Understanding the Basics of a PCB Fab Drawing
What is a PCB Fab Drawing?
A PCB fab drawing is a detailed technical illustration that depicts the physical layout, dimensions, and specifications of a printed circuit board. It includes information such as the board outline, layer stack-up, drill sizes, pad sizes, and other critical parameters required for manufacturing. The fab drawing acts as a bridge between the design and production stages, ensuring that the PCB is fabricated accurately and efficiently.
Why is a PCB Fab Drawing Important?
A well-prepared PCB fab drawing is essential for several reasons:
-
Clear Communication: It provides a clear and concise way to communicate the design intent to the manufacturing team, minimizing the chances of misinterpretation or errors.
-
Quality Assurance: By specifying the required tolerances, materials, and finishes, the fab drawing helps ensure that the manufactured PCB meets the desired quality standards.
-
Cost Optimization: A detailed fab drawing allows the manufacturing team to identify potential issues early in the process, reducing the risk of costly rework or delays.
-
Consistency: It serves as a reference document for future production runs, ensuring consistency and repeatability in the manufacturing process.
Key Elements of a PCB Fab Drawing
To effectively read and interpret a PCB fab drawing, it is essential to understand the various elements and symbols used. Let’s explore the key components of a typical fab drawing:
Board Outline and Dimensions
The board outline defines the physical shape and size of the PCB. It includes the overall dimensions, such as length, width, and thickness, as well as any cutouts, slots, or unique features. The dimensions are typically specified in millimeters (mm) or inches (in).
Layer Stack-up
The layer stack-up describes the arrangement and composition of the conductive layers and insulating materials within the PCB. It specifies the number of layers, their order, and the materials used for each layer (e.g., copper, prepreg, core). The stack-up also indicates the thickness of each layer and the overall board thickness.
Layer | Material | Thickness (mm) |
---|---|---|
Top Copper | Copper | 0.035 |
Prepreg | FR-4 | 0.2 |
Inner Layer 1 | Copper | 0.035 |
Core | FR-4 | 0.5 |
Inner Layer 2 | Copper | 0.035 |
Prepreg | FR-4 | 0.2 |
Bottom Copper | Copper | 0.035 |
Drill Holes and Sizes
Drill holes are used for through-hole components, vias, and mounting purposes. The fab drawing specifies the location, size, and type of each drill hole. Common drill hole types include:
-
Plated Through Holes (PTH): Used for through-hole component leads and vias, these holes are plated with conductive material to establish electrical connectivity between layers.
-
Non-Plated Through Holes (NPTH): Used for mounting or mechanical purposes, these holes are not plated and do not provide electrical connectivity.
The drill sizes are typically specified in decimal inches or metric units, such as 0.8mm or 0.031in.
Pads and Footprints
Pads are the conductive areas on the PCB where components are soldered. The fab drawing provides information about the size, shape, and location of each pad. Footprints are the specific patterns of pads and drill holes required for a particular component package (e.g., QFP, SOIC, BGA).
The fab drawing may include a separate component placement diagram or assembly drawing that shows the location and orientation of each component on the board.
Silkscreen and Legend
Silkscreen, also known as legend or overlay, refers to the text, symbols, and artwork printed on the surface of the PCB. It provides information such as component designators, polarity markers, and logos. The fab drawing specifies the content, location, and size of the silkscreen elements.
Solder Mask and Solder Paste
Solder mask is a protective coating applied to the PCB to prevent solder bridges and short circuits. It also helps to define the exposed copper areas where components will be soldered. The fab drawing indicates the color and type of solder mask to be used (e.g., green, black, matte, glossy).
Solder paste is a mixture of tiny solder particles suspended in flux, used for surface mount assembly. The fab drawing may include information about the solder paste stencil, specifying the aperture sizes and locations for precise solder paste application.
Fabrication Notes and Specifications
The fab drawing often includes additional notes and specifications that provide critical information for the manufacturing process. These may include:
-
Copper Weight: The thickness of the copper layers, typically expressed in ounces per square foot (oz/ft²) or microns (μm).
-
Finish Type: The surface finish applied to the exposed copper areas, such as HASL (Hot Air Solder Leveling), ENIG (Electroless Nickel Immersion Gold), or OSP (Organic Solderability Preservative).
-
Impedance Control: Specifications for controlled impedance traces, including the target impedance values and tolerances.
-
Special Requirements: Any unique or custom requirements, such as tight tolerances, specific materials, or testing procedures.
Interpreting Dimensional Tolerances
Dimensional tolerances are a critical aspect of PCB fab drawings, as they define the acceptable range of variation for various parameters. Understanding how to interpret these tolerances is essential for ensuring the manufacturability and functionality of the PCB.
Absolute and Relative Tolerances
Tolerances can be specified as absolute or relative values. Absolute tolerances are fixed values, such as ±0.1mm, while relative tolerances are expressed as a percentage of the nominal value, such as ±10%.
For example, if a pad size is specified as 1.0mm ±0.1mm, it means the acceptable range is from 0.9mm to 1.1mm. On the other hand, if a drill size is specified as 0.8mm ±10%, the acceptable range is from 0.72mm to 0.88mm.
Cumulative Tolerances
In some cases, tolerances can accumulate across multiple features or dimensions. For example, the position tolerance of a component pad may be affected by the tolerances of the drill hole, the copper etching, and the solder mask opening.
It is essential to consider the cumulative effect of tolerances and ensure that the overall tolerance stack-up meets the design requirements and manufacturing capabilities.
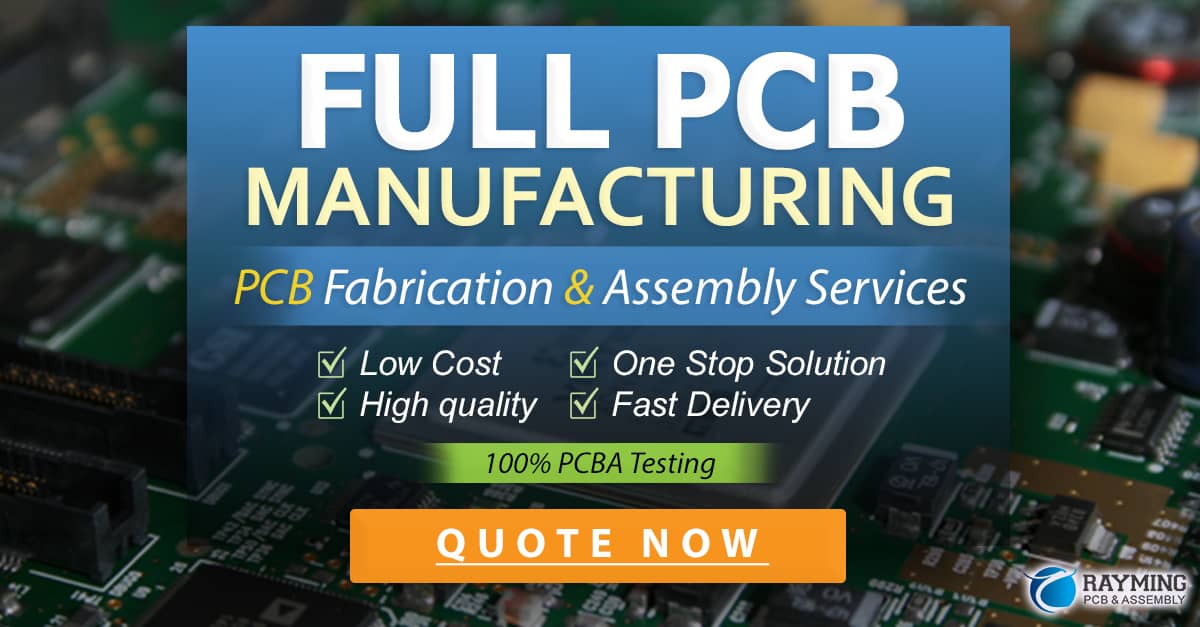
Best Practices for Creating and Using PCB Fab Drawings
To ensure effective communication and smooth manufacturing processes, follow these best practices when creating and using PCB fab drawings:
-
Use Standard Symbols and Notations: Adhere to industry-standard symbols, notations, and layer conventions to ensure clarity and consistency.
-
Provide Clear and Concise Information: Include all necessary information in the fab drawing, but avoid cluttering it with unnecessary details. Use clear and concise labels and notes.
-
Specify Critical Dimensions and Tolerances: Clearly indicate the critical dimensions and tolerances that are essential for the functionality and manufacturability of the PCB.
-
Review and Verify: Thoroughly review the fab drawing for accuracy, completeness, and consistency before releasing it for manufacturing. Verify that all requirements are met and that the drawing is free of errors or ambiguities.
-
Communicate with the Manufacturing Team: Maintain open communication with the PCB fabrication house to clarify any questions or concerns. Provide additional information or clarifications as needed to ensure a smooth manufacturing process.
Frequently Asked Questions (FAQ)
-
What is the difference between a PCB fab drawing and an assembly drawing?
A PCB fab drawing focuses on the fabrication aspects of the PCB, such as the board outline, layer stack-up, and drilling requirements. An assembly drawing, on the other hand, provides information for the component placement and soldering process, including the component locations, orientations, and bill of materials (BOM). -
How do I specify controlled impedance requirements in a PCB fab drawing?
Controlled impedance requirements are typically specified in the fabrication notes section of the fab drawing. Include the target impedance values, tolerances, and the specific traces or layers that require impedance control. Provide the necessary stack-up information and materials to enable the fabricator to achieve the desired impedance. -
What is the purpose of solder mask on a PCB?
Solder mask is a protective coating applied to the PCB to prevent solder bridges and short circuits during the soldering process. It also helps to define the exposed copper areas where components will be soldered, improving the accuracy and reliability of the assembly process. -
How do I ensure the manufacturability of my PCB design?
To ensure the manufacturability of your PCB design, consider the following factors: - Adhere to the fabricator’s design guidelines and capabilities.
- Use standard component packages and footprints.
- Provide adequate clearances and spacing between features.
- Specify realistic tolerances based on the fabrication capabilities.
-
Communicate any special requirements or constraints clearly in the fab drawing.
-
Can I use different units of measurement in a PCB fab drawing?
It is generally recommended to use a consistent unit of measurement throughout the fab drawing to avoid confusion and errors. The most common units used in PCB design are millimeters (mm) and mils (thousandths of an inch). If using different units, clearly specify the unit for each dimension or parameter.
Conclusion
Reading and interpreting a PCB fabrication drawing is a critical skill for anyone involved in the design, manufacturing, or assembly of printed circuit boards. By understanding the key elements, symbols, and tolerances used in fab drawings, you can effectively communicate design requirements, ensure manufacturability, and streamline the production process.
Remember to follow best practices, adhere to industry standards, and maintain open communication with the fabrication team to achieve the best results. With a well-prepared and accurately interpreted PCB fab drawing, you can bring your electronic designs to life with confidence and reliability.
0 Comments