What is a PCB Stencil?
A PCB (Printed Circuit Board) stencil is a thin sheet of metal, usually stainless steel, with laser-cut openings that correspond to the pads on a PCB. The stencil is used to apply solder paste to the PCB pads before components are placed and the board is sent through a reflow oven for soldering. This process is known as solder paste printing or solder paste application.
PCB stencils are an essential tool in the surface mount technology (SMT) assembly process, as they ensure precise and consistent application of solder paste, which is crucial for achieving reliable solder joints and high-quality PCB Assembly.
Why Use a PCB Stencil?
There are several reasons why PCB stencils are used in the SMT assembly process:
-
Precision: PCB stencils allow for precise control over the amount and placement of solder paste on the PCB pads. This precision is essential for achieving reliable solder joints and preventing defects such as bridging or insufficient solder.
-
Consistency: Using a PCB stencil ensures that the solder paste is applied consistently across all the pads on the board. This consistency is important for achieving uniform solder joints and minimizing variations in the assembly process.
-
Efficiency: PCB stencils enable the rapid application of solder paste to multiple boards in a production environment. This efficiency is crucial for high-volume manufacturing and reducing production time and costs.
-
Compatibility with fine-pitch components: As electronic components become smaller and more complex, PCB stencils are essential for applying solder paste to fine-pitch pads that are difficult or impossible to print using other methods.
Types of PCB Stencils
There are several types of PCB stencils available, each with its own characteristics and applications:
Stainless Steel Stencils
Stainless steel stencils are the most common type of PCB stencil. They are durable, easy to clean, and offer excellent print definition. Stainless steel stencils are available in various thicknesses, typically ranging from 0.1 mm to 0.2 mm (4 to 8 mils).
Advantages:
– Durable and long-lasting
– Easy to clean and maintain
– Excellent print definition
– Suitable for high-volume production
Disadvantages:
– More expensive than other types of stencils
– Not suitable for very fine-pitch applications (less than 0.4 mm)
Nickel Stencils
Nickel stencils are similar to stainless steel stencils but offer superior durability and corrosion resistance. They are often used in demanding applications or environments where the stencil may be exposed to harsh chemicals or abrasive cleaning processes.
Advantages:
– Excellent durability and corrosion resistance
– Suitable for demanding applications and environments
– Good print definition
Disadvantages:
– More expensive than stainless steel stencils
– Not suitable for very fine-pitch applications (less than 0.4 mm)
Polymer Stencils
Polymer stencils, also known as plastic or epoxy stencils, are made from a durable polymer material. They are less expensive than metal stencils and offer good print definition for less demanding applications.
Advantages:
– Lower cost compared to metal stencils
– Good print definition for less demanding applications
– Suitable for prototyping and low-volume production
Disadvantages:
– Less durable than metal stencils
– Not suitable for high-volume production or demanding applications
Nano-Coated Stencils
Nano-coated stencils are metal stencils (usually stainless steel) that have been coated with a nano-scale material, such as nickel-teflon or chromium. The coating helps to reduce solder paste adhesion to the stencil, improving the release characteristics and resulting in better print definition.
Advantages:
– Improved solder paste release characteristics
– Better print definition compared to uncoated stencils
– Reduced need for stencil cleaning
Disadvantages:
– More expensive than uncoated stencils
– The coating may wear off over time, requiring stencil replacement
Step Stencils
Step stencils, also known as multi-level or 3D stencils, have different thicknesses in specific areas to accommodate components with varying heights or to apply different amounts of solder paste to specific pads. Step stencils are used for advanced applications where a standard stencil cannot provide the required solder paste deposition.
Advantages:
– Accommodates components with varying heights
– Allows for different solder paste deposition on specific pads
– Enables advanced PCB designs
Disadvantages:
– More expensive than standard stencils
– Requires specialized design and manufacturing processes
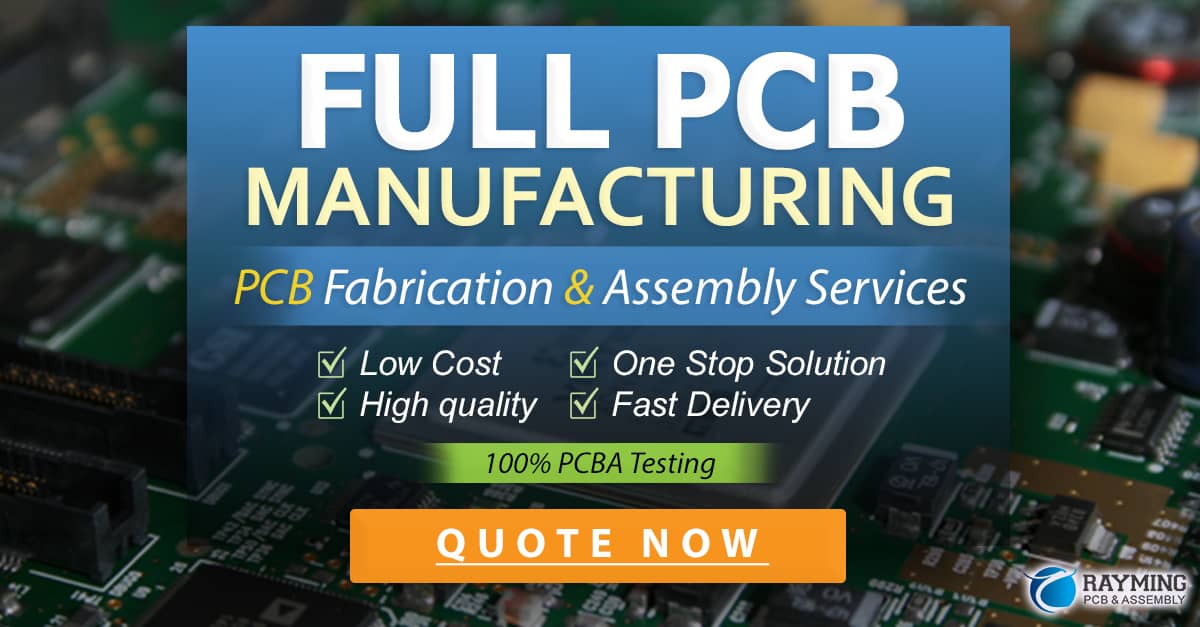
PCB Stencil Thickness
The thickness of a PCB stencil is a critical factor in determining the amount of solder paste deposited on the pads. The optimal stencil thickness depends on various factors, such as the size and pitch of the components, the PCB design, and the solder paste properties.
Common PCB stencil thicknesses:
Thickness (mm) | Thickness (mils) | Typical Applications |
---|---|---|
0.1 | 4 | Very fine-pitch components (0.3 mm or less) |
0.12 | 5 | Fine-pitch components (0.4 mm to 0.5 mm) |
0.15 | 6 | Standard SMD components (0.5 mm to 0.8 mm) |
0.2 | 8 | Larger SMD components (0.8 mm or more) |
Choosing the right stencil thickness is essential for achieving the desired solder paste deposition and ensuring reliable solder joints. Thinner stencils are typically used for smaller, fine-pitch components, while thicker stencils are used for larger components or when more solder paste is required.
PCB Stencil Aperture Design
The aperture design of a PCB stencil refers to the size, shape, and arrangement of the openings that correspond to the pads on the PCB. Proper aperture design is crucial for achieving the desired solder paste deposition and preventing defects such as bridging or insufficient solder.
Factors to consider when designing PCB stencil apertures:
-
Aperture size: The aperture size should be slightly larger than the pad size to allow for adequate solder paste deposition. A common rule of thumb is to make the aperture size 10% to 20% larger than the pad size.
-
Aperture shape: The shape of the aperture should match the shape of the pad. Common aperture shapes include rectangular, circular, and oblong.
-
Aperture orientation: The orientation of the aperture should match the orientation of the pad. This is particularly important for oblong or rectangular pads.
-
Aperture pitch: The pitch, or spacing, between apertures should be sufficient to prevent solder paste bridging between adjacent pads.
-
Aperture area ratio: The area ratio is the ratio of the aperture area to the stencil thickness. A higher area ratio allows for better solder paste release and print definition. A minimum area ratio of 0.66 is typically recommended.
Proper aperture design requires careful consideration of these factors and may involve iterations and testing to achieve the best results. Many PCB design software packages include tools for generating and optimizing stencil aperture designs based on the PCB layout.
PCB Stencil Cleaning and Maintenance
Regular cleaning and maintenance of PCB stencils are essential for ensuring consistent solder paste printing quality and extending the life of the stencil. Solder paste residue, dust, and other contaminants can accumulate on the stencil over time, leading to poor print definition and defects.
Cleaning Methods
There are several methods for cleaning PCB stencils:
-
Manual cleaning: Manual cleaning involves using a lint-free wipe or swab and a cleaning solution, such as isopropyl alcohol or a specialized stencil cleaning agent, to remove solder paste residue and other contaminants from the stencil surface and apertures.
-
Ultrasonic cleaning: Ultrasonic cleaning uses high-frequency sound waves to agitate a cleaning solution, creating tiny bubbles that help to dislodge and remove contaminants from the stencil surface and apertures. This method is more effective than manual cleaning for removing stubborn residue.
-
Automated cleaning: Automated cleaning systems use a combination of spraying, brushing, and drying to clean the stencil. These systems are efficient and effective for cleaning stencils in a production environment, as they reduce the need for manual labor and ensure consistent cleaning results.
Maintenance Tips
To maintain the quality and extend the life of your PCB stencils, follow these tips:
-
Clean the stencil regularly, ideally after every printing session or as recommended by the stencil manufacturer.
-
Use the appropriate cleaning method and solutions for your stencil type and application.
-
Inspect the stencil for damage or wear, such as bent apertures or worn coatings, and replace the stencil when necessary.
-
Store the stencil in a clean, dry environment to prevent contamination and damage.
-
Handle the stencil carefully to avoid bending or damaging the apertures.
By following proper cleaning and maintenance practices, you can ensure that your PCB stencils continue to provide consistent, high-quality solder paste printing results.
Frequently Asked Questions (FAQ)
-
What is the difference between a PCB stencil and a solder paste screen?
A PCB stencil and a solder paste screen are essentially the same things. Both terms refer to a thin sheet of metal with laser-cut openings used to apply solder paste to PCB pads. The term “stencil” is more commonly used in the industry. -
How often should I replace my PCB stencil?
The lifespan of a PCB stencil depends on various factors, such as the stencil material, the printing volume, and the cleaning and maintenance practices. On average, a stainless steel stencil can last for 50,000 to 100,000 prints with proper care. However, it is essential to inspect the stencil regularly for signs of wear or damage and replace it when necessary to maintain print quality. -
Can I use the same PCB stencil for different solder paste types?
In general, it is best to use a separate stencil for each type of solder paste to avoid cross-contamination and ensure optimal printing results. Different solder pastes may have different rheological properties, such as viscosity and slump, which can affect the printing process and require different stencil designs. -
How do I store my PCB stencils when not in use?
PCB stencils should be stored in a clean, dry environment to prevent contamination and damage. Store the stencils vertically in a rack or hanging system to avoid bending or warping. If storing the stencils horizontally, place them between clean, lint-free sheets of paper or cardboard to protect the surface and apertures. -
What are the most common causes of poor solder paste printing quality?
Some of the most common causes of poor solder paste printing quality include: - Dirty or damaged stencils
- Incorrect stencil design or aperture size
- Improper printer setup or calibration
- Incorrect solder paste viscosity or rheology
- Contaminated or expired solder paste
- Inadequate PCB pad preparation or cleanliness
By addressing these issues and following best practices for stencil design, cleaning, and maintenance, you can minimize print defects and achieve consistent, high-quality solder paste deposition.
Conclusion
PCB stencils are an essential tool in the SMT assembly process, enabling precise and consistent solder paste application for high-quality PCB assembly. By understanding the types of stencils available, proper aperture design, and cleaning and maintenance best practices, you can optimize your solder paste printing process and achieve reliable, defect-free solder joints.
When selecting a PCB stencil, consider factors such as the stencil material, thickness, and aperture design based on your specific application requirements and PCB design. Regularly clean and maintain your stencils to ensure consistent print quality and extend the stencil’s lifespan.
By following the information and guidelines provided in this definitive guide to PCB stencils, you can make informed decisions and implement best practices to streamline your SMT assembly process and produce high-quality, reliable PCBs.
0 Comments