Characteristics of Heavy Copper PCBs
Increased Copper Thickness
The defining characteristic of Heavy Copper PCBs is the increased thickness of the copper traces. While standard PCBs typically have copper thicknesses ranging from 1 oz to 3 oz per square foot (35 µm to 105 µm), Heavy Copper PCBs can have copper thicknesses of 4 oz to 20 oz per square foot (140 µm to 700 µm) or even higher in some cases. This increased copper thickness allows for higher current carrying capacity and better heat dissipation.
Copper Thickness | Standard PCB | Heavy Copper PCB |
---|---|---|
1 oz/sq. ft. | ✓ | |
2 oz/sq. ft. | ✓ | |
3 oz/sq. ft. | ✓ | |
4 oz/sq. ft. | ✓ | |
6 oz/sq. ft. | ✓ | |
8 oz/sq. ft. | ✓ | |
10 oz/sq. ft. | ✓ | |
12 oz/sq. ft. | ✓ | |
20 oz/sq. ft. | ✓ |
Improved Current Carrying Capacity
The thicker copper traces in Heavy Copper PCBs allow for higher current carrying capacity compared to standard PCBs. This is particularly important in power electronics, where high currents need to be efficiently transferred without causing excessive heating or voltage drops. The increased cross-sectional area of the copper traces reduces resistance, enabling the PCB to handle higher currents without compromising performance or reliability.
Enhanced Thermal Management
Heavy Copper PCBs offer superior thermal management properties due to the increased copper thickness. Copper is an excellent conductor of heat, and the thicker traces allow for better heat dissipation from high-power components. This helps to prevent hotspots and thermal stress on the PCB, improving the overall reliability and longevity of the electronic device.
Mechanical Stability
The increased copper thickness also contributes to the mechanical stability of Heavy Copper PCBs. Thicker copper traces provide a more robust structure, reducing the likelihood of warping or deformation during the manufacturing process or in high-stress applications. This enhanced mechanical stability is particularly valuable in industries such as automotive, aerospace, and military, where PCBs are subjected to harsh environments and vibrations.
Manufacturing Process of Heavy Copper PCBs
Substrate Selection
The manufacturing process of Heavy Copper PCBs begins with the selection of an appropriate substrate material. The substrate must be able to withstand the high temperatures and pressures involved in the lamination process, as well as provide adequate insulation and mechanical support. Common substrate materials for Heavy Copper PCBs include FR-4, high-temperature FR-4, polyimide, and ceramic.
Copper Foil Lamination
Once the substrate is selected, the next step is to laminate the thick copper foil onto the substrate. This process involves placing the copper foil and substrate layers in a lamination press, where they are subjected to high temperature and pressure. The lamination process ensures a strong bond between the copper foil and the substrate, creating a stable foundation for the subsequent manufacturing steps.
Patterning and Etching
After lamination, the Heavy Copper PCB undergoes patterning and etching processes to create the desired circuit layout. The patterning process involves applying a photoresist layer onto the copper foil and exposing it to UV light through a photomask. The exposed areas of the photoresist are then developed, leaving the desired circuit pattern protected.
The etching process removes the unwanted copper from the unprotected areas, leaving only the desired circuit traces. Due to the increased copper thickness, the etching process for Heavy Copper PCBs requires specialized equipment and longer etching times compared to standard PCBs.
Drilling and Plating
Once the circuit pattern is etched, the next step is to drill holes for through-hole components and vias. The drilling process for Heavy Copper PCBs requires high-quality drill bits and precise control to ensure clean and accurate holes. After drilling, the holes are plated with copper to establish electrical connectivity between layers.
Solder Mask and Silkscreen
The final steps in the manufacturing process involve applying a solder mask and silkscreen to the Heavy Copper PCB. The solder mask is a protective layer that covers the copper traces, leaving only the exposed pads for soldering components. The silkscreen is a printed layer that provides text, symbols, and labels for easy identification of components and connectors.
Applications of Heavy Copper PCBs
Power Electronics
Heavy Copper PCBs find extensive use in power electronics applications, where high currents and efficient power delivery are critical. Some common applications include:
- Power supplies
- Inverters
- Motor drives
- Battery management systems
- Renewable energy systems (solar and wind)
The increased current carrying capacity and thermal management properties of Heavy Copper PCBs make them ideal for handling the high power demands in these applications.
Automotive Electronics
The automotive industry relies on Heavy Copper PCBs for various electronic systems, such as:
- Engine control units (ECUs)
- Power distribution modules
- Electric vehicle charging systems
- Hybrid and electric vehicle battery packs
- Lighting systems
The mechanical stability and reliability of Heavy Copper PCBs are crucial in the automotive sector, where electronic components are subjected to harsh environments, vibrations, and temperature fluctuations.
Aerospace and Defense
Heavy Copper PCBs are used in aerospace and defense applications that require high reliability and performance under extreme conditions. Some examples include:
- Avionics systems
- Radar and communication equipment
- Satellite systems
- Military vehicles and weapons systems
The enhanced thermal management and mechanical stability of Heavy Copper PCBs make them suitable for the demanding requirements of aerospace and defense applications.
Industrial Automation and Control
In industrial automation and control systems, Heavy Copper PCBs are used for:
- Motor control systems
- Power distribution boards
- Programmable logic controllers (PLCs)
- Industrial sensors and actuators
The high current handling capability and robust construction of Heavy Copper PCBs ensure reliable operation in industrial environments, where electromagnetic interference (EMI) and harsh conditions are common.
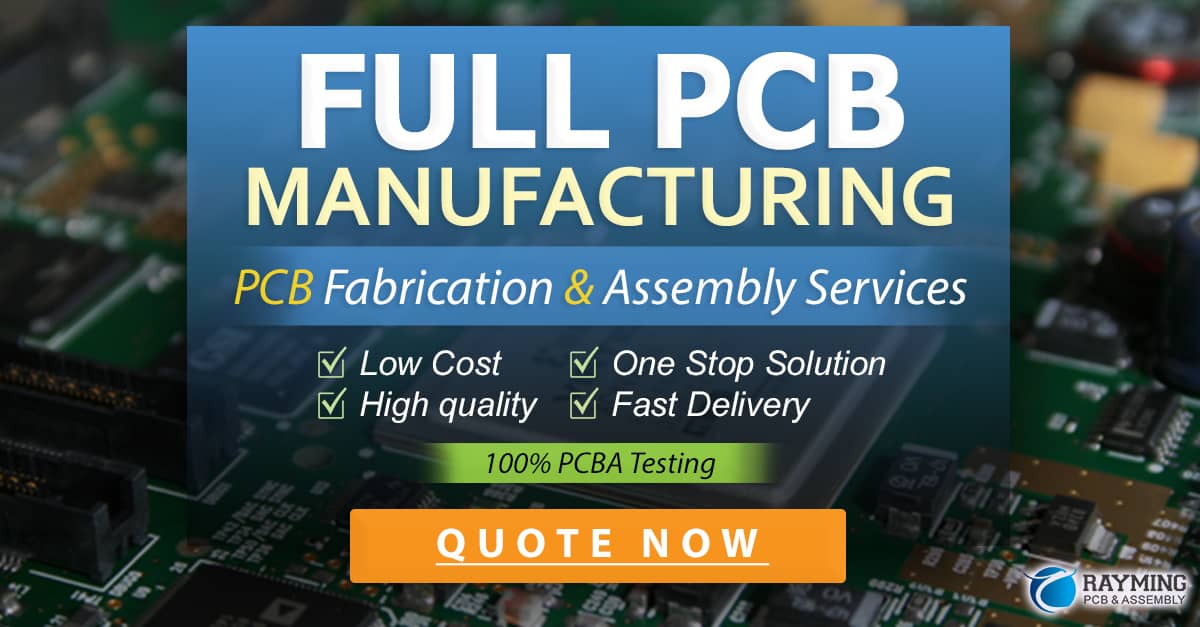
Frequently Asked Questions (FAQ)
1. What is the difference between Heavy Copper PCBs and standard PCBs?
The main difference between Heavy Copper PCBs and standard PCBs lies in the thickness of the copper traces. Heavy Copper PCBs have significantly thicker copper traces, typically ranging from 4 oz to 20 oz per square foot, compared to the 1 oz to 3 oz per square foot found in standard PCBs. This increased copper thickness enables Heavy Copper PCBs to handle higher currents, provide better thermal management, and offer enhanced mechanical stability.
2. What are the benefits of using Heavy Copper PCBs?
The benefits of using Heavy Copper PCBs include:
– Higher current carrying capacity
– Improved thermal management and heat dissipation
– Enhanced mechanical stability and resistance to warping
– Better performance in high-power and high-stress applications
– Increased reliability and longevity of electronic devices
3. What industries commonly use Heavy Copper PCBs?
Heavy Copper PCBs are commonly used in industries that require high-power electronics, reliable performance, and robustness. These industries include:
– Power electronics
– Automotive
– Aerospace and defense
– Industrial automation and control
– Renewable energy
4. Are Heavy Copper PCBs more expensive than standard PCBs?
Yes, Heavy Copper PCBs are generally more expensive than standard PCBs. The increased copper thickness and specialized manufacturing processes involved in producing Heavy Copper PCBs contribute to the higher cost. However, the improved performance, reliability, and longevity offered by Heavy Copper PCBs often justify the additional expense in applications where high power handling and robustness are critical.
5. Can Heavy Copper PCBs be manufactured with multiple layers?
Yes, Heavy Copper PCBs can be manufactured with multiple layers, just like standard PCBs. Multi-layer Heavy Copper PCBs offer the benefits of increased copper thickness combined with the advantages of multi-layer design, such as higher component density, better signal integrity, and improved EMI shielding. However, the manufacturing process for multi-layer Heavy Copper PCBs is more complex and requires specialized equipment and expertise.
Conclusion
Heavy Copper PCBs are specialized printed circuit boards designed to handle high currents, provide better thermal management, and offer increased mechanical stability. With copper thicknesses ranging from 4 oz to 20 oz per square foot or higher, Heavy Copper PCBs find applications in power electronics, automotive, aerospace, defense, industrial automation, and renewable energy sectors.
The manufacturing process of Heavy Copper PCBs involves careful substrate selection, copper foil lamination, patterning, etching, drilling, plating, and the application of solder mask and silkscreen. While more expensive than standard PCBs, the improved performance and reliability of Heavy Copper PCBs make them an essential component in high-power and high-stress applications.
As technology continues to advance and the demand for high-performance electronics grows, Heavy Copper PCBs will play an increasingly important role in enabling the development of reliable, efficient, and robust electronic systems across various industries.
0 Comments