Classification Based on Number of Layers
1. Single Layer PCB
Single layer PCBs, also known as Single-sided PCBs, have conductive traces on only one side of the substrate. The components are mounted on the same side as the traces. These PCBs are the simplest and most cost-effective to manufacture.
Advantages
- Low cost
- Easy to design and manufacture
- Suitable for simple circuits
Applications
- Simple electronic devices
- Low-frequency applications
- Prototyping
2. Double Layer PCB
Double layer PCBs have conductive traces on both sides of the substrate. The two layers are connected using vias (conductive holes). These PCBs offer better circuit density and signal integrity compared to single layer PCBs.
Advantages
- Improved circuit density
- Better signal integrity
- Suitable for more complex circuits
Applications
- Consumer electronics
- Telecommunications equipment
- Industrial control systems
3. Multi-Layer PCB
Multi-layer PCBs have three or more conductive layers separated by insulating layers. The layers are interconnected using vias. These PCBs offer the highest circuit density and best signal integrity among all types of PCBs.
Advantages
- High circuit density
- Excellent signal integrity
- Reduced electromagnetic interference (EMI)
Applications
- High-speed digital devices
- Aerospace and defense systems
- Medical equipment
Classification Based on Rigidity
1. Rigid PCB
Rigid PCBs are made using a solid substrate material, typically FR-4 (a glass-reinforced epoxy laminate). They maintain their shape and do not flex under normal conditions. Rigid PCBs are the most common type used in electronic devices.
Advantages
- Excellent mechanical stability
- Good heat dissipation
- Suitable for high-density circuits
Applications
- Computers and servers
- Automotive electronics
- Industrial automation systems
2. Flexible PCB
Flexible PCBs (FPCBs) are made using a flexible substrate material, such as polyimide or polyester. They can bend and flex without damaging the circuits. FPCBs are ideal for applications that require the PCB to conform to a specific shape or withstand repeated flexing.
Advantages
- Flexibility and bendability
- Lightweight and thin
- Reduced assembly costs
Applications
- Wearable devices
- Medical implants
- Aerospace and military equipment
3. Rigid-flex PCB
Rigid-flex PCBs combine the benefits of both rigid and flexible PCBs. They consist of rigid PCB sections connected by flexible PCB sections. This allows for three-dimensional packaging and improved reliability in applications that require both stability and flexibility.
Advantages
- 3D packaging capability
- Improved reliability
- Reduced weight and size
Applications
- Smartphones and tablets
- Aerospace and defense systems
- Medical devices
Classification Based on Material
1. FR-4 PCB
FR-4 (Flame Retardant 4) is the most commonly used PCB substrate material. It is a glass-reinforced epoxy laminate that offers excellent mechanical and electrical properties. FR-4 PCBs are suitable for a wide range of applications and are cost-effective.
Advantages
- Good mechanical strength
- Excellent electrical insulation
- Flame retardant properties
Applications
- Consumer electronics
- Industrial control systems
- Telecommunications equipment
2. Aluminum PCB
Aluminum PCBs use an aluminum substrate instead of the traditional FR-4. The aluminum substrate provides excellent thermal conductivity, making these PCBs ideal for applications that generate significant heat.
Advantages
- Excellent thermal conductivity
- Lightweight
- Good mechanical stability
Applications
- High-power LED lighting
- Automotive electronics
- Power electronics
3. Ceramic PCB
Ceramic PCBs use a ceramic substrate, typically alumina (Al2O3) or aluminum nitride (AlN). They offer excellent thermal conductivity, high-temperature resistance, and low dielectric loss. Ceramic PCBs are used in high-frequency and high-power applications.
Advantages
- Excellent thermal conductivity
- High-temperature resistance
- Low dielectric loss
Applications
- RF and microwave devices
- High-power laser diodes
- Aerospace and defense systems
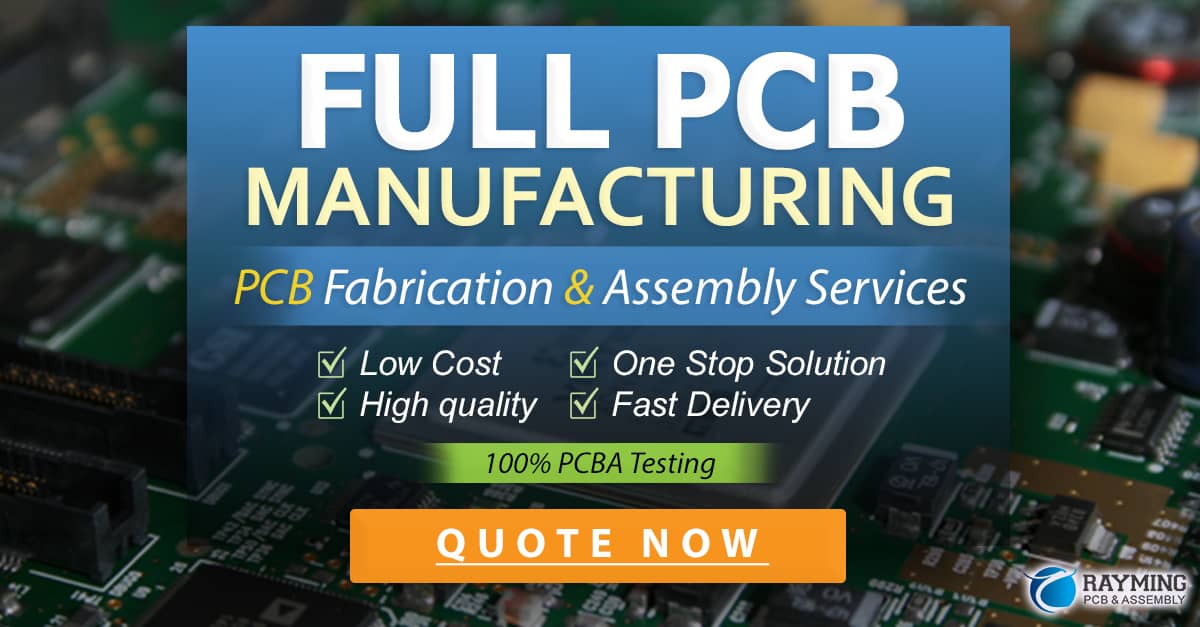
Classification Based on Manufacturing Technology
1. Through-Hole Technology (THT) PCB
THT PCBs have component leads inserted through drilled holes in the board and soldered on the opposite side. This technology is older but still used for components that require high mechanical strength or are not available in surface-mount packages.
Advantages
- Strong mechanical connections
- Suitable for high-power components
- Easy to assemble and repair
Applications
- Power electronics
- High-reliability systems
- Prototyping
2. Surface-Mount Technology (SMT) PCB
SMT PCBs have components mounted directly onto the surface of the board without through-holes. This technology allows for smaller components, higher circuit density, and automated assembly processes.
Advantages
- Higher component density
- Smaller board size
- Faster assembly processes
Applications
- Consumer electronics
- Telecommunications equipment
- Automotive electronics
3. Mixed Technology PCB
Mixed technology PCBs combine both THT and SMT components on the same board. This allows for the best of both worlds, with THT components providing mechanical strength and SMT components enabling high density and automated assembly.
Advantages
- Combines benefits of THT and SMT
- Suitable for complex designs
- Provides design flexibility
Applications
- Industrial control systems
- Medical devices
- Aerospace and defense systems
PCB Types Comparison Table
PCB Type | Layers | Rigidity | Material | Manufacturing Technology |
---|---|---|---|---|
Single Layer PCB | 1 | Rigid | FR-4 | THT, SMT |
Double Layer PCB | 2 | Rigid | FR-4 | THT, SMT |
Multi-Layer PCB | 3+ | Rigid | FR-4 | THT, SMT |
Flexible PCB | 1-2 | Flexible | Polyimide, Polyester | SMT |
Rigid-Flex PCB | 2+ | Rigid-Flexible | FR-4, Polyimide | THT, SMT |
Aluminum PCB | 1-2 | Rigid | Aluminum | SMT |
Ceramic PCB | 1-2 | Rigid | Alumina, Aluminum Nitride | THT, SMT |
Frequently Asked Questions (FAQ)
1. What is the most common type of PCB?
The most common type of PCB is the FR-4 rigid PCB, which is used in a wide range of electronic devices due to its good mechanical and electrical properties, as well as its cost-effectiveness.
2. What are the advantages of using a multi-layer PCB?
Multi-layer PCBs offer several advantages, including high circuit density, excellent signal integrity, and reduced electromagnetic interference (EMI). They are suitable for complex, high-speed digital devices and systems.
3. When should I choose a flexible PCB over a rigid PCB?
Flexible PCBs are ideal for applications that require the PCB to conform to a specific shape or withstand repeated flexing. They are commonly used in wearable devices, medical implants, and aerospace and military equipment.
4. What are the benefits of using an aluminum PCB?
Aluminum PCBs provide excellent thermal conductivity, making them suitable for applications that generate significant heat, such as high-power LED lighting and automotive electronics. They are also lightweight and offer good mechanical stability.
5. Can SMT and THT components be used on the same PCB?
Yes, mixed technology PCBs combine both THT and SMT components on the same board. This allows for the best of both worlds, with THT components providing mechanical strength and SMT components enabling high density and automated assembly.
In conclusion, the vast array of PCB types available today caters to the diverse needs of the electronics industry. By understanding the characteristics, advantages, and applications of each PCB type, designers and engineers can select the most suitable option for their projects. As technology continues to advance, we can expect to see further innovations in PCB design and manufacturing, enabling even more compact, high-performance electronic devices.
0 Comments