designers can effectively communicate the board’s requirements and specifications to the manufacturing and assembly teams.
The importance of mechanical layers cannot be overstated. They contribute to manufacturing accuracy, facilitate proper assembly and soldering, serve as a means of communication and documentation, and ultimately impact the quality and reliability of the final product.
To create effective and accurate mechanical layers, PCB designers should follow best practices such as adhering to design guidelines, using appropriate software tools, maintaining consistency and clarity, collaborating and communicating effectively, and performing thorough reviews and verification.
By giving due attention to mechanical layers in PCB design, designers can streamline the manufacturing process, reduce the chances of errors and issues, and ensure the successful realization of their electronic products.
0 Comments