What is Heavy Copper and Why is it Used in PCBs?
Heavy copper refers to printed circuit boards (PCBs) that use thicker copper layers than standard PCBs. While typical PCBs have copper layers ranging from 0.5 oz to 2 oz in thickness, heavy copper PCBs can have copper weights of 3 oz, 4 oz, 6 oz or even higher.
The main reasons for using heavy copper in PCB fabrication include:
- Carrying higher currents: Thicker copper traces can handle higher amperages without overheating
- Improved thermal management: Heavy copper helps dissipate more heat away from components
- Enhanced mechanical strength: Boards with heavy copper are more robust and durable
- Reduced resistance: Thicker copper means lower electrical resistance in traces
Heavy copper is often used in power electronics, automotive, aerospace, medical, and industrial applications where high currents, thermal dissipation, and reliability are critical. The table below shows some common copper weights and their typical current carrying capacity:
Copper Weight (oz) | Trace Thickness (mils) | Current Capacity (amps per inch width) |
---|---|---|
0.5 | 0.7 | 2.2 |
1 | 1.4 | 4.4 |
2 | 2.8 | 8.8 |
3 | 4.2 | 13.2 |
4 | 5.6 | 17.6 |
6 | 8.4 | 26.4 |
As can be seen, doubling the copper weight approximately doubles the current carrying capacity. However, using heavier copper does have tradeoffs in terms of cost, manufacturability, and design complexity that must be considered.
Advantages of Heavy Copper PCBs
Higher Current Carrying Capacity
One of the primary benefits of heavy copper PCBs is their ability to carry higher currents than standard thickness copper. In power electronics applications like motor drives, inverters, power supplies, etc., the components can draw substantial amounts of current that would overwhelm thin copper traces.
Using heavy copper allows designers to use wider traces while still fitting the PCB into size-constrained enclosures. Trying to carry high currents on thin copper necessitates extremely wide traces that take up excessive board real estate. Heavy copper provides a more space-efficient solution.
Improved Thermal Management
In addition to carrying current, copper layers on a PCB also serve as a heat spreader to take heat away from power components. Thicker copper weights provide a larger cross-sectional area for heat conduction, allowing the copper to act as a heatsink.
The improved thermal dissipation from heavy copper can allow some designs to use the PCB itself as the primary cooling path, eliminating the need for additional heatsinks or thermal management hardware. This can lead to cost and space savings in the final product.
Greater Mechanical Strength
PCBs that use heavy copper are inherently more robust and resistant to flexing and vibration compared to thin boards. The additional copper thickness makes the board more rigid.
For applications like automotive and aerospace where PCBs may be subject to constant vibration and mechanical shocks, using heavy copper can improve long-term reliability. Thicker boards are less prone to cracking or breaking of solder joints and traces over time.
Lower Electrical Resistance
Increasing the copper weight in PCBs has the effect of lowering the electrical resistance of the traces. This is beneficial for a few reasons:
-
Lower resistance means less voltage drop over long traces, which is important for minimizing power loss and maintaining proper voltage levels at components.
-
Reduced resistance also means less heat generation due to I2R losses in the traces themselves. This further improves thermal performance.
-
Lowering resistance can help with meeting target impedance requirements for sensitive analog/RF circuits and controlled impedance traces. Thicker copper makes hitting impedance targets easier.
Disadvantages of Heavy Copper PCBs
Increased Material Cost
The most obvious downside of heavy copper PCBs is that they simply use more copper which raises the material cost of the board. Copper is often the most expensive part of a PCB, so doubling or tripling the copper weight has a non-trivial cost impact.
However, the cost increase from heavy copper is often outweighed by the performance benefits and potential savings from eliminating other thermal management components. It’s important to consider the system-level cost impact rather than just raw PCB fab costs.
More Difficult Manufacturing
PCB fabrication with heavy copper layers is more challenging than standard copper weights. Issues include:
-
Drilling: Thicker copper is harder to drill cleanly through. Drill bits wear out faster and more care must be taken to avoid burrs, smearing, etc.
-
Etching: Heavier copper takes longer to etch through completely which increases process time. Etchant chemistries may need to be adjusted. Undercutting and line width growth is more of an issue.
-
Plating: Vias are harder to plate conformally and voids are more common with thicker copper layers. Longer plating times are required.
-
Registration: Achieving precise layer-to-layer registration is more difficult with heavy copper due to inherent stresses in the material.
In general, using heavy copper requires much tighter process controls and more experienced PCB fabricators to get right. It’s not unusual for heavy copper boards to have longer lead times and higher scrap rates than standard boards.
Design Limitations
Aside from fab challenges, heavy copper also imposes some design limitations on PCBs such as:
- Reduced trace/space: Minimum trace width and spacing is larger for heavy copper because fine features are harder to etch reliably. This can make routing density lower.
- More vias needed: Longer traces may require additional vias to stitch layers together which take up space and add resistance/inductance.
- Restricted layer counts: Heavy copper is typically used on outer layers or dedicated inner planes. Trying to use heavy copper on all layers severely impacts via reliability and manufacturability.
In many cases, only power nets that need to carry significant current are done in heavy copper, while signal traces use standard weights. This hybrid approach balances copper utilization, routability, signal integrity, and manufacturability.
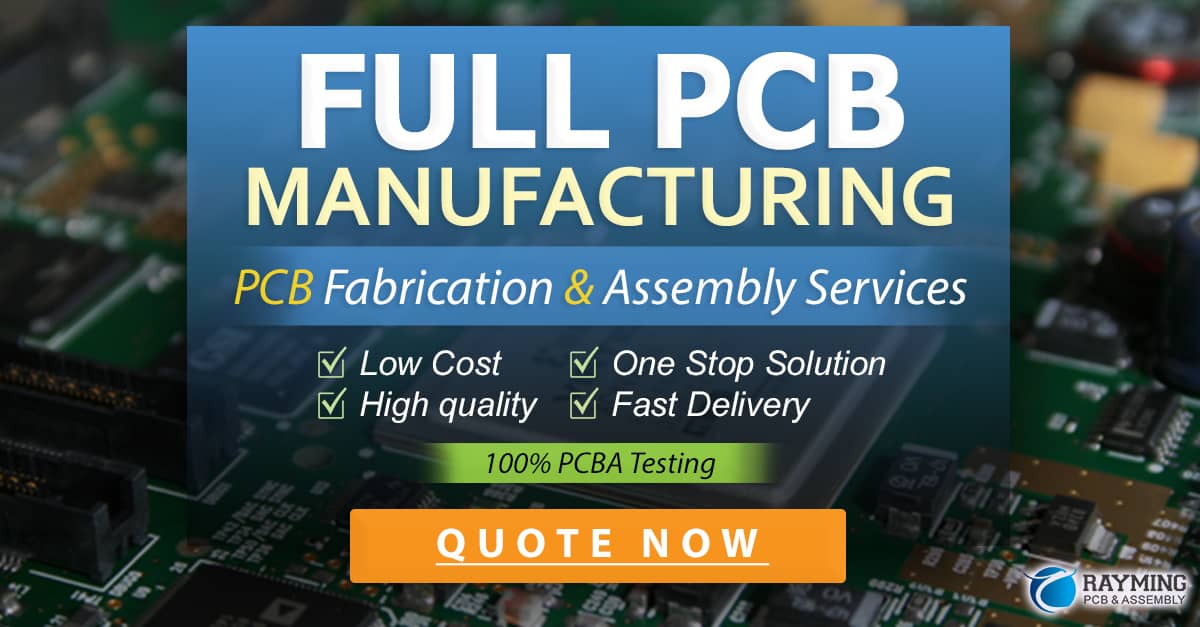
Design Considerations for Heavy Copper PCBs
When designing a PCB with heavy copper, there are several key considerations to keep in mind beyond just increasing the copper weight. Careful planning is needed to ensure the heavy copper is utilized effectively.
Copper Distribution
Simply specifying a heavy copper finish on a PCB is not sufficient. The designer must be intentional about where the heavy copper is actually used and how it is distributed. Some points to consider:
- Current paths: Heavy copper should be focused on the high current nets like power inputs, motor leads, etc. There is often no benefit to using heavy copper on signal traces.
- Copper balance: Thicker copper on specific layers can cause warpage due to uneven stresses. It’s good practice to balance copper weights on mirrored layers to prevent twisting.
- Trace width: Heavy copper traces can be made narrower than standard traces for the same current capacity. However, going too narrow introduces manufacturing risk. Consult with the fab house on minimum suggested heavy copper trace widths.
Thermal Analysis
Getting the most benefit from heavy copper on a PCB requires a detailed thermal analysis to identify heat flow and hot spots. Thermal simulation should be performed early in the design stage to determine what copper weights are actually needed and where they should be deployed.
Some specific thermal factors to analyze include:
- Component power dissipation
- Ambient temperature conditions
- Airflow and cooling paths
- Heatsinking and heat spreader placement
- Thermal vias and heat transfer through board layers
The results of this analysis will guide copper placement, trace sizing, and layout for optimal thermal performance. It may turn out that only certain layers or regions of the board need heavy copper to meet thermal requirements.
Manufacturing Tolerances
As mentioned previously, manufacturing heavy copper boards can be challenging. To minimize issues, the design should incorporate appropriate tolerances and adhere to fab house guidelines. Some key points:
- Trace/space: Increase nominal trace widths and clearances to account for etch variation and registration tolerances.
- Annular rings: Use larger annular rings on vias and pads to allow for more mis-registration.
- Soldermask: Increase soldermask web and clearances around pads to avoid solder bridging and tombstoning.
- Panelization: Be mindful of how the board outline and panel fiducials may be impacted by heavier copper and adjust panel layout accordingly.
Following the fab vendor’s specific heavy copper design rules is always advisable. They can provide customized guidelines based on the copper weights and layer stack being used.
FAQ
What is considered “heavy copper” in PCBs?
Heavy copper typically refers to copper weights of 3 oz or greater, though there is no firm threshold. Many PCB fabs consider 2 oz copper to be heavy. In general, heavy copper is any copper weight that exceeds the nominal 0.5-1 oz used on most standard PCBs.
Is heavy copper more expensive than regular copper?
Yes, heavy copper PCBs are more expensive than standard copper boards due to the increased material cost and specialized manufacturing processes required. The price difference depends on the specific copper weight and board complexity but is typically 20-50% higher.
Can I use heavy copper on inner layers?
Heavy copper is most commonly used on outer layers and power/ground planes. Using heavy copper on inner signal layers is more difficult for manufacturers and not typically recommended. If heavy copper is needed on inner layers, it’s best to consult with the fab house on the feasibility and cost impact.
What is the maximum copper weight possible on a PCB?
The maximum copper weight depends on the specific fab vendor but can range up to 10-12 oz in some cases. Above 6 oz is considered extreme and very costly. Most heavy copper designs use 3-4 oz copper which provides significant current handling benefits without excessive fabrication challenges.
How do I specify heavy copper on a PCB?
Heavy copper callouts should be clearly specified in the PCB Fab Drawing and layer stackup. Typically, copper weights are called out in ounces per square foot (oz/ft2) for each individual layer. The fab notes should also specify any special tolerances or design rules being used for the heavy copper sections.
Conclusion
Heavy copper PCBs offer significant advantages in terms of current carrying capacity, thermal dissipation, mechanical strength, and electrical performance. For power electronics and other high-reliability applications, using thicker copper layers can be an enabling technology.
However, heavy copper also comes with tradeoffs in terms of cost, manufacturability, and design complexity that must be carefully considered. Thermal analysis and close collaboration with the PCB fabricator are essential to realize the full benefits of heavy copper.
When used judiciously and with proper design practices, heavy copper can greatly enhance the capabilities and robustness of PCBs. As power levels continue to increase in many applications, heavy copper will be an increasingly valuable tool for PCB designers to meet performance and reliability goals.
0 Comments