Introduction to PCB Standards
Printed circuit boards (PCBs) are essential components in virtually all modern electronic devices. To ensure the quality, reliability, and consistency of PCBs, the electronics industry relies on various standards and guidelines. Two of the most crucial standards in PCB Production are IPC-6012, which defines the qualification and performance specifications for rigid printed boards, and IPC-A-600, which provides acceptability guidelines for PCBs. This article will explore the importance of these standards and their role in ensuring the production of high-quality PCBs.
What is IPC-6012?
IPC-6012 is a standard developed by the Association Connecting Electronics Industries (IPC) that establishes the qualification and performance requirements for rigid printed boards. This standard covers various aspects of PCB production, including:
- Material requirements
- Dimensional tolerances
- Hole sizes and locations
- Conductor width and spacing
- Surface finishes
- Electrical testing
- Mechanical testing
The goal of IPC-6012 is to provide a consistent set of requirements that PCB Manufacturers can follow to ensure their products meet the necessary quality and performance standards. By adhering to this standard, manufacturers can produce PCBs that are reliable, durable, and suitable for their intended applications.
IPC-6012 Classes
IPC-6012 defines three classes of PCBs based on their intended end-use and the level of reliability required:
Class | Description | Typical Applications |
---|---|---|
Class 1 | General Electronic Products | Consumer electronics, computer peripherals |
Class 2 | Dedicated Service Electronic Products | Telecommunications, industrial controls, instrumentation |
Class 3 | High Reliability Electronic Products | Aerospace, medical devices, military equipment |
Each class has increasingly stringent requirements for material selection, manufacturing processes, and testing procedures. By specifying the appropriate class for a given application, designers and manufacturers can ensure that the resulting PCBs will meet the necessary performance and reliability standards.
What is IPC-A-600?
IPC-A-600 is a companion standard to IPC-6012 that provides acceptability guidelines for printed circuit boards. This standard defines the visual and dimensional criteria for accepting or rejecting PCBs based on various characteristics, including:
- Soldermask coverage and registration
- Legend and marking
- Laminate imperfections
- Conductor definition and spacing
- Hole size and location
- Surface finish quality
The purpose of IPC-A-600 is to establish a common language and set of criteria for evaluating the quality of PCBs. By using this standard, PCB manufacturers, assemblers, and end-users can communicate more effectively and ensure that the PCBs being produced meet the necessary quality standards.
IPC-A-600 Acceptance Criteria
IPC-A-600 defines three levels of acceptance criteria based on the intended end-use and the level of quality required:
Level | Description | Typical Applications |
---|---|---|
Target | Highest quality, fewest allowable defects | High-reliability applications, aerospace, medical devices |
Acceptable | Moderate quality, some allowable defects | Industrial controls, automotive electronics |
Usable | Lowest quality, more allowable defects | Consumer electronics, low-cost applications |
By specifying the appropriate acceptance level for a given application, designers and manufacturers can ensure that the resulting PCBs will meet the necessary quality standards without incurring unnecessary costs associated with overly stringent requirements.
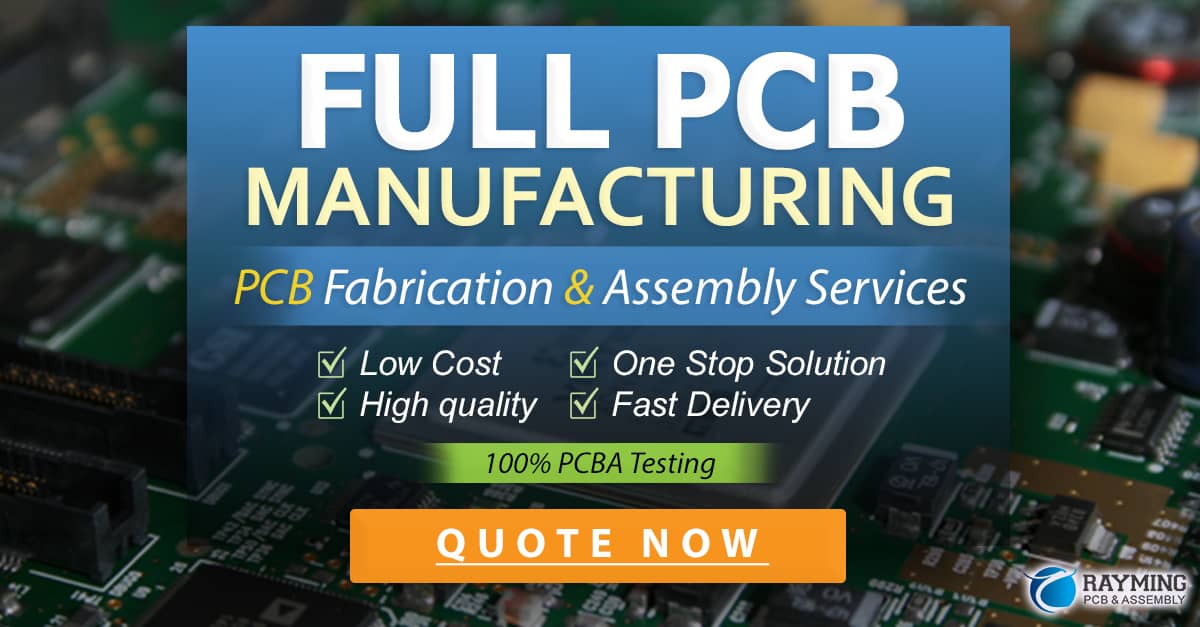
The Importance of IPC-6012 and IPC-A-600 in PCB Production
The use of IPC-6012 and IPC-A-600 standards in PCB production offers several key benefits:
1. Consistency and Reliability
By following the requirements and guidelines set forth in these standards, PCB manufacturers can produce boards that are consistent in quality and performance. This consistency translates into improved reliability for the end-use applications, as the PCBs are more likely to function as intended and withstand the stresses of their operating environments.
2. Improved Communication
The use of common standards like IPC-6012 and IPC-A-600 facilitates better communication between PCB designers, manufacturers, assemblers, and end-users. By referring to these standards, all parties involved in the PCB production process can have a clear understanding of the requirements and expectations for the final product.
3. Cost Savings
Adhering to IPC Standards can help reduce costs associated with PCB production in several ways. First, by producing boards that meet the necessary quality and reliability standards, manufacturers can minimize the need for rework and scrap. Second, by specifying the appropriate class and acceptance level for a given application, designers and manufacturers can avoid the costs associated with over-specifying the requirements for a PCB.
4. Regulatory Compliance
Many industries, such as aerospace, medical, and military, have strict regulatory requirements for the electronics used in their applications. By following IPC standards, PCB manufacturers can demonstrate compliance with these regulations and ensure that their products are suitable for use in these critical applications.
Implementing IPC-6012 and IPC-A-600 in PCB Production
To effectively implement IPC-6012 and IPC-A-600 in PCB production, manufacturers should follow these steps:
- Train personnel on the requirements and guidelines of the standards
- Establish clear specifications for each PCB design, including the appropriate class and acceptance level
- Implement robust quality control processes to ensure compliance with the standards
- Regularly audit manufacturing processes and finished products to identify areas for improvement
- Maintain accurate documentation of materials, processes, and test results
By following these steps, PCB manufacturers can ensure that their products consistently meet the necessary quality and reliability standards, while also improving efficiency and reducing costs.
Frequently Asked Questions (FAQ)
1. Are IPC-6012 and IPC-A-600 mandatory standards for PCB production?
While IPC-6012 and IPC-A-600 are not mandatory standards, they are widely recognized and adopted throughout the electronics industry. Many customers and regulatory agencies require compliance with these standards as a condition of doing business.
2. How often are IPC-6012 and IPC-A-600 updated?
IPC standards are regularly reviewed and updated to keep pace with changes in technology and industry practices. Typically, these standards are updated every 5-7 years, with occasional amendments released in between major revisions.
3. Can a single PCB have different IPC classes for different aspects of its design?
Yes, it is possible for a single PCB to have different IPC classes specified for different aspects of its design. For example, a PCB may have Class 2 requirements for its general construction and Class 3 requirements for its hole size and location tolerances.
4. How can I ensure that my PCB supplier is complying with IPC standards?
To ensure that your PCB supplier is complying with IPC standards, you should request documentation of their quality control processes, material certifications, and test results. You may also consider conducting on-site audits of their manufacturing facilities to verify compliance.
5. Are there any limitations to using IPC standards in PCB production?
While IPC standards provide a comprehensive set of guidelines for PCB production, they may not cover every possible scenario or application. In some cases, designers and manufacturers may need to develop custom specifications or testing procedures to meet the unique requirements of their products.
Conclusion
IPC-6012 and IPC-A-600 are essential standards in the world of PCB production, providing a consistent set of requirements and guidelines for ensuring the quality, reliability, and consistency of printed circuit boards. By understanding and implementing these standards, PCB designers, manufacturers, and end-users can work together to create products that meet the necessary performance and regulatory requirements while also optimizing costs and efficiency. As the electronics industry continues to evolve, the importance of these standards will only continue to grow, making them an indispensable tool for anyone involved in PCB production.
0 Comments