Introduction to PCB-Mounting Techniques
When it comes to designing and manufacturing printed circuit boards (PCBs), one of the crucial decisions to make is choosing the right mounting method for components. The two primary PCB-mounting techniques are through hole and surface mount. Each method has its own advantages and disadvantages, and selecting the appropriate technique depends on various factors such as the application, component availability, manufacturing capabilities, and cost.
In this article, we will dive deep into the world of through hole and surface mount technologies, exploring their characteristics, benefits, and drawbacks. We will also provide guidance on how to choose the right mounting method for your specific project.
What is Through Hole Mounting?
Through hole mounting, also known as through hole technology (THT), is a traditional PCB-mounting method where component leads are inserted through drilled holes in the PCB and soldered onto pads on the opposite side of the board. This technique has been widely used since the early days of PCB manufacturing and is still relevant in certain applications today.
Advantages of Through Hole Mounting
-
Mechanical Strength: Through hole components provide excellent mechanical strength and stability due to the leads being physically inserted through the board and soldered on the opposite side. This makes through hole mounting ideal for applications that require high durability and resistance to vibration or shock.
-
Ease of Manual Assembly: Through hole components are easier to handle and manually solder compared to surface mount components. This makes through hole mounting suitable for prototyping, low-volume production, or hobby projects where manual assembly is preferred.
-
Compatibility with High-Power Components: Through hole mounting is often used for high-power components such as transformers, large capacitors, and power transistors. These components generate significant heat and require robust mechanical connections, which through hole mounting provides.
-
Simplified Visual Inspection: With through hole mounting, the solder joints are visible on the opposite side of the board, making visual inspection and troubleshooting easier. This can be advantageous for quality control and repair purposes.
Disadvantages of Through Hole Mounting
-
Larger PCB Size: Through hole components require drilled holes and larger pad sizes, resulting in a larger overall PCB size compared to surface mount designs. This can be a limitation when designing compact or space-constrained devices.
-
Higher Manufacturing Costs: Through hole mounting involves additional steps such as drilling holes and manual insertion of components, which can increase manufacturing time and costs, especially for high-volume production.
-
Limited Component Density: Due to the larger size of through hole components and the need for drilled holes, the component density on a through hole PCB is lower compared to surface mount designs. This can be a drawback when designing complex circuits with a large number of components.
-
Reduced High-Frequency Performance: Through hole mounting can introduce longer lead lengths and larger parasitic inductances, which can negatively impact high-frequency performance. This can be a concern for high-speed digital circuits or RF applications.
What is Surface Mount Technology?
Surface mount technology (SMT) is a modern PCB-mounting method where components are mounted directly onto the surface of the PCB without the need for drilled holes. SMT components have small metal pads or leads that are soldered onto corresponding pads on the PCB surface. This technology has gained widespread adoption due to its numerous benefits.
Advantages of Surface Mount Technology
-
Miniaturization: SMT components are significantly smaller than through hole components, allowing for higher component density and more compact PCB designs. This is particularly advantageous for portable devices, wearables, and other space-constrained applications.
-
Improved High-Frequency Performance: SMT components have shorter lead lengths and smaller parasitic inductances compared to through hole components. This results in better high-frequency performance and reduced signal integrity issues, making SMT ideal for high-speed digital circuits and RF applications.
-
Automated Assembly: SMT is well-suited for automated assembly processes using pick-and-place machines and reflow soldering. This enables faster and more efficient manufacturing, reducing costs and improving consistency in high-volume production.
-
Reduced Manufacturing Costs: SMT eliminates the need for drilling holes and manual insertion of components, resulting in faster assembly times and lower manufacturing costs compared to through hole mounting, especially for large-scale production.
-
Design Flexibility: SMT allows for components to be placed on both sides of the PCB, enabling higher component density and more complex circuit designs. This flexibility is particularly beneficial for advanced electronic devices with limited board space.
Disadvantages of Surface Mount Technology
-
Challenging Manual Assembly: SMT components are small and require precise placement, making manual assembly more challenging compared to through hole components. This can be a drawback for prototyping or low-volume production where manual assembly is preferred.
-
Reduced Mechanical Strength: SMT components rely on the strength of the solder joint between the component pads and PCB pads for mechanical stability. This can make SMT assemblies more susceptible to damage from mechanical stress or vibration compared to through hole assemblies.
-
Specialized Equipment: SMT assembly requires specialized equipment such as pick-and-place machines, reflow ovens, and solder paste printers. This initial investment in equipment can be a barrier for small-scale or hobby projects.
-
Thermal Management: SMT components have limited heat dissipation capabilities due to their small size and lack of through hole leads. This can be a challenge for high-power components or applications with significant heat generation, requiring careful thermal management techniques.
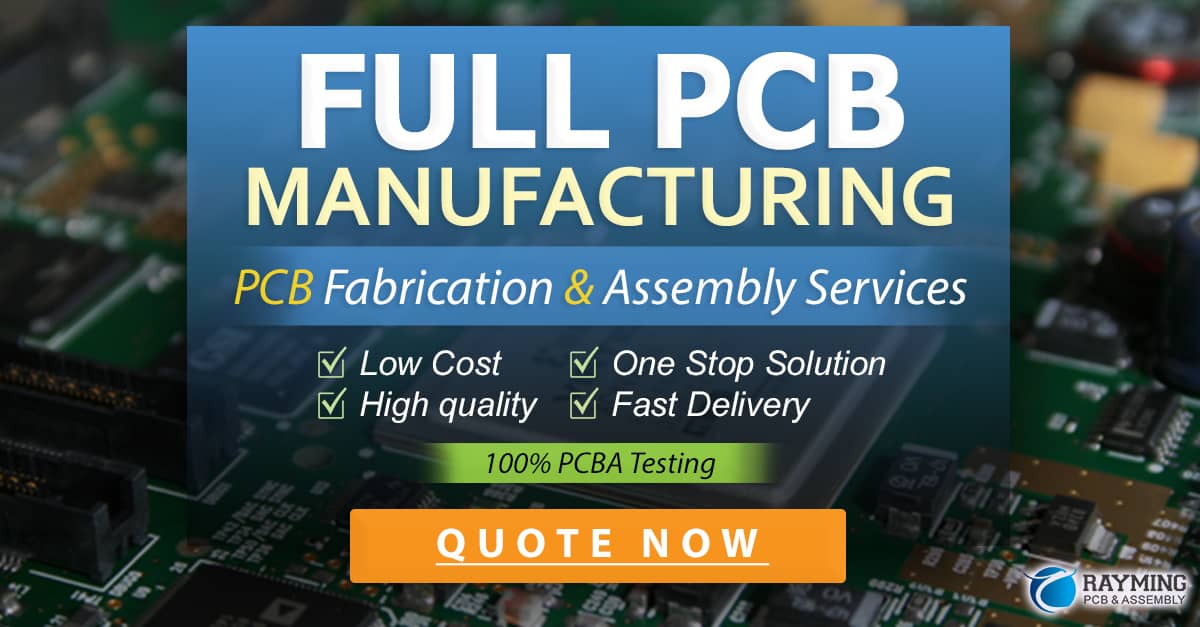
Factors to Consider When Choosing Between Through Hole and Surface Mount
When deciding between through hole and surface mount mounting methods, several factors should be considered to ensure the best fit for your specific project. These factors include:
-
Application Requirements: Consider the specific requirements of your application, such as mechanical strength, environmental conditions, high-frequency performance, and space constraints. These requirements will guide your decision towards the appropriate mounting method.
-
Component Availability: Check the availability of components in through hole or surface mount packages. Some components may only be available in one package type, which can dictate the mounting method choice.
-
Manufacturing Capabilities: Assess your manufacturing capabilities or those of your chosen PCB Assembly partner. SMT assembly requires specialized equipment and processes, while through hole mounting can be done with simpler tools and manual assembly.
-
Production Volume: Consider the expected production volume of your project. SMT is more cost-effective for high-volume production due to automated assembly processes, while through hole mounting can be more economical for low-volume or prototype builds.
-
Cost Considerations: Evaluate the overall cost implications of each mounting method, including component costs, PCB fabrication costs, and assembly costs. SMT generally offers lower costs for high-volume production, while through hole mounting can be more cost-effective for low-volume or manual assembly.
-
Design Complexity: Assess the complexity of your circuit design and the number of components required. SMT allows for higher component density and more complex designs, while through hole mounting may be sufficient for simpler circuits with fewer components.
-
Reliability and Durability: Consider the reliability and durability requirements of your application. Through hole mounting provides stronger mechanical connections and better resistance to vibration and shock, while SMT offers improved high-frequency performance and reduced signal integrity issues.
Mixed Mounting: Combining Through Hole and Surface Mount
In some cases, a combination of through hole and surface mount techniques can be used on the same PCB. This approach, known as mixed mounting or hybrid mounting, leverages the strengths of both methods to achieve the desired outcomes.
Mixed mounting can be beneficial in scenarios where certain components are only available in through hole packages, while others are available in surface mount packages. It can also be used to provide additional mechanical strength for specific components, such as connectors or large capacitors, while utilizing SMT for the majority of the circuit.
When using mixed mounting, it’s important to consider the assembly process and ensure compatibility between the through hole and surface mount components. The PCB design should accommodate the different mounting methods, and the assembly process should be optimized to handle both types of components efficiently.
PCB-Mounting Techniques Comparison Table
Factor | Through Hole Mounting | Surface Mount Technology |
---|---|---|
Component Size | Larger | Smaller |
PCB Size | Larger | Smaller |
Component Density | Lower | Higher |
Manufacturing Costs | Higher for high-volume | Lower for high-volume |
Assembly Process | Manual or automated | Automated |
Mechanical Strength | Strong | Weaker |
High-Frequency Performance | Limited | Better |
Heat Dissipation | Better | Limited |
Design Flexibility | Limited | Higher |
Prototype Suitability | Good | Challenging |
Frequently Asked Questions (FAQ)
-
Q: Can I use both through hole and surface mount components on the same PCB?
A: Yes, it is possible to use a combination of through hole and surface mount components on the same PCB. This approach is known as mixed mounting or hybrid mounting and can be beneficial in certain scenarios where specific components are only available in one package type or when additional mechanical strength is required for specific parts of the circuit. -
Q: Is surface mount technology suitable for high-power applications?
A: Surface mount technology has limitations when it comes to high-power applications due to the smaller size of SMT components and their reduced heat dissipation capabilities. For high-power components or applications with significant heat generation, through hole mounting is often preferred as it provides better thermal management and stronger mechanical connections. -
Q: Can I manually assemble surface mount components?
A: While manual assembly of surface mount components is possible, it can be challenging due to their small size and the need for precise placement. SMT components require steady hands, good eyesight, and specialized tools such as tweezers and soldering iron tips. For prototyping or low-volume production, manual SMT assembly can be done with practice and patience, but it is generally more time-consuming and error-prone compared to automated assembly processes. -
Q: Which mounting method is more cost-effective for high-volume production?
A: Surface mount technology is generally more cost-effective for high-volume production due to the automated assembly processes and faster assembly times. SMT eliminates the need for drilling holes and manual insertion of components, reducing manufacturing costs compared to through hole mounting. However, the initial investment in specialized SMT equipment can be a consideration for small-scale or low-volume production. -
Q: Are there any specific applications where through hole mounting is preferred over surface mount?
A: Through hole mounting is often preferred in applications that require high mechanical strength, durability, and resistance to vibration or shock. Examples include automotive electronics, industrial control systems, and aerospace applications where the PCBs are subjected to harsh environmental conditions. Through hole mounting is also commonly used for high-power components, such as transformers and large capacitors, due to their better heat dissipation capabilities and stronger mechanical connections.
Conclusion
Choosing the right PCB-mounting method between through hole and surface mount technologies is a critical decision that impacts the design, manufacturing, and performance of electronic devices. Through hole mounting offers advantages such as strong mechanical connections, ease of manual assembly, and compatibility with high-power components. On the other hand, surface mount technology enables miniaturization, improved high-frequency performance, automated assembly, and reduced manufacturing costs for high-volume production.
When selecting the appropriate mounting method, it’s essential to consider factors such as application requirements, component availability, manufacturing capabilities, production volume, cost considerations, design complexity, and reliability needs. In some cases, a combination of through hole and surface mount techniques can be used to leverage the strengths of both methods.
By understanding the characteristics, benefits, and drawbacks of through hole and surface mount technologies, designers and manufacturers can make informed decisions to optimize their PCB designs and ensure the best possible outcomes for their electronic products.
0 Comments