What are Vias and Traces?
Before we delve into the details of PCB Conductivity, let’s define what vias and traces are:
Vias
Vias are small holes drilled through a PCB to connect different layers of the board electrically. They allow signals and power to pass from one layer to another, enabling more complex routing and more efficient use of board space. Vias come in various types, which we will discuss later in this article.
Traces
Traces are the conductive pathways that carry electrical signals and power between components on a PCB. They are typically made of copper and are etched onto the surface of the board. The width, thickness, and spacing of traces can significantly impact the conductivity and performance of the PCB.
Factors Affecting PCB Conductivity
Several factors influence the conductivity of a PCB, particularly in relation to vias and traces. Let’s explore these factors in more detail:
Material Properties
The conductivity of a PCB is primarily determined by the materials used in its construction. The most common materials for PCB Fabrication are:
-
Copper: Copper is the most widely used conductor in PCBs due to its excellent electrical conductivity, thermal conductivity, and mechanical properties. The thickness of the copper layer, measured in ounces per square foot (oz/ft²), directly affects the conductivity of traces and vias.
-
Substrates: The substrate, or the insulating material between copper layers, also plays a role in PCB conductivity. Common substrates include FR-4, Rogers, and Polyimide. The dielectric constant and loss tangent of the substrate material can affect signal integrity and power loss.
Trace Geometry
The geometry of traces, including their width, thickness, and spacing, has a significant impact on PCB conductivity:
-
Width: Wider traces have lower resistance and can carry more current, resulting in better conductivity. However, wider traces also occupy more space on the board, which can limit routing options.
-
Thickness: Thicker traces have lower resistance and higher current-carrying capacity. PCB Manufacturers typically offer copper thicknesses ranging from 0.5 oz/ft² to 4 oz/ft², with 1 oz/ft² being the most common.
-
Spacing: The spacing between traces, known as the trace pitch, affects both conductivity and signal integrity. Closely spaced traces can lead to crosstalk and other signal integrity issues, while wider spacing can improve conductivity at the cost of board space.
Via Types and Properties
Vias come in several types, each with its own characteristics and impact on PCB conductivity:
-
Through-hole Vias: These vias go through the entire thickness of the board, connecting all layers. They offer excellent mechanical strength and conductivity but consume more board space and can be more challenging to manufacture.
-
Blind Vias: Blind vias connect an outer layer to an inner layer, but do not go through the entire board. They offer improved routing flexibility and can save board space, but are more expensive to manufacture.
-
Buried Vias: Buried vias connect inner layers of the board without being visible on the outer layers. They provide even more routing flexibility but are the most expensive and complex to manufacture.
-
Microvias: Microvias are small, laser-drilled vias that can connect adjacent layers or skip layers. They are commonly used in high-density interconnect (HDI) PCBs and offer excellent space savings and routing flexibility.
The size and plating of vias also affect their conductivity:
-
Via Diameter: Larger vias have lower resistance and can carry more current, but they also consume more board space. A balance must be struck between conductivity and routing density.
-
Via Plating: Vias are typically plated with copper to improve their conductivity. The plating thickness and quality can significantly impact the overall conductivity of the via.
Optimizing PCB Conductivity
To optimize the conductivity of your PCB, consider the following tips:
-
Choose the right copper thickness: Select a copper thickness that meets your current-carrying requirements while minimizing costs and manufacturing complexity.
-
Optimize trace geometry: Use wider traces for high-current paths and critical signals, and ensure adequate spacing between traces to minimize crosstalk and signal integrity issues.
-
Select appropriate via types: Use through-hole vias for mechanical strength and high-current applications, while leveraging blind, buried, and microvias for improved routing flexibility and space savings.
-
Consider via size and plating: Choose via sizes that balance conductivity and routing density, and ensure proper plating thickness for optimal performance.
-
Use appropriate substrate materials: Select substrate materials with suitable dielectric properties for your application, considering factors such as frequency, signal integrity, and power loss.
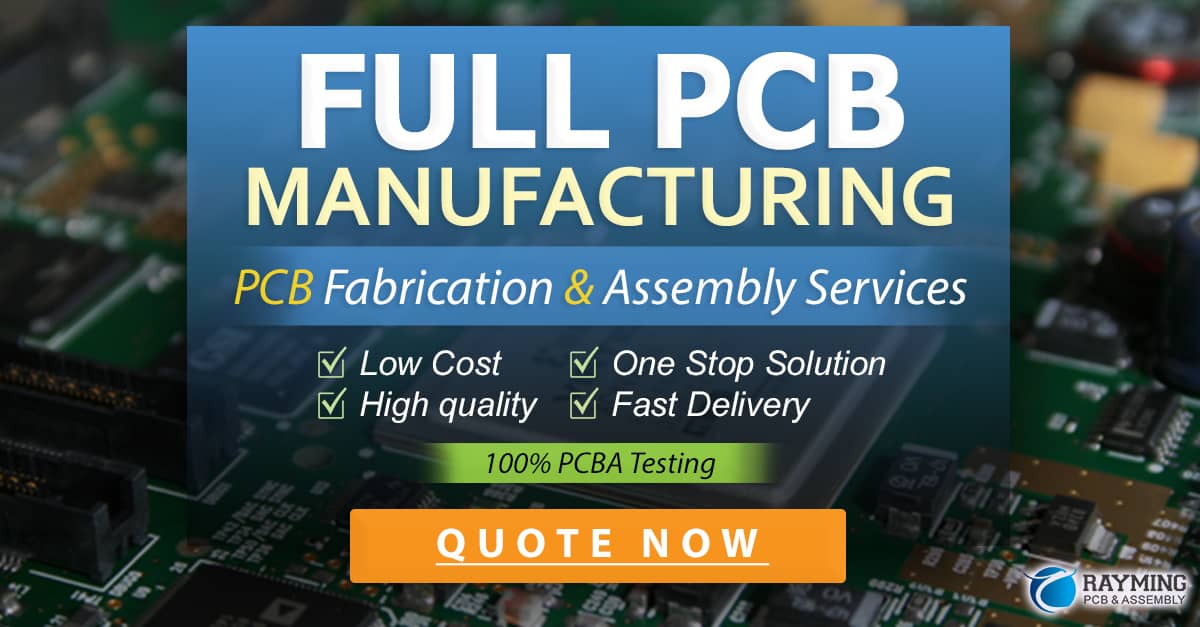
PCB Conductivity Simulation and Testing
To ensure optimal conductivity and performance, it is essential to simulate and test your PCB design before manufacturing:
Simulation Tools
PCB design software, such as Altium Designer, Cadence Allegro, and Mentor Graphics PADS, offer built-in simulation tools to analyze conductivity, signal integrity, and power integrity. These tools can help you optimize your design by identifying potential issues and suggesting improvements.
Testing Methods
Once your PCB is manufactured, several testing methods can be used to verify its conductivity and performance:
-
Continuity Testing: This test verifies that all connections on the board are intact and that there are no open circuits. It is typically performed using a multimeter or a dedicated continuity tester.
-
Resistance Testing: Resistance testing measures the resistance of traces and vias, ensuring that they meet the specified design requirements. This can be done using a multimeter or a four-wire Kelvin resistance tester for more accurate results.
-
High-Potential (HiPot) Testing: HiPot Testing applies a high voltage between conductors to ensure that the insulation between them can withstand the specified voltage without breaking down. This test is critical for ensuring the safety and reliability of the PCB.
-
Time-Domain Reflectometry (TDR): TDR testing uses high-frequency signals to measure the impedance and integrity of traces, helping to identify issues such as discontinuities, impedance mismatches, and signal reflections.
Frequently Asked Questions (FAQ)
-
Q: What is the difference between a via and a trace?
A: A via is a small hole drilled through a PCB to connect different layers electrically, while a trace is a conductive pathway that carries electrical signals and power between components on the same layer of the board. -
Q: How does copper thickness affect PCB conductivity?
A: Thicker copper layers have lower resistance and higher current-carrying capacity, resulting in better conductivity. PCB manufacturers typically offer copper thicknesses ranging from 0.5 oz/ft² to 4 oz/ft², with 1 oz/ft² being the most common. -
Q: What are the different types of vias, and how do they impact PCB conductivity?
A: The main types of vias are through-hole, blind, buried, and microvias. Through-hole vias offer excellent mechanical strength and conductivity but consume more board space. Blind, buried, and microvias provide improved routing flexibility and space savings but can be more expensive to manufacture. -
Q: How can I optimize the conductivity of my PCB design?
A: To optimize PCB conductivity, choose the right copper thickness, optimize trace geometry, select appropriate via types and sizes, ensure proper via plating, and use suitable substrate materials. Additionally, leverage simulation tools and testing methods to verify and improve your design. -
Q: What testing methods are used to verify PCB conductivity and performance?
A: Common testing methods for PCB conductivity and performance include continuity testing, resistance testing, high-potential (HiPot) testing, and time-domain reflectometry (TDR) testing. These tests help identify issues such as open circuits, inadequate conductor resistance, insulation breakdowns, and signal integrity problems.
Conclusion
Vias and traces are essential components of PCB design, playing a crucial role in the conductivity and overall performance of the board. By understanding the factors that influence PCB conductivity, such as material properties, trace geometry, and via types, designers can optimize their designs for maximum efficiency and reliability.
Leveraging simulation tools and thorough testing methods further ensures that the PCB will meet the specified requirements and perform as expected in the final application. As electronics continue to advance and become more complex, the importance of optimizing PCB conductivity through proper via and trace design will only continue to grow.
0 Comments